Het smeltproces van schroot gehard nodulair gietijzer
In het traditionele productieproces van nodulair gietijzer wordt over het algemeen ongeveer 10% koolstofschroot gebruikt voor ingrediënten. Dit artikel gaat alleen in op enkele zaken waaraan speciale aandacht moet worden besteed in het productieproces na verhoging van het aandeel koolstofschroot dat wordt gebruikt bij de productie van nodulair gietijzer in een inductieoven. Volgens de productiepraktijk brengt de auteur zijn eigen opvattingen naar voren ter referentie van collega's.
De keuze van de lading
(1) Schroot
Schroot dat bij de productie van nodulair gietijzer wordt gebruikt, moet koolstofschroot zijn. Het mag geen elementen bevatten die de grafitisering belemmeren, zoals chroom. Het mag geen anti-sferoïdiserende legeringselementen bevatten. De brokken staalschroot moeten ongeveer 30% in de vorm van dikke vlokken zijn, die plat in de oven kunnen worden gelegd.
(2) hercarburateur
- ① Hoogwaardige cola. Het zwavelgehalte moet laag zijn, de klonterigheid is 60-80 mm en het heeft een hoge sterkte. Het kan niet worden verpletterd nadat het is verbrand.
- ②Verbruikt elektrodenblok. Het is het beste om een bepaalde lengte te hebben om het snijden in het gesmolten ijzer te vergemakkelijken.
(3) Gietijzer
Het wordt voornamelijk gebruikt om het koolstofgehalte van gesmolten ijzer aan te passen. Hoop koolstofarm ruwijzer met een laag zwavelgehalte te gebruiken met wC> 4%. Het siliciumgehalte in het ruwijzer is passend hoger en de productie van nodulair gietijzer kan minder ferrosilicium zijn.
(4) sferoïdiserend
Sferoïdizer en inoculant worden gebruikt volgens traditionele technieken en worden bepaald in overeenstemming met de werkelijke omstandigheden van elke fabriek.
Spiering
Smeltproces: Cokesblok + staalschroot → elektrodeblok → temperatuurverhoging → cokesblok en elektrodeblok eruit trekken → monster en analyseer koolstofgehalte → ruwijzer → retourmateriaal → monster en analyseer Si, Mn → temperatuurstijging → ferromangaan + ferrosilicium → ontlading → Inoculatie + sferoïdisatie → gieten.
De voorzorgsmaatregelen tijdens het smeltproces zijn als volgt:
- Het cokesblok wordt op de bodem van de oven geplaatst, het doel is om een langere inweektijd van het cokesblok in het gesmolten ijzer te creëren. De hoeveelheid cokesblok is ongeveer 5% van het schroot. Ongeveer 50% van het schroot is gesmolten en de cokes moet worden bedekt met dik schroot. Het is ook mogelijk om afvalelektrodeblokken van 60-80 mm te gebruiken in plaats van cokes die op de bodem van de oven moeten worden geïnstalleerd als recarburizer, met een lager zwavelgehalte, wat gunstiger is om hoogwaardig nodulair gietijzer te verkrijgen.
- Het aandeel staalschroot dat wordt gebruikt, wordt voornamelijk bepaald door de efficiëntie van koolstoftoename. Voor fabrikanten die deze methode gaan gebruiken om nodulair gietijzer te produceren, is ongeveer 30% beter. Na het verbeteren van de efficiëntie van de koolstofverhoging, verhoogt u geleidelijk het aandeel schroot. Overmatig gebruik van staalschroot, als de efficiëntie van de koolstofverhoging niet hoog is, zal het koolstofsiliciumequivalent van het eindproduct beïnvloeden.
- Nadat het schrootstaal is gesmolten, plaatst u de elektrodestaaf om de temperatuur in de oven op de juiste manier te verhogen en de koolstofefficiëntie te verhogen. De oventemperatuur is echter te hoog, wat het energieverbruik verhoogt en ook schadelijk is voor de ovenbekleding.
- Nadat het koolstofgehalte hoog genoeg is geschat, verwijdert u het cokesblok en de elektrodestaaf en neemt u monsters en analyseert u het koolstofgehalte.
- Bereken op basis van de analyseresultaten de hoeveelheid toegevoegd ruwijzer en de gebruikte hoeveelheid gerecycleerd nodulair gietijzer.
- Bepaal of de totale hoeveelheid gesmolten ijzer kan worden gecompenseerd met het opgeknapte materiaal op basis van de schatting van het siliciumgehalte.
- Nadat het heropwarmingsmateriaal is gesmolten, neemt u een monster en analyseert u het gehalte aan Si, Mn en andere legeringselementen.
- Verhoog de temperatuur van het gesmolten ijzer op de juiste manier, vul de legeringselementen aan volgens de analyseresultaten en voeg ferrosilicium toe voordat de oven de oventemperatuur bereikt.
- Het ferrosilicium wordt gesmolten tot gesmolten toestand en komt onmiddellijk uit de oven.
- Sferoïdisatie, inoculatie en gieten worden zoals gebruikelijk uitgevoerd.
Compositie aanpassing berekening
Zoals we allemaal weten, hangen de mechanische eigenschappen van nodulair gietijzer voornamelijk af van de chemische samenstelling, de afkoelsnelheid (zoals gegoten nodulair gietijzer) en het warmtebehandelingsproces. De chemische samenstelling is de interne oorzaak, de wortel en de variabele, bijna elke oven is anders. Daarom is het noodzakelijk om de detectie van chemische componenten te versterken en zorgvuldige aanpassingen te maken, en het is niet gepast om "productie met een vaste verhouding" toe te passen. In de chemische samenstelling is het koolstofequivalent bijzonder belangrijk. In het bijzonder nodulair gietijzer geproduceerd door schrootstaal als hoofdlading te gebruiken, omdat de efficiëntie van koolstoftoename moeilijk te regelen is en het koolstofequivalent sterk fluctueert, dus speciale aandacht moet worden besteed aan het aanpassen van het koolstofequivalent.
- Bereken de hoeveelheid toegevoegd ruwijzer. Bereken de hoeveelheid toegevoegd ruwijzer op basis van de analyse van het koolstofgehalte. In feite is het om het koolstofequivalent van nodulair gietijzer zo aan te passen dat het koolstofequivalent van de smelt gevormd door zowel ruwijzer als schroot het koolstofequivalent bereikt dat nodig is voor nodulair gietijzer. De hoeveelheid toegevoegd ruwijzer = de hoeveelheid schroot toegevoegd × (het vereiste koolstofgehalte van nodulair gietijzer - analyse van het koolstofgehalte) / (het koolstofgehalte van ruwijzer - het vereiste koolstofgehalte van nodulair gietijzer)
- Berekening van de toegevoegde hoeveelheid gerecycled nodulair gietijzer Het koolstofequivalent van gerecycled nodulair gietijzer is in principe normaal en de toegevoegde hoeveelheid is niet groot. Daarom wordt, nadat het opnieuw verwarmde ijzer is toegevoegd, het koolstofgehalte van het gesmolten ijzer in de gehele oven gekwalificeerd. De hoeveelheid nodulair gietijzer die aan de oven wordt toegevoegd = de totale hoeveelheid lading - de hoeveelheid schroot - de hoeveelheid varken ijzer toegevoegd
- Schatting van het siliciumgehalte De berekeningsformule is als volgt: Siliciumgehalte ( ((toevoeging schroot staal + ruwijzer + nodulair gietijzer) × siliciumgehalte / totale lading] × 100% ≤ toelaatbaar siliciumgehalte van het oorspronkelijke gesmolten ijzer gehalte te hoog is, voeg dan een kleine hoeveelheid gerecycleerd nodulair gietijzer toe en gebruik dezelfde hoeveelheid ruwijzer en schroot met een verhouding van 9:1 om de totale lading aan te vullen.
- Berekening van toevoeging van ferrosilicium De berekeningsformule is als volgt: De hoeveelheid toegevoegd ferrosilicium = [totale hoeveelheid lading × (vereiste siliciumgehalte van nodulair gietijzer verhoogd siliciumgehalte door inoculatie verhoogd siliciumgehalte door sferoïdisatie-analyse van siliciumgehalte)] / siliciumgehalte van ferrosilicium
- De toegevoegde hoeveelheid mangaan en andere legeringselementen wordt als volgt berekend: De hoeveelheid toegevoegd gelegeerd ijzer = de totale hoeveelheid lading × (het vereiste gehalte aan legering van nodulair gietijzer-analysegehalte)/gelegeerd elementgehalte in gelegeerd ijzer Het verbrandingsverlies is niet meegenomen in bovenstaande berekeningen.
Dit komt omdat nodulair gietijzer in de inductieoven wordt gesmolten en de elementen niet veel worden verbrand, en het ijzer wordt tot op zekere hoogte ook verbrand. Als u bijzondere omstandigheden tegenkomt, moet u op verbranding letten.
Toepassingsvoorbeeld compositie aanpassing:
- Met behulp van een elektrische inductieoven van 1 ton om perlitisch nodulair gietijzer QT800-2 te produceren, is het gietgewicht 1000 kg.
- "De chemische samenstelling van de controle is: wC=3.5%, wSi=2.5%, wMn=0.5%, wP<0.07%, wS<0.02%, wMg=0.03%-0.06%, wRE=0.02%-0.04%.
- Na de heropkoling is het koolstofgehalte van het "schroot gesmolten staal" in de oven 2.5%.
- De hoeveelheid toegevoegd ruwijzer = 300 × (3.5%-2.5%) / (4%-3.5%) = 600 (kg)
- De hoeveelheid nodulair gietijzer die in de oven wordt gebruikt = 1000-300-600=100 (kg)
- Geschat siliciumgehalte = (300×0.3%+600×1.8%+100×2.5%)×100%=1.42%
- Als het siliciumgehalte van de nodulizer 0.6% is en het siliciumgehalte van het entmiddel 0.4%, dan moet het siliciumgehalte van het oorspronkelijke gesmolten ijzer 1.5% zijn, wat hoger is dan het geschatte siliciumgehalte. Hiervoor kan Z18-gietijzer worden gebruikt om het koolstofequivalent aan te passen, en het opnieuw gebakken nodulair gietijzer kan worden gebruikt om de totale hoeveelheid lading aan te vullen.
- Het siliciumgehalte is 1.38% en het mangaangehalte is 0.15% voordat de oven wordt vrijgegeven.
- Toegevoegde hoeveelheid ferrosilicium = [1000 (2.5%-0.6%-0.4%-1.38%)] / 75% = 1.6 kg
- Toegevoegde hoeveelheid ferromangaan = [1000 (0.5%-0.15%)] / 65% = 5.4 kg
4. Slotopmerkingen
Bij de productie van inductie-elektrische ovens gebruiken we schrootstaal om QT800-2 te produceren, de sterkte is 800 ~ 1000 MPa en de rek is meer dan 4%.
Momenteel is er veel schroot op de markt, ruwijzer is duur en hoogwaardig ruwijzer is nog schaarser. Daarom stellen we voor dat fabrikanten met productietaken van nodulair gietijzer kunnen verwijzen naar de bovengenoemde aanname en "ijzer vervangen door staal" om nodulair gietijzer te produceren.
Bewaar de bron en het adres van dit artikel voor herdruk:Het smeltproces van schroot gehard nodulair gietijzer
Minge Spuitgietbedrijf zijn toegewijd aan het vervaardigen en leveren van hoogwaardige en hoogwaardige gietstukken (het assortiment metalen spuitgietonderdelen omvat voornamelijk: Dunwandig spuitgieten,Hot Chamber Spuitgieten,Koude kamer spuitgieten),Ronde Service (Die Casting Service,CNC-bewerking,Matrijzen maken, Oppervlaktebehandeling). Elk aangepast aluminium spuitgieten, magnesium of Zamak / zink spuitgieten en andere gietstukken zijn welkom om contact met ons op te nemen.
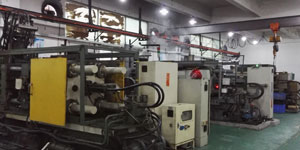
Onder controle van ISO9001 en TS 16949 worden alle processen uitgevoerd door honderden geavanceerde spuitgietmachines, 5-assige machines en andere faciliteiten, variërend van blasters tot Ultra Sonic-wasmachines. Minghe heeft niet alleen geavanceerde apparatuur, maar heeft ook professionele team van ervaren ingenieurs, operators en inspecteurs om het ontwerp van de klant waar te maken.
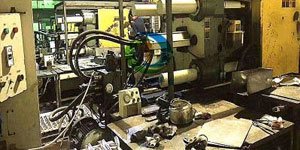
Contractfabrikant van spuitgietwerk. Mogelijkheden zijn onder meer koude kamer aluminium spuitgietonderdelen vanaf 0.15 lbs. tot 6 lbs., snelwissel instellen en machinaal bewerken. Diensten met toegevoegde waarde omvatten polijsten, trillen, ontbramen, stralen, schilderen, plateren, coaten, assembleren en bewerken. Materialen waarmee gewerkt is, zijn legeringen zoals 360, 380, 383 en 413.
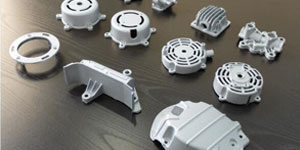
Hulp bij ontwerp van spuitgieten van zink/concurrent engineering. Custom fabrikant van precisie gegoten zink. Miniatuurgietstukken, hogedrukgietstukken, multi-slide gietstukken, conventionele gietstukken, eenheidsmatrijs en onafhankelijke spuitgietstukken en holteverzegelde gietstukken kunnen worden vervaardigd. Gietstukken kunnen worden vervaardigd in lengtes en breedtes tot 24 inch met een tolerantie van +/- 0.0005 inch.
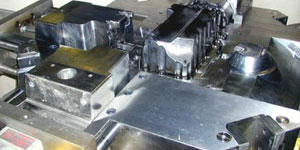
ISO 9001: 2015 gecertificeerde fabrikant van gegoten magnesium. Mogelijkheden zijn onder hoge druk spuitgieten van magnesium tot 200 ton hete kamer en 3000 ton koude kamer, gereedschapsontwerp, polijsten, gieten, machinale bewerking, poeder- en vloeistofverven, volledige QA met CMM-mogelijkheden , montage, verpakking & levering.
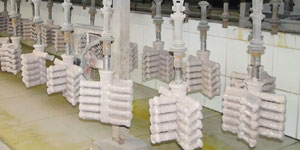
ITAF16949 gecertificeerd. Extra castingservice omvat: investering gieten,zandgieten,Zwaartekracht gieten, Verloren schuimafgietsel,Centrifugaal gieten,Vacuümgieten,Permanent vormgieten,. Mogelijkheden zijn onder meer EDI, technische assistentie, solide modellering en secundaire verwerking.
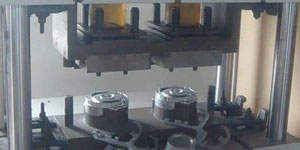
Gietindustrieën Casestudy's over onderdelen voor: auto's, fietsen, vliegtuigen, muziekinstrumenten, waterscooters, optische apparaten, sensoren, modellen, elektronische apparaten, behuizingen, klokken, machines, motoren, meubels, sieraden, mallen, telecom, verlichting, medische apparaten, fotografische apparaten, Robots, sculpturen, geluidsapparatuur, sportuitrusting, gereedschap, speelgoed en meer.
Wat kunnen we u hierna helpen doen?
∇ Ga naar de startpagina voor Spuitgieten China
→Gietonderdelen- Zoek uit wat we hebben gedaan.
→Gerangschikte tips over Spuitgietdiensten
By Minghe Die Casting Fabrikant: |Categorieën: Handige artikelen |Materiaal Tags: Aluminium gieten, Zink gieten, Magnesium gieten, Titanium gieten, Gieten van roestvrij staal, Messing gieten,Brons gieten,Video casten,Geschiedenis van ons bedrijf,Aluminium spuitgieten |Reacties uitgeschakeld