Het afbraakmechanisme van het smeden van schimmel
Matrijzensmeden is momenteel de meest geavanceerde smeedtechnologie, voornamelijk gebruikt voor massaproductie van belangrijke componenten van matrijzen. Het grootste nadeel is de slechte duurzaamheid van de vormgereedschappen. Volgens de redacteur van diecastingcompany.com bedragen de kosten van gereedschap 8-15% van de totale kosten van producten. Als u kijkt naar de tijd die nodig is om versleten gereedschap te vervangen en het verlies dat wordt veroorzaakt door onopzettelijk falen, kunnen de kosten zelfs oplopen tot 30% tot 50%. Bovendien zal de slijtage van het gereedschap een aanzienlijke verslechtering van de kwaliteit van het smeden veroorzaken. De meest voorkomende defecten die worden veroorzaakt door gereedschapsslijtage zijn holtevulfouten, dat wil zeggen vouwen, bramen, vervorming, krassen, delaminatie en micro- en macroscheuren.
Deze defecten zullen uiteindelijk de prestaties van vervalste producten beïnvloeden. Door de sterke concurrentie op de markt blijven fabrikanten van matrijzensmeedproducten hun kosten verlagen terwijl ze de kwaliteit van smeedstukken verbeteren. Toch zijn ze nog steeds erg geïnteresseerd in het probleem van de slechte duurzaamheid van het gereedschap.
De duurzaamheid van een gereedschap wordt meestal op verschillende manieren gedefinieerd. In termen van productie wordt de duurzaamheid van een gereedschap uitgedrukt door het aantal smeedstukken, dat wil zeggen het aantal producten van de verwachte kwaliteit dat met dit gereedschap kan worden verkregen. Volgens deze definitie kan de gemiddelde levensduur van gereedschappen variëren tussen 2,000 en 20,000 stuks. In termen van gereedschappen is duurzaamheid gerelateerd aan degradatie, dus wordt het gedefinieerd als het vermogen om degradatieverschijnselen te weerstaan. Dit artikel gebruikt voornamelijk de tweede definitie. Het moet gezegd worden dat smeedgereedschappen tijdens het gebruik worden beïnvloed door een verscheidenheid aan degraderende factoren, en de interactie van deze factoren maakt de analyse van het probleem moeilijker. In de literatuur over dit onderwerp zijn verschillende verklaringen te vinden voor degradatieverschijnselen.
Volgens de statistieken van veel geleerden is de belangrijkste reden voor het buiten gebruik stellen van smeedmatrijzen het gevolg van veranderingen in slijtageafmetingen. Schimmelafval als gevolg van slijtage is goed voor ongeveer 70%, plastische vervorming is goed voor ongeveer 25% en vermoeiingsscheuren en andere redenen vertegenwoordigen slechts ongeveer 5%. Veel verschijnselen treden vaak tegelijkertijd op en hun interactie hangt af van het ontwerp van de matrijs, de omstandigheden van het smeden en vervaardigen, de warmtebehandeling van het matrijsmateriaal en de vorm van de voorvorm en het inzetstuk.
Arbeidsomstandigheden van het smeden van matrijzen: Tijdens het heet smeden van matrijzen worden gereedschappen hoofdzakelijk onderworpen aan degradatie van drie aspecten: intensieve thermische schokken, periodieke veranderingen van mechanische belasting en hoge temperatuur en hoge druk. Om de vloeispanning van staalproducten tijdens heet smeden te verminderen, wordt het vervormde metaal verwarmd tot 10,000-2,000 graden Celsius. Op het moment van materiaalvervorming kan de temperatuur van het gereedschapsoppervlak 800 graden Celsius bereiken, gevolgd door intensieve koeling, en daarom zal het gereedschap worden blootgesteld aan een grote temperatuurgradiënt. Op de dwarsdoorsnede van de matrijs kunnen de matrijsoppervlaktetemperatuur en nabij-oppervlaktetemperatuur enkele honderden graden Celsius verschillen. De temperatuur van heet smeden is lager dan die van heet smeden, dat wil zeggen, de temperatuur van staalvervorming bereikt ongeveer 900 graden Celsius. Dit betekent dat de belasting die wordt gegenereerd door de cyclische verwarming en koeling van het gereedschapsoppervlak niet zo groot is als die van warmsmeedwerk. Niettemin is de levensduur van de gereedschappen die worden gebruikt in het halfwarme smeedproces nog vrij kort. Dit komt voornamelijk door het gecombineerde effect van de cyclische temperatuur en de grotere mechanische belasting. De mechanische belasting komt voornamelijk van koeling en hardere materialen.
Degeneratiemechanisme van smeedgereedschappen
De levensduur van smeedgereedschappen hangt voornamelijk af van hun ontwerp, voorbereiding, warmtebehandeling van gereedschapsmaterialen, hun smeedcondities, de vorm van preforms en kernblokken, enz. We kunnen veel informatie over degradatie vinden in de literatuur over dit onderwerp. Deze mechanismen zijn onderverdeeld in verschillende categorieën. Onderzoeksresultaten tonen aan dat de volgende slijtagemechanismen voornamelijk voorkomen op het oppervlak van smeedgereedschappen: abrasieve slijtage, thermomechanische vermoeidheid, plastische vervorming, vermoeiingsscheuren, adhesieve slijtage en oxidatie. De vorm van de werkende inkeping van het gereedschap bepaalt de contacttijd, druk, wrijvingspad en temperatuurveranderingen, die de snelheid van optreden van het speciale degradatiemechanisme bepalen.
In het vlakke gebied is de contacttijd tussen het gereedschap en het thermische materiaal het langst, en het is ook de plaats waar de maximale druk optreedt. Thermomechanische vermoeidheid is het belangrijkste degradatiemechanisme.
De binnenradius van de afronding wordt beïnvloed door de cyclische trekbelasting, die wordt veroorzaakt door de toename van de externe belasting, die voornamelijk optreedt wanneer de vervorming de neiging heeft zich tijdens het smeedproces te concentreren. Als gevolg hiervan ontwikkelen vermoeiingsmicroscheuren zich tijdens het gebruik van het gereedschap tot grote scheuren en verschijnen op deze plaatsen. De buitenste straal van de maldeuk en de plaats waar de malafdruk de flitsbrug binnenkomt als gevolg van de verzwakking van het materiaal onder hoge temperatuuromstandigheden, hoe lager de vloeigrens van het materiaal, wat leidt tot plastische vervorming. De dichte stroom van vervormde materialen veroorzaakt schurende slijtage in deze gebieden, die verder wordt verergerd door de harde oxiden, die worden gevormd op het oppervlak van het smeedmateriaal van het gereedschap tijdens het oxidatieproces bij hoge temperatuur.
Kleefslijtage van het degradatiemechanisme van smeedmatrijzen
Lijmslijtage treedt op in het plastische vervormingsgebied van de oppervlaktelaag, vooral waar het oppervlak onregelmatig is. Het treedt meestal op onder hoge druk en relatief lage snelheidsomstandigheden, voornamelijk als gevolg van vergelijkbare materiaalinteracties of materialen die chemische affiniteit vertonen (typische smeedverwerkingsomstandigheden). Onder hogere drukomstandigheden glijdt het materiaalvormstuk langs het oppervlak van het gereedschap, waardoor de oxidecoating wordt verwijderd, waardoor het verse oppervlak van het gereedschap zichtbaar blijft. Dit komt voornamelijk voor in het onregelmatige gebied van de oppervlakteprojectie (het piekgedeelte van het ruwe oppervlak).
Wanneer de materialen op deze plaatsen dicht bij elkaar worden geplaatst, zodat de interatomaire krachten beginnen te werken, worden lokale metaalbindingen gevormd. Toen de oppervlakken verder naar elkaar verschoven, werd de metaalbinding vernietigd. Bij dit proces wordt plastische vervorming van de oppervlaktelaag gevormd. Het verbreken van de metaalbinding leidt tot het afpellen van de metaaldeeltjes, die de neiging hebben om aan het oppervlak te kleven.
Schurende slijtage van het degradatiemechanisme van smeedmatrijzen
Materiaalverlies wordt meestal toegeschreven aan abrasieve slijtage. De grootte van de gepelde deeltjes hangt voornamelijk af van de smeedcoëfficiënt en de eigenschappen van de oppervlaktelaag van het gereedschap. Een voorbeeld van lijmslijtage is de tweede fase van het smeden van de homokineetbehuizing, zoals weergegeven in de afbeelding. De temperatuur waarbij het materiaal in dit proces vervormt, is ongeveer 900°C, dat wil zeggen, het is meestal veel lager dan het traditionele warmsmeedproces, dat dit soort slijtage neigt. Lijmslijtage hecht zich aan het materiaal zelf of aan het gereedschap, waar de dwarsdoorsnede wordt verkleind.
Schuurslijtage is het gevolg van materiaalverlies en wordt voornamelijk bereikt door het scheiden van materiaal van het oppervlak. Schurende slijtage zal optreden wanneer er losse of vaste schurende deeltjes zijn, of wanneer er onregelmatige delen van uitsteeksels op het interactie-oppervlak zijn. Voor het smeedgereedschap is de hardheid veel hoger dan die van het vervormde materiaal. In dit geval, als schurende deeltjes verschijnen in het contactgedeelte tussen het smeedgereedschap en het vervormde materiaal, zal schurende slijtage optreden. Schuurslijtage zal worden verergerd door het verschijnen van harde oxidedeeltjes, die worden gevormd op het oppervlak van kleine deeltjes die zijn gescheiden van het smeedgedeelte en de vorm en het vormoppervlak onder hoge temperatuuromstandigheden. Door dit mechanisme worden groeven gecreëerd langs de richting waarin de vervorming van het materiaal verandert.
Hun vorm en diepte zijn voornamelijk afhankelijk van de smeedomstandigheden. Het uitstekende deel is bijzonder gevoelig voor slijtage en zal tijdens de verdere service snel van het oppervlak van het gereedschap worden verwijderd, wat leidt tot materiaalverlies en veranderingen in de materiaalgeometrie. Bijzonder gemakkelijk te vormen abrasieve slijtage, en ook bijzonder gevoelig voor abrasieve slijtage is de plaats waar de langste slip optreedt tijdens de vervorming van het materiaal. De meest voorkomende is de buitenste straal van de matrijsholte, waar de matrijs de flitsbrug binnengaat.
Bewaar de bron en het adres van dit artikel voor herdruk: Het afbraakmechanisme van het smeden van schimmel
Minge Spuitgietbedrijf zijn toegewijd aan het vervaardigen en leveren van hoogwaardige en hoogwaardige gietstukken (het assortiment metalen spuitgietonderdelen omvat voornamelijk: Dunwandig spuitgieten,Hot Chamber Spuitgieten,Koude kamer spuitgieten),Ronde Service (Die Casting Service,CNC-bewerking,Matrijzen maken, Oppervlaktebehandeling). Elk aangepast aluminium spuitgieten, magnesium of Zamak / zink spuitgieten en andere gietstukken zijn welkom om contact met ons op te nemen.
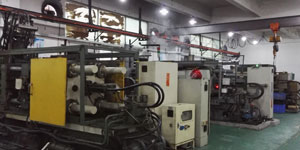
Onder controle van ISO9001 en TS 16949 worden alle processen uitgevoerd door honderden geavanceerde spuitgietmachines, 5-assige machines en andere faciliteiten, variërend van blasters tot Ultra Sonic-wasmachines. Minghe heeft niet alleen geavanceerde apparatuur, maar heeft ook professionele team van ervaren ingenieurs, operators en inspecteurs om het ontwerp van de klant waar te maken.
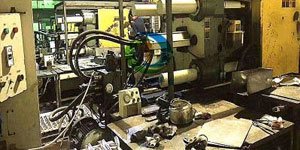
Contractfabrikant van spuitgietwerk. Mogelijkheden zijn onder meer koude kamer aluminium spuitgietonderdelen vanaf 0.15 lbs. tot 6 lbs., snelwissel instellen en machinaal bewerken. Diensten met toegevoegde waarde omvatten polijsten, trillen, ontbramen, stralen, schilderen, plateren, coaten, assembleren en bewerken. Materialen waarmee gewerkt is, zijn legeringen zoals 360, 380, 383 en 413.
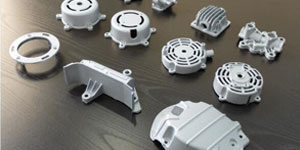
Hulp bij ontwerp van spuitgieten van zink/concurrent engineering. Custom fabrikant van precisie gegoten zink. Miniatuurgietstukken, hogedrukgietstukken, multi-slide gietstukken, conventionele gietstukken, eenheidsmatrijs en onafhankelijke spuitgietstukken en holteverzegelde gietstukken kunnen worden vervaardigd. Gietstukken kunnen worden vervaardigd in lengtes en breedtes tot 24 inch met een tolerantie van +/- 0.0005 inch.
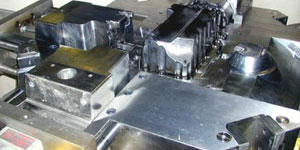
ISO 9001: 2015 gecertificeerde fabrikant van gegoten magnesium. Mogelijkheden zijn onder hoge druk spuitgieten van magnesium tot 200 ton hete kamer en 3000 ton koude kamer, gereedschapsontwerp, polijsten, gieten, machinale bewerking, poeder- en vloeistofverven, volledige QA met CMM-mogelijkheden , montage, verpakking & levering.
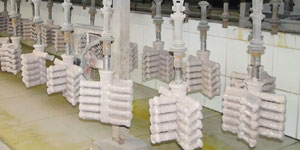
ITAF16949 gecertificeerd. Extra castingservice omvat: investering gieten,zandgieten,Zwaartekracht gieten, Verloren schuimafgietsel,Centrifugaal gieten,Vacuümgieten,Permanent vormgieten,. Mogelijkheden zijn onder meer EDI, technische assistentie, solide modellering en secundaire verwerking.
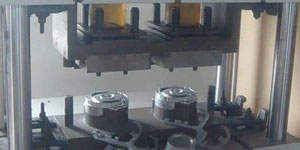
Gietindustrieën Casestudy's over onderdelen voor: auto's, fietsen, vliegtuigen, muziekinstrumenten, waterscooters, optische apparaten, sensoren, modellen, elektronische apparaten, behuizingen, klokken, machines, motoren, meubels, sieraden, mallen, telecom, verlichting, medische apparaten, fotografische apparaten, Robots, sculpturen, geluidsapparatuur, sportuitrusting, gereedschap, speelgoed en meer.
Wat kunnen we u hierna helpen doen?
∇ Ga naar de startpagina voor Spuitgieten China
→Gietonderdelen- Zoek uit wat we hebben gedaan.
→Gerangschikte tips over Spuitgietdiensten
By Minghe Die Casting Fabrikant: |Categorieën: Handige artikelen |Materiaal Tags: Aluminium gieten, Zink gieten, Magnesium gieten, Titanium gieten, Gieten van roestvrij staal, Messing gieten,Brons gieten,Video casten,Geschiedenis van ons bedrijf,Aluminium spuitgieten |Reacties uitgeschakeld