Drie redenen voor smeltlekkage tijdens de productie van mallen:
Vergeleken met gewone runner-mallen, is het poortsysteem in de hot runner-vorm altijd op hoge temperatuur tijdens gebruik, en de plastic smelt is geneigd te lekken bij de verbindingen van de onderdelen van het hot runner-systeem onder invloed van hoge temperatuur en hoge druk. Smeltlekkage heeft niet alleen invloed op de kwaliteit van plastic onderdelen, maar beschadigt ook de mal ernstig, waardoor de productie mislukt. Er zijn twee belangrijke lekkende delen van de hotrunner-vorm, het ene is het eindvlak van de runner op de runnerplaat en de andere is het verbindingsoppervlak van de runnerplaat en het mondstuk (inclusief het poortmondstuk en het hoofdrunnermondstuk) . Er zijn veel redenen voor smeltlekkage, die kunnen worden samengevat in drie aspecten: onjuiste werking, montageproces en onredelijk afdichtingsontwerp. Dit artikel introduceert de oorzaken van smeltlekkage en voorzorgsmaatregelen.
Smeltlekkage veroorzaakt door procesfactoren
Onjuiste bedrijfstechnologie is een van de belangrijkste redenen voor smeltlekkage tijdens de productie van matrijzen. Om de thermische uitzetting van de onderdelen van het hotrunner-systeem te compenseren, is er vaak een zekere koude spleet tussen de onderdelen bij het ontwerpen en assembleren van de matrijs. Alleen onder de gespecificeerde bedrijfstemperatuur kan de thermische uitzetting van de onderdelen de koude spleet volledig elimineren en afdichting en lekpreventie bereiken. Smeltlekkage veroorzaakt door onjuiste bediening treedt voornamelijk op in de volgende situaties:
- Smeltlekkage veroorzaakt door onjuist verwarmingsproces van het systeem of ongelijkmatige temperatuurregeling. Als tijdens het verwarmingsproces de verwarmingssnelheid van het mondstuk hoger is dan de verwarmingssnelheid van de hotrunner-plaat, zal de axiale thermische uitzetting van de systeemonderdelen de transversale thermische uitzetting van de hotrunner-plaat beperken, waardoor de hotrunner-plaat vervormt en smeltlekkage veroorzaken. De ongelijkmatige temperatuur van de onderdelen van het poortsysteem zal een ongelijkmatige uitzetting van de onderdelen veroorzaken en zal er ook voor zorgen dat de onderdelen vervormen en smeltlekkage veroorzaken.
- Injecteer vooraf wanneer het systeem de opgegeven bedrijfstemperatuur niet bereikt. Zoals getoond, nadat het systeem is verwarmd, ondergaan de steunring 6, de hotrunner-plaat 5 en het poortmondstuk 4 thermische uitzetting in de axiale richting en wordt de steunring samengedrukt op de vaste matrijsmontageplaat 3, en een bepaalde hoeveelheid warmte wordt gegenereerd tussen de hot runner plaat en het mondstuk. druk. Als de injectie wordt uitgevoerd wanneer de gespecificeerde temperatuur niet wordt bereikt, is de thermische druk die wordt gegenereerd door thermische uitzetting niet voldoende om de smeltdruk te compenseren, waardoor het mondstuk 4 en de hete spuitkanaalplaat 5 zullen scheiden en smeltlekkage zal veroorzaken.
- Smeltlekkage veroorzaakt doordat de verwarmingstemperatuur van het systeem hoger is dan de bedrijfstemperatuur. In dit geval wordt door de overmatige thermische uitzetting een grote thermische druk gegenereerd, waardoor de systeemonderdelen vervormen en smeltlekkage veroorzaken.
Aan de andere kant, wanneer de temperatuur van het poortsysteem wordt verlaagd tot de bedrijfstemperatuur, zal er ook smeltlekkage optreden als gevolg van het slechte aanpassingsvermogen van het thermische mondstuk met stijve randen aan thermische uitzetting.
Samenvattend is het werken volgens de juiste stappen en procescondities een voorwaarde om smeltlekkage te voorkomen. De algemene hotrunner-mal kan volgens de volgende stappen worden bediend:
- Verwarm het hotrunner systeem tot de ingestelde temperatuur. Het is over het algemeen verdeeld in twee stappen: De eerste is een zachte start om het vocht in de verwarmer te verwijderen.
- Verwarm de vorm tot de ingestelde temperatuur. Vooral bij grote matrijzen wordt het vóór het spuiten verwarmd en tijdens het spuiten gekoeld.
- Verwarm het vat van de injectiemachine tot de ingestelde temperatuur. De tweede stap is het verwarmen van het systeem tot de ingestelde temperatuur bij vollast. De temperatuur van het mondstuk kan worden verwarmd tot 2/3 van de temperatuur van de hotrunner-plaat. Nadat de temperatuur van de hotrunner-plaat de ontwerptemperatuur heeft bereikt, wordt de temperatuur van het mondstuk verwarmd tot de ingestelde temperatuur.
- Voor het nieuwe of gereinigde hotrunner-systeem moet eerst langzame lagedrukinjectie worden gebruikt.
- Als er na meerdere injectiecycli geen smeltlekkage is, worden de ingestelde parameters van het injectieproces gebruikt voor productie.
Afdichtingsontwerp van hot runner-systeem
Thermische uitzettingscompensatie van hot runner-systeem
De bij kamertemperatuur geassembleerde mal zorgt ervoor dat de relatieve positie van de onderdelen verandert tijdens de thermische uitzetting van de onderdelen van het hotrunner-systeem. Om de thermische uitzetting van de onderdelen te compenseren, is het noodzakelijk om een geschikte uitzettingsvoeg te laten, zoals de koude spleet A en C getoond. Het wordt vastgezet op het vaste sjabloon 1 door middel van de centreerpen 7 en rekt rond nadat het is verwarmd. De transversale thermische uitzetting van de hotrunner-plaat zal de opening A tussen de hotrunner-plaat en de anti-rotatiepen 2 verkleinen. Als de waarde A kleiner is dan de transversale thermische uitzetting van de hotrunner-plaat in het ontwerp, zal de anti- rotatiepen voorkomt de dwarsuitstrekking van de hotrunner-plaat na verwarming.
Het veroorzaakt kromtrekken en vervorming van de hotrunner-plaat, waardoor de afdichting tussen de hotrunner-plaat en het mondstuk ondoeltreffend wordt en er smeltlekkage ontstaat. De axiale thermische uitzetting van de steunring 6, de hot runner-plaat 5 en het poortmondstuk 4 zal de koude spleet C elimineren. Als de koude spleet te groot is en de axiale thermische uitzetting onvoldoende is, zal de smeltdruk tijdens injectie veroorzaken het poortmondstuk 4 en de hete runner De plaat 5 is gescheiden en de smelt lekt. Als de koude spleet te klein is en de thermische uitzettingsdruk van het systeem te groot is, zullen de systeemdelen worden gebogen of zal de drukspanning de vloeispanning van de vaste sjabloon overschrijden, waardoor de steunring de vaste zal verpletteren sjabloon, waardoor de laterale thermische uitzetting van de hotrunner-plaat wordt beperkt en de poort wordt veroorzaakt. Er is smeltlekkage opgetreden tussen het mondstuk en de hotrunner-plaat.
Daarom zijn het correct berekenen van de thermische uitzetting van het systeem en het vrijlaten van een redelijke thermische uitzettingsvoeg bij het ontwerpen van de matrijs de voorwaarden om smeltlekkage te voorkomen. De lineaire thermische uitzetting van het systeem kan worden berekend met de volgende formule: L=TL (1) De thermische spanning veroorzaakt door de weerstand van de thermische uitzetting van het systeem is: =EL-CL (2) De druk van de vaste vaste plaat wordt gecontroleerd met de volgende formule p(3) waarbij: L de lineaire thermische uitzetting is van het hotrunner-systeem, mm; is de lineaire thermische uitzettingscoëfficiënt van het materiaal van de systeemonderdelen; T is het temperatuurverschil tussen de onderdelen van het hotrunner-systeem en de mal; L is de lengte van de onderdelen van het runnersysteem in de expansierichting bij kamertemperatuur, mm; is de thermische uitzetting van het systeem. De thermische spanning veroorzaakt door weerstand, MPa; C is de hoeveelheid gereserveerde opening, mm; E is de elasticiteitsmodulus van de systeemdelen, MPa; p is de toelaatbare drukspanning van het materiaal van de vaste vormplaat.
De afdichtingsvorm van het hotrunner-systeem
De vlakke afdichting tussen de hotrunnerplaat en het mondstuk is een gebruikelijke afdichtingsvorm in buitenlandse hotrunnersystemen. Nadat het systeem thermisch in axiale richting is uitgezet, wordt de steunring op de vaste vormplaat gedrukt en wordt een bepaalde thermische druk gegenereerd op het verbindingsvlak van de hete runnerplaat en het mondstuk om de smeltdruk te compenseren om af te dichten en te voorkomen lekkage. Dit type structuur kan geen koude afdichting garanderen en er is geen bescherming tegen oververhitting. Alleen onder de ingestelde temperatuuromstandigheden kunnen de hotrunner-plaat en het mondstuk worden afgedicht. Bij het ontwerpen is het noodzakelijk om de thermische uitzetting nauwkeurig te berekenen en een geschikte koude spleet C te laten.
B. O-vormige afdichtring wordt gebruikt op het verbindingsvlak van mondstuk en hotrunner-plaat. O-vormige afdichtring is gemaakt van roestvrij stalen buis. Bij de montage is er een voorbelasting van 2030 stalen buisdiameter om smeltlekkage te voorkomen. Deze structuur is zeer geschikt voor hotrunner-platen en -mallen met een lage stijfheid.
De elastische verbinding wordt aangenomen en de veer zorgt voor voorspanning om de afdichting in de koeltoestand te realiseren. Bij oververhitting absorbeert de veer thermische uitzetting om systeemschade en lekkage te voorkomen. Het is een ideale verzegelingsvorm.
Het poortmondstuk is met schroefdraad op de hotrunner-plaat bevestigd en het mondstuk en de glijdende drukring bewegen met de hotrunner-plaat wanneer het systeem thermisch uitzet. Aangezien de beweging van het mondstuk een verkeerde uitlijning van de mondstukgeleideras en de poortas op de vaste sjabloon veroorzaakt, moet bij het ontwerpen van de mondstukpositie rekening worden gehouden met laterale thermische uitzetting. Dit type afdichting is geschikt voor gelegenheden met weinig injectiepunten en kleine mondstukafstanden.
Het montageproces van de hotrunnerplaat
De montagenauwkeurigheid en installatievolgorde van het hotrunner-systeem houden rechtstreeks verband met het feit of de smelt lekt. Als de mondstukhoogte niet consistent is, zal de opening tussen het kortste mondstuk en de hotrunner-plaat smeltlekkage veroorzaken, en de vervorming van de hotrunner-plaat veroorzaakt door de inconsistente hoogte van het steunkussen en de mondstukhoogte zal ook smeltlekkage veroorzaken.
Het volgende neemt een 1-vorm 4-holtes plastic hotrunner-vorm als voorbeeld om het assemblageproces van de hotrunner-plaat te illustreren:
- Bevestig de vormbevestigingsplaat stevig.
- Druk het runnerblok 7 in de hotrunnerplaat 10, installeer de antirotatiepen 2 na het corrigeren van de richting en druk vervolgens op het blok met de compressieschroef 3 en gebruik de O-vormige metalen afdichtring om te voorkomen dat de smelt lekt.
- Installeer het poortmondstuk 1 en het steunkussen 15 in het vaste sjabloon 14 en controleer of de hoogte van alle montagevlakken van het mondstuk hetzelfde is op basis van het vaste sjabloonvlak. Als ze niet consistent zijn, slijp dan met de minimumwaarde, met een tolerantie van 0.01 mm.
- Probeer de hotrunnerplaat te installeren en controleer of de hotrunnerplaat en de antirotatiepen 2 de nodige spelingen A en B hebben in radiale en axiale richting.
- Bevestig het achterplaatframe 12 op de vaste sjabloon 14 met bouten.
- Repareer op basis van het bovenvlak van het steunframe 12 alle drukringen 6 om ze consistent in hoogte te maken en een opening te hebben met het bovenvlak van het steunframe. C.
- Schroef het hoofdkanaalmondstuk 9 in de hotrunnerplaat 10.
Bewaar de bron en het adres van dit artikel voor herdruk:Drie redenen voor smeltlekkage tijdens de productie van mallen:
Minge Spuitgietbedrijf zijn toegewijd aan het vervaardigen en leveren van hoogwaardige en hoogwaardige gietstukken (het assortiment metalen spuitgietonderdelen omvat voornamelijk: Dunwandig spuitgieten,Hot Chamber Spuitgieten,Koude kamer spuitgieten),Ronde Service (Die Casting Service,CNC-bewerking,Matrijzen maken, Oppervlaktebehandeling). Elk aangepast aluminium spuitgieten, magnesium of Zamak / zink spuitgieten en andere gietstukken zijn welkom om contact met ons op te nemen.
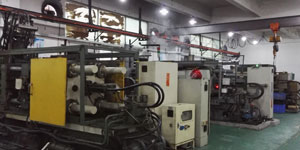
Onder controle van ISO9001 en TS 16949 worden alle processen uitgevoerd door honderden geavanceerde spuitgietmachines, 5-assige machines en andere faciliteiten, variërend van blasters tot Ultra Sonic-wasmachines. Minghe heeft niet alleen geavanceerde apparatuur, maar heeft ook professionele team van ervaren ingenieurs, operators en inspecteurs om het ontwerp van de klant waar te maken.
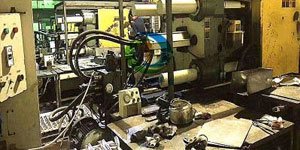
Contractfabrikant van spuitgietwerk. Mogelijkheden zijn onder meer koude kamer aluminium spuitgietonderdelen vanaf 0.15 lbs. tot 6 lbs., snelwissel instellen en machinaal bewerken. Diensten met toegevoegde waarde omvatten polijsten, trillen, ontbramen, stralen, schilderen, plateren, coaten, assembleren en bewerken. Materialen waarmee gewerkt is, zijn legeringen zoals 360, 380, 383 en 413.
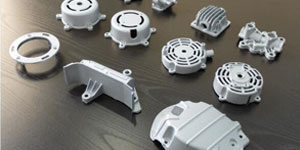
Hulp bij ontwerp van spuitgieten van zink/concurrent engineering. Custom fabrikant van precisie gegoten zink. Miniatuurgietstukken, hogedrukgietstukken, multi-slide gietstukken, conventionele gietstukken, eenheidsmatrijs en onafhankelijke spuitgietstukken en holteverzegelde gietstukken kunnen worden vervaardigd. Gietstukken kunnen worden vervaardigd in lengtes en breedtes tot 24 inch met een tolerantie van +/- 0.0005 inch.
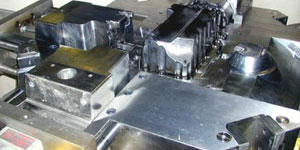
ISO 9001: 2015 gecertificeerde fabrikant van gegoten magnesium. Mogelijkheden zijn onder hoge druk spuitgieten van magnesium tot 200 ton hete kamer en 3000 ton koude kamer, gereedschapsontwerp, polijsten, gieten, machinale bewerking, poeder- en vloeistofverven, volledige QA met CMM-mogelijkheden , montage, verpakking & levering.
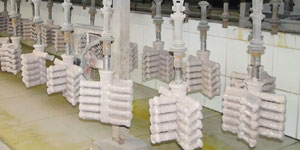
ITAF16949 gecertificeerd. Extra castingservice omvat: investering gieten,zandgieten,Zwaartekracht gieten, Verloren schuimafgietsel,Centrifugaal gieten,Vacuümgieten,Permanent vormgieten,. Mogelijkheden zijn onder meer EDI, technische assistentie, solide modellering en secundaire verwerking.
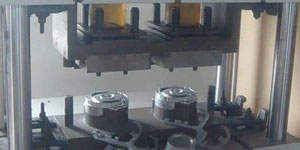
Gietindustrieën Casestudy's over onderdelen voor: auto's, fietsen, vliegtuigen, muziekinstrumenten, waterscooters, optische apparaten, sensoren, modellen, elektronische apparaten, behuizingen, klokken, machines, motoren, meubels, sieraden, mallen, telecom, verlichting, medische apparaten, fotografische apparaten, Robots, sculpturen, geluidsapparatuur, sportuitrusting, gereedschap, speelgoed en meer.
Wat kunnen we u hierna helpen doen?
∇ Ga naar de startpagina voor Spuitgieten China
→Gietonderdelen- Zoek uit wat we hebben gedaan.
→Gerangschikte tips over Spuitgietdiensten
By Minghe Die Casting Fabrikant: |Categorieën: Handige artikelen |Materiaal Tags: Aluminium gieten, Zink gieten, Magnesium gieten, Titanium gieten, Gieten van roestvrij staal, Messing gieten,Brons gieten,Video casten,Geschiedenis van ons bedrijf,Aluminium spuitgieten |Reacties uitgeschakeld