Voedingsdraadmethode Nodulair gietijzerbehandelingsproces
Door daadwerkelijke productie worden de ponsmethode en de voedingsmethode gebruikt om nodulair gietijzer te produceren en worden de kenmerken van de twee processen geanalyseerd. Door de vergelijking zijn de uitgebreide prestaties van de gietstukken geproduceerd door de voedingsmethode stabieler dan die van de ponsmethode; en het voedingsproces is bolvormig. Om enkele van de ervaringen erin te delen.
1. Overzicht
Zoals we allemaal weten, is de as een belangrijk dragend onderdeel van het voertuig en houdt het rechtstreeks verband met de veiligheid van het voertuig. Het ashuis is een van de belangrijkste componenten van de as. De prestaties van het materiaal van de asbehuizing zijn rechtstreeks bepalend voor het draagvermogen van het voertuig. Momenteel worden de ashuizen in de zware vrachtwagenindustrie over het algemeen verdeeld in twee categorieën: gestanste en gelaste ashuizen en gegoten ashuizen, en gegoten ashuizen kunnen worden onderverdeeld in gietstalen ashuizen en gietijzeren ashuizen.
Het gegoten ashuis heeft altijd de hoofdpositie ingenomen van het ashuis van zware vrachtwagens vanwege het hoge draaggewicht en de lage productiekosten. Vanwege de zware werkomgeving van het ashuis en langdurig werk onder dynamische belasting stelt dit hoge eisen aan de materiaaleigenschappen van het ashuis. Terwijl het de sterkte garandeert, moet het ook een hogere plasticiteit en taaiheid verkrijgen om zich aan te passen aan het ashuis. Werk kenmerken.
We weten dat voor nodulair gietijzer het sferoïdisatieproces een belangrijke schakel is in de productie van nodulair gietijzer, en dat de kwaliteit van de sferoïdisatiebehandeling rechtstreeks van invloed is op de kwaliteit van het nodulair gietijzer. In het begin was het sferoïdisatieproces dat we gebruikten het sferoïdisatieproces van de rush-in-methode. Hoewel deze methode eenvoudig en gemakkelijk te bedienen is, heeft deze veel tekortkomingen, zoals: lage legeringsopbrengst; grote rookontwikkeling en slechte werkomgeving; reactie De hoeveelheid geproduceerde slak is groot; het behandelingseffect wordt gemakkelijk beïnvloed door externe factoren, wat leidt tot schommelingen in de kwaliteit van gietstukken en vaak ongekwalificeerde sferoïdisatie. Deze kwaliteitsschommelingen hebben invloed op de prestaties van het ashuis en zelfs op de veiligheid van het voertuig.
Het sferoïdiserende behandelingsproces van de draadaanvoermethode werd toegepast op de productie van gietijzer. Het begon in de jaren 1980 in het buitenland. Hoewel de binnenlandse productie van nodulair gietijzer deze technologie laat begon toe te passen, is de technologie populair geworden en snel in het land gebruikt, en het is nuttig voor het verbeteren van de productie van nodulair grafiet. Het stabiliteitseffect van gietijzerkwaliteit is duidelijk.
2. Sferoïdisatieproces van voedingsdraad
Het basisprincipe van het draadvoedende sferoïdisatieproces is om een bepaalde samenstelling van poedervormig sferoïdisatiemiddel en inoculant door de stalen huid te wikkelen en het met een bepaalde snelheid door de apparatuur in het sferoïdisatiebehandelingspakket te sturen, zodat de sferoïdisatie aan de onderkant van het pakket zal ontploffen. Om het doel van sferoïdisatie-inentingsbehandeling te bereiken.
Op dit moment is het draadaanvoerende sferoïdisatieproces dat we gebruiken: pas de chemische samenstelling aan de procesvereisten aan, verwarm tot 1510-1520 ℃ en laat het stilstaan, de taptemperatuur is 1480 ~ 1500 ℃, de ijzeroutput is 2t, en de sferoïdiserende behandelingstemperatuur is 1420~1450℃. De giettemperatuur is 1370 ~ 1380 ℃. Het inentingspercentage met de stroom is 0.1%.
De lengte van de bolvormige lijn is 39-46 m, aangepast aan het zwavelgehalte van het oorspronkelijke gesmolten ijzer. Hoe hoger het zwavelgehalte, hoe langer de sferoïdisatielijn moet worden toegevoegd, en vice versa. De lengte van de entlijn is 32m.
3. Het sferoïdisatieproces van het aanvoeren van draad verbetert de kwaliteit van gietstukken
Na meer dan een jaar productie is de kwaliteit van onze ashuizen aanzienlijk verbeterd ten opzichte van voorheen. Vooral de stabiliteit van samenstelling, metallografie en mechanische eigenschappen is sterk verbeterd.
Vergelijking van metallografische structuur Selecteer dezelfde positie van het gietstuk om de metallografische structuur te polijsten en te observeren. De gemaakte metallografische foto wordt getoond in figuur 2. Vergeleken met de ponsmethode zijn de grafietballen van het gietstuk geproduceerd door de voedingsmethode meer en dunner en is de ronding beter.
4. Voordelen van het sferoïdisatieproces met schroefdraad
Volgens onze daadwerkelijke productievergelijking heeft het sferoïdisatieproces met schroefdraad veel voordelen ten opzichte van het sferoïdisatieproces van de ponsmethode.
- Verbetering van de on-site productieomgeving. Wanneer het sferoïdiserende middel reageert met het gesmolten ijzer, wordt een grote hoeveelheid rook en sterk licht gegenereerd, wat de werkomgeving ter plaatse verslechtert; wanneer de draadaanvoermethode wordt gebruikt voor sferoïdisatie, het verwerkingsstation Er is een deksel om de sferoïdisatiezak te bedekken en het deksel is verbonden met het stofverwijderingssysteem van het verwerkingsstation, zodat de rook in plaats daarvan wordt verwerkt door het stofverwijderingssysteem direct vrijkomen in de werkplaats.
- De hoeveelheid toegevoegde legering wordt verminderd en de productiekosten worden verlaagd. Na berekening kan de verwerking van 1 ton gesmolten ijzervoedingsmethode ongeveer 78 yuan aan grondstofkosten besparen dan de impulsmethode. Volgens de jaarlijkse productiecapaciteit van 10,000 ton nodulair gietijzeren ashuis van onze fabriek, is de jaarlijkse besparing 780,000 yuan en zijn de voordelen aanzienlijk.
- Realiseer taakautomatisering en verminder de arbeidsintensiteit van werknemers. Wanneer het sferoïdisatieproces wordt uitgevoerd, zijn de voorbereidende voorbereidingen van de arbeiders omslachtig, inclusief het wegen van het sferoïdiserende middel en het inoculant, het toevoegen van het sferoïdiserende middel en het inoculant aan de zak, en aanstampen en afdekken zijn vereist; de toevoeging van de sferoïdisatie- en inoculatielijnen van de draadaanvoermethode wordt automatisch toegevoegd via de schakelkast, wat veel werk vermindert.
- De kwaliteit van sferoïdisatie is stabiel en het sferoïdisatie-effect is beter. Volgens statistieken is het slagingspercentage van de sferoïdisatie sinds het gebruik van het draadvoedende sferoïdisatieproces in 2013 meer dan 99.5%, terwijl het slagingspercentage van het sferoïdisatieproces slechts 95,% is.
5. Hoe de procesparameters van het voeden van draadsferoïdisatie correct te kiezen
In de daadwerkelijke productie vereist het correct selecteren van de parameters van het draadaanvoerproces een bepaald aantal tests om te verifiëren. Vanaf het begin van de organisatie van de test tot aan de formele massaproductie hebben we veel procesaanpassingen ondergaan. Het volgende zal onze ervaring delen met collega's.
Om de procesparameters van de sferoïdisatie van de voedingsdraad correct te selecteren, moet u op de volgende aspecten letten:
- (1) De keuze van gevulde draad Enige buitenlandse ervaring raadt het gebruik van gevulde draad met een hoog Mg-gehalte niet aan. Het Mg-gehalte is te hoog, de sferoïdisatiereactie is intens, het Mg brandt veel en de hoeveelheid slakken is groot. Over het algemeen wordt aanbevolen om een Mg-gehalte van ongeveer 30% te selecteren en Ba-bevattende inentingsdraad te gebruiken, die de inentingsafname effectief kan voorkomen. De belangrijkste parameters van de kerndraad die door ons bedrijf wordt gebruikt, zijn: de dikte van de buitenste stalen mantel is 0.4 mm en de diameter van de kerndraad is 13 mm. Controleer voor gebruik of het uiterlijk van de gevulde draad rond is en vrij van scheuren, poederlekkage, enz. Bij de daadwerkelijke productie is het noodzakelijk om aan te passen aan de behandelingstemperatuur en de hoogte van het gesmolten ijzer. Over het algemeen geldt: hoe hoger de behandelingstemperatuur, hoe hoger de hoogte van het gesmolten ijzer en hoe sneller de draadaanvoersnelheid. In aanvulling. Sommige materialen hebben ook een handige en haalbare methode geïntroduceerd om de optimale draadaanvoersnelheid te meten: meet eerst de hoogte van het gesmolten ijzer in de verwerkingszak en voer vervolgens handmatig de draadmachine in zodat de kerndraad net het vloeistofoppervlak raakt, dan maak de teller leeg, de handmatige draadaanvoermachine voert draadaanvoer uit. Wanneer u het "boom"-reactiegeluid hoort, controleer dan onmiddellijk de invoerlengte. Als deze lengte in principe gelijk is aan de hoogte van het gesmolten ijzer, moet de snelheid geschikt zijn. Na verificatie hebben we de invoersnelheid van 30 m/min geselecteerd.
- Selectie van draadaanvoerhoeveelheid De juiste draadaanvoerhoeveelheid is om de draad met de minste kern te voeden met als uitgangspunt het sferoïdisatie-effect te waarborgen. De hoeveelheid draadaanvoer moet worden bepaald op basis van het verwerkingsvolume van het gesmolten ijzer, de verwerkingstemperatuur en het zwavelgehalte van het gesmolten ijzer. Volgens ons oorspronkelijke zwavelgehalte van gesmolten ijzer en productprocesvereisten, gecombineerd met experimentele verificatie, op voorwaarde dat het resterende magnesiumgehalte wordt gewaarborgd, is de lengte van de sferoïdisatielijn 39-46 m en de lengte van de inentingslijn 32 m.
- De keuze van de verwerkingstemperatuur De verwerkingstemperatuur moet zo veel mogelijk worden verlaagd met als uitgangspunt de schenktemperatuur te waarborgen. Hoe lager de verwerkingstemperatuur, hoe hoger de opnamesnelheid van magnesium en hoe lager het verbruik van gevulde draad. Volgens daadwerkelijke productietesten is de tijd vanaf het begin van de sferoïdiserende behandeling tot het begin van het gieten 4 tot 5 minuten, gedurende welke de temperatuurdaling 40 tot 50°C is en de sferoïdiserende reactietijd 80 tot 90 seconden is. Aangezien het bolvormingsproces moet worden omgedraaid, stellen we de verwerkingstemperatuur in op 1410 ~ 1450 ℃, de bovengrens wordt genomen wanneer de kamertemperatuur lager is dan 5 ℃ en de ondergrens wanneer de kamertemperatuur hoger is dan 25 ℃.
- Selectie van het resterende magnesiumgehalte in gesmolten ijzer na behandeling. Het resterende magnesiumgehalte moet worden gereserveerd voor een bepaalde hoeveelheid magnesiumgehalte, afhankelijk van de kenmerken van het gietstuk zelf. In eerste instantie hebben we het resterende magnesiumgehalte gecontroleerd op 0.03% tot 0.06%, maar na daadwerkelijke productieverificatie is het geschikter om het resterende magnesiumgehalte te regelen op 0.05% tot 0.06%, omdat we ontdekten dat wanneer het resterende magnesiumgehalte minder is dan 0.04%, zijn grafiet. De ronding van de bal is iets slechter. Wanneer het hoger is dan 0.07%, is cementiet geneigd te verschijnen en wordt de krimpneiging van het gesmolten ijzer groter.
- Het probleem van vastlopen van de draad tijdens gebruik oplossen Het fenomeen van draadopstopping zal optreden tijdens het transportproces van de gevulde draad, waardoor het hele pakket gesmolten ijzer wordt afgedankt. Hiertoe hebben we de volgende maatregelen genomen: een daarvan is het installeren van een stalen ring boven de gevulde draadhaspel, zoals weergegeven in figuur 5, die het buigen van de kerndraad kan verminderen en ervoor kan zorgen dat deze soepel in het geleidingsmechanisme komt; de tweede is om de twee spoelen met elkaar te verbinden. Tijdens het lassen polijst u na het lassen de grotere oneffenheden weg om te voorkomen dat de draad vastloopt tijdens het transportproces; ten derde, vermijd bochten met een diameter van minder dan 1 m in de transportleiding of route van de gevulde draad om te voorkomen dat de gevulde draad wordt getransporteerd. Er is tijdens het proces poederlekkage of vastlopen opgetreden
6 Conclusie
- Het sferoïdisatieproces van de voedingsdraadmethode heeft een laag legeringstoevoegingsbedrag, een hoge Mg-absorptiesnelheid en kan rook en sterke lichtvervuiling in de werkplaats effectief verminderen, wat goede economische en milieuvoordelen oplevert voor gieterijbedrijven.
- Het sferoïdisatieproces van de draadaanvoermethode kan het faalpercentage van de sferoïdisatie effectief verminderen, de kwaliteit van nodulair gietijzer verbeteren, de uitgebreide mechanische eigenschappen ervan verbeteren en het marktconcurrentievermogen van de onderneming verbeteren.
- Elke gieterij moet de juiste procesparameters voor draadsferoïdisatie selecteren op basis van zijn eigen productieomstandigheden en productprocesvereisten, gecombineerd met de productie-ervaring van de collega's.
Het sferoïdisatieproces van de voedingslijn kan de stabiliteit van de kwaliteit van nodulair gietijzer aanzienlijk verbeteren, de productiekosten verlagen, de productieomgeving verbeteren en de arbeidsintensiteit van werknemers verminderen. Dit is de recente ontwikkelingstrend van het bolvormingsproces.
Bewaar de bron en het adres van dit artikel voor herdruk: Fdraadmethode Nodulair gietijzer behandelingsproces
Minge Spuitgietbedrijf zijn toegewijd aan het vervaardigen en leveren van hoogwaardige en hoogwaardige gietstukken (het assortiment metalen spuitgietonderdelen omvat voornamelijk: Dunwandig spuitgieten,Hot Chamber Spuitgieten,Koude kamer spuitgieten),Ronde Service (Die Casting Service,CNC-bewerking,Matrijzen maken, Oppervlaktebehandeling). Elk aangepast aluminium spuitgieten, magnesium of Zamak / zink spuitgieten en andere gietstukken zijn welkom om contact met ons op te nemen.
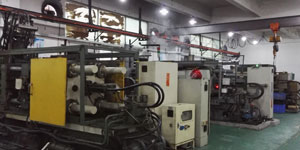
Onder controle van ISO9001 en TS 16949 worden alle processen uitgevoerd door honderden geavanceerde spuitgietmachines, 5-assige machines en andere faciliteiten, variërend van blasters tot Ultra Sonic-wasmachines. Minghe heeft niet alleen geavanceerde apparatuur, maar heeft ook professionele team van ervaren ingenieurs, operators en inspecteurs om het ontwerp van de klant waar te maken.
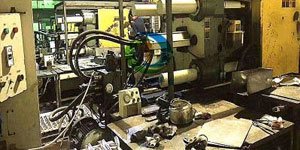
Contractfabrikant van spuitgietwerk. Mogelijkheden zijn onder meer koude kamer aluminium spuitgietonderdelen vanaf 0.15 lbs. tot 6 lbs., snelwissel instellen en machinaal bewerken. Diensten met toegevoegde waarde omvatten polijsten, trillen, ontbramen, stralen, schilderen, plateren, coaten, assembleren en bewerken. Materialen waarmee gewerkt is, zijn legeringen zoals 360, 380, 383 en 413.
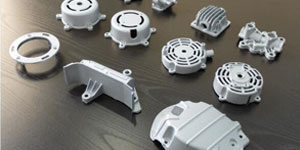
Hulp bij ontwerp van spuitgieten van zink/concurrent engineering. Custom fabrikant van precisie gegoten zink. Miniatuurgietstukken, hogedrukgietstukken, multi-slide gietstukken, conventionele gietstukken, eenheidsmatrijs en onafhankelijke spuitgietstukken en holteverzegelde gietstukken kunnen worden vervaardigd. Gietstukken kunnen worden vervaardigd in lengtes en breedtes tot 24 inch met een tolerantie van +/- 0.0005 inch.
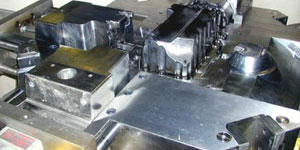
ISO 9001: 2015 gecertificeerde fabrikant van gegoten magnesium. Mogelijkheden zijn onder hoge druk spuitgieten van magnesium tot 200 ton hete kamer en 3000 ton koude kamer, gereedschapsontwerp, polijsten, gieten, machinale bewerking, poeder- en vloeistofverven, volledige QA met CMM-mogelijkheden , montage, verpakking & levering.
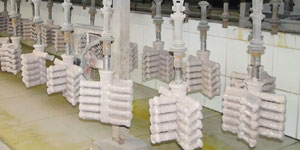
ITAF16949 gecertificeerd. Extra castingservice omvat: investering gieten,zandgieten,Zwaartekracht gieten, Verloren schuimafgietsel,Centrifugaal gieten,Vacuümgieten,Permanent vormgieten,. Mogelijkheden zijn onder meer EDI, technische assistentie, solide modellering en secundaire verwerking.
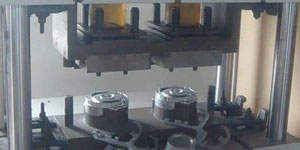
Gietindustrieën Casestudy's over onderdelen voor: auto's, fietsen, vliegtuigen, muziekinstrumenten, waterscooters, optische apparaten, sensoren, modellen, elektronische apparaten, behuizingen, klokken, machines, motoren, meubels, sieraden, mallen, telecom, verlichting, medische apparaten, fotografische apparaten, Robots, sculpturen, geluidsapparatuur, sportuitrusting, gereedschap, speelgoed en meer.
Wat kunnen we u hierna helpen doen?
∇ Ga naar de startpagina voor Spuitgieten China
→Gietonderdelen- Zoek uit wat we hebben gedaan.
→Gerangschikte tips over Spuitgietdiensten
By Minghe Die Casting Fabrikant: |Categorieën: Handige artikelen |Materiaal Tags: Aluminium gieten, Zink gieten, Magnesium gieten, Titanium gieten, Gieten van roestvrij staal, Messing gieten,Brons gieten,Video casten,Geschiedenis van ons bedrijf,Aluminium spuitgieten |Reacties uitgeschakeld