Snijbewerking van onderdelen voor poedermetallurgie (P/M)
Het gebruik van poedermetallurgie (P/M) om onderdelen voor aandrijfsystemen voor auto's te vervaardigen blijft groeien. Onderdelen vervaardigd volgens het P / M-proces hebben veel belangrijke en unieke voordelen. De resterende poreuze structuur die opzettelijk in deze delen is achtergebleven, is goed voor zelfsmering en geluidsisolatie. Complexe legeringen die moeilijk of onmogelijk te vervaardigen zijn door middel van traditioneel gietproces, kunnen worden geproduceerd met behulp van P/M-technologie. Onderdelen vervaardigd met deze technologie hebben meestal weinig of geen verwerkingscapaciteit, waardoor ze goedkoper zijn en minder materiaalverspilling. Helaas zijn achter de aantrekkingskracht van deze functies P / M-onderdelen moeilijk te bewerken.
Hoewel een van de oorspronkelijke bedoelingen van de P/M-industrie is om alle bewerkingen te elimineren, is dit doel nog niet bereikt. De meeste onderdelen kunnen alleen "dicht bij de uiteindelijke vorm" zijn en hebben nog wat afwerking nodig.
In vergelijking met giet- en smeedstukken is een kleine hoeveelheid materiaal die van P/M-onderdelen moet worden verwijderd echter een typisch slijtvast materiaal.
Poreuze structuur is een van de kenmerken die ervoor zorgen dat p/M-onderdelen een breed scala aan toepassingen hebben, maar de standtijd zal ook worden beschadigd door poreuze structuur. Poreuze structuur kan olie en geluid opslaan, maar leidt ook tot micro-intermitterend snijden. Bij het heen en weer bewegen van het gat naar de vaste deeltjes, wordt de gereedschapspunt continu beïnvloed, wat kan leiden tot een zeer kleine vervorming van de vermoeidheidsbreuk en een fijne randinstorting langs de snijkant. Om het nog erger te maken, zijn de deeltjes meestal erg hard. Zelfs als de macrohardheid van het gemeten materiaal tussen de 20 en 35 graden ligt, is de deeltjesgrootte van het onderdeel maar liefst 60 graden. Deze harde deeltjes veroorzaken ernstige en snelle snijkantslijtage. Veel p/M-onderdelen zijn warmtebehandelbaar en de hardheid en sterkte van het materiaal zijn hoger na warmtebehandeling. Ten slotte zal het oppervlak van het materiaal door de sinter- en warmtebehandelingstechnologie en de gebruikte gassen harde en slijtvaste oxiden en/of carbiden bevatten.
Prestaties van P / M-onderdelen
De meeste eigenschappen van P/M-onderdelen, inclusief bewerkbaarheid, zijn niet alleen gerelateerd aan de chemische samenstelling van de legering, maar ook aan het porositeitsniveau van de poreuze structuur. De porositeit van veel constructiedelen is tot 15% ~ 20%. De porositeit van onderdelen die als filtratie-inrichtingen worden gebruikt, kan oplopen tot 50%. Aan de andere kant van de serie is de porositeit van gesmede of heupdelen slechts 1% of minder. Deze materialen worden bijzonder belangrijk in auto- en vliegtuigtoepassingen omdat ze een hogere sterkte kunnen bereiken.
De treksterkte, taaiheid en taaiheid van de P/M-legering zullen toenemen met de toename van de dichtheid, en de bewerkbaarheid kan ook worden verbeterd, omdat de porositeit schadelijk is voor de gereedschapspunt.
De toename van het porositeitsniveau kan de geluidsisolatieprestaties van onderdelen verbeteren. De dempingsoscillatie in standaardonderdelen wordt aanzienlijk verminderd in P / M-onderdelen, wat erg belangrijk is voor werktuigmachines, airconditioning-blaaspijpen en pneumatisch gereedschap. Hoge porositeit is ook nodig voor zelfsmerende tandwielen.
Moeilijkheden bij machinale bewerking
Hoewel een van de doelen van de continue ontwikkeling van de P/M-industrie is om machinale bewerking te elimineren, en een van de belangrijkste attracties van het P/M-proces is dat er slechts een kleine hoeveelheid bewerking nodig is, hebben veel onderdelen nog steeds een nabehandeling nodig om te verkrijgen hogere nauwkeurigheid of betere oppervlakteafwerking. Helaas is het bewerken van deze onderdelen uiterst moeilijk. De meeste problemen worden veroorzaakt door porositeit. Porositeit leidt tot microvermoeidheid van de snijkant. De snijkant snijdt voortdurend in en uit. Het gaat tussen deeltjes en gaten. Herhaalde kleine impact leidt tot kleine scheurtjes op de snijkant.
Deze vermoeiingsscheuren groeien totdat de snijkant instort. Dit soort micro-afbreekrand is meestal erg klein en vertoont meestal normale schurende slijtage.
Porositeit vermindert ook de thermische geleidbaarheid van P / M-onderdelen, wat resulteert in hoge temperaturen op de snijkant en kraterslijtage en vervorming veroorzaakt. De inwendig verbonden poreuze structuur verschaft een pad voor de afvoer van snijvloeistof uit het snijgebied. Dit kan hete scheuren of vervorming veroorzaken, vooral bij het boren.
De toename van het oppervlak veroorzaakt door interne poreuze structuur leidt ook tot oxidatie en / of carbonisatie tijdens warmtebehandeling. Zoals eerder vermeld zijn deze oxiden en carbiden hard en slijtvast.
De poreuze structuur geeft ook het falen van de hardheidsaflezing van het onderdeel, wat uiterst belangrijk is. Wanneer de macrohardheid van een P/M-onderdeel opzettelijk wordt gemeten, omvat deze de factor gathardheid. De poreuze structuur leidt tot het instorten van de structuur en geeft de verkeerde indruk van relatief zachte delen. De deeltjes zijn veel harder. Zoals hierboven beschreven, is het verschil dramatisch.
Ook het bestaan van insluitsels in PM-delen is nadelig. Tijdens het machinaal bewerken worden deze deeltjes van het oppervlak omhoog getrokken en ontstaat er een kras of kras op het oppervlak van het onderdeel wanneer het voor het gereedschap wordt gewreven. Deze insluitsels zijn meestal groot en laten zichtbare gaten op het oppervlak van het onderdeel achter.
Het verschil in koolstofgehalte leidt tot de inconsistentie van de bewerkbaarheid. Het koolstofgehalte van de fc0208-legering varieert bijvoorbeeld van 0.6% tot 0.9%. Een partij materialen met 0.9% koolstofgehalte is relatief hard, wat resulteert in een slechte standtijd. De andere partij materialen met een koolstofgehalte van 0.6% heeft een uitstekende standtijd. Beide legeringen vallen binnen het toegestane bereik.
Het uiteindelijke bewerkingsprobleem is gerelateerd aan het type snede dat optreedt op het P / M-onderdeel. Omdat het onderdeel dicht bij de uiteindelijke vorm is, is de snijdiepte meestal erg ondiep. Dit vereist een vrije snijkant. Spaanopbouw op de snijkant leidt vaak tot microchips.
Verwerking technologie
Om deze problemen op te lossen, worden verschillende technologieën (uniek voor de industrie) toegepast. De poreuze oppervlaktestructuur wordt vaak afgedicht door infiltratie. Extra vrij snijden is meestal vereist. Onlangs zijn verbeterde poederproductietechnieken gebruikt die zijn ontworpen om de reinheid van het poeder te vergroten en oxiden en carbiden tijdens warmtebehandeling te verminderen.
De poreuze structuur met gesloten oppervlak wordt bereikt door infiltratie van metaal (meestal koper) of polymeer. Er is gespeculeerd dat infiltratie als smeermiddel werkt. De meeste experimentele gegevens laten zien dat het echte voordeel ligt in het sluiten van de poreuze oppervlaktestructuur en het voorkomen van microvermoeidheid van de snijkant. De vermindering van chatter verbetert de standtijd en oppervlakteafwerking. Het meest dramatische gebruik van infiltratie laat een 200% langere standtijd zien wanneer de poreuze structuur gesloten is.
Van additieven zoals MNS, s, MoS2, MgSiO3 en BN is bekend dat ze de standtijd verlengen. Deze additieven verbeteren de bewerkbaarheid door het gemakkelijker te maken voor spanen om van het werkstuk te scheiden, spanen te breken, spaanophoping te voorkomen en de snijkant te smeren. Het verhogen van de hoeveelheid additieven kan de bewerkbaarheid verbeteren, maar de sterkte en taaiheid verminderen.
Poederverstuivingstechnologie om sinter- en warmtebehandelingsovengas te regelen, maakt het mogelijk om schoon poeder en onderdelen te produceren, waardoor het optreden van insluitsels en oppervlakteoxidecarbiden wordt geminimaliseerd.
Gereedschapsmateriaal
De meest gebruikte gereedschappen in de P / M-industrie zijn die materialen die slijtvast, randscheurbestendig en spaanvrij zijn onder de voorwaarde van een goede oppervlakteafwerking. Deze kenmerken zijn nuttig voor elke bewerking, vooral voor P / M-onderdelen. De gereedschapsmaterialen in deze categorie zijn kubisch boornitride (CBN) gereedschappen, ongecoate en gecoate cermets en verbeterde gecoate gesinterde gecementeerde carbiden.
CBN-gereedschappen zijn aantrekkelijk vanwege hun hoge hardheid en slijtvastheid. Dit gereedschap wordt al vele jaren gebruikt bij de bewerking van staal en gietijzer met een Rockwell-hardheid van 45 en hoger. Vanwege de unieke eigenschappen van de P/M-legering en het significante verschil tussen microhardheid en macrohardheid, kunnen CBN-gereedschappen echter worden gebruikt voor P/M-onderdelen met een Rockwell-hardheid van 25. De belangrijkste parameter is de hardheid van deeltjes. Wanneer de hardheid van deeltjes Rockwell 50 graden overschrijdt, zijn CBN-gereedschappen beschikbaar, ongeacht de macrohardheidswaarde. De voor de hand liggende beperking van deze gereedschappen is hun gebrek aan taaiheid. In het geval van intermitterend snijden of hoge porositeit, is randversterking inclusief negatief afschuinen en zwaar honen noodzakelijk. Eenvoudig licht snijden kan worden gedaan met een geslepen snijkant.
Er zijn verschillende materialen van CBN die effectief zijn. Het materiaal met de beste taaiheid bestaat voornamelijk uit het hele CBN. Ze hebben een uitstekende taaiheid, zodat ze kunnen worden gebruikt voor voorbewerken. Hun beperkingen zijn meestal gerelateerd aan de oppervlakteafwerking. Het wordt grotendeels bepaald door de individuele CBN-deeltjes waaruit het gereedschap bestaat. Wanneer de deeltjes van de snijkant vallen, zullen ze het oppervlak van het werkstukmateriaal aantasten. Het is echter niet zo erg dat het fijnstofgereedschap van één deeltje valt.
Het gewoonlijk gebruikte CBN-materiaal heeft een hoog CBN-gehalte en een gemiddelde deeltjesgrootte. Het CBN-afwerkingsblad is fijnkorrelig en het CBN-gehalte is laag. Ze zijn het meest effectief wanneer licht snijden en oppervlakteafwerking vereist zijn of wanneer de legering die wordt verwerkt bijzonder hard is.
Bij veel snijtoepassingen is de standtijd onafhankelijk van het materiaaltype. Met andere woorden, elk CBN-materiaal kan een vergelijkbare standtijd bereiken. In deze gevallen is de materiaalkeuze voornamelijk gebaseerd op de laagste kosten van elke snijkant. Eén rond mes heeft een heel CBN-bovenoppervlak en kan vier of meer snijkanten bieden, wat goedkoper is dan vier ingelegde CBN-messen.
Wanneer de hardheid van P / M-onderdelen lager is dan Rockwell 35 graden, en de hardheid van deeltjes binnen het bereik ligt, is cermet meestal een van de keuzes. Cermets zijn erg hard, kunnen spaanopbouw effectief voorkomen en zijn bestand tegen hoge snelheden. Omdat cermets altijd zijn gebruikt voor het met hoge snelheid en nabewerken van staal en roestvrij staal, hebben ze bovendien meestal ideale geometrische groeven die geschikt zijn voor dicht bij gevormde onderdelen.
De cermets van vandaag zijn ingewikkeld in de metallurgie, met maximaal 11 legeringselementen. Ze zijn meestal gesinterd uit TiCN-deeltjes en Ni Mo-lijm. TiCN biedt hardheid, weerstand tegen spaanvorming en chemische stabiliteit die belangrijk zijn voor het succesvolle gebruik van cermets. Bovendien hebben deze gereedschappen meestal een hoog lijmgehalte, waardoor ze een goede taaiheid hebben. Kortom, ze hebben alle kenmerken om P / M-legeringen effectief te verwerken. Verschillende soorten cermets zijn effectief, net als wolfraamcarbide gesinterd gecementeerd carbide, hoe hoger het gehalte aan bindmiddel, hoe beter de taaiheid.
Een bekende relatief nieuwe ontwikkeling is dat medium temperature chemical vapour deposition (mtcvd) ook een voordeel biedt voor de P/M industrie. Mtcvd behoudt alle slijtvastheid en kraterslijtageweerstand van de traditionele chemische dampafzetting (CVD), maar verbetert ook objectief de taaiheid. De toename van de taaiheid komt voornamelijk door de afname van scheuren. De coating wordt bij hoge temperatuur afgezet en vervolgens afgekoeld in de oven. De coating bevat barsten wanneer het gereedschap kamertemperatuur bereikt als gevolg van inconsistente thermische uitzetting. Net als bij krassen op vlak glas, verminderen deze barsten de sterkte van de snijkant. De lagere afzettingstemperatuur van mtcvd leidt tot een lagere scheurfrequentie en een betere taaiheid van de snijkant.
Wanneer het substraat van CVD-coating en mtcvd-coating dezelfde kenmerken en randafwerking hebben, kan het verschil in taaiheid worden aangetoond. Bij gebruik in toepassingen waar randtaaiheid vereist is, zijn de prestaties van mtcvd-coating beter dan die van CVD-coating. Door analyse, bij het bewerken van P / M-onderdelen met poreuze structuur, is de randtaaiheid belangrijk. Mtcvd-coating is beter dan CVD-coating.
De Physical Vapour Deposition (PVD) coating is dunner en minder slijtvast dan mtcvd of CVD coating. PVD-coating is echter bestand tegen aanzienlijke impact bij het aanbrengen. PVD-coating is effectief wanneer snijden slijtage veroorzaakt, CBN en cermets zijn te broos en vereisen een uitstekende oppervlakteafwerking.
De snijkant van C-2 hardmetaal kan bijvoorbeeld worden bewerkt fc0205 met een lijnsnelheid van 180 m/min en een voedingssnelheid van 0.15 mm/omwenteling. Na het bewerken van 20 onderdelen kan de spaanopbouw micro-instorting veroorzaken. Wanneer PVD-titaannitride (TIN)-coating wordt gebruikt, wordt de spaanopbouw beperkt en wordt de standtijd verlengd. Wanneer tincoating wordt gebruikt voor deze test, wordt verwacht dat de schurende slijtage-eigenschappen van P / M-onderdelen effectiever zijn met TiCN-coating. TiCN heeft bijna dezelfde weerstand tegen chipopbouw als tin, maar is harder en slijtvaster dan tin.
De poreuze structuur is belangrijk en beïnvloedt de bewerkbaarheid van de fc0208-legering. Wanneer de poreuze structuur en kenmerken veranderen, bieden verschillende gereedschapsmaterialen overeenkomstige voordelen. Wanneer de dichtheid laag is (6.4 g/cm3), is de macrohardheid laag. In dit geval biedt mtcvd gecoat hardmetaal de beste standtijd. De microvermoeidheid van de snijkant is erg belangrijk en de snijkanttaaiheid is erg belangrijk. In dit geval zorgt een cermetblad met een goede taaiheid voor een maximale standtijd.
Bij het produceren van dezelfde legering met een dichtheid van 6.8 g/cm3, wordt abrasieve slijtage belangrijker dan randscheuren. In dit geval zorgt de mtcvd-coating voor de beste standtijd. PVD gecoat hardmetaal wordt gebruikt om de twee soorten extreem harde onderdelen te testen, en het breekt wanneer het de snijkant raakt.
Wanneer de snelheid toeneemt (de lineaire snelheid is meer dan 300 meter per minuut), zullen cermets en zelfs gecoate cermets kraterslijtage veroorzaken. Gecoat hardmetaal is meer geschikt, vooral wanneer de snijkanttaaiheid van gecoat hardmetaal goed is. Mtcvd-coating is vooral effectief voor gecementeerd carbide met een kobaltrijk gebied.
Cermets worden het meest gebruikt bij draaien en kotteren. PVD-gecoate gecementeerde carbiden zijn ideaal voor draadbewerking omdat lagere snelheden en meer aandacht voor opbouw kunnen worden verwacht.
Bewaar de bron en het adres van dit artikel voor herdruk:Snijbewerking van onderdelen voor poedermetallurgie (P/M)
Minghe Casting Company is toegewijd aan het produceren en leveren van hoogwaardige en hoogwaardige gietstukken (het assortiment metalen spuitgietonderdelen omvat voornamelijk: Dunwandig spuitgieten,Hot Chamber Spuitgieten,Koude kamer spuitgieten),Ronde Service (Die Casting Service,CNC-bewerking,Matrijzen maken, Oppervlaktebehandeling). Elk aangepast aluminium spuitgieten, magnesium of Zamak / zink spuitgieten en andere gietstukken zijn welkom om contact met ons op te nemen.
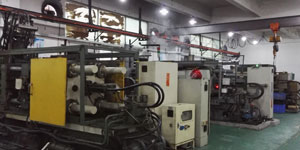
Onder controle van ISO9001 en TS 16949 worden alle processen uitgevoerd door honderden geavanceerde spuitgietmachines, 5-assige machines en andere faciliteiten, variërend van blasters tot Ultra Sonic-wasmachines. Minghe heeft niet alleen geavanceerde apparatuur, maar heeft ook professionele team van ervaren ingenieurs, operators en inspecteurs om het ontwerp van de klant waar te maken.
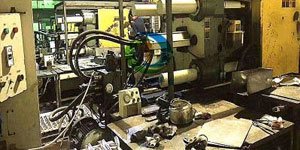
Contractfabrikant van spuitgietwerk. Mogelijkheden zijn onder meer koude kamer aluminium spuitgietonderdelen vanaf 0.15 lbs. tot 6 lbs., snelwissel instellen en machinaal bewerken. Diensten met toegevoegde waarde omvatten polijsten, trillen, ontbramen, stralen, schilderen, plateren, coaten, assembleren en bewerken. Materialen waarmee gewerkt is, zijn legeringen zoals 360, 380, 383 en 413.
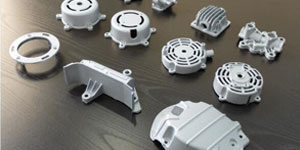
Hulp bij ontwerp van spuitgieten van zink/concurrent engineering. Custom fabrikant van precisie gegoten zink. Miniatuurgietstukken, hogedrukgietstukken, multi-slide gietstukken, conventionele gietstukken, eenheidsmatrijs en onafhankelijke spuitgietstukken en holteverzegelde gietstukken kunnen worden vervaardigd. Gietstukken kunnen worden vervaardigd in lengtes en breedtes tot 24 inch met een tolerantie van +/- 0.0005 inch.
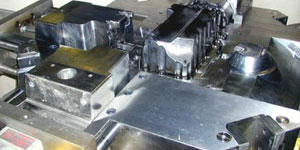
ISO 9001: 2015 gecertificeerde fabrikant van gegoten magnesium. Mogelijkheden zijn onder hoge druk spuitgieten van magnesium tot 200 ton hete kamer en 3000 ton koude kamer, gereedschapsontwerp, polijsten, gieten, machinale bewerking, poeder- en vloeistofverven, volledige QA met CMM-mogelijkheden , montage, verpakking & levering.
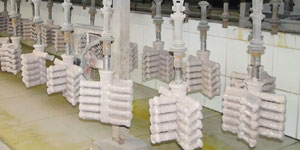
ITAF16949 gecertificeerd. Extra castingservice omvat: investering gieten,zandgieten,Zwaartekracht gieten, Verloren schuimafgietsel,Centrifugaal gieten,Vacuümgieten,Permanent vormgieten,. Mogelijkheden zijn onder meer EDI, technische assistentie, solide modellering en secundaire verwerking.
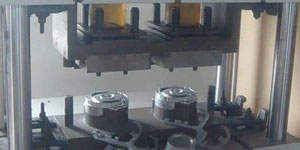
Gietindustrieën Casestudy's over onderdelen voor: auto's, fietsen, vliegtuigen, muziekinstrumenten, waterscooters, optische apparaten, sensoren, modellen, elektronische apparaten, behuizingen, klokken, machines, motoren, meubels, sieraden, mallen, telecom, verlichting, medische apparaten, fotografische apparaten, Robots, sculpturen, geluidsapparatuur, sportuitrusting, gereedschap, speelgoed en meer.
Wat kunnen we u hierna helpen doen?
∇ Ga naar de startpagina voor Spuitgieten China
→Gietonderdelen- Zoek uit wat we hebben gedaan.
→Gerangschikte tips over Spuitgietdiensten
By Minghe Die Casting Fabrikant: |Categorieën: Handige artikelen |Materiaal Tags: Aluminium gieten, Zink gieten, Magnesium gieten, Titanium gieten, Gieten van roestvrij staal, Messing gieten,Brons gieten,Video casten,Geschiedenis van ons bedrijf,Aluminium spuitgieten |Reacties uitgeschakeld