7 Veelgestelde vragen op het gebied van matrijsproductie
Wat is de belangrijkste factor die de bewerkbaarheid van het materiaal beïnvloedt?
De chemische samenstelling van staal is erg belangrijk. Hoe hoger de legeringssamenstelling van het staal, hoe moeilijker het te verwerken is. Wanneer het koolstofgehalte toeneemt, neemt de metaalbewerkingsprestatie af.
De structuur van staal is ook erg belangrijk voor het snijden van metaal. Verschillende structuren omvatten: gesmeed, gegoten, geëxtrudeerd, gewalst en machinaal bewerkt. Smeedstukken en gietstukken hebben zeer moeilijk te bewerken oppervlakken.
Hardheid is een belangrijke factor die de snijprestaties van metaal beïnvloedt. De algemene regel is dat hoe harder het staal, hoe moeilijker het te bewerken is. Snelstaal (HSS) kan worden gebruikt voor het verwerken van materialen met een hardheid tot 330-400HB; snelstaal + TiN-coating kan materialen verwerken met een hardheid tot 45HRC; en voor materialen met een hardheid van 65-70HRC, moet u hardmetaal, keramiek, cermets en kubisch boornitride (CBN) gebruiken.
Niet-metalen insluitsels hebben over het algemeen een nadelig effect op de standtijd. Al2O3 (aluminiumoxide), dat een pure keramiek is, is bijvoorbeeld zeer abrasief.
De laatste is restspanning, die prestatieproblemen bij het snijden van metaal kan veroorzaken. Het wordt vaak aanbevolen om na een voorbewerking een spanningsontlastingsproces uit te voeren.
Wat zijn de snijeigenschappen van gietijzer?
Over het algemeen is het:
Hoe hoger de hardheid en sterkte van gietijzer, hoe lager de snijprestaties van metaal en hoe lager de verwachte levensduur van de messen en frezen. De meeste soorten gietijzer die bij de productie van metaal worden gebruikt, hebben over het algemeen goede prestaties bij het snijden van metaal. De snijprestaties van metaal zijn gerelateerd aan de structuur en harder perlitisch gietijzer is ook moeilijker te verwerken. Vlokgrafiet gietijzer en smeedbaar gietijzer hebben uitstekende snij-eigenschappen, terwijl nodulair gietijzer vrij slecht is.
De belangrijkste soorten slijtage die optreden bij het bewerken van gietijzer zijn: slijtage, adhesie en diffusieslijtage. Slijtage wordt voornamelijk veroorzaakt door carbiden, zanddeeltjes en hard gegoten huiden. Bondslijtage met snijkantopbouw treedt op bij lage snijtemperatuur en snijsnelheid. Het ferrietgedeelte van gietijzer is het gemakkelijkst aan het blad te lassen, maar dit kan worden ondervangen door de snijsnelheid en temperatuur te verhogen.
Aan de andere kant is diffusieslijtage temperatuurafhankelijk en treedt op bij hoge snijsnelheden, vooral wanneer hoogwaardige gietijzersoorten worden gebruikt. Deze soorten hebben een hoge weerstand tegen vervorming, wat leidt tot hoge temperaturen. Deze slijtage houdt verband met de interactie tussen het gietijzer en het snijgereedschap, waardoor sommige gietijzers moeten worden bewerkt met keramische of kubische boornitride (CBN) snijgereedschappen met hoge snelheden om een goede standtijd en oppervlaktekwaliteit te verkrijgen.
Over het algemeen zijn de typische gereedschapseigenschappen die vereist zijn voor het bewerken van gietijzer: hoge thermische hardheid en chemische stabiliteit, maar het is ook gerelateerd aan het proces, het werkstuk en de snijomstandigheden; de snijkant moet taaiheid, weerstand tegen hittemoeheid en snijkantsterkte hebben. De mate van voldoening van het snijden van gietijzer hangt af van hoe de slijtage van de snijkant zich ontwikkelt: snelle botheid betekent dat hete scheuren en inkepingen ervoor zorgen dat de snijkant voortijdig breekt, werkstukbeschadigingen, slechte oppervlaktekwaliteit, overmatige golving, enz. Normale flankslijtage , balans en scherpe snijkanten zijn wat over het algemeen inspanning vereist.
Wat zijn de belangrijkste en gebruikelijke verwerkingsprocedures bij het vervaardigen van matrijzen?
Het snijproces moet worden onderverdeeld in ten minste 3 procestypes:
Ruwe bewerking, semi-nabewerken en nabewerken, en soms zelfs supernabewerken (meestal high-speed snijtoepassingen). Na het semi-nabewerkingsproces wordt het restfrezen uiteraard voorbereid voor de nabewerking. In elk proces moet worden gestreefd naar een uniform verdeelde marge voor het volgende proces, wat erg belangrijk is. Als de richting en werkbelasting van het gereedschapspad zelden snel veranderen, kan de levensduur van het gereedschap worden verlengd en voorspelbaarder. Indien mogelijk moet het afwerkingsproces worden uitgevoerd op een speciale werktuigmachine. Dit zal de geometrische nauwkeurigheid en kwaliteit van de mal verbeteren in een kortere debugging- en montagetijd.
Wat voor soort tools moeten worden gebruikt in deze verschillende processen?
Ruw bewerkingsproces: frees met ronde bladen, kogelfrees en frezen met grote neusboogradius.
Semi-nabewerkingsproces: frees met ronde bladen (frees met ronde bladen met een diameterbereik van 10-25 mm), frees met kogelkop.
Afwerkingsproces: frees met ronde bladen, frees met kogelkop.
Restfreesproces: frees met ronde bladen, frees met kogelkop, verticale frees.
Het is erg belangrijk om het snijproces te optimaliseren door een combinatie van speciale gereedschapsmaten, geometrieën en hardmetaalsoorten te selecteren, evenals snijparameters en geschikte freesstrategieën.
Voor de gereedschappen met hoge productiviteit die kunnen worden gebruikt, zie catalogus C-1102:1 voor het maken van matrijzen
Is er een van de belangrijkste factoren in het snijproces?
Een van de belangrijkste doelen in het snijproces is het creëren van een uniform verdeelde bewerkingstoeslag voor elk gereedschap in elk proces. Dit betekent dat gereedschappen met verschillende diameters (van groot tot klein) moeten worden gebruikt, vooral bij voorbewerken en semi-nabewerken. Het belangrijkste criterium moet op elk moment zo dicht mogelijk bij de uiteindelijke vorm van de mal in elk proces liggen.
Het verstrekken van uniform verdeelde bewerkingstoegiften voor elk gereedschap zorgt voor een constante en hoge productiviteit en een veilig snijproces. Wanneer ap/ae (axiale snedediepte/radiale snedediepte) niet verandert, kunnen ook de snijsnelheid en voeding constant op een hoog niveau worden gehouden. Op deze manier zijn de mechanische actie en veranderingen in de werkbelasting op de snijkant klein, dus de gegenereerde hitte en vermoeidheid zijn ook minder, waardoor de standtijd wordt verlengd. Als de daaropvolgende processen enkele semi-nabewerkingsprocessen zijn, met name alle afwerkingsprocessen, kan onbemande verwerking of gedeeltelijke onbemande verwerking worden uitgevoerd. Constante materiaalbewerkingstoegift is ook de basisnorm voor snijtoepassingen met hoge snelheid.
Een ander gunstig effect van de constante bewerkingstoeslag is het kleine nadelige effect op de werktuigmachine-geleiderails, kogelschroeven en spindellagers.
Waarom zijn frezen met ronde bladen de meest voorkomende keuze voor voorbewerkingsgereedschappen?
Als een vierkante hoekfrees wordt gebruikt voor het voorbewerken van de holte, zal een grote hoeveelheid getrapte snijtoeslag worden verwijderd bij de semi-nabewerken. Hierdoor verandert de snijkracht en zal het gereedschap buigen. Het resultaat is dat er een ongelijkmatige bewerkingstoeslag overblijft voor de afwerking, waardoor de geometrische nauwkeurigheid van de mal wordt beïnvloed. Als u een vierkante hoekfrees (met een driehoekige wisselplaat) met een zwakkere neus gebruikt, geeft dit onvoorspelbare snijeffecten. Driehoekige of diamanten wisselplaten produceren ook grotere radiale snijkrachten, en omdat het aantal snijkanten van de wisselplaten klein is, zijn het minder economische voorbewerkingsgereedschappen.
Anderzijds kan het ronde inzetstuk in verschillende materialen en in alle richtingen worden gefreesd. Als het wordt gebruikt, is de overgang tussen aangrenzende gereedschapsbanen soepeler en kan het ook een kleinere en meer uniforme bewerking voor semi-nabewerken achterlaten. marge. Een van de kenmerken van ronde messen is dat de dikte van de chips die ze produceren variabel is. Hierdoor kunnen ze hogere voedingen gebruiken dan de meeste andere wisselplaten.
De instelhoek van de ronde wisselplaat is veranderd van bijna nul (zeer ondiep snijden) naar 90 graden, en de snijactie is erg soepel. Bij de maximale zaagdiepte is de instelhoek 45 graden. Bij het snijden langs een rechte wand met een buitencirkel is de intredehoek 90 graden. Dit verklaart ook waarom de kracht van het ronde mesgereedschap groot is - de snijbelasting neemt geleidelijk toe. Voor voorbewerken en semi-voorbewerken moet altijd de eerste keuze zijn met rondbladige frezen, zoals CoroMill200 (zie malfabricagecatalogus C-1102:1). Bij 5-assig snijden zijn ronde wisselplaten zeer geschikt, vooral omdat er geen beperkingen zijn.
Door het gebruik van een goede programmering kunnen frezen met ronde wisselplaten de kogelfrezen grotendeels vervangen. Het ronde blad met kleine uitloop wordt gecombineerd met de fijngeslepen, positieve spaanhoek en lichte snijgeometrie, en kan ook worden gebruikt voor semi-nabewerken en sommige afwerkingsprocessen.
Wat is de effectieve snijsnelheid (ve) en waarom is het altijd erg belangrijk voor de basisberekening van de effectieve snijsnelheid op de effectieve diameter van hoge productiviteit.
Aangezien de tafelvoeding afhankelijk is van de rotatiesnelheid bij een bepaalde snijsnelheid, wordt de tafelvoeding onjuist berekend als de effectieve snelheid niet wordt berekend.
Als de nominale diameter van het gereedschap (Dc) wordt gebruikt bij het berekenen van de snijsnelheid en de snijdiepte ondiep is, is de effectieve of werkelijke snijsnelheid veel lager dan de berekende snelheid. Zoals CoroMill200-gereedschappen met ronde wisselplaat (vooral in het bereik van kleine diameters), kogelfrezen, vingerfrezen met grote neusboogradius en CoroMill390-vingerfrezen en ander gereedschap (raadpleeg voor deze gereedschappen Sandvik Coromant's matrijsproductie Monster C-1102:1 ). Als gevolg hiervan is de berekende voedingssnelheid ook veel lager, wat de productiviteit sterk vermindert. Belangrijker is dat de snijomstandigheden van het gereedschap lager zijn dan de mogelijkheden en het aanbevolen toepassingsbereik.
Bewaar de bron en het adres van dit artikel voor herdruk:7 Veelgestelde vragen op het gebied van matrijsproductie
Minge Spuitgietbedrijf zijn toegewijd aan het vervaardigen en leveren van hoogwaardige en hoogwaardige gietstukken (het assortiment metalen spuitgietonderdelen omvat voornamelijk: Dunwandig spuitgieten,Hot Chamber Spuitgieten,Koude kamer spuitgieten),Ronde Service (Die Casting Service,CNC-bewerking,Matrijzen maken, Oppervlaktebehandeling). Elk aangepast aluminium spuitgieten, magnesium of Zamak / zink spuitgieten en andere gietstukken zijn welkom om contact met ons op te nemen.
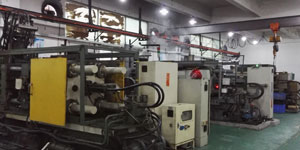
Onder controle van ISO9001 en TS 16949 worden alle processen uitgevoerd door honderden geavanceerde spuitgietmachines, 5-assige machines en andere faciliteiten, variërend van blasters tot Ultra Sonic-wasmachines. Minghe heeft niet alleen geavanceerde apparatuur, maar heeft ook professionele team van ervaren ingenieurs, operators en inspecteurs om het ontwerp van de klant waar te maken.
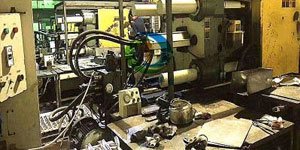
Contractfabrikant van spuitgietwerk. Mogelijkheden zijn onder meer koude kamer aluminium spuitgietonderdelen vanaf 0.15 lbs. tot 6 lbs., snelwissel instellen en machinaal bewerken. Diensten met toegevoegde waarde omvatten polijsten, trillen, ontbramen, stralen, schilderen, plateren, coaten, assembleren en bewerken. Materialen waarmee gewerkt is, zijn legeringen zoals 360, 380, 383 en 413.
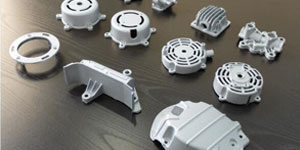
Hulp bij ontwerp van spuitgieten van zink/concurrent engineering. Custom fabrikant van precisie gegoten zink. Miniatuurgietstukken, hogedrukgietstukken, multi-slide gietstukken, conventionele gietstukken, eenheidsmatrijs en onafhankelijke spuitgietstukken en holteverzegelde gietstukken kunnen worden vervaardigd. Gietstukken kunnen worden vervaardigd in lengtes en breedtes tot 24 inch met een tolerantie van +/- 0.0005 inch.
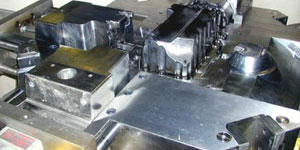
ISO 9001: 2015 gecertificeerde fabrikant van gegoten magnesium. Mogelijkheden zijn onder hoge druk spuitgieten van magnesium tot 200 ton hete kamer en 3000 ton koude kamer, gereedschapsontwerp, polijsten, gieten, machinale bewerking, poeder- en vloeistofverven, volledige QA met CMM-mogelijkheden , montage, verpakking & levering.
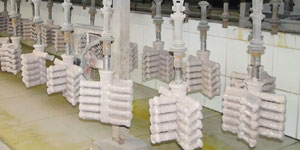
ITAF16949 gecertificeerd. Extra castingservice omvat: investering gieten,zandgieten,Zwaartekracht gieten, Verloren schuimafgietsel,Centrifugaal gieten,Vacuümgieten,Permanent vormgieten,. Mogelijkheden zijn onder meer EDI, technische assistentie, solide modellering en secundaire verwerking.
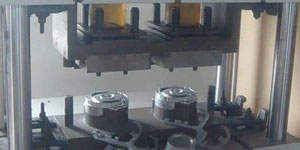
Gietindustrieën Casestudy's over onderdelen voor: auto's, fietsen, vliegtuigen, muziekinstrumenten, waterscooters, optische apparaten, sensoren, modellen, elektronische apparaten, behuizingen, klokken, machines, motoren, meubels, sieraden, mallen, telecom, verlichting, medische apparaten, fotografische apparaten, Robots, sculpturen, geluidsapparatuur, sportuitrusting, gereedschap, speelgoed en meer.
Wat kunnen we u hierna helpen doen?
∇ Ga naar de startpagina voor Spuitgieten China
→Gietonderdelen- Zoek uit wat we hebben gedaan.
→Gerangschikte tips over Spuitgietdiensten
By Minghe Die Casting Fabrikant: |Categorieën: Handige artikelen |Materiaal Tags: Aluminium gieten, Zink gieten, Magnesium gieten, Titanium gieten, Gieten van roestvrij staal, Messing gieten,Brons gieten,Video casten,Geschiedenis van ons bedrijf,Aluminium spuitgieten |Reacties uitgeschakeld