Het ontwerpdetail van het spuitgieten van aluminiumlegeringen:
Dit artikel analyseert eerst de structuur en het spuitgietproces van de schaal van aluminiumlegering en gebruikt UG-software om het ontwerp van de spuitgietmatrijs van aluminiumlegering te voltooien. Door de praktijk bewezen, is het ontworpen spuitgieten redelijk, het oppervlak van het verkregen gietstuk is glad en schoon en de productkwaliteit voldoet aan de eisen.
Analyse van de structuur en het proces van het spuitgieten van delen van de achterschaal van aluminiumlegering
- 1.1 Spuitgietconstructie Uit figuur 1 blijkt dat de gietconstructie van de achterschaalvulling relatief eenvoudig is, de wanddikte van het gietstuk is in wezen uniform, er zijn twee gietgaten, maar omdat de wand van het gietgat iets dikker is, heet vlekken zijn gemakkelijk te verschijnen, de totale wanddikte van de spuitgietonderdelen is relatief uniform. Bij het kiezen van de wanddikte moet met verschillende factoren rekening worden gehouden: spuitgietstructuur, materiaaleigenschappen en het ontworpen spuitgietproces. Alleen dunwandige of uniforme wanddiktes kunnen aan alle aspecten voldoen. vraag.
- 1.2 De minimale wanddikte van de buitenrand van het gietstuk. Goede gietvormomstandigheden vereisen een bepaalde wanddikte van de buitenrand. De relatie tussen de randwanddikte s en de diepte h is s≥(1/4~1/3)hmm. Wanneer h<4.5 mm, dan s≥1.5 mm.
- 1.3 Spuitgietmateriaal Het materiaal van het spuitgieten is een spuitgietaluminiumlegering, de kwaliteit is YZAlSi9Cu4, de treksterkte is 240MPa, de Brinell-hardheid is 85HBS en de gemiddelde krimpsnelheid is 0.6%. De geselecteerde legering resulteert in goede gieteigenschappen en is bijzonder geschikt voor spuitgieten.
- 1.4 Gietstraal Om het gesmolten metaal soepeler te laten stromen en het gas gemakkelijker af te voeren, is de structuur ontworpen om gegoten filets te gebruiken, en het gebruik van filets om de scherpe hoeken van de constructie te vervangen kan ook scheuren voorkomen. De straal van de afgeronde hoeken van de ontworpen structuur is afhankelijk van de wanddikte van de structuur en het bereik is over het algemeen 0.5 tot 1 mm.
- 1.5 De ontwerphoek moet worden gekozen door een uitgebreide overweging van vele factoren: gietgeometrie (diepte, wanddikte, holte of kernoppervlak), ruwheid, verwerkingskorrelrichting, enz. Rekening houdend met de bovenstaande factoren, het ontwerp van de helling voor het ontvormen van de schaal van het gietstuk: α=30' aan de buitenzijde en β=1° aan de binnenzijde.
Ontwerp van parameters voor spuitgieten
2.1 Selectie spuitgietmachine Bij de keuze voor een spuitgietmachine moet eerst de klemkracht worden bepaald. De klemkracht heeft twee functies: de ene wordt gebruikt om de tegendruk in evenwicht te brengen om het doel van het vergrendelen van het scheidingsoppervlak te bereiken; de andere is om spatten van gesmolten metaal te voorkomen om het doel van het bereiken van de beoogde maatnauwkeurigheid te bereiken. Er is geen gedeeltelijke uitzettingskracht in het ontworpen gietstuk, omdat deze mal geen zijkerntrekkracht heeft (het spuitgietstuk heeft geen zijgaten en ondersnijdingen). Daarom is F lock ≥ KF main=1.25×1288.352=1610.44kN. Volgens de bovenstaande berekening worden de waarde van de klemkracht en het gewicht van het gietstuk verkregen. Volgens deze twee hoofdfactoren wordt de spuitgietmachine geselecteerd en het uiteindelijk geselecteerde model is: horizontale spuitgietmachine met koude kamer (2500 kN) ——— J1125 type, belangrijkste parameters:
- ①Maximum metalen gietvolume ——— 3.2 kg,
- ②Mold dikte————250~650mm,
- ③Moulding seat plate stroke————400mm,
- ④Injectiekracht—— —143~280kN.
2.2 Spuitgietdruk Spuitgietdruk is een van de belangrijkste parameters in het spuitgietproces. Daarom is het van groot belang om de drukverandering van vloeibaar metaal tijdens de druk te begrijpen spuitgieten proces en om de druk in elke fase van het spuitgietproces redelijk te beheersen:
- ① Zorg voor gekwalificeerde gietstukken —— — Dichte organisatie, duidelijk overzicht;
- ②Initiële berekening van specifieke injectiedruk — Bereken volgens de geselecteerde injectiekracht. De specifieke injectiedruk is ook gerelateerd aan de vormholte, de wanddikte van het gietstuk, het gesmolten metaalproces en andere factoren. Door de specifieke parameters van de ontworpen mal en de beginwaarde te combineren, wordt de injectiespecifieke druk van deze spuitgietmatrijs uiteindelijk ingesteld op 90 MPa.
2.3 Spuitgietsnelheid De keuze van de spuitgietsnelheid heeft de volgende twee aspecten: selectie van injectiesnelheid en selectie van vulsnelheid. De keuze van de twee snelheden is erg belangrijk, wat direct de interne en externe kwaliteit en contourdefinitie van het gietstuk bepaalt. Factoren waarmee rekening moet worden gehouden bij het selecteren van de vulsnelheid:
- ①De grootte van het gietstuk,
- ②De complexiteit van de structuur van het gietstuk,
- ③Het type legering dat is geselecteerd voor het gieten,
- ④Het injectiedrukniveau.
Specifieke keuzes:
- ① De gietstukken die gemakkelijker te vullen zijn --- gietstukken met een eenvoudige wanddikte of hogere interne kwaliteitseisen, kies: lage snelheid, hoge specifieke druk, grote poort;
- ②Snel vullen is vereist ---complex dunwandig of Kies voor gietstukken met hogere eisen aan de oppervlaktekwaliteit: hoge snelheid, hoge specifieke druk. Alomvattende overweging, volgens de specifieke kenmerken van dit spuitgietonderdeel - de structuur is relatief eenvoudig, selecteer de gemiddelde snelheid, het bereik is 20 ~ 90 m / s.
2.4 De spuitgiettijd bepaalt de spuitgiettijd, die bestaat uit drie delen van de benodigde tijd: vultijd, houdtijd en de tijd dat het spuitgietdeel in de spuitgietmatrijs blijft. Verschillende factoren gecombineerd om dit resultaat te produceren: druk, snelheid, temperatuur, eigenschappen van gesmolten metaal, evenals gietstructuur (voornamelijk wanddikte en volume) en vormstructuur (vooral het poortsysteem en afvoersysteem) en andere factoren. De vultijd ligt meestal tussen 0.01 en 0.2s. De lengte wordt bepaald door de grootte van het gietstuk en de complexiteit van de constructie: een gietstuk met een eenvoudige structuur en een groot volume vereist een relatief lange vultijd; een gietstuk met een complexere structuur en een kleinere wanddikte vergt een korte tijd. Na praktische tests is de vultijd vastgesteld op ongeveer 0.2 s, wat redelijk is voor de middelgrote en kleine gietstukken van aluminiumlegeringen die in dit document zijn ontworpen. De functie van het vasthouden van de druktijd is: de injectiestempel heeft voldoende tijd om druk uit te oefenen op het niet-gestolde metaal, zodat het kristallisatieproces onder druk kan worden uitgevoerd, wat de toevoer verbetert en met succes een dichte structuur verkrijgt. Factoren die van invloed zijn op de tijdsduur: het smeltpunt van de geselecteerde legering, het kristallisatietemperatuurbereik en de wanddikte van het gietstuk. Gietstukken met een hoog smeltpunt, een groot bereik en een grote wanddikte hebben een lange tijd nodig, 2~3s; wanneer de bepaalde tijd te kort is, zal krimp optreden, maar het heeft geen significant effect als de houdtijd wordt verlengd. 1~2s is het algemene houdtijdbereik. De gemiddelde wanddikte van het gietstuk in dit ontwerp is 3 mm. Gezien de structuur en legeringseigenschappen wordt 3s gekozen als houdtijd. 2.5 Giettemperatuur De belangrijkste procesparameters om gekwalificeerde gietstukken te garanderen: de giettemperatuur van gesmolten metaal en de werktemperatuur van de mal. Er zijn veel factoren die het beïnvloeden: de structuur van het gietstuk, wanddikte, vuldruk, snelheid en legeringstypes. Het is noodzakelijk om de bovenstaande parameters uitgebreid in overweging te nemen om ervoor te zorgen dat de spuitgiettemperatuur binnen een redelijk bereik stabiel is en goede vulcondities biedt. Als de giettemperatuur niet binnen een redelijk bereik ligt, zal de kwaliteit van het product verslechteren of zelfs ongeschikt zijn:
① Overmatige giettemperatuur - veroorzaakt overmatige krimp tijdens het koelen, het product is vatbaar voor scheuren, grotere korrels en slechte mechanische prestaties, en veroorzaakt zelfs schimmelvorming, verkort de levensduur van de mal;
② Een te lage giettemperatuur veroorzaakt defecten, waaronder koude barrière, oppervlaktepatroon en onvoldoende gieten. Om gekwalificeerde gietstukken te verkrijgen, moeten naast de giettemperatuur ook rekening worden gehouden met de druk, de temperatuur van de spuitgietmatrijs, de vulsnelheid en de legering die voor gietstukken is geselecteerd. De spuitgietonderdelen zijn gemaakt van een aluminium-siliciumlegering. Volgens zijn vloeibaarheid en vormkenmerken wordt 620 ℃ geselecteerd als spuitgiettemperatuur.
Structuurontwerp van spuitgieten spuitgieten van rugschaal
3.1 Bepaling van het scheidingsoppervlak Het onderdeel heeft een eenvoudige structuur. Volgens het principe van selectie van scheidingsoppervlakken, moet het grootste projectiegedeelte worden geselecteerd, zoals weergegeven in figuur 2.
3.2 Ontwerp van het poortsysteem Het poortsysteem bestaat uit vier delen:
- ① rechte loper
- ② horizontale loper
- ③ interne poort,
- ④ koud slakkengat.
Specifiek ontwerp:
- ①Integrale drukkamer——de verbindingsmethode van drukkamer en aanspuitbus;
- ②De vorm van de dwarsdoorsnede van de hardloper - platte trapezium;
- ③ Binnenpoort—— ringvormige zijpoort;
- ④Side gieten Mond-gerangschikt op het scheidingsoppervlak van het gietstuk;
- ⑤ Eén mal met vier holtes, figuur 3 toont de specifieke structuur.
3.3 Ontwerp van de overlooptank en het uitlaatsysteem Het constructieve ontwerp van de overlooptank wordt uitgevoerd en de vorm van de dwarsdoorsnede die wordt gekozen na uitgebreide overweging van verschillende factoren is trapeziumvormig (figuur 4). Een redelijke structuur heeft de volgende functies:
- ① Verbeter de thermische balans van de mal - pas de temperatuur overal in de mal aan, verminder de stroommarkeringen, koude barrières en onvoldoende gieten van de gietstukken, breng krimpholtes, krimpporositeit en beknelling van wervelingen over;
- ② ontlading Het gas in de holte wordt snel afgevoerd met de uitlaatgroef;
- ③ opslag van koude, vuile metaalvloeistof - een mengsel van verfresten en gas.
3.4 Ontwerp van het uitwerpsysteem In het spuitgietproces, nadat een volledige vormingscyclus is voltooid, moet de matrijs worden geopend om het gegoten onderdeel te nemen, en het verpakte gegoten onderdeel bevindt zich aan de zijkant van de punch, die moet worden verwijderd. Deze taak vereist een extra soort topstukmechanisme om uit te voeren. Het uitwerpsysteem neemt een belangrijke plaats in bij het ontwerp van de vormstructuur. Er zijn drie hoofdonderdelen van het uitwerpsysteem:
- ① uitwerpen,
- ② opnieuw instellen
- ③ gids. Deze set mallen maakt gebruik van twee uitwerpmechanismen voor uitwerpen, die worden gebruikt voor gieten en uitwerpen van spruw. De diameters van de uitwerppennen zijn respectievelijk 6 mm en 8 mm.
Ontwerp begrenzingsinrichtingen in het systeem:
- ① limietblok,
- ② resethendel om de resetnauwkeurigheid van het mechanisme te verbeteren en te voorkomen dat de slag de limiet overschrijdt tijdens de beweging van de mechanismecomponenten.
3.5 Berekening van de grootte van het gevormde onderdeel
3.5.1 Caviteit en kernmaat:
3.5.2 Bereken de hartafstand en positiegrootte: waarbij: L-de hartafstand van het vormdeel en de gemiddelde grootte van de positie (mm); L-de gemiddelde grootte van de middenafstand van het spuitgieten en de positie (mm).
3.6 Het ontwerp van het koelsysteem kiest voor een efficiënte en eenvoudig te bedienen vormkoelmethode: waterkoeling om gietstukken van hoge kwaliteit en een lange levensduur van de vorm te verkrijgen. Het koeleffect van waterkoeling hangt af van de lay-out van het koelkanaal, dat in de spouw is aangebracht:
- ①De hoogste temperatuur,
- ②De warmte is meer geconcentreerd,
- ③Onder de vorm,
- ④De kant tegenover de operator. Om het installatiegemak van de watertoevoerslang te verbeteren, is het vereist om de geometrische afmetingen van de buitendiameter van het waterkanaal te verenigen. De structurele opstelling wordt getoond in figuur 5.
3.7 Algemene montagetekening van spuitgietmatrijs Maak de algemene montagetekening van de spuitgietmal van de achterschaalafdekking (afbeelding 6). De spuitgietmal bestaat uit twee delen: een vaste mal en een beweegbare mal. De vaste matrijs staat stil en bevindt zich op de vaste matrijsplaat. De beweegbare vorm beweegt mee met de volgplaat en bevindt zich op de vaste plaat van de volgvorm. De mal wordt gesloten en geopend door de beweging van de beweegbare mal ten opzichte van de beweegbare mal.
① Vormklemming: de twee worden gesloten om een holte te vormen en de holte wordt onder hoge druk gevuld met gesmolten metaal met behulp van een poortsysteem; ② vormopening: de twee worden gescheiden nadat de druk is gehandhaafd en het uitwerpmechanisme voltooit de taak om producten uit de holte te werpen.
Dit artikel maakt gebruik van UG-software om de onderdelen van de achterkant te modelleren en voltooit de procesanalyse, spuitgietprocesparameters en het ontwerp van de matrijsstructuur van de onderdelen van de achterkant. De holte wordt beperkt door de volgende factoren: productie-, proces- en productie-efficiëntie, enz., rekening houdend met de bovengenoemde factoren, wordt het bepaald als een redelijkere lay-out met vier holtes in één vorm. Praktische productie laat zien dat de spuitgiet-specifieke druk van 90 MPa is geselecteerd, de spuitgietsnelheid is geselecteerd in het bereik van 20-90 m / s, de giettijd van 0.2 s, de houdtijd van 3 s en het spuitgieten temperatuur van 620 ℃, de resulterende benauwde hoes aan de achterkant. Het heeft een glad oppervlak en voldoet aan de kwaliteitseisen van het product.
Bewaar de bron en het adres van dit artikel voor herdruk: Het ontwerpdetail van het spuitgieten van aluminiumlegeringen:
Minge Spuitgietbedrijf zijn toegewijd aan het vervaardigen en leveren van hoogwaardige en hoogwaardige gietstukken (het assortiment metalen spuitgietonderdelen omvat voornamelijk: Dunwandig spuitgieten,Hot Chamber Spuitgieten,Koude kamer spuitgieten),Ronde Service (Die Casting Service,CNC-bewerking,Matrijzen maken, Oppervlaktebehandeling). Elk aangepast aluminium spuitgieten, magnesium of Zamak / zink spuitgieten en andere gietstukken zijn welkom om contact met ons op te nemen.
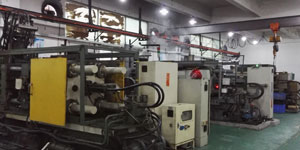
Onder controle van ISO9001 en TS 16949 worden alle processen uitgevoerd door honderden geavanceerde spuitgietmachines, 5-assige machines en andere faciliteiten, variërend van blasters tot Ultra Sonic-wasmachines. Minghe heeft niet alleen geavanceerde apparatuur, maar heeft ook professionele team van ervaren ingenieurs, operators en inspecteurs om het ontwerp van de klant waar te maken.
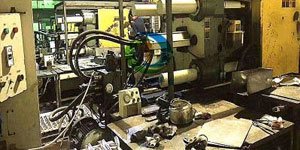
Contractfabrikant van spuitgietwerk. Mogelijkheden zijn onder meer koude kamer aluminium spuitgietonderdelen vanaf 0.15 lbs. tot 6 lbs., snelwissel instellen en machinaal bewerken. Diensten met toegevoegde waarde omvatten polijsten, trillen, ontbramen, stralen, schilderen, plateren, coaten, assembleren en bewerken. Materialen waarmee gewerkt is, zijn legeringen zoals 360, 380, 383 en 413.
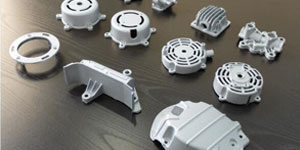
Hulp bij ontwerp van spuitgieten van zink/concurrent engineering. Custom fabrikant van precisie gegoten zink. Miniatuurgietstukken, hogedrukgietstukken, multi-slide gietstukken, conventionele gietstukken, eenheidsmatrijs en onafhankelijke spuitgietstukken en holteverzegelde gietstukken kunnen worden vervaardigd. Gietstukken kunnen worden vervaardigd in lengtes en breedtes tot 24 inch met een tolerantie van +/- 0.0005 inch.
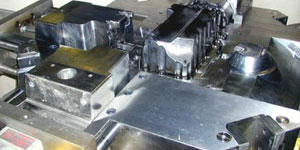
ISO 9001: 2015 gecertificeerde fabrikant van gegoten magnesium. Mogelijkheden zijn onder hoge druk spuitgieten van magnesium tot 200 ton hete kamer en 3000 ton koude kamer, gereedschapsontwerp, polijsten, gieten, machinale bewerking, poeder- en vloeistofverven, volledige QA met CMM-mogelijkheden , montage, verpakking & levering.
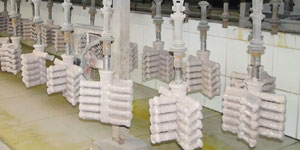
ITAF16949 gecertificeerd. Extra castingservice omvat: investering gieten,zandgieten,Zwaartekracht gieten, Verloren schuimafgietsel,Centrifugaal gieten,Vacuümgieten,Permanent vormgieten,. Mogelijkheden zijn onder meer EDI, technische assistentie, solide modellering en secundaire verwerking.
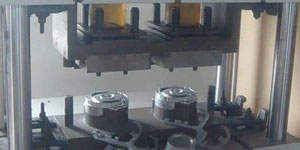
Gietindustrieën Casestudy's over onderdelen voor: auto's, fietsen, vliegtuigen, muziekinstrumenten, waterscooters, optische apparaten, sensoren, modellen, elektronische apparaten, behuizingen, klokken, machines, motoren, meubels, sieraden, mallen, telecom, verlichting, medische apparaten, fotografische apparaten, Robots, sculpturen, geluidsapparatuur, sportuitrusting, gereedschap, speelgoed en meer.
Wat kunnen we u hierna helpen doen?
∇ Ga naar de startpagina voor Spuitgieten China
→Gietonderdelen- Zoek uit wat we hebben gedaan.
→Gerangschikte tips over Spuitgietdiensten
By Minghe Die Casting Fabrikant: |Categorieën: Handige artikelen |Materiaal Tags: Aluminium gieten, Zink gieten, Magnesium gieten, Titanium gieten, Gieten van roestvrij staal, Messing gieten,Brons gieten,Video casten,Geschiedenis van ons bedrijf,Aluminium spuitgieten |Reacties uitgeschakeld