Zeer sterke smelttechnologie van grijs gietijzer
Dit artikel laat zien hoe u hoogwaardige technologie voor het smelten van grijs gietijzer kunt verkrijgen onder de voorwaarden van een hoger koolstofequivalent en betere prestatie-eisen in het smeltproces van elektrische ovens, en hoe u de sporenelementen van het materiaal kunt beheersen.
Steekwoorden: grijs gietijzer, koolstofequivalent, mechanische eigenschappen, verwerkingseigenschappen, sporenelementen
De traditionele controlerichting voor het smelten van grijs gietijzer is koolstofarm gietijzer met hoge sterkte (C: 2.7 ~ 3.0, Si: 2.0 ~ 2.3, Mn: 0.9 ~ 1.3). Hoewel dergelijke materialen kunnen voldoen aan de eisen van materiële mechanische eigenschappen, zijn hun gietprestaties en verwerking slecht. Met de marktontwikkeling en -uitbreiding van het bedrijf worden steeds meer gietproducten met een hoge moeilijkheidsgraad en hoge technische kwaliteitseisen opgenomen in de MINGHE-productievolgorde, vooral wanneer MINGHE het smeltproces van de elektrische oven met elektrische frequentie gebruikt om het smeltproces van de koepel te vervangen.
Het verkrijgen van hoogwaardig gietijzer met een hoog koolstofgehalte onder smeltomstandigheden in elektrische ovens om aan de eisen van de klant te voldoen, was in die tijd een onderzoeksonderwerp. Dit artikel beschrijft de productietechnologie van hoogwaardig grijs gietijzer onder smeltomstandigheden in elektrische ovens.
De factoren die de materiële prestaties beïnvloeden
1.1 Het effect van koolstofequivalent op materiaaleigenschappen
De belangrijkste factoren die de eigenschappen van grijs gietijzer bepalen, zijn de grafietmorfologie en de eigenschappen van de metaalmatrix. Wanneer het koolstofequivalent (CE=C+1/3Si) hoog is, neemt de hoeveelheid grafiet toe en verslechtert de vorm van grafiet wanneer de incubatieomstandigheden niet goed zijn of wanneer er sporen van schadelijke elementen aanwezig zijn. Dergelijk grafiet vermindert het effectieve oppervlak van de metalen matrix dat de belasting kan dragen en veroorzaakt spanningsconcentratie bij het dragen van de belasting, zodat de sterkte van de metalen matrix niet normaal kan worden gebruikt, waardoor de sterkte van het gietijzer wordt verminderd. Van de materialen heeft perliet een goede sterkte en hardheid, terwijl ferriet een zachtere basis en lagere sterkte heeft. Naarmate de hoeveelheid C en Si toeneemt, zal de hoeveelheid perliet afnemen en de hoeveelheid ferriet toenemen. Daarom zal de toename van het koolstofequivalent van invloed zijn op de treksterkte van gietijzeren gietstukken en de hardheid van de gieteenheid in zowel de grafietvorm als de matrixstructuur. Bij de controle van het smeltproces is de controle van het koolstofequivalent een zeer belangrijke factor om de materiaalprestaties op te lossen.
1.2 De invloed van legeringselementen op materiaaleigenschappen
De legeringselementen in grijs gietijzer verwijzen voornamelijk naar Mn, Cr, Cu, Sn, Mo en andere elementen die de vorming van perliet bevorderen. De inhoud van deze elementen heeft direct invloed op de inhoud van perliet. Tegelijkertijd wordt het door de toevoeging van legeringselementen tot op zekere hoogte verfijnd. De toevoeging van grafiet vermindert of verdwijnt zelfs de hoeveelheid ferriet in de matrix, terwijl perliet tot op zekere hoogte wordt verfijnd en het ferriet erin een vaste oplossing is die wordt versterkt door een bepaalde hoeveelheid legeringselementen, zodat het gietijzer altijd een hogere sterkte heeft. Bij de beheersing van het smeltproces is ook de beheersing van de legering een belangrijk middel.
1.3 De invloed van de ladingsverhouding op materialen
In het verleden hebben we er altijd op aangedrongen dat zolang de chemische samenstelling voldoet aan de vereisten van de specificatie, we een weergave zouden moeten kunnen verkrijgen die voldoet aan de standaard mechanische eigenschappen van het materiaal, maar in feite ziet deze visie alleen de conventionele chemische samenstelling en negeert sommige legeringselementen en schadelijke elementen daarin. De rol van. Ruwijzer is bijvoorbeeld de belangrijkste bron van Ti, dus de gebruikte hoeveelheid ruwijzer heeft direct invloed op het gehalte aan Ti in het materiaal en heeft een grote invloed op de mechanische eigenschappen van het materiaal. Evenzo is schroot de bron van veel legeringselementen, dus de hoeveelheid schroot heeft een zeer direct effect op de mechanische eigenschappen van gietijzer. Vroeger, toen de elektrische oven in gebruik werd genomen, gebruikten we altijd de laadverhouding van de koepeloven (ruwijzer: 25~35%, schroot: 30~35%). Hierdoor waren de mechanische eigenschappen (treksterkte) van het materiaal erg laag. Wanneer de hoeveelheid gebruikt staal van invloed is op de prestaties van gietijzer, is het probleem na tijdige aanpassing van de hoeveelheid schroot snel opgelost. Daarom is schroot een zeer belangrijke controleparameter in het smeltcontroleproces. Daarom heeft de ladingsverhouding een directe invloed op de mechanische eigenschappen van gietijzermaterialen en is dit de focus van de smeltcontrole.
1.4 De invloed van sporenelementen op materiaaleigenschappen
In het verleden besteedden we alleen aandacht aan de invloed van de conventionele vijf hoofdelementen op de kwaliteit van gietijzer tijdens het smeltproces, terwijl het effect van andere sporenelementen slechts een kwalitatief begrip was, maar zelden kwantitatief werden geanalyseerd en besproken. Als gevolg van de impact van de vooruitgang van de giettechnologie wordt de afgelopen jaren de smeltapparatuur voortdurend bijgewerkt en zijn koepels geleidelijk vervangen door elektrische ovens. Hoewel het smelten in een elektrische oven onvergelijkbare voordelen heeft bij het smelten van koepels, verliest het smelten in een elektrische oven ook enkele van de voordelen van het smelten van koepels, dus de invloed van sommige sporenelementen op gietijzer wordt ook weerspiegeld. Omdat de metallurgische reactie in de koepel erg sterk is, de lading zich in een sterk oxiderende atmosfeer bevindt, wordt het meeste geoxideerd en afgevoerd met de slak, slechts een klein deel zal in het gesmolten ijzer achterblijven, dus sommige hebben een nadelig effect op het gieten. Door het metallurgische proces van de koepel hebben de sporenelementen over het algemeen geen nadelig effect op gietijzer. Tijdens het smeltproces van de koepel lost een deel van de stikstof in de cokes en stikstof (N2) in de lucht bij hoge temperaturen in de vorm van atomen op in het gesmolten ijzer, waardoor het stikstofgehalte in het gesmolten ijzer relatief hoog is.
Volgens de statistieken waren de afvalproducten veroorzaakt door een hoog loodgehalte en het afgedankte gesmolten ijzer sinds de ingebruikname van de elektrische oven niet minder dan 100 ton, omdat het loodgehalte te hoog was om te worden aangepast, en het aantal niet-gekwalificeerde producten als gevolg van onvoldoende stikstofgehalte was ook vrij hoog, waardoor het bedrijf grote economische verliezen leed.
Op basis van onze jarenlange ervaring en theorie met het smelten van elektrische ovens, geloof ik dat de belangrijkste sporenelementen in het smeltproces van elektrische ovens voornamelijk N, Pb en Ti zijn. De effecten van deze elementen op grijs gietijzer zijn hoofdzakelijk als volgt:
Leiden
Wanneer het loodgehalte in het gesmolten ijzer hoog is (>20PPm), vooral bij interactie met het hogere waterstofgehalte, is het gemakkelijk om Widmanstatten-grafiet te vormen in gietstukken met dikke secties. Dit komt omdat het harszand goede thermische isolatie-eigenschappen heeft en het gesmolten ijzer langzamer afkoelt in de mal (deze neiging is duidelijker voor dikke delen), het gesmolten ijzer blijft langer in vloeibare toestand en het stollen van het gesmolten ijzer ligt dichter bij de stollingstoestand in de evenwichtstoestand vanwege de werking van lood en waterstof. Wanneer dit type gietstuk wordt gestold en blijft afkoelen, zal de koolstof in het austeniet neerslaan en secundair grafiet in vaste toestand worden. Onder normale omstandigheden verdikt het secundaire grafiet alleen de eutectische grafietvlokken, wat geen grote invloed zal hebben op de mechanische eigenschappen. Wanneer het stikstof- en waterstofgehalte echter hoog is, zal de oppervlakte-energie van grafiet op hetzelfde vaste kristalvlak van austeniet worden verminderd en zal het secundaire grafiet opgroeien langs een bepaald kristalvlak van austeniet en zich uitstrekken tot in de metaalmatrix. Observeer onder een microscoop. Aan de zijkant van de vlok groeien veel kleine braamachtige grafietvlokken, algemeen bekend als grafietharen, wat de reden is voor de vorming van Widman's grafiet. Het aluminium in gietijzer kan het vloeibare ijzer bevorderen om waterstof te absorberen en zijn waterstofgehalte te verhogen. Daarom heeft aluminium ook een indirect effect op de vorming van Widmanstatten-grafiet.
Wanneer Widmanstatten-grafiet in gietijzer verschijnt, worden de mechanische eigenschappen ervan sterk beïnvloed, vooral de sterkte en hardheid, die in ernstige gevallen met ongeveer 50% kunnen worden verminderd.
Widman's grafiet heeft de volgende metallografische kenmerken:
- 1) Op de 100-voudige microfoto zijn er veel kleine doornachtige grafietvlokken bevestigd aan de grove grafietschilfer, die Widmanstatten-grafiet is.
- 2) De relatie van het gewone kristallijne grafiet is met elkaar verbonden.
- 3) Wanneer het Widmanstatten-grafietnetwerk zich bij kamertemperatuur in de matrix uitstrekt, wordt het het kwetsbare oppervlak van de matrix, wat de mechanische eigenschappen van grijs gietijzer aanzienlijk zal verminderen. Maar vanuit de dwarsdoorsnede strekken de breukscheuren zich nog steeds uit langs het co-chipachtige grafiet.
Stikstof
Een juiste hoeveelheid stikstof kan grafietkiemvorming bevorderen, perliet stabiliseren, de structuur van grijs gietijzer verbeteren en de prestaties van grijs gietijzer verbeteren.
Stikstof heeft twee belangrijke invloeden op grijs gietijzer. De ene is de invloed op de vorm van grafiet en de andere is de invloed op de matrixstructuur. Het effect van stikstof op de morfologie van grafiet is een zeer ingewikkeld proces. Komt vooral tot uiting in: de invloed van de adsorptielaag op het grafietoppervlak en de invloed van de grootte van de eutectische groep. Aangezien stikstof bijna onoplosbaar is in grafiet, wordt stikstof continu geadsorbeerd aan de voorkant van de grafietgroei en aan beide zijden van grafiet tijdens het eutectische stollingsproces, wat resulteert in een toename van de omringende grafietconcentratie tijdens het precipitatieproces, vooral wanneer grafiet zich uitstrekt tot gesmolten ijzer. Aan de punt beïnvloedt het de groei van grafiet op het vloeistof-vaste raakvlak. Tijdens het eutectische groeiproces is er een significant verschil in de verdeling van de stikstofconcentratie aan de punt en beide zijden van de grafietplaat. De adsorptielaag van stikstofatomen op het grafietoppervlak kan de diffusie van koolstofatomen naar het grafietoppervlak belemmeren. Wanneer de stikstofconcentratie van het grafietfront hoger is dan die van de twee zijden, wordt de groeisnelheid van het grafiet in de lengterichting verminderd. Daarentegen wordt de laterale groei gemakkelijker, met als gevolg dat het grafiet korter en dikker wordt. Tegelijkertijd, aangezien er altijd defecten zijn in het grafietgroeiproces, wordt een deel van de stikstofatomen geadsorbeerd op de defectpositie en kan niet diffunderen, en zal de korrelgrens asymmetrisch hellend zijn aan de voorkant van de grafietgroei, en de rest zal nog steeds in de oorspronkelijke richting groeien. Grafiet produceert vertakkingen en de toename van grafietvertakkingen is nog een reden waarom grafiet korter wordt. Op deze manier wordt door de verfijning van de grafietstructuur het splijtende effect op de matrixstructuur verminderd, wat bevorderlijk is voor de verbetering van de prestaties van gietijzer.
Het effect van stikstof op de matrixstructuur is dat het een perliet stabiliserend element is. De toename van het stikstofgehalte verlaagt de eutectoïde transformatietemperatuur van gietijzer. Daarom kan, wanneer een bepaalde hoeveelheid stikstof in grijs gietijzer aanwezig is, de mate van onderkoeling van de eutectoïde transformatie worden verhoogd, waardoor perliet wordt verfijnd. Aan de andere kant, omdat de atomaire straal van stikstof kleiner is dan die van koolstof en ijzer, kan het worden gebruikt als interstitiële atomen om op te lossen in ferriet en cementiet, waardoor het kristalrooster wordt vervormd. Om de bovenstaande twee redenen kan stikstof een versterkend effect hebben op de matrix.
Hoewel stikstof de prestaties van grijs gietijzer kan verbeteren, zullen stikstofporiën en microscheurtjes worden gegenereerd als het een bepaalde hoeveelheid overschrijdt, zoals weergegeven in figuur 2, dus de controle van stikstof moet binnen een bepaald bereik worden geregeld. Over het algemeen 70-120PPm, wanneer het 180PPm overschrijdt, zullen de prestaties van gietijzer sterk dalen.
Ti is een schadelijk element in gietijzer. De reden is dat titanium een sterke affiniteit heeft met stikstof. Wanneer het gehalte aan titanium in grijs gietijzer hoog is, is dat niet gunstig voor de versterkende werking van stikstof. Ten eerste vormt het een TiN-verbinding met stikstof, die vermindert. In feite is het juist omdat deze vrije stikstof een vaste-oplossingsversterkend effect heeft op grijs gietijzer. Daarom heeft het titaniumgehalte indirect invloed op de prestaties van grijs gietijzer.
Smeltcontroletechnologie
2.1 Selectie van materiaal chemische samenstelling
Door de bovenstaande analyse is de controle van de chemische samenstelling erg belangrijk in de smelttechnologie en vormt het de basis van de smeltcontrole. Daarom is een redelijke chemische samenstelling de basis voor het waarborgen van de prestaties van het materiaal. Gewoonlijk omvat de samenstellingscontrole van hoogwaardig gietijzer (treksterkte ≥300N/mm2) voornamelijk etc. C, Si, Mn, P, S, Cu, Cr, Pb, N
2.3 Controletechniek van sporenelementen
In de eigenlijke procescontrole wordt op basis van de analyse van de lading bevestigd dat de bron van lood voornamelijk schrootstaal is. Daarom is de controle van lood in de grondstof voornamelijk om de loodinsluitsels in het schroot te beheersen, en het loodgehalte wordt meestal onder de 15 ppm gehouden. Als het loodgehalte in het ruwe gesmolten ijzer> 20 ppm is, moet tijdens de incubatiebehandeling een speciale verslechteringsbehandeling worden uitgevoerd.
Aangezien Ti voornamelijk is afgeleid van ruwijzer, is de controle van Ti voornamelijk om ruwijzer te beheersen. Enerzijds is het nodig om bij de inkoop strenge eisen te stellen aan het Ti-gehalte in ruwijzer. Gewoonlijk moet het titaniumgehalte van ruwijzer zijn: Ti <0.8%, en het andere aspect is om de gebruikshoeveelheid in de tijd aan te passen aan het titaniumgehalte van ruwijzer.
Komt voornamelijk uit herkoolstofmaterialen en schroot, dus de controle van N is voornamelijk om herkoolstofmaterialen en schroot te beheersen. Zoals hierboven vermeld, hebben te laag en te hoog echter een negatieve kant aan de prestaties van grijs gietijzer, dus de inhoud van N Het regelbereik is over het algemeen: 70 ~ 120ppm, maar de inhoud van N moet redelijk overeenkomen met de inhoud van Ti. Over het algemeen is de relatie tussen N en Ti: N:Ti=1:3.42, dat wil zeggen, 0.01% van Ti kan 30ppm stikstof absorberen. De algemeen aanbevolen hoeveelheid stikstof tijdens productie is: N=0.006~0.01+Ti/3.42.
2.4 Besturingstechnologie van het smeltproces
1) Inentingstechnologie
Het doel van inentingsbehandeling is om grafitisatie te bevorderen, de neiging tot witte mond te verminderen en de gevoeligheid van het eindoppervlak te verminderen; controleer de morfologie van grafiet en elimineer onderkoeld grafiet; verhoog op passende wijze het aantal eutectische clusters en bevorder de vorming van vlokperliet, om de sterkteprestaties van gietijzer en andere prestatiedoeleinden te verbeteren.
De invloed van de temperatuur van gesmolten ijzer op de inenting en het beheersen van de temperatuur van gesmolten ijzer hebben een significante invloed op de inenting. Door de oververhittingstemperatuur van gesmolten ijzer binnen een bepaald bereik te verhogen en deze gedurende een bepaalde periode vast te houden, kunnen de onopgeloste grafietdeeltjes in het gesmolten ijzer blijven, dat volledig in het gesmolten ijzer kan worden opgelost om de genetische invloed van ruwijzer te elimineren en het inentingseffect van de inoculant volledig te spelen, het vruchtbaarheidsvermogen van gesmolten ijzer te verbeteren. Bij de procesregeling wordt de oververhittingstemperatuur verhoogd tot 1500 ~ 1520 ℃ en de inentingstemperatuur wordt geregeld op 1420 ~ 1450 ℃.
De deeltjesgrootte van het entmiddel is een belangrijke indicator van de status van het entmiddel en heeft een grote invloed op het effect van het inoculant. Als de deeltjesgrootte te fijn is, is het gemakkelijk om in de gesmolten slak te dispergeren of te oxideren en zijn effect te verliezen. Als de deeltjesgrootte te groot is, zal het inoculant niet smelten of volledig oplossen. Het kan niet alleen zijn inentingseffect niet volledig uitoefenen, maar het veroorzaakt ook segregatie, harde plekken, onderkoeld grafiet en andere defecten. Daarom moet de deeltjesgrootte van het inoculant zoveel mogelijk binnen 2 ~ 5 mm worden geregeld. Zorg voor het incubatie-effect.
Bij de procescontrole wordt het inoculatieproces voornamelijk geënt in de incubatietank, zodat het gieten van een pakket gietstukken in principe kan worden voltooid voordat de incubatie afneemt. Maar voor relatief grote onderdelen en onderdelen die met een dubbele gietpan zijn gegoten, kan het niet aan de eisen voldoen. Daarom wordt de late inentingsmethode toegepast: dat wil zeggen, de drijvende siliciuminenting wordt uitgevoerd in de gietpan voordat het gietstuk wordt gegoten (inentingshoeveelheid is 0.1%), wat de afname van de inoculatie vermindert of niet doet en het inentingseffect verbetert.
2) Legeringsbehandeling
Legeringsbehandeling voegt een kleine hoeveelheid legeringselementen toe aan gewoon gietijzer om de mechanische eigenschappen van grijs gietijzer te verbeteren. Bij de controle van het smeltproces is de toevoeging van legeringen voornamelijk voor de onderdelen die klanten nodig hebben om te worden geblust en de onderdelen met relatief dikke geleiderails, de belangrijkste toegevoegde legeringselementen en de hoeveelheid toevoeging.
Dit zorgt tot op zekere hoogte voor afname van de prestatie door de verhoging van de CE-waarde, en voor de afgeschrikte delen wordt de hardbaarheid tijdens het afschrikken verbeterd. Zorg voor de afschrikdiepte.
Tijdens het toevoer- en smeltproces is de toevoervolgorde van de belangrijkste controle in dit stadium om het schroot, mechanisch ijzer en ruwijzer aan te voeren in de volgorde van prioriteit. Om het verbrandingsverlies van legeringselementen te verminderen, moet de ferrolegering aan het einde worden toegevoegd. Wanneer het koude materiaal volledig is verwijderd, wordt de temperatuur verhoogd tot 1450 ℃. Dat is punt A. Als deze lager is dan 1450°C, bestaat het risico dat de recarburizer of ferrolegering onvolledig oplost.
In paragrafen AB moeten de volgende behandelingen worden uitgevoerd:
- Temperatuurmeting;
- Slakken uitmesten;
- Bemonstering en analyse van chemische samenstelling;
- Analyseer conventionele elementen en sporenelementen met thermische spectrometer;
- Neem het driehoeksproefstuk om de CW-waarde te meten;
- Na het aanpassen van het gesmolten ijzer aan de hand van verschillende testresultaten, blijft u gedurende 10 minuten stroom leveren en neemt u vervolgens opnieuw monsters en analyseert u het. Nadat u heeft bevestigd dat alle gegevens normaal zijn, gaat u door met het verhogen van de temperatuur tot ongeveer 1500°C, dat wil zeggen punt C. Laat het gesmolten ijzer in het CD-gedeelte 5 tot 10 minuten staan en neem dan een driehoekig proefstuk om de CW-waarde te testen. Na het meten van de temperatuur bereidt u het strijkijzer voor op het tappen.
Driehoekige proefstukcontrole
Bepaal voor verschillende soorten het regelbereik van de witte mond (CW) van verschillende driehoekstestblokken en bepaal de kwaliteit van gesmolten ijzer in combinatie met de samenstellingsanalyse voor de oven.
Conclusie
De bovengenoemde grijze gietijzeren smelttechnologie is 8 jaar met succes toegepast in CSMF van 1996 tot 2003. Het CE van Castings wordt gecontroleerd onder het uitgangspunt van 3.6 ~ 3.9, of het de treksterkte-index is of de fysieke hardheidsindex (vooral onderdeel van de hardheid van de rail van de gidstrail van machinegereedschap is een grote verbetering van de casting van de casting van de casting van de rail van de rail van de gids. als volgt:
- 3.1 Controle van de chemische samenstelling van materialen
- 3.2 Bepaling van de ladingsverhouding
- 3.3 Controletechniek van sporenelementen
- 3.4 Beheersing van het inentingsbehandelingsproces
- 3.5 Legeringsbehandeling
- 3.6 Temperatuurbeheersing van het smeltproces
- 3.7 Controle driehoek proefstuk
Bewaar de bron en het adres van dit artikel voor herdruk: Zeer sterke smelttechnologie van grijs gietijzer
Minge Spuitgietbedrijf zijn toegewijd aan het vervaardigen en leveren van hoogwaardige en hoogwaardige gietstukken (het assortiment metalen spuitgietonderdelen omvat voornamelijk: Dunwandig spuitgieten,Hot Chamber Spuitgieten,Koude kamer spuitgieten),Ronde Service (Die Casting Service,CNC-bewerking,Matrijzen maken, Oppervlaktebehandeling). Elk aangepast aluminium spuitgieten, magnesium of Zamak / zink spuitgieten en andere gietstukken zijn welkom om contact met ons op te nemen.
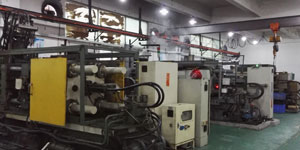
Onder controle van ISO9001 en TS 16949 worden alle processen uitgevoerd door honderden geavanceerde spuitgietmachines, 5-assige machines en andere faciliteiten, variërend van blasters tot Ultra Sonic-wasmachines. Minghe heeft niet alleen geavanceerde apparatuur, maar heeft ook professionele team van ervaren ingenieurs, operators en inspecteurs om het ontwerp van de klant waar te maken.
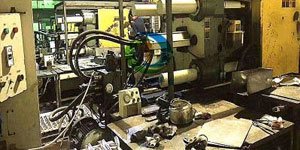
Contractfabrikant van spuitgietwerk. Mogelijkheden zijn onder meer koude kamer aluminium spuitgietonderdelen vanaf 0.15 lbs. tot 6 lbs., snelwissel instellen en machinaal bewerken. Diensten met toegevoegde waarde omvatten polijsten, trillen, ontbramen, stralen, schilderen, plateren, coaten, assembleren en bewerken. Materialen waarmee gewerkt is, zijn legeringen zoals 360, 380, 383 en 413.
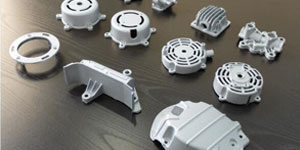
Hulp bij ontwerp van spuitgieten van zink/concurrent engineering. Custom fabrikant van precisie gegoten zink. Miniatuurgietstukken, hogedrukgietstukken, multi-slide gietstukken, conventionele gietstukken, eenheidsmatrijs en onafhankelijke spuitgietstukken en holteverzegelde gietstukken kunnen worden vervaardigd. Gietstukken kunnen worden vervaardigd in lengtes en breedtes tot 24 inch met een tolerantie van +/- 0.0005 inch.
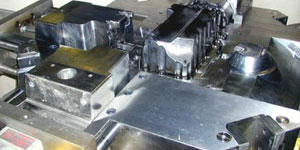
ISO 9001: 2015 gecertificeerde fabrikant van gegoten magnesium. Mogelijkheden zijn onder hoge druk spuitgieten van magnesium tot 200 ton hete kamer en 3000 ton koude kamer, gereedschapsontwerp, polijsten, gieten, machinale bewerking, poeder- en vloeistofverven, volledige QA met CMM-mogelijkheden , montage, verpakking & levering.
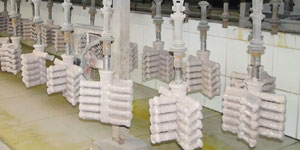
ITAF16949 gecertificeerd. Extra castingservice omvat: investering gieten,zandgieten,Zwaartekracht gieten, Verloren schuimafgietsel,Centrifugaal gieten,Vacuümgieten,Permanent vormgieten,. Mogelijkheden zijn onder meer EDI, technische assistentie, solide modellering en secundaire verwerking.
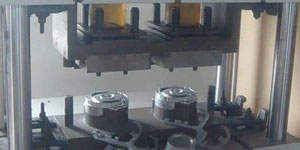
Gietindustrieën Casestudy's over onderdelen voor: auto's, fietsen, vliegtuigen, muziekinstrumenten, waterscooters, optische apparaten, sensoren, modellen, elektronische apparaten, behuizingen, klokken, machines, motoren, meubels, sieraden, mallen, telecom, verlichting, medische apparaten, fotografische apparaten, Robots, sculpturen, geluidsapparatuur, sportuitrusting, gereedschap, speelgoed en meer.
Wat kunnen we u hierna helpen doen?
∇ Ga naar de startpagina voor Spuitgieten China
→Gietonderdelen- Zoek uit wat we hebben gedaan.
→Gerangschikte tips over Spuitgietdiensten
By Minghe Die Casting Fabrikant: |Categorieën: Handige artikelen |Materiaal Tags: Aluminium gieten, Zink gieten, Magnesium gieten, Titanium gieten, Gieten van roestvrij staal, Messing gieten,Brons gieten,Video casten,Geschiedenis van ons bedrijf,Aluminium spuitgieten |Reacties uitgeschakeld