De toepassing van Rapid Prototyping-technologie bij het gieten van investeringen
Rapid Prototyping (RP) is een hightech ontwikkeld in de jaren negentig. Het kan de ontwerpconcepten in de hoofden van mensen snel veranderen in echte objecten. Het is met name vermeldenswaard dat het hele productontwikkelingsproces geen matrijzen en procesapparatuur vereist, wat de proefproductiecyclus van prototypes en nieuwe producten aanzienlijk verkort en snel een belangrijk middel en hulpmiddel wordt om het concurrentievermogen van ondernemingen te verbeteren. Uit de internetenquête die is gepubliceerd door INCAST 1990 (2004) blijkt dat meer dan 11% van de meer dan 93 fabrikanten van investeringsgietstukken in Europa gebruik hebben gemaakt van rapid prototyping. Alle geïnterviewden zijn het erover eens dat het gebruik van deze nieuwe technologie essentieel is voor het versnellen van nieuwe producten. Het is van groot belang het vermogen van ondernemingen om snel op de markt te reageren, te ontwikkelen en te verbeteren.
De toepassing van gemeenschappelijke methoden voor snelle prototypen bij het gieten van investeringen
De toepassing van rapid prototyping-technologie bij het gieten van investeringen omvat voornamelijk de volgende aspecten:
1. Doe een investering
Bij het maken van patronen kan de rapid prototyping-machine niet alleen driedimensionale geometrische modellen invoeren die zijn vastgesteld door andere CAD-software, maar ook gegevensbestanden ontvangen die zijn gescand door industriële CT (computertomografie). Scan bijvoorbeeld eerst het onderdeel (schroefschroef, figuur 12-1a) door CT om een tweedimensionaal beeld van de dwarsdoorsnede te krijgen (figuur 12-1b). Vervolgens combineert de beeldverwerkingssoftware de tweedimensionale afbeeldingen van elke sectie (Figuur 12-1c) om een driedimensionaal geometrisch model te vormen (Figuur 12-1d). Stuur het vervolgens naar de rapid prototyping-machine om een patroon te maken (Figuur 12-1e) [2]. Deze restauratie (reverse) engineering methode kan niet alleen machineonderdelen herstellen, maar ook bepaalde menselijke organen nabootsen.
2. Matrijzen maken (persgieten) en andere procesapparatuur
Er zijn twee methoden om precisiegietmatrijzen te maken door middel van rapid prototyping: de ene is om eerst een mastermal te maken en vervolgens om epoxy- of siliconenrubberprofilering opnieuw te maken; de andere methode is om het driedimensionale profileringsblok te gebruiken dat in het CAD-systeem is gegenereerd. Het geometrische model wordt rechtstreeks ingevoerd in de rapid prototyping-machine om harsvormen te maken. Dit type profilering is vooral geschikt voor kleine serieproductie (tientallen stuks). Als een metalen laag van ongeveer 2 mm dik op het oppervlak van de master-mal wordt gespoten en daarna epoxyhars wordt gevuld om een metaal-epoxy-composietprofiel te maken, kan het voldoen aan de vereisten voor het produceren van honderden precisiegietstukken. Bij gebruik van de SLS-methode wordt het verwerkingsobject bijvoorbeeld veranderd van harspoeder in staalpoeder met een dunne laag thermohardende hars op het oppervlak, lasergesinterd om een compact te vormen en vervolgens gebakken om de hars te verwijderen, en uiteindelijk kopervloeistof wordt geïnfiltreerd in de poriën van het compact. De resulterende profilering is vergelijkbaar met die van metaal in termen van sterkte en thermische geleidbaarheid. Daarnaast kan de rapid prototyping-technologie ook worden gebruikt om bepaalde onregelmatig gevormde mallen te maken.
3. Directe productie van gietstukken
Begin jaren negentig voerde het Sandiana National Laboratory in de Verenigde Staten een speciaal onderzoek uit, Fast Casting (FastCAST) genaamd, dat Direct Shell Casting (DSPC) werd genoemd. Helaas zijn er later maar weinig meldingen.
In 1994 ontwikkelde Z Corporation uit de Verenigde Staten met succes de 3D-printtechnologie 3D Printing. De technologie is oorspronkelijk uitgevonden en gepatenteerd door professor Ely Sachs van het Massachusetts Institute of Technology. Het basisprincipe is vergelijkbaar met de SLS-methode. Eerst wordt met een roller een laag vuurvast materiaal of kunststofpoeder gespoten. Het verschil met SLS is dat in plaats van een laser-emitterende kop aan te drijven, het een inkjetprintkop aandrijft om lijm te spuiten voor "afdrukken" volgens de dwarsdoorsnedevorm van het product. Herhaal bovenstaande handelingen totdat de onderdelen klaar zijn, het heet dus '3D printtechnologie'. De voordelen zijn lage bedrijfskosten en materiaalkosten en hoge snelheid. Als het gespoten poeder een gemengd poeder is van gips en keramiek, kan er direct en snel een mal (gipsvorm) van worden gemaakt voor het gieten van aluminium, magnesium, zink en andere non-ferrolegeringen, genaamd ZCast (Figuur 12-2) .
De vergelijking van veelgebruikte Rapid Prototyping-methoden Toepassingseffecten
Op dit moment zijn de meer populaire rapid prototyping-methoden in de werkelijke productie onder meer driedimensionale lithografie (SLA), selectieve lasersintering (SLS), fusiedepositie (FDM), laminaatproductie (LOM) en direct gieten (DSPC)). Wacht. In de afgelopen jaren hebben veel buitenlandse onderzoeksinstellingen de bovenstaande methoden vergeleken op het gebied van de kwaliteit van productiepatronen en prestaties bij het gieten van investeringen. De resultaten zijn als volgt:
- 1) De SLA-methode heeft de hoogste maatnauwkeurigheid van het patroon, gevolgd door SLS en FDM, en de LOM-methode is de laagste [4].
- 2) Oppervlakteruwheid van het patroon Het oppervlak van het patroon wordt gepolijst en afgewerkt en gemeten met een oppervlakteruwheidsmeter. De resultaten worden getoond in Tabel 12-1 [4]. Het is te zien dat de oppervlakteruwheid fijner is door de SLA- en LOM-methoden, en de FDM-methode het dikst.
- 3) Het vermogen om fijne delen te reproduceren Het vermogen van deze vier methoden om fijne delen te reproduceren werd onderzocht met een tandheugel met een tandafstand van ongeveer 3 mm als object. Als gevolg hiervan is SLA de beste en FDM de slechtste [4].
- 4) Prestaties bij het gieten van investeringen Van de bovengenoemde vier methoden is het product zelf een wasvormmethode (zoals FDM of SLS), die zich gemakkelijk kan aanpassen aan de vereisten van het investeringsgietproces en ongetwijfeld beter presteert. Hoewel patronen van hars of papier ook kunnen worden gebrand, zijn ze niet zo eenvoudig aan te passen aan de vereisten van investeringsgieten als wasvormen. Voortdurende verbeteringen zijn nodig om nadelen te voorkomen.
Vergelijking van oppervlakteruwheid van patronen
Meten Deel: | OOM | SLS | FDM | SLA |
Niveau vliegtuig | 1.5 | 5.6 | 14.5 | 0.6 |
Hellend vlak | 2.2 | 4.5 | 11.4 | 6.9 |
Verticaal vlak | 1.7 | 8.2 | 9.5 | 4.6 |
Hoewel de SLA-methode in het algemeen niet compatibel is met het investeringsgietproces, is ze populair vanwege de goede maatnauwkeurigheid en oppervlaktekwaliteit. In het buitenland, vooral in de lucht- en ruimtevaart en de militaire industrie, worden investeringsgietbedrijven veel gebruikt. Hoewel de kwaliteit van de SLS-methode iets inferieur is aan die van SLA, is deze eenvoudig aan te passen aan de procesvereisten van investeringsgieten. Daarom worden steeds meer toepassingen gebruikt bij het gieten van binnenlandse investeringen. Hoewel de FDM-methode het gemakkelijkst kan worden aangepast aan de procesvereisten van investeringsgieten, zijn de maatnauwkeurigheid en oppervlaktekwaliteit van de wasvormen niet bevredigend; terwijl de LOM-methode van acceptabele kwaliteit is, maar moeilijk aan te passen aan investeringsgieten. Daarom is het moeilijk om je aan te passen aan investeringsgieten. De promotie en toepassing van de twee methoden bij het gieten van investeringen zijn onderworpen aan bepaalde beperkingen.
Nieuwe ontwikkelingen in de toepassing van SLA en SLS bij het gieten van investeringen
1. Nieuwe lichtuithardende hars
De SLA-methode is al in 1987 gecommercialiseerd. Oorspronkelijk werd het gebruikt om fysieke modellen en prototypes met bepaalde functies te maken. In het begin van de jaren negentig werd de QuickCast-software van 1990D System Inc in de Verenigde Staten met succes ontwikkeld, waardoor de SLA rapid prototyping-machine een honingraatvormige structuur kon produceren (Figuur 3-12a) met behoud van een glad en compact uiterlijk (Figuur 3 -12b), bespaart niet alleen 3% van de vormmaterialen, maar ook wanneer de schaal wordt gebakken, stort het patroon eerst naar binnen zonder de schaal te barsten. Daarnaast ontdekte men geleidelijk aan dat ze voor lichtuithardende harsen voor het maken van matrijzen ook aan de volgende speciale eisen moeten voldoen:
- Viscositeit - als de harsviscositeit te hoog is, zal het moeilijk zijn om de resterende hars in de holte af te voeren nadat het patroon is gemaakt. Als er te veel harsresten zijn, kan de schaal tijdens het bakken nog steeds barsten, dus centrifugale scheiding is vaak nodig. Maatregelen. Bovendien is het oppervlak van het voltooide patroon ook moeilijk schoon te maken.
- Restas - dit is misschien wel de belangrijkste vereiste. Als de resterende as nadat de schaal is gebakken, zal dit niet-metalen insluitsels en andere defecten op het oppervlak van het gietstuk veroorzaken.
- · Inhoud van zware metalen elementen - dit is vooral belangrijk voor het gieten van superlegeringen. Antimoon is bijvoorbeeld een relatief veel voorkomend element in SLA-lichtuithardende harsen. Als het in de resterende as verschijnt nadat de schaal is gebakken, kan het de legering verontreinigen en zelfs ertoe leiden dat het gietstuk wordt gesloopt.
- Dimensionale stabiliteit - de grootte van het patroon moet tijdens de hele operatie stabiel blijven. Om deze reden is ook de lage vochtopname van de hars erg belangrijk.
In de afgelopen jaren heeft DSM Somos uit de Verenigde Staten met succes een nieuw type lichtuithardende hars Somos 10120 ontwikkeld, die voldoet aan de bovengenoemde hoofdeisen en zeer geliefd is bij fabrikanten van investeringsgietstukken. Dit nieuwe product is gegoten in drie verschillende precisiegietfabrieken in drie legeringen (aluminium, titanium en kobalt-molybdeenlegering) en heeft bevredigende resultaten opgeleverd.
2. Gebruik het SLA-model voor kleine batchproductie
Er zijn twee belangrijke zaken waarmee rekening moet worden gehouden bij de productie van kleine batches van precisiegietstukken met behulp van SLA-patronen: een is de maatnauwkeurigheid die het patroon en het gieten kunnen bereiken, en de andere is of de productiekosten en levertijd voordelen hebben. Verschillende precisiegietfabrieken in de Verenigde Staten, zoals Solidiform, Nu-Cast, PCC en Uni-Cast, hebben SLA-patronen gebruikt om honderden gietstukken te gieten. Na daadwerkelijke meting van de gietgrootte blijkt uit statistische analyse dat de nieuwe 11120 lichtuithardende hars, ontwikkeld door DSM Somos, is gebruikt. Met QuickCast-technologie heeft het resulterende SLA-patroon een maatafwijking van niet meer dan 50% van de giettolerantiewaarde. De afmetingen van de meeste gietstukken voldoen aan de tolerantie-eisen en het slagingspercentage is meer dan 95% (Figuur 12-4) [7].
Hoewel de kosten voor het maken van een SLA-patroon veel hoger zijn dan die voor het maken van dezelfde wasvorm, en het duurt langer, maar het is niet nodig om de profilering te ontwerpen en te vervaardigen. Daarom, wanneer een enkel stuk in kleine batches wordt geproduceerd, zijn de kosten en levertijd nog steeds voordelen. Hoe complexer het gieten, hoe duidelijker dit voordeel. Neem het complexe luchtvaartprecisiegietwerk geproduceerd door Nu-Cast als voorbeeld (Figuur 12-5) [7], de kosten voor het maken van matrijzen bedragen ongeveer 85,000 US dollar, er worden elke dag 4 wasvormen geproduceerd en de kosten van elke was schimmel (inclusief materialen en arbeid) 150 USD. Als de SLA-methode wordt toegepast, kost elk SLA-model 2846 Amerikaanse dollars, maar het is niet nodig om matrijzen te ontwerpen en te vervaardigen. Uit deze berekening, als de output minder dan 32 stuks is, zijn de kosten van het gebruik van SLA-mallen lager dan die van wasmallen; als er meer dan 32 stuks zijn, zijn de kosten hoger dan bij wasvormen (Figuur 12-6); met behulp van wasmallen duurt het 14-16 weken om mallen te ontwerpen en te vervaardigen, en de SLA-mal heeft geen mal nodig. Als de output minder is dan 87 stuks, is de levering van gietstukken bij gebruik van SLA-mallen sneller dan die van was (Figuur 12-7). Maar meer dan 87 stuks is de wasvorm sneller [7]. Een andere factor waarmee rekening moet worden gehouden, is dat als een wasvorm wordt gebruikt, wanneer het product wordt bijgewerkt, de vorm opnieuw moet worden gemaakt, wat kostbaar is; terwijl met het SLA-uiterlijk alleen het CAD-geometrische model hoeft te worden gewijzigd, wat veel gemakkelijker en sneller is dan het opnieuw maken van de mal. .
3. SLS gesinterd polystyreen poeder geïmpregneerd waspatroon;
SLS gebruikte in eerste instantie een laser om een speciaal waspoeder in een wasmal te sinteren, wat zeer geschikt is voor de proceseigenschappen van investeringsgieten. Reeds eind 1990 waren er meer dan 50 gieterijen in de Verenigde Staten, die ongeveer 3000 wasvormen produceerden en deze met succes afgieten. Produceer een verscheidenheid aan metalen gietstukken. Waspoeder is echter niet het meest ideale vormmateriaal. De sterkte van de wasvorm die ervan is gemaakt, is onvoldoende, en het is gemakkelijk te verzachten en te vervormen wanneer de temperatuur hoog is, en het is gemakkelijk te breken als de temperatuur laag is. Daarom probeerden sommige SLA-gebruikers in de Verenigde Staten begin jaren negentig waspoeder te vervangen door thermoplastische poeders zoals polystyreen (PS) of polycarbonaat (PC). Dit soort materiaal wordt in een losse en poreuze vorm gemaakt (de porositeit is meer dan 1990%), wat het risico op zwelling en barsten van de schaal tijdens het ontvormen vermindert. Nadat de schaal is gebakken, is het asgehalte minder, maar het oppervlak van het patroon is ruw. Daarom moet het patroon, nadat het is gemaakt, met de hand worden gewaxt en gepolijst om het oppervlak glad en dicht te maken. Inmiddels wordt deze methode veel toegepast in binnen- en buitenland.
Bewaar de bron en het adres van dit artikel voor herdruk:De toepassing van Rapid Prototyping-technologie bij het gieten van investeringen
Minghe Casting Company is toegewijd aan het produceren en leveren van hoogwaardige en hoogwaardige gietstukken (het assortiment metalen spuitgietonderdelen omvat voornamelijk: Dunwandig spuitgieten,Hot Chamber Spuitgieten,Koude kamer spuitgieten),Ronde Service (Die Casting Service,CNC-bewerking,Matrijzen maken, Oppervlaktebehandeling). Elk aangepast aluminium spuitgieten, magnesium of Zamak / zink spuitgieten en andere gietstukken zijn welkom om contact met ons op te nemen.
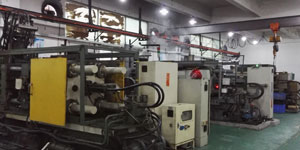
Onder controle van ISO9001 en TS 16949 worden alle processen uitgevoerd door honderden geavanceerde spuitgietmachines, 5-assige machines en andere faciliteiten, variërend van blasters tot Ultra Sonic-wasmachines. Minghe heeft niet alleen geavanceerde apparatuur, maar heeft ook professionele team van ervaren ingenieurs, operators en inspecteurs om het ontwerp van de klant waar te maken.
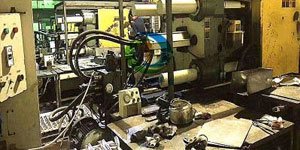
Contractfabrikant van spuitgietwerk. Mogelijkheden zijn onder meer koude kamer aluminium spuitgietonderdelen vanaf 0.15 lbs. tot 6 lbs., snelwissel instellen en machinaal bewerken. Diensten met toegevoegde waarde omvatten polijsten, trillen, ontbramen, stralen, schilderen, plateren, coaten, assembleren en bewerken. Materialen waarmee gewerkt is, zijn legeringen zoals 360, 380, 383 en 413.
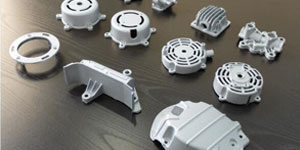
Hulp bij ontwerp van spuitgieten van zink/concurrent engineering. Custom fabrikant van precisie gegoten zink. Miniatuurgietstukken, hogedrukgietstukken, multi-slide gietstukken, conventionele gietstukken, eenheidsmatrijs en onafhankelijke spuitgietstukken en holteverzegelde gietstukken kunnen worden vervaardigd. Gietstukken kunnen worden vervaardigd in lengtes en breedtes tot 24 inch met een tolerantie van +/- 0.0005 inch.
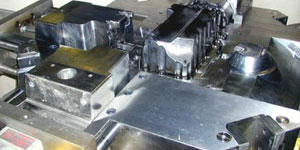
ISO 9001: 2015 gecertificeerde fabrikant van gegoten magnesium. Mogelijkheden zijn onder hoge druk spuitgieten van magnesium tot 200 ton hete kamer en 3000 ton koude kamer, gereedschapsontwerp, polijsten, gieten, machinale bewerking, poeder- en vloeistofverven, volledige QA met CMM-mogelijkheden , montage, verpakking & levering.
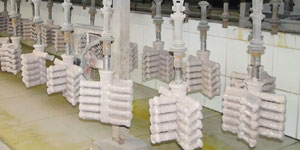
ITAF16949 gecertificeerd. Extra castingservice omvat: investering gieten,zandgieten,Zwaartekracht gieten, Verloren schuimafgietsel,Centrifugaal gieten,Vacuümgieten,Permanent vormgieten,. Mogelijkheden zijn onder meer EDI, technische assistentie, solide modellering en secundaire verwerking.
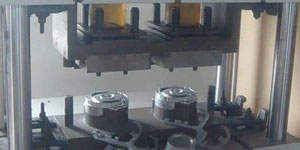
Gietindustrieën Casestudy's over onderdelen voor: auto's, fietsen, vliegtuigen, muziekinstrumenten, waterscooters, optische apparaten, sensoren, modellen, elektronische apparaten, behuizingen, klokken, machines, motoren, meubels, sieraden, mallen, telecom, verlichting, medische apparaten, fotografische apparaten, Robots, sculpturen, geluidsapparatuur, sportuitrusting, gereedschap, speelgoed en meer.
Wat kunnen we u hierna helpen doen?
∇ Ga naar de startpagina voor Spuitgieten China
→Gietonderdelen- Zoek uit wat we hebben gedaan.
→Gerangschikte tips over Spuitgietdiensten
By Minghe Die Casting Fabrikant: |Categorieën: Handige artikelen |Materiaal Tags: Aluminium gieten, Zink gieten, Magnesium gieten, Titanium gieten, Gieten van roestvrij staal, Messing gieten,Brons gieten,Video casten,Geschiedenis van ons bedrijf,Aluminium spuitgieten |Reacties uitgeschakeld