Basiskennis van spuitgieten van aluminiumlegeringen
1. De basisdefinitie van spuitgieten van aluminiumlegeringen:
Matrijzenbouw verwijst naar de verwerking van gereedschappen voor het maken van vormen en blanco's. Daarnaast omvat het ook snijmatrijs en stansgereedschap. In het algemeen bestaat tooling uit een bovenste module en een onderste module. De stalen plaat wordt tussen de bovenste en onderste matrijzen geplaatst en het materiaal wordt gevormd onder invloed van de pers. Wanneer de pers wordt geopend, wordt het door de vorm van het gereedschap bepaalde werkstuk verkregen of wordt het bijbehorende afval verwijderd. Onderdelen zo klein als elektronische connectoren en zo groot als het dashboard van een auto kunnen worden gegoten met gereedschap.
Progressieve matrijs is een set gereedschappen die het werkstuk automatisch van het ene station naar het andere kan verplaatsen en het vormdeel in het laatste station kan krijgen.
Het gereedschapsproces omvat: snijmatrijs, stansmatrijs, samengestelde matrijs, extrusiematrijs, vierschuifmatrijs, progressieve matrijs, stempelmatrijs, stansgereedschap, enz.
2. Type gereedschap
- (1) Metalen stempelgereedschap: continue matrijs, enkele matrijs, samengestelde matrijs, tekenmatrijs;
- (2) Kunststof vormvorm: spuitgietvorm, extrusievorm, zuigvorm;
- (3) spuitgieten tooling: zinklegering spuitgieten tooling, aluminium spuitgieten tooling;
- (4) Smeden gereedschap tool
- (5) Poedermetallurgie gereedschap
- (6) Rubberen gereedschap
3. Bewerkingsproces
- Snijden: voorste matrijsmateriaal, achterste matrijsmateriaal, inzetmateriaal, rijpositiemateriaal en hellend vijzelmateriaal;
- Open frame: frame aan de voorkant en frame aan de achterkant;
- Opening: opening aan de voorkant van de vormholte, opening aan de achterkant van de vormholte, opening van de scheidingslijn;
- Koperen mannetje: voorste sterven koperen mannetje, achterste mal koperen mannetje, scheidingslijn hoekspeling koperen mannetje;
- Draadknippen: scheidingslijn invoegen, koperen mannelijke, schuine positie van het bovenste kussen;
- Computergongs: fijne gongs scheidingslijn, fijne gongs na malkern;
- EDM: voorste mal dik, koper mannelijk, mannelijke mallijn hoekreiniging, achterste mal botpositie, kussenpositie;
- Boren, gaatje, vingerhoed; tooling top pinhole waterweg gat verwerkingslijn positie, rij positie paal;
- Schuine top, samengestelde vingerhoed, met vingerhoed.
4 Anderen
- (1) Chui, code schimmel pit, vuilnis nagel (limiet nagel);
- (2) Vliegend model;
- (3) mondstuk, steunkop, veer- en watertransport;
- (4) De positie van het opslaan van schimmel-, polijst-, voorvorm- en achtervormbotpositie;
- (5) Fijne waterstructuur, trekstangschroefhaak, veer;
- (6) Warmtebehandeling, afschrikken en nitreren van belangrijke onderdelen;
5. Gereedschapssoftware
UGNX, Pro/NC, CATIA, master cam, SURFCAM, topsolid cam, space-e, camworks, worknc, tebis, hyperMILL, PowerMILL, gibbscam, featurecam, etc.
6. Basisfuncties
- (1) Een paar gereedschappen bestaat over het algemeen uit een vrouwelijke matrijs, een pons en een matrijsbasis, en sommige daarvan kunnen meerdelige montagemodules zijn. Daarom vereisen de combinatie van bovenste en onderste matrijzen, de combinatie van inzetstukken en holtes en de assemblage van modules allemaal een hoge bewerkingsnauwkeurigheid. De maatnauwkeurigheid van precisiegereedschap is vaak tot μ m-niveau.
- (2) Het vormoppervlak van sommige producten, zoals autobekledingsonderdelen, vliegtuigonderdelen, speelgoed en huishoudelijke apparaten, bestaat uit een verscheidenheid aan gebogen oppervlakken, dus het oppervlak van de gereedschapsholte is zeer complex. Sommige oppervlakken moeten wiskundig worden behandeld.
- (3) De productie van kleine gereedschappen in batch is geen massaproductie. In veel gevallen wordt er maar één levering geproduceerd.
- (4) Er zijn veel soorten werkprocedures tijdens het bewerken, zoals frezen, kotteren, boren, ruimen en tappen.
- (5) Het gebruik van gereedschap voor herhaalde productie heeft een lange levensduur. Wanneer een paar gereedschappen wordt gebruikt na hun levensduur, is het noodzakelijk om deze te vervangen door een nieuwe, dus de productie van gereedschappen is vaak repetitief.
- (6) Soms zijn er geen tekeningen of gegevens bij de productie van profilering en moet de profileringsverwerking worden uitgevoerd in overeenstemming met het werkelijke object. Dit vereist een hoge precisie en geen vervorming.
- (7) Gereedschapsmaterialen zijn uitstekend en hebben een hoge hardheid. De belangrijkste materialen van gereedschap zijn gemaakt van hoogwaardig gelegeerd staal, vooral die met een hoge levensduur, die vaak zijn gemaakt van ledeburietstaal zoals Crl2 en CrWMn. Dit soort staal stelt strenge eisen, van blank smeden, verwerking tot warmtebehandeling. Daarom kan de voorbereiding van de verwerkingstechnologie niet worden genegeerd, vervorming door warmtebehandeling is ook een serieus probleem bij de verwerking.
Volgens de bovenstaande kenmerken moet de selectie van werktuigmachines zoveel mogelijk voldoen aan de verwerkingsvereisten. De functie van het CNC-systeem moet bijvoorbeeld sterk zijn, de precisie van de werktuigmachine moet hoog zijn, de stijfheid moet goed zijn, de thermische stabiliteit moet goed zijn en de profileringsfunctie moet worden geboden.
7. Processtroomregeling
- (1) Bodemverwerking, verwerkingshoeveelheidsgarantie;
- (2) Gieten van blanco benchmarkuitlijning, 2D, 3D inspectie van oppervlaktetoelagen;
- (3) Ruwe bewerking van 2D- en 3D-profiel, niet-installatie en niet-werkvlakbewerking (inclusief veiligheidsplatformoppervlak, buffermontageoppervlak, persplaatvlak en zijreferentievlak);
- (4) Voor de semi-afwerking moet het zijreferentievlak correct worden gevonden om de nauwkeurigheid te garanderen;
- (5) Semi-afwerking machinale bewerking van 2D- en 3D-oppervlakken, afwerking van alle soorten installatiewerkoppervlakken (inclusief limietblokinstallatie-oppervlak en contactoppervlak, inzet-installatie-oppervlak en achterkant, ponsinstallatie-oppervlak, afvalsnijder installatie-oppervlak en achterkant, veerinstallatie oppervlak en contactoppervlak, verschillende werkvlakken met slaglimiet, wiginstallatie-oppervlak en achterkant), semi-afwerking van alle soorten geleideoppervlakken en geleidegaten, en houd rekening met afwerking Verwerk datumgat en hoogtedatum en registreer gegevens;
- (6) Controleer en controleer de bewerkingsnauwkeurigheid opnieuw;
- (7) monteur inlegproces;
- (8) Voordat u klaar bent, lijnt u het referentievlak van het procesreferentiegat uit en controleert u de inzettoeslag;
- (9) Beëindig bewerkingsprofiel 2D, 3D, zijponsprofiel en gatpositie, voltooi het referentiegat van het bewerkingsproces en hoogtedatum, voltooi het machinale geleidingsoppervlak en het geleidegat;
- (10) Controleer en controleer de bewerkingsnauwkeurigheid opnieuw.
8. Zaken die aandacht behoeven
(1) De procesvoorbereiding is beknopt en gedetailleerd, en de verwerkingsinhoud wordt zo numeriek mogelijk uitgedrukt;
(2) Voor de belangrijkste en moeilijke verwerkingspunten moet vooral de nadruk worden gelegd op het vakmanschap;
(3) Het is noodzakelijk om verwerkingslocaties te combineren en het proces komt duidelijk tot uiting;
(4) Wanneer het inzetstuk afzonderlijk moet worden verwerkt, let dan op de procesvereisten van de verwerkingsnauwkeurigheid;
(5) Na gecombineerde verwerking, voor de inzetstukken die afzonderlijk moeten worden verwerkt, is het proces uitgerust met de benchmarkvereisten voor gescheiden verwerking tijdens gecombineerde verwerking;
(6) Veren worden het gemakkelijkst beschadigd bij het verwerken van mallen, dus moet worden gekozen voor malveren met een lange levensduur.
Verwerkingsproblemen van grote spuitgietmatrijzen van aluminiumlegeringen
1. Enorme grootte en gewicht
Bij het verwerken van grote matrijzen is het omgaan met de eigen enorme omvang en gewicht een grote uitdaging voor verwerkende bedrijven. De verwerking van grote mallen vereist vaak veel arbeid, speciale apparatuur en meerdere aanpassingen en opspanningen, en de verwerkingsnauwkeurigheid wordt ook beïnvloed door veel potentiële factoren en kan niet eenvoudig worden gegarandeerd.
2. De kwestie van acquisitiekosten:
De grootste kostenpost die rechtstreeks verband houdt met de verwerking en productie van verschillende grote matrijzen, zijn de aanschafkosten van de werktuigmachine. De werktuigmachine die grote matrijzen kan produceren, is vrij duur, vooral onder de complexe procesregeling zijn meerdere werktuigmachines nodig om alle processen van voorbewerken tot afwerken van de mal te voltooien. Dergelijke vroege hoge inputkosten zijn ook het grootste obstakel voor veel bedrijven om deze markt te betreden. Hieruit kunnen we zien dat als het voorbewerken en afwerken van grote matrijzen kan worden gerealiseerd op een geschikte gereedschapsmachine, zelfs als er maar één foutopsporing en opspannen nodig is, veel problemen zullen worden opgelost en de nauwkeurigheid van de bewerking kan worden gegarandeerd.
Bewerkingscentrum
1. De structuur van het gietijzerbed, de werktuigmachineas heeft de functie van de hittedissipatie;
Gietijzeren materiaal heeft een hoge stijfheid en warmteafvoer, dus het is het meest stabiele materiaal voor het vervaardigen van constructies voor werktuigmachines. Voor elke werktuigmachine die wordt gebruikt voor het frezen van grote onderdelen, moet deze eerst een zeer sterke gietijzeren structuur hebben en zijn uitgerust met een spindel met warmteafvoerfunctie.
Wat de hoofdas van de werktuigmachine betreft, moet deze ingebouwde koeltechnologie gebruiken om de hoofdas vanaf de buitenkant van het lager te koelen om ervoor te zorgen dat de hoofdas zelf niet doorbrandt of aan precisie verliest door thermische expansie tijdens langdurige bewerking. Deze factoren zijn erg belangrijk, omdat het verwerken van grote matrijzen lang duurt, en onder zware snijomstandigheden zal dit de hitte en stress van de mal verhogen. Daarom moeten de structurele delen van de werktuigmachine goede stijfheid en warmteafvoereigenschappen hebben, wat een voorwaarde is voor het verwerken van grootschalige hoogwaardige spuitgietmatrijzen van aluminiumlegeringen. Daarom is het noodzakelijk om de trillingen van de werktuigmachine tijdens het bewerkingsproces zoveel mogelijk te beperken en de warmte die tijdens het bewerkingsproces wordt gegenereerd snel te verspreiden. Het kiezen van de juiste bewerkingsmachines en gereedschappen kan een win-winsituatie opleveren in termen van kosten en cyclustijd.
2. Thermische stabiliteitstechnologie
Vanwege de lange verwerkingstijd moet ook rekening worden gehouden met de invloed van de omgevingstemperatuur. Bijvoorbeeld, het verwerken van een grote spuitgietvorm van aluminiumlegering op een gewone werktuigmachine, wanneer de omgevingstemperatuur met 10 ° C verandert, zal een temperatuurverandering van 6 ° C in de kolom van de bewerkingsmachine veroorzaken, wat een verandering van 0.07 mm in het parallellisme van de spilhoekplaat. Daarom moet het ontwerp van de werktuigmachine rekening houden met het effect van de omgevingstemperatuur om de invloed van de omgevingstemperatuur op de nauwkeurigheid van bewerkte onderdelen te voorkomen.
3. Snelheid
Voor een groot bewerkingscentrum voor matrijzen dat snel kan bewegen, moet de spilsnelheid van de grote werktuigmachine voor matrijzenverwerking ten minste 20000 r / min bereiken en moet de snijsnelheid van het metaal 762 ~ 20000 mm / min bereiken.
4. precisie
Precisiecontrole doorloopt altijd alle stadia van de matrijsverwerking. Als u ruwe bewerkingen en afwerking van grote mallen op een bewerkingscentrum moet uitvoeren, moet u de positioneringsnauwkeurigheid en herhaalpositioneringsnauwkeurigheid van de bewerkingsmachine strikt controleren. Het bewerkingscentrum voor grote matrijzen heeft over het algemeen een positioneringsnauwkeurigheid van ±1.5 m en een herhaalde positioneringsnauwkeurigheid van ± 1 m. Tegelijkertijd moet de nauwkeurigheid van de toonhoogte binnen 5 m worden gehouden.
5. Feedbackresolutie:
Voor zeer nauwkeurige oppervlaktebewerking is de feedbackresolutie van de werktuigmachine zelf erg belangrijk voor het detecteren van de nauwkeurigheid van de bewerkte onderdelen. Met de standaard feedbackresolutie van 1 m zijn de gewoonlijk verkregen resultaten niet erg bevredigend. Als de resolutie 0.05 m kan bereiken, is het afwerkingsresultaat bijna zonder gebreken. Bovendien kan de verwerkingskwaliteit van het oppervlak van het onderdeel verder worden verbeterd door de beheersing van de resolutie van bewerkingsmachines, schaalfeedback en kogelomloopspindels met kleine spoed.
6. spil
De spil die op het bewerkingscentrum voor grote vormen wordt gebruikt, moet voldoen aan de vereisten van ruwe bewerking, semi-nabewerken en hoogwaardige afwerking, en als referentiestandaard moet de kwaliteit van de oppervlaktebewerking die kan worden bereikt, worden gecontroleerd op een niveau van 2 m. Meestal is het erg belangrijk voor de afwerking van het sluitoppervlak van de matrijs en het deel van de scheidingslijn, maar onder de traditionele technologie moeten veel matrijsfabrikanten handmatig polijsten gebruiken om het gebrek aan nauwkeurigheid bij het bewerken van het gereedschap te compenseren. Omdat grootschalige bewerkingsmachines duur zijn om te bouwen, is het uiteraard onpraktisch om voor dit proces een multifunctionele bewerkingsmachine aan te schaffen.
Bovendien moet een redelijk spindelontwerp in staat zijn om de levensduur van het gereedschap te maximaliseren, zodat het tijdens de bewerkingscyclus met lage trillingen en lage temperatuurstijging kan blijven werken. Wanneer bijvoorbeeld auto-dashboardmallen worden verwerkt op een groot bewerkingscentrum voor matrijzen en een 16 mm CBN-wisselplaat wordt gebruikt voor afwerkingsgereedschappen, kan de verwerkingssnelheid 8 m / min bereiken, is de levensduur langer dan 30 uur en kan de kwaliteit van het verwerkte oppervlak worden gecontroleerd binnen 0.336~3.2m. Het is te zien dat, gezien de toename van de gereedschapskosten bij het verwerken van grote matrijzen, het gebruik van speciaal ontworpen werktuigmachines voor het verwerken van grote matrijzen niet alleen de levensduur van de gereedschappen kan verlengen, maar ook veel gereedschapskosten kan besparen voor het verwerken van elke mal .
7. Beweegbare meerassige bewerkingskop
Door de beperking van de matrijsgrootte en het gewicht duurt het meestal lang om het werkstuk op te spannen. Daarom vermindert het gebruik van een 3-assig bewerkingscentrum niet alleen het aantal foutopsporings- en klemtijden van het werkstuk, maar heeft het ook geen invloed op de bewerkingsnauwkeurigheid van de werktuigmachine, waardoor de productiecapaciteit van de werkplaats voor het verwerken van grote mallen.
De beweegbare meerassige bewerkingskop kan worden gebruikt om grote vormen met bijzonder complexe structuren te verwerken. De bewerkingskop ontworpen volgens de variabele geometrie maakt gelijktijdige bewerking met 3 assen mogelijk. Voor het frezen en bewerken van diepe holtes kan slechts één klemming van het werkstuk worden gebruikt. Mallen en koelgaten, evenals het snijden van vele andere onderdelen met complexe geometrieën. Wanneer de spil bijvoorbeeld onder een optimale hoek staat, kan de nabijheid van de bewerkingskop tot het freesbewerkingspunt worden vergroot, zodat de meerassige bewerkingskop kan worden gebruikt om de bewerking van het schuine gat te voltooien.
Omdat de meerassige bewerkingskop het oppervlak van het werkstuk bewerkt, wordt bovendien de radiusrand van het gereedschap gebruikt in plaats van de punt van het gereedschap, zodat de oppervlakteruwheid kan worden verbeterd.
8. Chipbeheer
Bij het snijden van metaal ontstaat een grote hoeveelheid spanen. Als het niet op tijd kan worden geëlimineerd, zal het onvermijdelijk leiden tot secundair snijden en de temperatuurstijging van structurele onderdelen van werktuigmachines of werkstukoppervlakken veroorzaken. Er zijn meestal 18 spaangaten onder de werktafel van een groot matrijsbewerkingscentrum, ongeacht waar de werktafel wordt verplaatst, de spanen kunnen betrouwbaar worden verwijderd. Er zijn 4 ingebouwde scharnierende spanentransportbanden op de werktuigmachine, die de spanen met hoge snelheid naar de voorkant van de werktuigmachine sturen.
9. Hogedruk koelvloeistof
Bij het verwerken van grote matrijzen speelt hogedrukkoelvloeistof een zeer belangrijke rol. Wanneer bijvoorbeeld de 2+3-assige bewerkingsmethode wordt gebruikt om schuine gaten te boren, is een koelmiddel met een druk van 1000 psi (1psi = 6890 Pa) vereist om de spanen effectief te verwijderen en een hogere precisie te bereiken. Als zo'n hogedrukkoelvloeistof niet aanwezig is, moeten extra werktuigmachines worden toegevoegd bij het verwerken van schuine gaten, is een secundaire installatie vereist, wat de verwerkingsnauwkeurigheid vermindert en de cycluskosten verhoogt. Volgens de bovenstaande analyse kan worden gezien dat de eenvoudige verwerking van grote matrijzen vereist dat de werktuigmachine meer en betere functies heeft. Het nieuwe MCC2516VG 3-assige horizontale bewerkingscentrum ontwikkeld door Makino, de spilsnelheid kan 15000r/min bereiken, en past de "askernkoeling"-methode en de "lager interne druksmering"-functie toe om ervoor te zorgen dat de spil en de daaraan bevestigde lagers kunnen op tijd en effectief worden gekoeld.
Bovendien kan de hoofdas niet alleen langs de horizontale X-as, de verticale Y-as en de voorste en achterste Z-asrichtingen bewegen, maar ook roteren met de A-as en de C-as. Met twee indexeringsfuncties kan het niet alleen de aanpassingswerklast verminderen, maar ook complexe werkstukken snijden, zoals bumpers, instrumentenpanelen en koplamplenzen van auto's.
Bewaar de bron en het adres van dit artikel voor herdruk:Basiskennis van spuitgieten van aluminiumlegeringen
Minge Spuitgietbedrijf zijn toegewijd aan het vervaardigen en leveren van hoogwaardige en hoogwaardige gietstukken (het assortiment metalen spuitgietonderdelen omvat voornamelijk: Dunwandig spuitgieten,Hot Chamber Spuitgieten,Koude kamer spuitgieten),Ronde Service (Die Casting Service,CNC-bewerking,Matrijzen maken, Oppervlaktebehandeling). Elk aangepast aluminium spuitgieten, magnesium of Zamak / zink spuitgieten en andere gietstukken zijn welkom om contact met ons op te nemen.
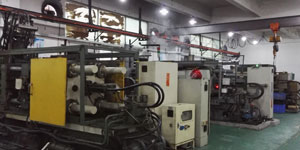
Onder controle van ISO9001 en TS 16949 worden alle processen uitgevoerd door honderden geavanceerde spuitgietmachines, 5-assige machines en andere faciliteiten, variërend van blasters tot Ultra Sonic-wasmachines. Minghe heeft niet alleen geavanceerde apparatuur, maar heeft ook professionele team van ervaren ingenieurs, operators en inspecteurs om het ontwerp van de klant waar te maken.
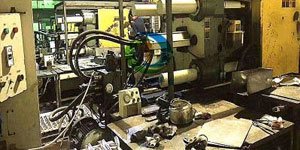
Contractfabrikant van spuitgietwerk. Mogelijkheden zijn onder meer koude kamer aluminium spuitgietonderdelen vanaf 0.15 lbs. tot 6 lbs., snelwissel instellen en machinaal bewerken. Diensten met toegevoegde waarde omvatten polijsten, trillen, ontbramen, stralen, schilderen, plateren, coaten, assembleren en bewerken. Materialen waarmee gewerkt is, zijn legeringen zoals 360, 380, 383 en 413.
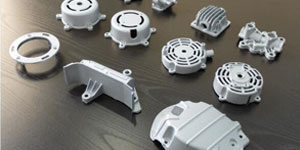
Hulp bij ontwerp van spuitgieten van zink/concurrent engineering. Custom fabrikant van precisie gegoten zink. Miniatuurgietstukken, hogedrukgietstukken, multi-slide gietstukken, conventionele gietstukken, eenheidsmatrijs en onafhankelijke spuitgietstukken en holteverzegelde gietstukken kunnen worden vervaardigd. Gietstukken kunnen worden vervaardigd in lengtes en breedtes tot 24 inch met een tolerantie van +/- 0.0005 inch.
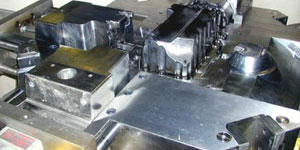
ISO 9001: 2015 gecertificeerde fabrikant van gegoten magnesium. Mogelijkheden zijn onder hoge druk spuitgieten van magnesium tot 200 ton hete kamer en 3000 ton koude kamer, gereedschapsontwerp, polijsten, gieten, machinale bewerking, poeder- en vloeistofverven, volledige QA met CMM-mogelijkheden , montage, verpakking & levering.
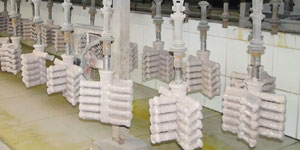
ITAF16949 gecertificeerd. Extra castingservice omvat: investering gieten,zandgieten,Zwaartekracht gieten, Verloren schuimafgietsel,Centrifugaal gieten,Vacuümgieten,Permanent vormgieten,. Mogelijkheden zijn onder meer EDI, technische assistentie, solide modellering en secundaire verwerking.
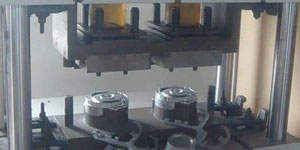
Gietindustrieën Casestudy's over onderdelen voor: auto's, fietsen, vliegtuigen, muziekinstrumenten, waterscooters, optische apparaten, sensoren, modellen, elektronische apparaten, behuizingen, klokken, machines, motoren, meubels, sieraden, mallen, telecom, verlichting, medische apparaten, fotografische apparaten, Robots, sculpturen, geluidsapparatuur, sportuitrusting, gereedschap, speelgoed en meer.
Wat kunnen we u hierna helpen doen?
∇ Ga naar de startpagina voor Spuitgieten China
→Gietonderdelen- Zoek uit wat we hebben gedaan.
→Gerangschikte tips over Spuitgietdiensten
By Minghe Die Casting Fabrikant: |Categorieën: Handige artikelen |Materiaal Tags: Aluminium gieten, Zink gieten, Magnesium gieten, Titanium gieten, Gieten van roestvrij staal, Messing gieten,Brons gieten,Video casten,Geschiedenis van ons bedrijf,Aluminium spuitgieten |Reacties uitgeschakeld