Verschillende factoren die de maatvastheid van investeringsgietstukken beïnvloeden
Het continu verbeteren van de maatnauwkeurigheid van investeringsgietwerk en het verminderen van afvalproducten veroorzaakt door overmaat is altijd een van de belangrijkste doelen geweest die door investeringsgietarbeiders in binnen- en buitenland worden nagestreefd.
1. Dimensionele stabiliteit van investeringsafgietsels
1. Dimensionele stabiliteit van wasmodel en zijn beïnvloedende factoren
In de meeste gevallen fluctueert de maat van de wasmal sterk als de maat van het gietstuk fluctueert, en er zijn een paar uitzonderingen. Over het algemeen is de groottefluctuatie van de wasvorm verantwoordelijk voor 10% tot 70% van de groottefluctuatie van het gietstuk.
De parameters van het vormproces hebben een beslissende invloed op de vormvastheid van de wasvorm. De belangrijkste factoren zijn als volgt:
(1) Perstemperatuur was
Verschillende vormmaterialen hebben verschillende prestaties vanwege de invloed van de wasperstemperatuur. Wanneer vormmaterialen op wasbasis worden gebruikt, is de wasperstemperatuur zeer gevoelig voor de invloed van vormvastheid van wasvormen, terwijl vormmaterialen op harsbasis minder invloed hebben.
(2) Injectiedruk
Wanneer de druk klein is, neemt de krimpsnelheid van de wasvorm aanzienlijk af wanneer de druk toeneemt. Nadat de druk echter tot op zekere hoogte is verhoogd (≥1.6 MPa), heeft de druk bijna geen effect op de grootte van de wasvorm. Het is geen wonder dat buitenlandse testresultaten vaak concluderen dat "de druk niets te maken heeft met de grootte van de wasvorm", maar de indruk van veel binnenlandse bedrijven is niet helemaal hetzelfde.
(3) Stroomsnelheid
De stroomsnelheid van het vormmateriaal kan op de volgende twee manieren worden gewijzigd, maar de invloed op de grootte van de wasvorm is niet hetzelfde:
·Door de instelling van de stroomsnelheid van de waspers te veranderen, heeft deze methode weinig effect op de krimp van de wasvorm. Het heeft echter een belangrijke invloed op de vulling en oppervlaktekwaliteit van dunwandige onderdelen met complexe vormen of wasvormen met kernen.
·Deze methode heeft een grote invloed door de dwarsdoorsnede van de wasinjectiepoort te veranderen, omdat het vergroten van de dwarsdoorsnede van de wasinjectiepoort niet alleen de wasperstemperatuur kan verlagen, maar ook de stolling kan verlengen tijd van het vormmateriaal bij de wasinjectiepoort, waardoor de verdichting van de wasvorm toeneemt. De mate van krimp en oppervlaktekrimp worden verminderd.
(4) Injectietijd
De zogenaamde injectietijd omvat hier drie tijdsperioden van vullen, verdichten en onderhouden. Vultijd verwijst naar de tijd die het vormmateriaal nodig heeft om de vormholte te vullen; verdichting verwijst naar de tijd vanaf het vullen van het vormstuk tot het sluiten van het wasinjectiemondstuk; en vasthouden verwijst naar de tijd vanaf het sluiten van het wasinjectiemondstuk tot het uitwerpen van de vorm.
De injectietijd heeft een significant effect op de krimpsnelheid van de wasvorm. Dit komt omdat er meer vormmateriaal in de holte kan worden geperst door de injectietijd te verlengen, en de wasvorm zal meer worden verdicht, waardoor de krimpsnelheid wordt verminderd. Het gewicht van het wasmodel neemt toe met de langere verdichtingstijd. De verdichtingstijd moet geschikt zijn. Als de verdichtingstijd te lang is, is het vormmateriaal bij de wasinjectiepoort volledig gestold en zal de verdichting niet werken. Uit figuur 4 blijkt ook dat wanneer de injectietijd kort is (15-25 s), de wasperstemperatuur stijgt en de krimpsnelheid toeneemt; maar wanneer de injectietijd wordt verlengd tot 25-35s (onder de premisse dat de vultijd constant blijft, is de werkelijke Het bovenstaande is om de verdichtingstijd te verlengen) wordt de invloed van de wasperstemperatuur kleiner; wanneer de injectietijd toeneemt tot meer dan 35 seconden, zal de tegenovergestelde situatie optreden, dat wil zeggen, als de wasperstemperatuur stijgt, zal in plaats daarvan de krimpsnelheid van de wasvorm afnemen. Dit fenomeen kan worden verklaard doordat het verhogen van de temperatuur van het vormmateriaal en het verlengen van de verdichtingstijd hetzelfde effect hebben als het verhogen van de mate van verdichting van de wasvorm.
(5) Giettemperatuur en waspersapparatuur
De vormtemperatuur is hoog, de wasvorm koelt langzaam af en de krimpsnelheid neemt toe. Dit komt doordat de wasvorm zich nog in het persgieten bevindt voordat de vorm wordt uitgeworpen en de krimp beperkt is, maar nadat de vorm is uitgeworpen, kan deze vrij krimpen. Daarom, als de temperatuur van de wasvorm hoog is wanneer de vorm wordt losgelaten, zal de uiteindelijke krimpsnelheid groot zijn en vice versa zal de krimpsnelheid klein zijn.
Op dezelfde manier kan het koelsysteem van de waspers een impact hebben van ongeveer 0.3% op de grootte van de wasvorm.
Ten slotte is het de moeite waard om te benadrukken dat bij het gebruik van op was gebaseerde vormmaterialen, waspasta een driefasig coëxistentiesysteem is van vast, vloeibaar en gas. De volumeverhouding tussen de drie fasen heeft een grote invloed op de grootte van de wasvorm. De proportionele relatie tussen deze drie kan in de daadwerkelijke productie niet worden gecontroleerd, wat ook een belangrijke reden is voor de slechte maatvastheid van wasvormen met op was gebaseerde vormmaterialen.
2. De invloed van het schaalmateriaal en het maakproces van de schaal op de vormvastheid van gietstukken
De invloed van de vormschaal op de grootte van het gietstuk wordt voornamelijk veroorzaakt door de thermische uitzetting en thermische vervorming (kruip bij hoge temperatuur) van de vormschaal tijdens het bakken, en de beperking (obstructie) van de vormschaal op de koelkrimp van de gieten.
(1) Thermische uitzetting van de schaal
Hangt voornamelijk af van het schaalmateriaal. Verschillende vuurvaste materialen hebben verschillende expansiesnelheden. Van de veelgebruikte vuurvaste materialen heeft gesmolten silica de kleinste uitzettingssnelheid, gevolgd door aluminiumsilicaat en is silica de grootste en ongelijke. Na het testen is vastgesteld dat de schaal van aluminiumsilicaat kan worden verwarmd van kamertemperatuur tot 1000 ℃, de schaal kan ongeveer 0.25% uitzetting produceren, wat een klein deel van de totale krimp van de gietmaat verklaart. Daarom, als dergelijke vuurvaste materialen worden gebruikt, de schaal Het heeft een betere maatvastheid, zoals gesmolten silica ongetwijfeld beter zal zijn. Als er echter silica wordt gebruikt, fluctueert de grootte van de schaal sterk.
(2) Thermische vervorming (kruip bij hoge temperatuur)
Een schaal die bijvoorbeeld waterglas als bindmiddel gebruikt, heeft bij hoge temperaturen boven 1000 °C een aanzienlijk grotere kruipgraad dan die van silicasol en ethylsilicaatschalen. Hoewel het gesmolten korund zelf een hoge vuurvastheid heeft, kan door de aanwezigheid van onzuiverheden zoals natriumoxide de granaatvuurtemperatuur hoger dan 1000 ℃ ook kruip veroorzaken, wat resulteert in een slechte dimensionele stabiliteit.
(3) De beperking van de vormschaal op de krimp van het gietstuk - de terugtrekking en inklapbaarheid van de vormschaal Dit hangt ook voornamelijk af van het materiaal van de vormschaal.
Samenvattend spelen vuurvaste materialen een grote rol in de invloed van de schaal op de maatfluctuatie van het gietstuk, maar de rol van het bindmiddel kan niet worden genegeerd. De impact van het schelpenmaakproces is daarentegen klein.
3. De invloed van spanning veroorzaakt door ongelijkmatige afkoeling van gietstukken op de maatvastheid
De afkoelsnelheid van elk onderdeel van het gietstuk (inclusief het poortsysteem) is anders, wat thermische spanning genereert en het gietstuk vervormt, waardoor de maatvastheid wordt aangetast. Dit komt vaak voor in de daadwerkelijke productie. Het verminderen van de afkoelsnelheid van gietstukken en het verbeteren van de combinatie van hardlopers zijn effectieve preventieve maatregelen.
2. De sleutel tot het verbeteren van de nauwkeurigheid: de krimpsnelheid van de matrijs is correct toegewezen
De bovengenoemde "maatvastheid" is iets anders dan "maatnauwkeurigheid" en "precisie (precisie)". Dimensionale stabiliteit (dwz precisie) is synoniem met dimensionale consistentie, die de mate van dimensionale fluctuatie of spreiding weergeeft, en wordt meestal gemeten door de standaarddeviatie σ. De belangrijkste oorzaak van dimensionale instabiliteit is een lakse procescontrole, wat een willekeurige fout is. Nauwkeurigheid verwijst naar de mate waarin het rekenkundig gemiddelde van veel gemeten waarden afwijkt van de nominale maat voor een bepaalde maat op het gietstuk, dat wil zeggen de grootte van de gemiddelde afwijking. Voor investeringsgieten is de belangrijkste reden voor de slechte maatnauwkeurigheid de onjuiste toewijzing van de krimpsnelheid tijdens het profileringsontwerp, wat een systematische fout is, die meestal wordt gecorrigeerd door de mal herhaaldelijk te repareren. De maatnauwkeurigheid (precisie) is een combinatie van de bovenstaande twee. Om de maatnauwkeurigheid van gietstukken te verbeteren en het probleem van productmaattoleranties op te lossen, moet daarom niet alleen het proces strikt worden gecontroleerd om maatschommelingen te verminderen, maar moet ook de krimpsnelheid van elke dimensie van het gietstuk correct worden toegewezen bij het ontwerpen van het profiel .
Het is algemeen bekend dat de uiteindelijke totale krimp van precisiegietstukken een combinatie is van wasvorm, legeringskrimp en een kleine hoeveelheid uitzetting van de schaal. De schaal zwelt ongeveer 0.25% op en het effect is beperkt. Hoewel de lineaire krimpsnelheid van de legering vaak groter is dan die van de wasvorm, heeft de dimensionale fluctuatie veroorzaakt door het waspersproces een grotere impact. Om de kosten van schimmelreparatie te verlagen en de fluctuatie van de gietmaat te verminderen, is het erg belangrijk om de krimpsnelheid van de wasvorm te beheersen.
1. Wasvorm krimp
De krimp van de wasvorm moet worden gemeten nadat de grootte van de wasvorm volledig is gestabiliseerd. Dit komt omdat het krimpen van de wasvorm niet volledig stopt nadat de vorm is uitgeworpen. De grootte van de wasvorm stabiliseert soms pas een paar dagen nadat de vorm is uitgeworpen. Het grootste deel van het krimpen van het vormmateriaal is echter in principe voltooid binnen één tot enkele uren nadat de vorm is uitgeworpen. De krimpsnelheid van de wasvorm heeft voornamelijk de volgende beïnvloedende factoren:
(1) Type matrijsmateriaal;
(2) doorsnede van wasmodel;
Het is de moeite waard om te benadrukken dat de grootte van de dwarsdoorsnede van de wasvorm een significant effect heeft op de krimpsnelheid. Bijvoorbeeld de krimpsnelheid van een typisch ongevuld vormmateriaal bij het persen van wasvormen van verschillende diktes. De dikte van het gedeelte van de wasvorm mag over het algemeen niet groter zijn dan 13 mm. Wanneer de dikte groter is dan 13 mm, kan de wanddikte worden verminderd door koude wasblokken of metalen kernen te gebruiken om het doel van het verminderen van krimp te bereiken, wat vooral belangrijk is voor niet-vulbare vormmaterialen.
Opmerking: 1. De krimpsnelheid van het in water oplosbare vormmateriaal is ongeveer 0.25%;
2. Bij gebruik van oplosbare kernen, keramische kernen of kwartsglasbuizen is er geen lineaire krimp van de wasvorm in contact met de kern;
(3) Kerntypen
De grootte van de holte van de wasvorm komt ongetwijfeld overeen met de vorm van de kern. Daarom is het gebruik van kernen een manier geworden om de maatnauwkeurigheid van de holte van de wasvorm te verbeteren.
2. Legeringskrimp
Legeringskrimp hangt voornamelijk af van de volgende factoren:
· Type gegoten legering en chemische samenstelling;
· Gietgeometrie (inclusief beperkingsstatus en sectiegrootte);
· Gietparameters, zoals giettemperatuur, schaaltemperatuur, gietkoelsnelheid, etc.;
· Gebruik van keramische kernen, kwartsglazen buizen etc.
Aangezien de giettemperatuur, schaaltemperatuur, afkoelsnelheid van het gieten en andere procesparameters over het algemeen strikt worden gecontroleerd door standaard proceskaarten tijdens het productieproces, zijn de grootteschommelingen die hierdoor worden veroorzaakt niet groot tussen verschillende productiebatches. Zelfs als de giettemperatuur het bereik overschrijdt dat vereist is door de processpecificatie, is de fluctuatie van de gietmaat meestal niet groot. Net als bij de wasvorm zijn de sectiegrootte van het gietstuk en de beperkingen van de vormschaal de belangrijkste factoren die de krimp van de legering beïnvloeden. De ervaring leert dat het krimppercentage van de volledig ingeperkte maat 85% tot 89% is van het vrije krimppercentage; de semi-beperkte grootte is 94% tot 95%.
3. Het minimum aantal van de eerste batch monsters voor meting
Het hierboven vermelde inkrimpingspercentage is empirische gegevens op basis van ervaringen uit het verleden, niet het werkelijke inkrimpingspercentage. Ontwerp en maak matrijzen volgens deze gegevens, reparatie is onvermijdelijk. Om de nauwkeurigheid en het slagingspercentage van reparaties te verbeteren en het aantal reparaties te verminderen, is een belangrijke schakel het zorgvuldig controleren van de grootte van een voldoende aantal proefgietmonsters. Omdat de grootte van de gietstukken die we produceren niet exact hetzelfde kan zijn, dus alleen als het aantal gemeten monsters groot genoeg is, kan de verkregen gemiddelde waarde dicht bij het werkelijke rekenkundig gemiddelde liggen. Hieruit is het niet moeilijk om te zien dat het minimale aantal meetmonsters direct gerelateerd is aan het procesvermogen van het productieproces om de consistentie van de productgrootte te beheersen (Process Capability). Als de gietstukken volledig dezelfde maat hebben, hoeft er maar één monster te worden getest; Omgekeerd, als de gietmaat sterk fluctueert,
Het is noodzakelijk om veel monsters te meten om nauwkeurigere krimpgegevens te krijgen. Zoals eerder vermeld, kan het vermogen van het productieproces om de maat te regelen worden weergegeven door de 6σ van de gietmaat die door dit proces wordt geproduceerd. Vanaf het huidige technologische niveau van de meeste investeringsgieterijen ligt Hp meestal boven de 0.5, dus voor de eerste batch meetmonsters zijn over het algemeen minimaal 11 monsters nodig.
drie. Meetsysteem analyse
Bij het analyseren en oplossen van problemen met productafmetingen moeten we letten op de nauwkeurigheid en betrouwbaarheid van het gebruikte meetsysteem. Naast het veelvuldig kalibreren van meetinstrumenten en apparatuur zelf, is het ook belangrijk om meetfouten tot een minimum te beperken. Als het meetsysteem (inclusief de operator en de bedieningsmethode) een grote fout heeft, kunnen niet alleen de afgekeurde producten worden beoordeeld als gekwalificeerde producten, maar kunnen ook veel gekwalificeerde producten verkeerd worden beoordeeld als afgekeurde producten, die beide grote ongelukken of onnodige economische gevolgen kunnen hebben. verliezen. De eenvoudigste manier om te bepalen of een meetsysteem geschikt is voor een bepaalde meettaak, is het uitvoeren van reproduceerbaarheids- en herhaalbaarheidskwalificatietesten. De zogenaamde herhaalbaarheid betekent dat dezelfde inspecteur hetzelfde instrument (of apparaat) en dezelfde methode gebruikt om hetzelfde onderdeel te inspecteren en de consistentie van de resultaten te verkrijgen. Reproduceerbaarheid verwijst naar de consistentie van resultaten verkregen door verschillende operators die verschillende instrumenten gebruiken om hetzelfde onderdeel te controleren. De American Automotive Industry Action Group (Automotive Industry Action Group) bepaalt dat het percentage van de geïntegreerde standaarddeviatie van herhaalbaarheid en reproduceerbaarheid R&R in de standaarddeviatie van de gemeten gietmaatfluctuaties ≤30% is als norm voor het meetsysteem om te voldoen aan de vereisten [5]. Bij het meten van sommige grote en complex gevormde gietstukken kunnen niet alle meetsystemen aan deze eis voldoen. De toegestane meetfout bij het meten van mallen moet kleiner zijn, meestal 1/3.
vier. Matrijsstructuur en verwerkingsniveau
Het is algemeen bekend dat de vormstructuur en verwerkingskwaliteit een belangrijke invloed hebben op de grootte en geometrie van de wasvorm. Of het positionerings- en klemmechanisme bijvoorbeeld nauwkeurig en betrouwbaar is, of de bijpassende speling van de beweegbare delen (zoals beweegbare blokken, bouten, enz.) Geschikt is, of de tekenmethode gunstig is om de maatnauwkeurigheid van de gietstukken te waarborgen , enz. Onnodig te zeggen dat voor een aanzienlijk aantal binnenlandse investeringsgietfabrieken het niveau van matrijsontwerp en -productie nog steeds dringend moet worden verbeterd.
Vijven. ten slotte
Uit de bovenstaande analyse is het niet moeilijk om te zien dat het verbeteren van de maatnauwkeurigheid van investeringsgietwerk een systematisch project is waarbij alle aspecten van het productieproces van investeringsgietwerk betrokken zijn. De belangrijkste punten kunnen als volgt worden samengevat:
1) Controleer strikt de parameters van het vormproces, vooral de parameters die een aanzienlijke invloed hebben op de grootte van het gietstuk.
2) Kies het juiste schaalmateriaal.
3) Verzamel, tel en analyseer gegevens met betrekking tot krimp in een correcte methode die voldoet aan statistische principes om de nauwkeurigheid van krimptoewijzing te verbeteren.
4) Controleer regelmatig het meetsysteem (inclusief apparatuur, inspectiepersoneel en technologie) om ervoor te zorgen dat de herhaalbaarheid en reproduceerbaarheidsfouten voldoen aan de gespecificeerde eisen.
5) Verbeter continu het niveau van matrijsontwerp en -productie.
6) Maatregelen zoals gietcorrectie en stabilisatiewarmtebehandeling zijn in veel gevallen nog steeds onmisbaar
Bewaar de bron en het adres van dit artikel voor herdruk: Verschillende factoren die de maatvastheid van investeringsgietstukken beïnvloeden
Minge Spuitgietbedrijf zijn toegewijd aan het vervaardigen en leveren van hoogwaardige en hoogwaardige gietstukken (het assortiment metalen spuitgietonderdelen omvat voornamelijk: Dunwandig spuitgieten,Hot Chamber Spuitgieten,Koude kamer spuitgieten),Ronde Service (Die Casting Service,CNC-bewerking,Matrijzen maken, Oppervlaktebehandeling). Elk aangepast aluminium spuitgieten, magnesium of Zamak / zink spuitgieten en andere gietstukken zijn welkom om contact met ons op te nemen.
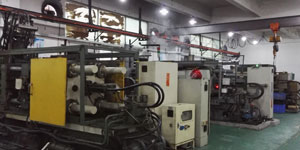
Onder controle van ISO9001 en TS 16949 worden alle processen uitgevoerd door honderden geavanceerde spuitgietmachines, 5-assige machines en andere faciliteiten, variërend van blasters tot Ultra Sonic-wasmachines. Minghe heeft niet alleen geavanceerde apparatuur, maar heeft ook professionele team van ervaren ingenieurs, operators en inspecteurs om het ontwerp van de klant waar te maken.
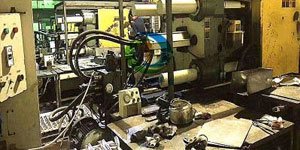
Contractfabrikant van spuitgietwerk. Mogelijkheden zijn onder meer koude kamer aluminium spuitgietonderdelen vanaf 0.15 lbs. tot 6 lbs., snelwissel instellen en machinaal bewerken. Diensten met toegevoegde waarde omvatten polijsten, trillen, ontbramen, stralen, schilderen, plateren, coaten, assembleren en bewerken. Materialen waarmee gewerkt is, zijn legeringen zoals 360, 380, 383 en 413.
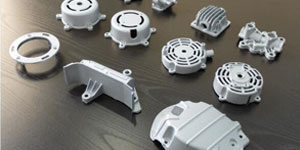
Hulp bij ontwerp van spuitgieten van zink/concurrent engineering. Custom fabrikant van precisie gegoten zink. Miniatuurgietstukken, hogedrukgietstukken, multi-slide gietstukken, conventionele gietstukken, eenheidsmatrijs en onafhankelijke spuitgietstukken en holteverzegelde gietstukken kunnen worden vervaardigd. Gietstukken kunnen worden vervaardigd in lengtes en breedtes tot 24 inch met een tolerantie van +/- 0.0005 inch.
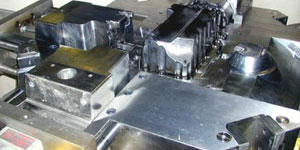
ISO 9001: 2015 gecertificeerde fabrikant van gegoten magnesium. Mogelijkheden zijn onder hoge druk spuitgieten van magnesium tot 200 ton hete kamer en 3000 ton koude kamer, gereedschapsontwerp, polijsten, gieten, machinale bewerking, poeder- en vloeistofverven, volledige QA met CMM-mogelijkheden , montage, verpakking & levering.
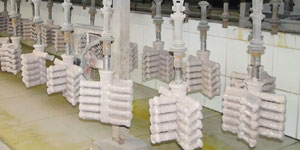
ITAF16949 gecertificeerd. Extra castingservice omvat: investering gieten,zandgieten,Zwaartekracht gieten, Verloren schuimafgietsel,Centrifugaal gieten,Vacuümgieten,Permanent vormgieten,. Mogelijkheden zijn onder meer EDI, technische assistentie, solide modellering en secundaire verwerking.
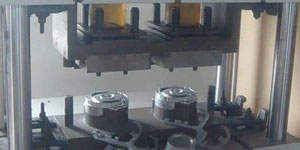
Gietindustrieën Casestudy's over onderdelen voor: auto's, fietsen, vliegtuigen, muziekinstrumenten, waterscooters, optische apparaten, sensoren, modellen, elektronische apparaten, behuizingen, klokken, machines, motoren, meubels, sieraden, mallen, telecom, verlichting, medische apparaten, fotografische apparaten, Robots, sculpturen, geluidsapparatuur, sportuitrusting, gereedschap, speelgoed en meer.
Wat kunnen we u hierna helpen doen?
∇ Ga naar de startpagina voor Spuitgieten China
→Gietonderdelen- Zoek uit wat we hebben gedaan.
→Gerangschikte tips over Spuitgietdiensten
By Minghe Die Casting Fabrikant: |Categorieën: Handige artikelen |Materiaal Tags: Aluminium gieten, Zink gieten, Magnesium gieten, Titanium gieten, Gieten van roestvrij staal, Messing gieten,Brons gieten,Video casten,Geschiedenis van ons bedrijf,Aluminium spuitgieten |Reacties uitgeschakeld