Verschillen in de stollingskenmerken van nodulair gietijzer
Over het algemeen hebben gietijzeren gietstukken een veel grotere neiging tot krimp en porositeit dan gietstukken van grijs gietijzer. Het voorkomen van krimpdefecten is vaak een zeer moeilijk probleem in het procesontwerp. In dit opzicht is de ervaring die is samengevat van de werkelijke productie zeer inconsistent, en elk heeft zijn eigen meningen: sommige mensen denken dat het principe van sequentiële stolling moet worden gevolgd en dat een grote stijgbuis in de uiteindelijke stollingspositie moet worden geplaatst om het volume aan te vullen gegenereerd tijdens het stollingsproces van het gieten. krimp; Sommige mensen denken dat onderdelen van nodulair gietijzer alleen kleine stootborden nodig hebben, en soms kunnen degelijke gietstukken worden gemaakt zonder stootborden.
Om de productiesnelheid van het proces te maximaliseren en tegelijkertijd de kwaliteit van de gietstukken te waarborgen, is het niet voldoende om de chemische samenstelling van gietijzer te controleren. Op basis van het begrijpen van de stollingskenmerken van nodulair gietijzer, is het noodzakelijk om het smelten, sferoïdisatie, inenting en behandeling van gietijzer effectief te beheersen. Tijdens het hele proces van gieten moet de stijfheid van de mal effectief worden gecontroleerd.
1. De stollingskenmerken van nodulair gietijzer:
Het grootste deel van het nodulair gietijzer dat in de werkelijke productie wordt gebruikt, ligt dicht bij de eutectische samenstelling. Dikwandige gietstukken gebruiken hypoeutectische samenstelling en dunwandige gietstukken gebruiken hypereutectische samenstelling, maar ze zijn niet ver van eutectische samenstelling.
Voor nodulair gietijzer met eutectische en hypereutectische componenten worden tijdens de eutectische stolling eerst kleine grafietballen uit de vloeibare fase neergeslagen. Zelfs voor nodulair gietijzer met hypo-eutectische samenstelling zullen, als gevolg van de toename van de mate van onderkoeling van het gesmolten ijzer na de sferoïdisatie en inoculatiebehandeling, eerst kleine grafietballen worden neergeslagen bij een temperatuur die veel hoger is dan de evenwichtseutectische overgangstemperatuur. De eerste batch kleine grafietbolletjes is gevormd bij temperaturen van 1300°C of hoger.
In het daaropvolgende stollingsproces, als de temperatuur daalt, groeien enkele van de eerste kleine grafietbolletjes op, en sommige worden opnieuw opgelost in het gesmolten ijzer, en nieuwe grafietbolletjes zullen ook worden neergeslagen. Het neerslaan en groeien van grafietbolletjes vindt plaats in een breed temperatuurbereik.
Wanneer de grafietbol opgroeit, neemt het koolstofgehalte in het gesmolten ijzer eromheen af en zal er een austeniet omhulsel rond de grafietbol worden gevormd. De vormingstijd van de austenietkorst is gerelateerd aan de afkoelsnelheid van het gietstuk in de mal: de afkoelsnelheid is hoog en de koolstof in het gesmolten ijzer heeft geen tijd om uniform te diffunderen en de austenietkorst wordt eerder gevormd; de afkoelsnelheid is laag, wat gunstig is voor de afkoelsnelheid in het gesmolten ijzer. De koolstof diffundeert gelijkmatig en de austenietkorst wordt later gevormd.
Voordat de austenietschaal wordt gevormd, komt de grafietbal direct in contact met het gesmolten ijzer met een hoog koolstofgehalte, en de koolstof in het gesmolten ijzer is gemakkelijk te diffunderen in de grafietbal, zodat de grafietbal opgroeit. Nadat de austenietschaal is gevormd, wordt de diffusie van koolstof in het gesmolten ijzer naar de grafietballen belemmerd en neemt de groeisnelheid van de grafietballen sterk af. Omdat de latente warmte van kristallisatie die vrijkomt wanneer grafiet wordt neergeslagen uit gesmolten ijzer groot is, ongeveer 3600 J/g, is de latente warmte van kristallisatie die vrijkomt wanneer austeniet wordt neergeslagen uit gesmolten ijzer minder, ongeveer 200 J/g, waardoor een austenietschil rond de grafietbol De groei van grafietbolletjes wordt belemmerd, wat het vrijkomen van latente kristallisatiewarmte aanzienlijk zal vertragen. Onder deze omstandigheden hangt de voortgang van eutectische stolling af van het verder verlagen van de temperatuur om nieuwe kristalkernen te produceren. Daarom moet de eutectische transformatie van gietijzer met sferoïdaal grafiet worden voltooid binnen een relatief groot temperatuurbereik, en het stoltemperatuurbereik is twee keer of meer dan dat van grijs gietijzer, dat typische pasta-achtige stollingskenmerken heeft.
Kortom, de stollingseigenschappen van nodulair gietijzer hebben voornamelijk de volgende aspecten.
1. Breed stollingstemperatuurbereik:
Uit het evenwichtsdiagram van de ijzer-koolstoflegering blijkt dat het bereik van de stollingstemperatuur niet breed is in de buurt van de eutectische samenstelling. In feite wijkt het stollingsproces na de sferoïdisatie en entbehandeling van gesmolten ijzer ver af van de evenwichtsomstandigheden. Bij ongeveer 150°C boven de eutectische overgangstemperatuur (1150°C) beginnen grafietbolletjes neer te slaan, en de temperatuur waarbij de eutectische overgang weer eindigt Het kan ongeveer 50°C lager zijn dan de evenwichtseutectische overgangstemperatuur.
Een legering met een dergelijk breed stoltemperatuurbereik wordt op een pasta-achtige manier stollen, en het is moeilijk om opeenvolgende stolling van gietstukken te bereiken. Daarom is, volgens het ontwerpprincipe van de stijgbuis van de stalen gietstukken, het procesplan voor het realiseren van de opeenvolgende stolling van de gietstukken en het plaatsen van een grote stijgleiding bij de laatste gestolde hete verbinding niet erg geschikt.
Omdat grafietbolletjes bij zeer hoge temperaturen worden geprecipiteerd en eutectische transformatie plaatsvindt, bestaan de twee fasen vloeibaar en vast gedurende lange tijd naast elkaar, en krimp van vloeistof en krimp door stollen treden gelijktijdig op tijdens het stollen van gesmolten ijzer. Daarom is het onmogelijk om de vloeistofkrimp volledig aan te vullen via het poortsysteem en de stijgbuis zoals stalen gietstukken.
2. De precipitatie van grafiet tijdens de eutectische transformatie leidt tot volume-expansie
In de buurt van de eutectische temperatuur is de dichtheid van austeniet ongeveer 7.3 g/cm3 en de dichtheid van grafiet ongeveer 2.15 g/cm3. Tijdens het stollen van het gietstuk zal het neerslaan van grafiet de volume-expansie van het systeem veroorzaken. Ongeveer 1% (massafractie) neergeslagen grafiet kan een volume-expansie van 3.4% veroorzaken.
Correct gebruik van de grafitisatie-expansie in gietijzer kan de volumekrimp tijdens het stollen effectief compenseren. Onder bepaalde omstandigheden kunnen degelijke gietstukken worden geproduceerd zonder stootborden.
Benadrukt moet worden dat zowel grijs gietijzer als nodulair gietijzer grafiet neerslaan tijdens het eutectische transformatieproces en volume-expansie ondergaan. Vanwege de verschillende grafietmorfologie en het groeimechanisme in de twee gietijzers, is het effect van grafitisatie-expansie op de gietprestaties van gietijzer echter ook heel anders.
Voor het vlokgrafiet in het eutectische cluster van grijs gietijzer groeit bij voorkeur de punt die in direct contact staat met het gesmolten ijzer. Het grootste deel van de volume-expansie die wordt veroorzaakt door de groei van grafiet, werkt op het gesmolten ijzer in contact met de grafietpunt, wat gunstig is om het te dwingen te vullen met austeniet-takken. De opening tussen hen maakt het gieten dichter.
Het grafiet in nodulair gietijzer wordt gekweekt onder de voorwaarde dat het wordt omgeven door een austenietschaal. De volume-expansie die optreedt wanneer de grafietbol opgroeit, vindt voornamelijk plaats door de austenietschaal die inwerkt op de aangrenzende eutectische clusters, wat kan worden Uitknijpen vergroot de opening tussen de eutectische clusters, en het is gemakkelijk om in te werken op de malwanden van de mal door de eutectische clusters, waardoor de malwanden bewegen.
3. Grafitisatie-expansie tijdens het stollen van het gietstuk is gemakkelijk om de mal in de muur te laten bewegen;
Nodulair gietijzer stolt in een pasta-achtige stollingsmethode. Wanneer het gietstuk begint te stollen, is de buitenste oppervlaktelaag van het gietstuk op het grensvlak tussen vorm en metaal veel dunner dan grijs gietijzer en groeit langzaam. Ook na lange tijd is de oppervlaktelaag nog sterk. Dunne schaal met lage stijfheid. Wanneer gegrafitiseerde uitzetting binnenin optreedt, kan de buitenste schil naar buiten bewegen als deze niet sterk genoeg is om de uitzettingskracht te weerstaan. Als de stijfheid van de mal slecht is, zal de wandbeweging optreden en zal de holte uitzetten. Als gevolg hiervan wordt niet alleen de maatnauwkeurigheid van het gietstuk beïnvloed, maar kan de krimp na grafitisatie-expansie niet worden aangevuld, en zullen defecten zoals krimpholte en porositeit in het gietstuk worden gegenereerd.
4. Het koolstofgehalte in eutectisch austeniet is hoger dan dat in grijs gietijzer
Volgens een onderzoeksrapport van RW Heine in de Verenigde Staten is tijdens de eutectische stolling van nodulair gietijzer het koolstofgehalte van austeniet hoger dan dat van grijs gietijzer.
Wanneer grijs gietijzer eutectisch stolt, komen de grafietvlokken in het eutectische cluster in direct contact met zowel austeniet als gesmolten ijzer met een hoog koolstofgehalte. De koolstof in het gesmolten ijzer diffundeert niet alleen in grafiet via austeniet, maar diffundeert ook direct in de grafietvlokken, dus het koolstofgehalte in de austeniet op het grensvlak van gesmolten ijzer en austeniet is relatief laag, ongeveer 1.55%.
Wanneer nodulair gietijzer eutectisch gestold is, komen de grafietballen in het eutectische cluster alleen in contact met de austenietschaal, niet met het gesmolten ijzer. Wanneer de grafietballen opgroeien, diffundeert de koolstof in het gesmolten ijzer in de grafietballen door de austenietschaal. Daarom is het koolstofgehalte in het austeniet bij het gesmolten ijzer-austeniet-grensvlak relatief hoog en bereikt het ongeveer 2.15%.
Tijdens eutectische stolling van nodulair gietijzer kan het koolstofgehalte in austeniet hoger zijn. Onder dezelfde omstandigheden van koolstof- en siliciumgehalte, als dezelfde koelsnelheid wordt gehandhaafd, zal de hoeveelheid neergeslagen grafiet minder zijn. Daarom, wanneer het eutectische stolt, zal de volumekrimp iets groter zijn dan die van grijs gietijzer. Dit is ook een van de redenen waarom gietstukken van nodulair gietijzer meer vatbaar zijn voor krimp en porositeit. Het handhaven van een lage afkoelsnelheid tijdens het stollingsproces is een factor die bevorderlijk is voor de analyse van grafietlading.
Onder de omstandigheden die grafitisatie voldoende kunnen maken, is het koolstofgehalte in eutectische austeniet (dat wil zeggen de maximale vaste oplosbaarheid van koolstof in austeniet) gerelateerd aan het siliciumgehalte in gietijzer en kan in het algemeen worden berekend met de volgende formule.
De maximale vaste oplosbaarheid van koolstof in austeniet CE = 2.045-0.178 Si
2. Volumeverandering tijdens het stollen van gietijzeren gietstukken
Vanaf het moment dat het gesmolten ijzer in de mal wordt gegoten, tot het einde van de eutectische stolling en de volledige stolling van het gietstuk, zal het gietijzer in de holte vloeistofkrimp ondergaan, volume-expansie veroorzaakt door de precipitatie van primair grafiet en stolling krimp veroorzaakt door de precipitatie van eutectisch austeniet, Verschillende volumeveranderingen zoals volume-expansie veroorzaakt door precipitatie van eutectisch grafiet. Om de beschrijving van de volumeverandering tijdens het stollen van nodulair gietijzer te vergemakkelijken, is het noodzakelijk om te verwijzen naar het vereenvoudigde fasediagram getoond in FIG. 2.
1. Vloeibare krimp van gesmolten ijzer
Nadat het gesmolten ijzer in de mal is gekomen, krimpt het volume naarmate de temperatuur daalt. De hoeveelheid vloeibare krimp van gesmolten ijzer zal variëren als gevolg van de chemische samenstelling en verwerkingsomstandigheden, maar dit wordt meestal genegeerd. Over het algemeen wordt rekening gehouden met een volumekrimp van 1.5% voor elke temperatuurdaling van 100 °C. Het temperatuurbereik waarin vloeistofkrimp optreedt, wordt berekend op basis van de daling van de giettemperatuur naar de evenwichtseutectische overgangstemperatuur (1150 °C). Wanneer de nodulair gietijzeren onderdelen bij verschillende giettemperaturen worden gegoten, wordt de vloeistofkrimp weergegeven in Tabel 1.
Tabel 1 Vloeibare krimp van nodulair gietijzer bij gieten bij verschillende temperaturen
Giettemperatuur (℃) | 1400 | 1350 | 1300 |
Vloeistofkrimp (%) | 3.75 | 3.00 | 2.25 |
2. Volume-expansie veroorzaakt door de precipitatie van primair grafiet
Hoewel hypoeutectisch gietijzer met sferoïdaal grafiet kleine grafietbolletjes boven de liquidustemperatuur zal neerslaan, is de hoeveelheid erg klein en meestal verwaarloosbaar.
Zoals eerder vermeld, kan elke 1% (massafractie) neergeslagen grafiet een volume-expansie van 3.4% produceren. Daarom is de volume-expansie veroorzaakt door de precipitatie van primair grafiet gelijk aan 3.4G.
Tabel 2 toont de volume-expansie veroorzaakt door de precipitatie van primair grafiet uit verschillende nodulair gietijzer met verschillende koolstof- en siliciumgehaltes.
Hoewel het geprecipiteerde primaire grafiet de vloeibare krimp tijdens het stollen van gietijzer kan compenseren, kunnen bij gietstukken met een wanddikte van meer dan 40 mm defecten zoals grafietinsluitingen of grafietdrijven optreden. In dit geval moet speciale aandacht worden besteed aan het beheersen van het koolstof- en siliciumgehalte.
Tabel 2 Volume-expansie veroorzaakt door de precipitatie van primair grafiet in verschillende nodulair gietijzer
- Koolstofgehalte van gietijzer (%): 3.6/3.5/3.6/3.7/3.6/3.7/3.8
- Siliciumgehalte van gietijzer (%): 2.2/2.4/2.4/2.4/2.6/2.6/2.6
- Eutectisch koolstofgehalte CC (%)/3.54/3.47/3.47/3.47/3.40/3.40/3.40
- Neerslaghoeveelheid primair grafiet G aanvankelijk (%)/0.06/0.03/0.13/0.24/0.21/0.31/0.41
- Volume-expansie veroorzaakt door precipitatie van primair grafiet (%): 0.21/0.10/0.44/0.82/0.71/1.05/1.39
3. Volumekrimp veroorzaakt door precipitatie van eutectisch austeniet
Om de volumekrimp te berekenen die wordt veroorzaakt door de precipitatie van eutectisch austeniet, de massafractie van de eutectische vloeistoffase (hierna de "eutectische vloeistoffasehoeveelheid" genoemd), de hoeveelheid vloeistofkrimp en het eutectische austeniet dat uit de eenheid eutectische vloeibare fase moet worden overwogen Volume- en stollingskrimp. De berekening van vloeistofkrimp is hierboven beschreven. De stollingskrimp van uit de eutectische vloeibare fase neergeslagen austeniet is in het algemeen 3.5%.
Tabel 3 toont de volumekrimp veroorzaakt door de precipitatie van eutectisch austeniet in verschillende nodulair gietijzer met verschillende koolstof- en siliciumgehaltes.
Tabel 3 Volumekrimp veroorzaakt door precipitatie van eutectisch austeniet in verschillende nodulair gietijzer
- Koolstofgehalte van gietijzer (%) 3.6/3.5/3.6/3.7/3.6/3.7/3.8
- Siliciumgehalte van gietijzer (%)/2.2/2.4/2.4/2.4/2.6/2.6/2.6
- Hoeveelheid eutectische vloeibare fase (%) 99.94/99.97/99.87/99.76/99.79/99.69/99.59
- De hoeveelheid austeniet geprecipiteerd in de eenheidseutectische vloeistoffase (%)~98.1
- Volumekrimp van austeniet bij gieten bij 1400℃ (%)/3.30/3.30/3.30/3.30/3.30/3.29/3.29
- Volumekrimp van austeniet bij gieten bij 1350℃ (%)/3.33/3.33/3.33/3.32/3.32/3.32/3.32
- Volumekrimp van austeniet bij gieten bij 1300℃ (%) 3.35/3.35/3.35/3.35/3.35/3.34
Voor verschillende veelgebruikte nodulair gietijzeren, houd de giettemperatuur onder 1350℃. Onder de voorwaarde dat er geen wandbeweging van de mal is, kan de volume-uitzetting veroorzaakt door grafitisering tijdens het stollen van het gietstuk de vloeistofkrimp en stollingskrimp compenseren. Het is mogelijk om degelijke gietstukken te produceren zonder stootborden in te stellen. Wanneer de giettemperatuur 1400 is en een hoger koolstofequivalent wordt geselecteerd voor gietijzer, kan grafitisatie-expansie ook verschillende volumekrimp compenseren, maar deze methode is alleen geschikt voor dunwandige gietstukken, dikkere wandafgietsels zijn vatbaar voor grafietopname en slakken Grafiet drijvende defecten.
De informatie in tabel 5 is echter verkregen uit het evenwichtsdiagram en is gebaseerd op de veronderstelling dat de 'potentieel neergeslagen koolstof' tijdens het stollingsproces volledig wordt neergeslagen door grafietkristallen. Bij de daadwerkelijke productie moet het natuurlijk gebaseerd zijn op effectieve sferoïdisatie en inentingsbehandeling, en voldoende grafitisatie is essentieel. Voor gietstukken met hoge afkoelsnelheden en dunwandige gietstukken is, als gevolg van onvoldoende grafitisering tijdens eutectische stolling, de volume-uitzetting veroorzaakt door de precipitatie van eutectisch grafiet minder dan de bovengenoemde berekende waarde, en het is nog steeds gemakkelijk om defecten te produceren zoals krimpholten en krimpporositeit. .
Tegelijkertijd is ook de stijfheid van de matrijs een zeer belangrijke factor. Als de stijfheid van de gietvorm niet hoog is en de wandbeweging optreedt tijdens grafitisering en expansie, kan de krimp na expansie niet worden aangevuld en zullen er defecten zijn zoals krimpholte en krimpporositeit in het gietstuk.
3. Voorwaarden voor het realiseren van no-riser casting
Vanaf de voltooiing van het gieten tot het einde van het stollen, zullen vloeistofkrimp en stollingskrimp optreden in het gietstuk. Bovendien, omdat nodulair gietijzer wordt gestold in een pasta-achtige stollingsmethode, is het moeilijk om de vloeibare krimp volledig aan te vullen door het gietsysteem om stijgbuisvrij gieten te bereiken. De vloeistofkrimp en stollingskrimp van gietijzer moet worden gecompenseerd door de volume-expansie wanneer grafietkristallen worden neergeslagen. Hiervoor moet aan de volgende voorwaarden worden voldaan.
De metallurgische kwaliteit van gesmolten ijzer is goed
Onder normale omstandigheden is het koolstofequivalent beter om 4.3 of 4.4 te kiezen, en het koolstofequivalent kan op passende wijze worden verhoogd voor dunwandige gietstukken. Om de hoeveelheid neergeslagen grafiet te vergroten, is het, als het koolstofequivalent gelijk wordt gehouden, voordeliger om het koolstofgehalte te verhogen dan om het siliciumgehalte te verhogen.
De sferoïdiserende operatie moet strikt worden gecontroleerd. Op voorwaarde dat de globalisering van grafiet wordt gegarandeerd, moet de hoeveelheid resterend magnesium zoveel mogelijk worden verminderd en moet de massafractie van resterend magnesium op ongeveer 0.06% worden gehouden.
De inentingsbehandeling moet adequaat zijn. Naast de inoculatiebehandeling die tegelijkertijd met de sferoïdiseringsbehandeling wordt uitgevoerd, moet de instantinoculatie ook tijdens het gieten worden uitgevoerd. Dunwandige gietstukken kunnen het beste vooraf worden ingeënt voordat het gesmolten ijzer vrijkomt.
De afkoelsnelheid tijdens het stollen van het gietstuk mag niet te hoog zijn
Als de afkoelsnelheid van het gietstuk te hoog is, kan het grafiet niet volledig worden geanalyseerd tijdens het stollingsproces en is de grafitiseringsuitzetting niet voldoende om de krimp van het gietijzer te compenseren, en kan dus geen stijgbuisvrij gieten worden gerealiseerd.
Gieten op lage temperatuur
Om vloeistofkrimp te verminderen, kan de giettemperatuur het best worden geregeld onder 1350 , meestal 1320 ± 20 .
Vlokvormige binnenpoort gebruiken
Om te voorkomen dat het gesmolten ijzer uit de binnenste poort wordt geperst tijdens grafitisering en expansie, moet de binnenste poort snel stollen nadat het gesmolten ijzer met de mal is gevuld. Daarom moet, wanneer het gietschema zonder stijgbuis wordt toegepast, een dunne en brede binnenpoort worden gebruikt. , De verhouding van de breedte tot de dikte is over het algemeen 4 tot 5. Bij de selectie van de dikte van de binnenpoort moet ook rekening worden gehouden met de giettemperatuur en mag de binnenpoort niet stollen tijdens het gietproces.
Verbeter de stijfheid van de mal:
Om de uitzetting van de holte tijdens grafitisatie-expansie te voorkomen, is het verbeteren van de stijfheid van de mal een van de belangrijke voorwaarden om de kwaliteit van het gietstuk te waarborgen. Ongeacht het gebruik van klei-nat zandmodellering of verschillende zelfhardende zandmodellering, ongeacht hoeveel nadruk wordt gelegd op "beukende solide", het zal niet overdreven zijn.
Bij het maken van grotere gietstukken met zelfhardend zand, moeten gekoelde ijzeren of grafietblokken op het oppervlak van de mal worden geplaatst, overeenkomend met enkele dikke delen op het gietstuk. Koud ijzer en grafietblokken hebben natuurlijk een verkoelend effect, maar ze moeten ook een goed begrip hebben van hun rol bij het verbeteren van de stijfheid van de mal. In sommige gevallen worden vuurvaste stenen gebruikt in plaats van gekoelde ijzeren of grafietblokken, waarvan de belangrijkste functie is om de stijfheid van de mal te vergroten.
4. Het instellingsprincipe van de stijgbuis bij gebruik van mallen met hoge stijfheid:
Bij het gebruik van verschillende zelfhardende zandvormprocessen, schaalvormprocessen of kernassemblagevormprocessen om nodulair gietijzeren onderdelen te produceren, is de stijfheid van de mal relatief hoog, wat handig is om grafitisatie-expansie te gebruiken om de vloeistofkrimp en stollingskrimp van de gietijzer. Indien goed gecontroleerd, zal er een stijgbuisloos proces zijn om degelijke gietstukken te produceren. Als het proces zonder stijgbuis om verschillende redenen niet geschikt is, kan een stijgbuis met een smalle hals worden gebruikt.
Gietproces zonder stijgbuis
Onder de omstandigheden van hoge vormstijfheid en goede metallurgische kwaliteit van gesmolten ijzer is het laag houden van de afkoelsnelheid van gietstukken, zodat grafiet volledig kan uitkristalliseren, een belangrijke voorwaarde voor het realiseren van stootbordvrij gieten.
Volgens een onderzoeksrapport van Goto et al. is de stollingstijd van nodulair gietijzer meer dan 20 minuten en kan de hoeveelheid grafietprecipitatie de verzadigingswaarde bereiken.
SI Karsay is van mening dat: de gemiddelde modulus van gietstukken van niet minder dan 25 mm één van de voorwaarden is om stijgbuisvrij gieten te realiseren. In het bijzonder mag de gemiddelde wanddikte van plaatgietstukken niet minder zijn dan 50 mm.
De meningen van Goto et al. en Karsay zijn verschillend, en uit de analyse van de afkoelsnelheid blijkt dat ze eigenlijk hetzelfde zijn.
Op voorwaarde dat de metallurgische kwaliteit van het gesmolten ijzer goed is (zoals het gebruik van pre-entingsbehandeling of dynamische entbehandeling en andere maatregelen), kunnen sommige dunwandige gietstukken ook zonder stijgbuizen worden gegoten.
Bij het toepassen van het gietproces zonder stijgbuis, kan het ontwerp van het poortsysteem verwijzen naar de volgende meningen.
(1) Over de hardloper
De loper moet groter en groter zijn. Over het algemeen kan de verhouding van het dwarsdoorsnede-oppervlak van de spruw, het dwarsdoorsnede-oppervlak van de loper en het dwarsdoorsnede-oppervlak van de binnenpoort 4:8:3 zijn. De verhouding van de hoogte van de doorsnede tot de breedte van de loper kan worden genomen als (1.8~2):1.
Op deze manier heeft het poortsysteem een beter effect als aanvulling op de vloeistofkrimp van het gietstuk.
(2) Over de binnenpoort
Om te voorkomen dat de druk die wordt gegenereerd door de volumetrische uitzetting van het gietstuk in de holte, ervoor zorgt dat het gesmolten ijzer vanuit de binnenste poort terugstroomt in het gietsysteem, moet een dun gevormde binnenste poort worden gebruikt en de dikte ervan wordt gekozen om zorg ervoor dat de binnenpoort niet wordt verhinderd tijdens het gietproces. Het principe is om snel te stollen en te stollen nadat de spouw is gevuld. In het algemeen kan de verhouding van de sectiedikte tot de breedte van de binnenpoort 1:4 zijn.
Omdat de binnenste poort dun is en het dwarsdoorsnede-oppervlak klein is, moeten meerdere binnenpoorten worden voorzien voor grotere gietstukken om ervoor te zorgen dat de holte snel wordt gevuld. Op deze manier is er ook het effect van het gelijk maken van de temperatuur van het gieten en het verminderen van hotspots.
2. Gebruik een dunne nekverhoger
Als er zich de volgende situaties voordoen, kan het gebruik van een stootbordloos gietschema de kwaliteit van het gietstuk niet garanderen, dan kunt u overwegen om een smalhals stootbord te gebruiken:
- L De wand van het gietstuk is dun en de grafitisering is onvoldoende tijdens het stollen;
- L Er zijn verspreide hete knooppunten op het gietstuk en er zijn geen krimpdefecten binnen toegestaan;
- L De giettemperatuur is hoger (meer dan 1350 ).
De belangrijkste functie van de smalle halsverhoger is om een gedeeltelijke aanvulling te bieden voor de vloeibare krimp van het gietstuk, om een gietstuk te verkrijgen zonder krimp of porositeit. De smalle hals verbonden met het gietstuk moet worden gestold voordat het gietstuk begint te stollen om te voorkomen dat gesmolten ijzer de stijgbuis binnendringt tijdens grafitisering en expansie. De dikte van de verbinding tussen de hals van de stijgbuis en het gietstuk is het kleinst en de dikte wordt geleidelijk groter bij het overgangsgedeelte dat naar de stijgbuis leidt om het aanvullen van gesmolten ijzer naar het gietstuk te vergemakkelijken.
De dikte van de stijgbuishals kan in het algemeen 0.4 tot 0.6 van de dikte van het voedende deel van het gietstuk zijn.
Indien mogelijk is het het beste om de runner te verbinden met de riser en het gesmolten ijzer wordt gevuld door de hals van de riser zonder een binnenpoort.
5. Het instellingsprincipe van de stijgbuis bij gebruik van het klei-natte zandtype:
De stijfheid van de kleigroene zandvorm is slecht en het is gemakkelijk om het spouwvolume uit te breiden door de beweging van de vormwand. De uitzetting van het holtevolume wordt beïnvloed door vele factoren, zoals de kwaliteit van het vormzand, de compactheid van de vorm, de giettemperatuur en de vorm. De statische drukkop van het gesmolten ijzer in de holte, enz., De werkelijke volume-uitbreiding kan tussen 2-8% zijn.
Omdat de volume-uitbreiding van de spouw sterk varieert, is het principe van het instellen van de stijgbuis natuurlijk afhankelijk van de specifieke situatie.
Dunwandige gietstukken
Gietstukken met een wanddikte van minder dan 8 mm hebben over het algemeen geen duidelijke wandbeweging en de vloeistofkrimp nadat het gesmolten ijzer met de mal is gevuld, is niet te groot en het gietproces zonder stijgbuis kan worden gebruikt. Het ontwerp van het poortsysteem kan verwijzen naar de vorige sectie.
Gietstukken met een wanddikte van 8-12mm
Voor dit type gietstukken, als de wanddikte uniform is en er geen grote hotspots zijn, kan het gietproces zonder stijgbuis ook worden gebruikt, zolang het gieten bij lage temperatuur strikt wordt gecontroleerd.
Als er een hete verbinding is en krimpgaten en krimp binnen niet zijn toegestaan, moet een stijgbuis met een smalle hals worden geplaatst in overeenstemming met de grootte van de hete verbinding.
Gietstukken met een wanddikte van meer dan 12 mm
Bij de productie van dergelijke gietstukken met kleigroene zandvormen, is de wandbeweging vrij groot en is het moeilijker om gietstukken te vervaardigen zonder interne defecten. Overweeg bij het formuleren van het procesplan eerst het gebruik van een stijgbuis met een smalle hals en controleer het gieten bij lage temperatuur strikt. Als deze oplossing het probleem niet kan oplossen, moet een speciale stijgbuis worden ontworpen.
Gebruik klei nat zand om nodulair gietijzeren onderdelen te produceren. Als u een riser wilt installeren, kunt u het beste het volgende doen:
- LA dunne binnenpoort wordt gebruikt om het te laten stollen nadat de mal is gevuld. Nadat de binnenpoort is gestold, vormen het gietstuk en de stijgbuis een geheel, dat niet is verbonden met het poortsysteem;
- L Wanneer het gietstuk vloeibare krimp ondergaat, vult de stijgbuis het gesmolten ijzer aan het gietstuk aan;
- L Wanneer het gietstuk wordt gegrafitiseerd en geëxpandeerd, stroomt het gesmolten ijzer naar de stijgbuis om de druk in de holte af te laten. Verminder het effect op de malwand;
- L Wanneer het gietlichaam secundaire krimp ondergaat na grafitisering en expansie, kan de stijgbuis ijzervloeistof aan het gietstuk leveren.
Het lijkt niet ingewikkeld om het te zeggen, maar in feite moeten veel beïnvloedende factoren worden overwogen bij het ontwerp van de riser, en tot nu toe is er geen effectief specifiek schema gezien en is er geen eenvoudig te gebruiken complete set Van de gegevens. Bij de productie moet rekening worden gehouden met de kwaliteit van de gietstukken en de snelheid van de procesopbrengst, en moet vaak worden onderzocht en geëxperimenteerd.
Bewaar de bron en het adres van dit artikel voor herdruk: Verschillen in de stollingskenmerken van nodulair gietijzer
Minge Spuitgietbedrijf zijn toegewijd aan het vervaardigen en leveren van hoogwaardige en hoogwaardige gietstukken (het assortiment metalen spuitgietonderdelen omvat voornamelijk: Dunwandig spuitgieten,Hot Chamber Spuitgieten,Koude kamer spuitgieten),Ronde Service (Die Casting Service,CNC-bewerking,Matrijzen maken, Oppervlaktebehandeling). Elk aangepast aluminium spuitgieten, magnesium of Zamak / zink spuitgieten en andere gietstukken zijn welkom om contact met ons op te nemen.
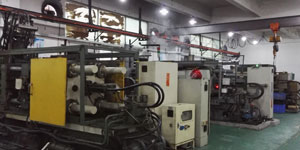
Onder controle van ISO9001 en TS 16949 worden alle processen uitgevoerd door honderden geavanceerde spuitgietmachines, 5-assige machines en andere faciliteiten, variërend van blasters tot Ultra Sonic-wasmachines. Minghe heeft niet alleen geavanceerde apparatuur, maar heeft ook professionele team van ervaren ingenieurs, operators en inspecteurs om het ontwerp van de klant waar te maken.
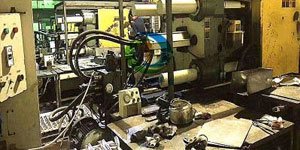
Contractfabrikant van spuitgietwerk. Mogelijkheden zijn onder meer koude kamer aluminium spuitgietonderdelen vanaf 0.15 lbs. tot 6 lbs., snelwissel instellen en machinaal bewerken. Diensten met toegevoegde waarde omvatten polijsten, trillen, ontbramen, stralen, schilderen, plateren, coaten, assembleren en bewerken. Materialen waarmee gewerkt is, zijn legeringen zoals 360, 380, 383 en 413.
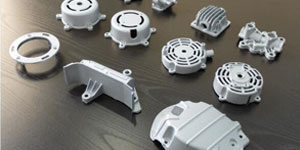
Hulp bij ontwerp van spuitgieten van zink/concurrent engineering. Custom fabrikant van precisie gegoten zink. Miniatuurgietstukken, hogedrukgietstukken, multi-slide gietstukken, conventionele gietstukken, eenheidsmatrijs en onafhankelijke spuitgietstukken en holteverzegelde gietstukken kunnen worden vervaardigd. Gietstukken kunnen worden vervaardigd in lengtes en breedtes tot 24 inch met een tolerantie van +/- 0.0005 inch.
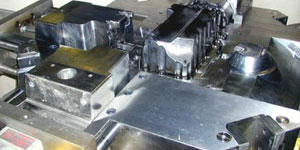
ISO 9001: 2015 gecertificeerde fabrikant van gegoten magnesium. Mogelijkheden zijn onder hoge druk spuitgieten van magnesium tot 200 ton hete kamer en 3000 ton koude kamer, gereedschapsontwerp, polijsten, gieten, machinale bewerking, poeder- en vloeistofverven, volledige QA met CMM-mogelijkheden , montage, verpakking & levering.
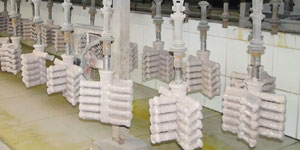
ITAF16949 gecertificeerd. Extra castingservice omvat: investering gieten,zandgieten,Zwaartekracht gieten, Verloren schuimafgietsel,Centrifugaal gieten,Vacuümgieten,Permanent vormgieten,. Mogelijkheden zijn onder meer EDI, technische assistentie, solide modellering en secundaire verwerking.
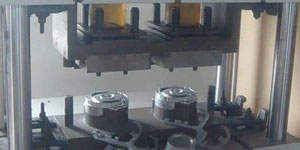
Gietindustrieën Casestudy's over onderdelen voor: auto's, fietsen, vliegtuigen, muziekinstrumenten, waterscooters, optische apparaten, sensoren, modellen, elektronische apparaten, behuizingen, klokken, machines, motoren, meubels, sieraden, mallen, telecom, verlichting, medische apparaten, fotografische apparaten, Robots, sculpturen, geluidsapparatuur, sportuitrusting, gereedschap, speelgoed en meer.
Wat kunnen we u hierna helpen doen?
∇ Ga naar de startpagina voor Spuitgieten China
→Gietonderdelen- Zoek uit wat we hebben gedaan.
→Gerangschikte tips over Spuitgietdiensten
By Minghe Die Casting Fabrikant: |Categorieën: Handige artikelen |Materiaal Tags: Aluminium gieten, Zink gieten, Magnesium gieten, Titanium gieten, Gieten van roestvrij staal, Messing gieten,Brons gieten,Video casten,Geschiedenis van ons bedrijf,Aluminium spuitgieten |Reacties uitgeschakeld