De methode en toepassing van met zand beklede gietijzeren gietvorm
Wat is gieten van ijzeren mallen met zandcoating
Zandgieten met ijzeren mal is een gietproces waarbij een dunne laag zand wordt bedekt op de binnenholte van een metalen mal (een ijzeren mal genoemd) om een mal te vormen. Omdat de zandcoatinglaag relatief dun is (4~8 mm), is het economisch redelijk om duurdere modelleermaterialen van hoge kwaliteit te gebruiken. Hierdoor wordt de kwaliteit van de gietstukken sterk verbeterd en wordt de verspilling aanzienlijk verminderd; door de stijfheid van de met ijzerzand beklede gietvorm. Zeer goed, waardoor de maatnauwkeurigheid en compactheid van het gietstuk aanzienlijk worden verbeterd.
Duitsland, de voormalige Sovjet-Unie en andere landen begonnen rond de jaren zestig gietstukken met ijzerzand te gebruiken bij de gietproductie, voornamelijk voor de productie van nodulair gietijzeren krukassen, remnaven, remschijven, cilindervoeringen, bomgranaten, tanksporen en motorbases , enz. Soort gietstukken. Het Chinese toepassingsonderzoek naar gietstukken met een ijzeren mal begon in het begin van de jaren zeventig. In 1960 werkten het Zhejiang Mechanical and Electrical Design Institute en de Yongkang Tractor Factory samen om dit proces voor het eerst te gebruiken bij de massagietproductie van S1970-krukasplano's. Tegelijkertijd werd de prestatie-evaluatie van de door dit proces geproduceerde nodulair gietijzeren krukas voltooid, in termen van vermoeiingssterkte (vergelijking van vermoeiingsgrensspanning σ-1979), breuksterkte (vergelijking van drempelwaarde ΔKth en vergelijking van breuktaaiheid K195C ) en levensduur (vergelijking van de duurzaamheidstest van een bank van 1 uur), enz., vergeleken met de krukas van zandgieten, is het beter dan zandgieten. In de daaropvolgende 1 jaar is het proces voortdurend verbeterd in de toepassing. Begin jaren negentig hadden zeven bedrijven het proces toegepast, met name het met ijzerzand beklede gietproces voor eencilinderkrukassen en viercilinderkrukassen. Een groot succes. De representatieve ondernemingen tijdens deze periode zijn de Yongkang-tractorfabriek, de Shangyu Power Machinery-fabriek, de Wangdu-krukas- en drijfstangfabriek, de Wanbei-krukasfabriek, de Jinhua-fabriek voor interne verbrandingsmotoronderdelen, de Changzhou-dieselmotorfabriek, enz. In 10000 keurde de Staatsplanningscommissie ijzer goed. schimmel zandgecoat gieten als een belangrijk project voor de promotie van nieuwe technologie van het "Achtste Vijfjarenplan" van het land, en maakte het Zhejiang Mechanical and Electrical Design Institute tot de technische ondersteuningseenheid van het project. Dit is een aanzienlijke verbetering in de zandgecoate giettechnologie van mijn land. Ontwikkeling heeft een grote rol gespeeld bij de promotie. Nadat ons instituut het promotieproject had ondernomen, werd in de daaropvolgende vijf tot zes jaar een reeks problemen met het met ijzer beklede zandgieten voor massaproductie feitelijk opgelost.
Hoofdzakelijk:
- ①Ontworpen en voltooide de met zand gecoate vormmachine, die het al lang bestaande probleem van het opnieuw aanbrengen en vervangen van kernschieters oploste;
- ②De standaard productielijn voor zandbekleed gieten van het ijzertype werd voltooid en gestandaardiseerd, en de oorspronkelijke, relatief eenvoudige productielijn voor zandbekleed gieten van het ijzertype werd verbeterd en toegepast in bedrijven zoals Shanghai Nodular Iron Plant;
- ③De toepassing van met zand bedekt ijzergietwerk wordt uitgebreid naar sommige gietstukken met moeilijkere gietprocessen, zoals zescilinderkrukassen en driecilinderkrukassen;
- ④ Het introduceren van gecoat zand in de productie van met ijzer bedekt zandgieten, waardoor de kwaliteit van het met zand bedekte gietwerk aanzienlijk wordt verbeterd;
- ⑤Het ontwerp van het met zand gecoate gietproces met ijzeren mal is verder gestandaardiseerd en het ontwerpniveau is ook aanzienlijk verbeterd. De computersimulatiesoftware van het met zand beklede gietproces met ijzeren mal en de computerondersteunde ontwerpsoftware van het met zand beklede gietproces met ijzeren mal zijn ontwikkeld.
Momenteel hebben bijna honderd ondernemingen in het hele land een met ijzerzand bedekt gietproces toegepast om meer dan 30 soorten gietstukken te produceren, zoals nodulair gietijzeren krukassen, nokkenassen, balansassen, drukbestendige kleplichamen, cilindervoeringen en slijtvaste tandwiel schijven. De jaarlijkse productie wordt geschat op gietstukken. Ongeveer 10×104t. Typische bedrijven zijn onder meer de Shanghai Automobile Foundry General Ductile Iron Factory, Shenyang No. 1 Crankash Factory, Guangxi Baikuang Group, Yixing Machinery General Factory, Shandong Jiuyang Group, Zhejiang Shuguang Crankash Factory, Benxi Tianyuan Crankash Factory, Baoding Film Machinery Factory, Shanxi Lucheng Crankash Factory , Hebei Xinji Crankshaft Factory, enz. Deze bedrijven hebben echter verschillende manieren om het proces te introduceren: sommige hebben ons instituut toevertrouwd om het ontwerp of de bouw te doen, en sommige hebben het zelf geïmiteerd en ontwikkeld. Daarom is hun beheersing van het met zand beklede gietproces met ijzeren mallen heel anders. Als we alleen het afvalpercentage van met zand beklede ijzeren mallen als voorbeeld nemen, kunnen veel bedrijven die een beter inzicht hebben dit percentage stabiliseren op ongeveer 3% en zeer goede economische voordelen hebben behaald. Er zijn echter ook een paar bedrijven waarvan het afvalpercentage van met zand beklede ijzeren mallen wel ongeveer 20% bedraagt, wat de economische voordelen van dit proces aanzienlijk compenseert. De reden is dat deze bedrijven de essentiële ontwerp- en productieprincipes van het proces niet volledig hebben begrepen en dat het productiemanagement wordt verwaarloosd.
De belangrijkste oplossingen voor het ontwerp en de daadwerkelijke productie van het ijzergietproces met zandcoating:
- ①De dikte van de ijzeren wand en de dikte van de zandcoatinglaag en de combinatie van beide kunnen voldoen aan de verschillende eisen voor het stollen en afkoelen van gietstukken met verschillende wanddiktes en verschillende materialen;
- ②Handige en economische vormmethode met zandcoating om te voldoen aan de eisen van verschillende gietstukken voor oppervlaktekwaliteit en maatnauwkeurigheid;
- ③Procesparameters. Zoals bepaling van poortsysteem, zandschietsysteem, uitlaatsysteem etc.;
- ④ De realisatie van massaproductie. Bijvoorbeeld het ontwerp en de vorm van de productielijn en de met zand bedekte host- en hulpapparatuur;
- ⑤Het formuleren van procesvoorschriften, zoals de voorschriften voor het gieten, koelen en uitpakken, evenals het aanpassen van de gietsamenstelling.
Warmte-uitwisselingskenmerken van ijzer-type zandgecoat gietwerk
Nadat het vloeibare metaal in de met ijzerzand beklede gietvorm is gegoten, is de "gietzandbekleding-ijzervorm" een onstabiel warmtewisselingssysteem. Om het probleem te vereenvoudigen wordt aangenomen dat het gieten semi-beperkt is; en er wordt aangenomen dat het temperatuurveld van elke component in het systeem in een rechte lijn is verdeeld. Figuur 1 toont een deel van het systeem. Het is duidelijk dat dezelfde specifieke warmtestroom q door elke component in het systeem gaat:
Twee warmteoverdrachtscriteria die respectievelijk de warmte-uitwisselingsintensiteit vertegenwoordigen tussen het gietstuk en de met zand beklede laag, en de ijzeren mal en de met zand beklede laag. k1 is de verhouding tussen de thermische weerstand van het gietstuk en de thermische weerstand van de zandcoating; k2 is de verhouding tussen de thermische weerstand van het ijzertype en de thermische weerstand van de zandcoating. Gezien de combinatie van k1 en k2, met de verandering van de dikte van de zandcoating, zijn er de volgende drie verschillende situaties van warmteoverdracht tussen "gieten-zandcoaten-ijzeren mal" die feitelijk kunnen optreden:
- ① Wanneer k≤1 en k2≤1 ligt de zandcoatinglaag binnen de normale dikte en neemt de afkoelsnelheid van het gietstuk toe naarmate de dikte van de zandcoatinglaag afneemt.
- ②Wanneer de dikte van de met zand beklede laag een bepaalde dikte overschrijdt, heeft de ijzeren mal geen effect op de koeling van het gietstuk. Op dit moment is het gelijk aan gewoon zandgieten of harszandgieten. Omdat de thermische geleidbaarheid van de met zand beklede laag veel kleiner is dan die van het ijzertype, koelt het gietstuk langzaam af.
- ③Wanneer k≧1 en k2≧1 is de dikte van de zandcoating te dun, wat overeenkomt met het gieten van metalen mallen.
De bovengenoemde warmte-uitwisselingskarakteristieken zijn door experimenten bevestigd. Wanneer de dikte van de zandcoatinglaag van het ijzer-type zandgecoate gietstuk van de krukas (CTЦ-14) geleidelijk verandert van 4 naar 32 mm, wordt de hoeveelheid cementiet in de krukasstructuur voortdurend verminderd en wordt de hoeveelheid perliet en de De hoeveelheid ferriet blijft toenemen. Wanneer de dikte van de gezandstraalde laag kleiner is dan 4 mm, is de koelsterkte van het gietstuk vergelijkbaar met die van het metaaltype (dikke verf); wanneer de met zand beklede laag groter is dan 32 mm, is de koelsterkte gelijk aan die van gewoon harszandgieten.
Wanneer met ijzerzand bedekt gietwerk wordt gebruikt bij de productie van verschillende gietstukken, wordt door middel van experimenten of empirische analogie de dikte van de met zand bedekte laag en de dikte van het ijzer bepaald om de stollingssnelheid van het gietstuk te controleren. Bij het ontwerp van het 490Q nodulair gietijzeren krukasgietproces met zandcoating is de dikte van de zandcoatinglaag bijvoorbeeld 5-8 mm en de wanddikte van de ijzeren mal 20-30 mm, wat een hoge kwaliteit oplevert als -gegoten nodulair gietijzer zonder stootborden. De belangrijkste reden is:
- ① De met zand beklede laag regelt effectief de afkoelsnelheid van het gietstuk, enerzijds zorgt het ervoor dat het gietstuk er minder wit uitziet, en anderzijds is de afkoelsnelheid groter dan die bij zandgieten. Zoals weergegeven in figuur 2, daalt de temperatuur van het gietstuk na 930 minuten naar ongeveer 8°C wanneer het gesmolten ijzer in de met zand beklede ijzeren mal wordt gegoten, en duurt het 24 minuten voordat de zandmal naar dezelfde temperatuur is gedaald. en de koelsnelheid wordt ongeveer drie keer verhoogd. Als gevolg hiervan worden de mechanische eigenschappen van gietstukken aanzienlijk verbeterd.
- ②De ijzeren mal heeft geen concessie, maar de dunne zandcoating kan de krimpweerstand van de mal op passende wijze verminderen; en de stijfheid van de ijzeren mal maakt effectief gebruik van de grafitisatie-expansie van het nodulair gietijzer tijdens het stollingsproces om gieten zonder stijgbuis te bereiken; door de dunne zandcoating is de holte niet gemakkelijk te vervormen en is de precisie van het gietstuk aanzienlijk verbeterd dan die van de zandvorm.
Twee warmteoverdrachtscriteria die respectievelijk de warmte-uitwisselingsintensiteit vertegenwoordigen tussen het gietstuk en de met zand beklede laag, en de ijzeren mal en de met zand beklede laag. k1 is de verhouding tussen de thermische weerstand van het gietstuk en de thermische weerstand van de zandcoating; k2 is de verhouding tussen de thermische weerstand van het ijzertype en de thermische weerstand van de zandcoating. Gezien de combinatie van k1 en k2, met de verandering van de dikte van de zandcoating, zijn er de volgende drie verschillende situaties van warmteoverdracht tussen "gieten-zandcoaten-ijzeren mal" die feitelijk kunnen optreden:
- ① Wanneer k≤1 en k2≤1 ligt de zandcoatinglaag binnen de normale dikte en neemt de afkoelsnelheid van het gietstuk toe naarmate de dikte van de zandcoatinglaag afneemt.
- ②Wanneer de dikte van de met zand beklede laag een bepaalde dikte overschrijdt, heeft de ijzeren mal geen effect op de koeling van het gietstuk. Op dit moment is het gelijk aan gewoon zandgieten of harszandgieten. Omdat de thermische geleidbaarheid van de met zand beklede laag veel kleiner is dan die van het ijzertype, koelt het gietstuk langzaam af.
- ③Wanneer k≧1 en k2≧1 is de dikte van de zandcoating te dun, wat overeenkomt met het gieten van metalen mallen.
De bovengenoemde warmte-uitwisselingskarakteristieken zijn door experimenten bevestigd. Wanneer de dikte van de zandcoatinglaag van het ijzer-type zandgecoate gietstuk van de krukas (CTЦ-14) geleidelijk verandert van 4 naar 32 mm, wordt de hoeveelheid cementiet in de krukasstructuur voortdurend verminderd en wordt de hoeveelheid perliet en de De hoeveelheid ferriet blijft toenemen. Wanneer de dikte van de gezandstraalde laag kleiner is dan 4 mm, is de koelsterkte van het gietstuk vergelijkbaar met die van het metaaltype (dikke verf); wanneer de met zand beklede laag groter is dan 32 mm, is de koelsterkte gelijk aan die van gewoon harszandgieten.
Wanneer met ijzerzand bedekt gietwerk wordt gebruikt bij de productie van verschillende gietstukken, wordt door middel van experimenten of empirische analogie de dikte van de met zand bedekte laag en de dikte van het ijzer bepaald om de stollingssnelheid van het gietstuk te controleren. Bij het ontwerp van het 490Q nodulair gietijzeren krukasgietproces met zandcoating is de dikte van de zandcoatinglaag bijvoorbeeld 5-8 mm en de wanddikte van de ijzeren mal 20-30 mm, wat een hoge kwaliteit oplevert als -gegoten nodulair gietijzer zonder stootborden. De belangrijkste reden is:
- ① De met zand beklede laag regelt effectief de afkoelsnelheid van het gietstuk, enerzijds zorgt het ervoor dat het gietstuk er minder wit uitziet, en anderzijds is de afkoelsnelheid groter dan die bij zandgieten. Zoals weergegeven in figuur 2, daalt de temperatuur van het gietstuk na 930 minuten naar ongeveer 8°C wanneer het gesmolten ijzer in de met zand beklede ijzeren mal wordt gegoten, en duurt het 24 minuten voordat de zandmal naar dezelfde temperatuur is gedaald. en de koelsnelheid wordt ongeveer drie keer verhoogd. Als gevolg hiervan worden de mechanische eigenschappen van gietstukken aanzienlijk verbeterd.
- ②De ijzeren mal heeft geen concessie, maar de dunne zandcoating kan de krimpweerstand van de mal op passende wijze verminderen; en de stijfheid van de ijzeren mal maakt effectief gebruik van de grafitisatie-expansie van het nodulair gietijzer tijdens het stollingsproces om gieten zonder stijgbuis te bereiken; door de dunne zandcoating is de holte niet gemakkelijk te vervormen en is de precisie van het gietstuk aanzienlijk verbeterd dan die van de zandvorm.
Koelsnelheid van met ijzerzand beklede gietstukken
De factoren die de afkoelsnelheid van met ijzerzand beklede gietstukken beïnvloeden, zijn onder meer de dikte van de gietwand, het gietmateriaal, de giettemperatuur, de dikte van de zandcoating, het materiaal van de zandcoating, de dikte van de ijzeren mal, het materiaal van de ijzeren mal en de maltemperatuur. Hier wordt alleen de invloed van de gietwanddikte (bc), de dikte van de zandlaag (bm) en de ijzerdikte (bi) besproken.
De invloed van bc, bm en bi op gietkoeling
Verschillende gietwanddiktes (respectievelijk 10 mm, 20 mm, 40 mm, 80 mm), verschillende diktes van de zandcoating (respectievelijk 4 mm en 32 mm) en verschillende wanddiktes van het ijzertype (respectievelijk 32 mm en 8 mm), gemaakt onder de volgende experimentele omstandigheden. De invloed van de koelsnelheid van met zand beklede gietstukken van het ijzertype: de chemische samenstelling van het gietstuk is 3.52% C, 2.46% Si, 0.80% Mn, 0.18% P, 0.031% S, en de chemische samenstelling van de met zand beklede laag is: 90% kwartszand, 8% klei, steenkoolpoeder 2%, vocht 3%
- ①De wanddikte van het gietstuk, de dikte van de zandlaag en de wanddikte van ijzer beïnvloeden de koelsnelheid van het gietstuk. Daarom moeten bij de daadwerkelijke productie de geschikte dikte van de ijzeren mal en de dikte van de zandcoating worden geselecteerd op basis van verschillende gietwanddiktes om de vereiste koelsnelheid te verkrijgen.
- ② Gietstukken met verschillende diktes kunnen worden verkregen door de juiste dikte van de zandlaag en de ijzerwanddikte te selecteren om dezelfde koelsnelheid te verkrijgen. In figuur 3 betekent zone I bijvoorbeeld dat de dikte 10 mm en 20 mm is, zone II betekent 20 mm en 40 mm, en zone III betekent 40 mm. En de overlap tussen het koelbereik van 80 mm gietstukken.
- ③Hoewel bm en bi kunnen worden gewijzigd om dezelfde koelsnelheid te verkrijgen voor gietstukken van verschillende diktes, kunnen niet alle gietdiktes dezelfde koelsnelheid verkrijgen. Onder de experimentele omstandigheden kunnen gietstukken met een dikte van 10 mm en een dikte van 40 mm niet exact dezelfde koelsnelheid worden verkregen (er is geen overlap tussen de curven).
Selectie van zandlaagdikte (bm) en ijzeren wanddikte (bi)
Bm en bi worden doorgaans bepaald op basis van ervaring of experiment. Hier is een grafiekmethode die geschikt is voor gietdiktes (bc) van 10 tot 80 mm en een uitpaktemperatuur van 600 ℃. De ordinaat is de koeltijd. Op de abscis van de rechter curve is de dikte van de zandlaag aangegeven, die kan worden bepaald uit de tijd die het bekende gietstuk nodig heeft om af te koelen tot 600°C en de dikte van diverse gietstukken, en in de benodigde gietwanddikte (10, 20, 40, 80 mm) bekend is, dan is het erg handig om de dikte van de zandcoating en de dikte van de ijzeren mal te bepalen. Zoek de overeenkomstige bc (bijvoorbeeld bc=20 mm) vanaf de horizontale as van de linkerhelft van de curve en teken een horizontale lijn.
Als de twee lijnen elkaar kruisen binnen het bereik van de gearceerde curve, geeft dit aan dat dit gietstuk geschikt is voor gieten met ijzerzandcoating. Verleng deze horizontale lijn naar rechts, zodat deze zich uitstrekt tot in het gebied van bc=20 mm, en teken een verticale lijn naar beneden in dit gebied om de vereiste dikte van de zandlaag te verkrijgen. Deze verticale lijn moet echter zoveel mogelijk naar rechts worden getrokken om de kleinste dikte van de zandlaag en de dikte van de ijzeren mal te verkrijgen. Als de dikte van de te bepalen zandcoatinglaag niet binnen dit bereik ligt, kunt u deze op vergelijkbare wijze uit het aangrenzende curvebereik vinden.
- ①De wanddikte van het gietstuk, de dikte van de zandlaag en de wanddikte van ijzer beïnvloeden de koelsnelheid van het gietstuk. Daarom moeten bij de daadwerkelijke productie de geschikte dikte van de ijzeren mal en de dikte van de zandcoating worden geselecteerd op basis van verschillende gietwanddiktes om de vereiste koelsnelheid te verkrijgen.
- ② Gietstukken met verschillende diktes kunnen worden verkregen door de juiste dikte van de zandlaag en de ijzerwanddikte te selecteren om dezelfde koelsnelheid te verkrijgen. In figuur 3 betekent zone I bijvoorbeeld dat de dikte 10 mm en 20 mm is, zone II betekent 20 mm en 40 mm, en zone III betekent 40 mm. En de overlap tussen het koelbereik van 80 mm gietstukken.
- ③Hoewel bm en bi kunnen worden gewijzigd om dezelfde koelsnelheid te verkrijgen voor gietstukken van verschillende diktes, kunnen niet alle gietdiktes dezelfde koelsnelheid verkrijgen. Onder de experimentele omstandigheden kunnen gietstukken met een dikte van 10 mm en een dikte van 40 mm niet exact dezelfde koelsnelheid worden verkregen (er is geen overlap tussen de curven).
Bewaar de bron en het adres van dit artikel voor herdruk: De methode en toepassing van met zand beklede gietijzeren gietvorm
Minge Spuitgietbedrijf zijn toegewijd aan het vervaardigen en leveren van hoogwaardige en hoogwaardige gietstukken (het assortiment metalen spuitgietonderdelen omvat voornamelijk: Dunwandig spuitgieten,Hot Chamber Spuitgieten,Koude kamer spuitgieten),Ronde Service (Die Casting Service,CNC-bewerking,Matrijzen maken, Oppervlaktebehandeling). Elk aangepast aluminium spuitgieten, magnesium of Zamak / zink spuitgieten en andere gietstukken zijn welkom om contact met ons op te nemen.
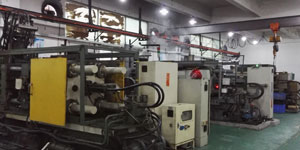
Onder controle van ISO9001 en TS 16949 worden alle processen uitgevoerd door honderden geavanceerde spuitgietmachines, 5-assige machines en andere faciliteiten, variërend van blasters tot Ultra Sonic-wasmachines. Minghe heeft niet alleen geavanceerde apparatuur, maar heeft ook professionele team van ervaren ingenieurs, operators en inspecteurs om het ontwerp van de klant waar te maken.
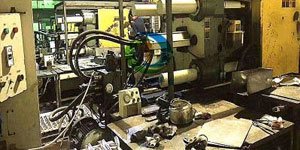
Contractfabrikant van spuitgietwerk. Mogelijkheden zijn onder meer koude kamer aluminium spuitgietonderdelen vanaf 0.15 lbs. tot 6 lbs., snelwissel instellen en machinaal bewerken. Diensten met toegevoegde waarde omvatten polijsten, trillen, ontbramen, stralen, schilderen, plateren, coaten, assembleren en bewerken. Materialen waarmee gewerkt is, zijn legeringen zoals 360, 380, 383 en 413.
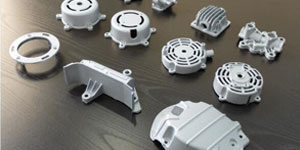
Hulp bij ontwerp van spuitgieten van zink/concurrent engineering. Custom fabrikant van precisie gegoten zink. Miniatuurgietstukken, hogedrukgietstukken, multi-slide gietstukken, conventionele gietstukken, eenheidsmatrijs en onafhankelijke spuitgietstukken en holteverzegelde gietstukken kunnen worden vervaardigd. Gietstukken kunnen worden vervaardigd in lengtes en breedtes tot 24 inch met een tolerantie van +/- 0.0005 inch.
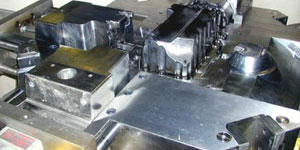
ISO 9001: 2015 gecertificeerde fabrikant van gegoten magnesium. Mogelijkheden zijn onder hoge druk spuitgieten van magnesium tot 200 ton hete kamer en 3000 ton koude kamer, gereedschapsontwerp, polijsten, gieten, machinale bewerking, poeder- en vloeistofverven, volledige QA met CMM-mogelijkheden , montage, verpakking & levering.
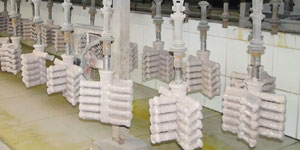
ITAF16949 gecertificeerd. Extra castingservice omvat: investering gieten,zandgieten,Zwaartekracht gieten, Verloren schuimafgietsel,Centrifugaal gieten,Vacuümgieten,Permanent vormgieten,. Mogelijkheden zijn onder meer EDI, technische assistentie, solide modellering en secundaire verwerking.
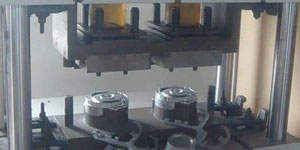
Gietindustrieën Casestudy's over onderdelen voor: auto's, fietsen, vliegtuigen, muziekinstrumenten, waterscooters, optische apparaten, sensoren, modellen, elektronische apparaten, behuizingen, klokken, machines, motoren, meubels, sieraden, mallen, telecom, verlichting, medische apparaten, fotografische apparaten, Robots, sculpturen, geluidsapparatuur, sportuitrusting, gereedschap, speelgoed en meer.
Wat kunnen we u hierna helpen doen?
∇ Ga naar de startpagina voor Spuitgieten China
→Gietonderdelen- Zoek uit wat we hebben gedaan.
→Gerangschikte tips over Spuitgietdiensten
By Minghe Die Casting Fabrikant: |Categorieën: Handige artikelen |Materiaal Tags: Aluminium gieten, Zink gieten, Magnesium gieten, Titanium gieten, Gieten van roestvrij staal, Messing gieten,Brons gieten,Video casten,Geschiedenis van ons bedrijf,Aluminium spuitgieten |Reacties uitgeschakeld