De atmosfeercontrole tijdens het sinterproces van gesinterd staal en zijn prestaties
Sinteratmosfeer en zijn selectie
Als alleen het sinteren van koolstofhoudend staal wordt overwogen, is de sinteratmosfeer die in de poedermetallurgie-industrie wordt gebruikt waterstof, stikstof, stikstof + waterstof (koolstofpotentieel of geen koolstofpotentieel), ontleding van ammoniak, endotherm gas, endotherm gas + stikstof, synthese Voor gas en vacuüm vereist de juiste selectie van sinteratmosfeer inzicht in de kenmerken en prestaties van verschillende sinteratmosferen en selectie in overeenstemming met de principes van het waarborgen van kwaliteit en het verlagen van kosten.
Waterstof is een sterk reducerende atmosfeer. Veel mensen geloven dat waterstof een zeker ontkolend effect heeft, maar dit hangt grotendeels af van de zuiverheid van de gebruikte waterstof en niet van de waterstof zelf. Over het algemeen bevat de waterstof na elektrolyse of katalytische omzetting een bepaalde hoeveelheid onzuiverheidsgas, zoals H2, O2, CO en CH4, enz., Soms kan de totale hoeveelheid ongeveer 0.5% bereiken. Daarom is het het beste om het voor gebruik te drogen en te zuiveren om het zuurstofgehalte en het dauwpunt te verlagen. Vanwege de hoge prijs van waterstof wordt pure waterstof echter zelden gebruikt als sinteratmosfeer, tenzij er speciale redenen zijn.
Stikstof is een veilig en goedkoop inert gas, maar omdat pure stikstof niet reduceerbaar is bij de sintertemperatuur, wordt pure stikstof zelden gebruikt als sinteratmosfeer bij de productie van traditioneel poedermetallurgiestaal. In de afgelopen jaren, aangezien de kosten van stikstofzuivering zijn afgenomen en de luchtdichtheid van de sinteroven is verbeterd, is stikstof ook begonnen te worden gebruikt als een sinteratmosfeer voor het sinteren van koolstofhoudend staal.
De laatste jaren wordt het stikstof-waterstofmengsel steeds vaker gebruikt bij het sinteren van koolstofstaal. Stikstof/waterstof wordt meestal gebruikt tussen 95/5-50/50. Dit mengsel heeft een zekere mate van reduceerbaarheid en het dauwpunt kan lager zijn dan -60 ℃, in het algemeen moet een bepaalde hoeveelheid CH4 of C3H8 worden toegevoegd om een bepaald koolstofpotentieel te behouden bij gebruik van dit gas bij 1050-1150 ℃, tijdens het sinteren koolstofstaal boven 1250℃ hoeft het koolstofpotentieel niet te beheersen. Dit mengsel kan worden gebruikt om chroomhoudende legeringen op ijzerbasis beneden 1120°C te sinteren zonder oxidatie.
Ontbonden ammoniak wordt gemaakt door ammoniakgas te ontleden via een verwarmde katalysator, waaronder 75% H2 en 25% N2. Maar over het algemeen blijft er altijd een kleine hoeveelheid niet-afgebroken ammoniakmoleculen in de afgebroken ammoniak. Wanneer ze bij hoge temperaturen in contact komen met ruwijzer, zullen ze uiteenvallen in zeer actieve waterstof- en stikstofatomen, waardoor het metaal wordt genitreerd. Recente onderzoeken hebben aangetoond dat, indien goed gecontroleerd, het sinteren van AstaloyCrM bij 1120°C het 90N2/10H2-mengsel zal ontleden en met een sterkere reduceerbaarheid zal ammoniak vormen. De belangrijkste reden is dat deze actieve waterstofatomen die net zijn afgebroken tijdens het sinterproces effectiever zijn dan 90N2 / De waterstof in het 10H2 menggas heeft een sterkere reduceerbaarheid en kan de oxidelaag buiten de AstaloyCrM-deeltjes effectief verminderen. Om de ammoniak te zuiveren en af te breken, kunt u deze door water leiden en drogen, of geactiveerd aluminiumoxide of een moleculaire zeef gebruiken om de resterende ammoniak te verwijderen.
Endotherm gas is een soort gemengd gas dat wordt verkregen door koolwaterstofgas (CH4 of C3H8) in een bepaalde verhouding te mengen met lucht, voor te verwarmen op 900-1000 ° C en katalytisch om te zetten door middel van een nikkeloxidekatalysator. Afhankelijk van de verhouding lucht tot steenkoolgas gaat het omzettingsproces gepaard met endotherme of exotherme reacties. Het resulterende gemengde gas wordt endotherm gas of exotherm gas genoemd en de reactie kan als volgt zijn:
CmHn+m(O2+3.774N2)—mCO+n/H2+1.887mN2
Als de bovenstaande reactie volledig moet worden uitgevoerd, dat wil zeggen dat alle C in CmHm zojuist heeft gereageerd met O2 in de lucht, moet de vereiste lucht/gas m/2 (1+3.774) zijn, wat 2.387 m is. Als het gebruikte koolwaterstofgas bijvoorbeeld CH4 is, moet de vereiste lucht/gas 2.387 zijn, en het op dat moment geproduceerde gemengde gas bevat 40.9% H2, 38.6% N2 en 20.5% CO. Na de reactie bevat het gemengde gas H2 Het gehalte aan CO en CO neemt af met de toename van lucht/gas, maar het gehalte aan H2O en CO2 neemt toe. Het laat ook zien dat het koolstofpotentieel in het gemengde gas na de reactie afneemt met de toename van lucht/gas, en dat de oxidatieprestaties toenemen. Dit is ook de belangrijkste reden waarom exotherm gas zelden wordt gebruikt bij het sinteren van koolstofhoudend staal en het meeste endotherme gas wordt gebruikt.
Over het algemeen wordt het gemengde gas geproduceerd door lucht/gas tussen 2.0-3.0 genoemd absorptie Heet gas, en het gemengde gas dat wordt geproduceerd wanneer de verhouding groter is dan 5.0 wordt exotherm gas genoemd. De relatie tussen het dauwpunt van het endotherme gas geproduceerd met CH4 als grondstof en lucht/gas laat zien dat de lucht/gas slechts stijgt van 2.4 naar 2.5, en het dauwpunt van het geproduceerde menggas stijgt van -25°C naar boven 0°C. Daarom moeten gebruikers, als gebruikers zelf endotherm gas produceren, speciale aandacht besteden aan het beheersen van de verhouding van lucht tot gas in de grondstoffen (bij voorkeur niet meer dan 2.4) om endotherm gas met een voldoende laag dauwpunt te verkrijgen. In het gemengde gas na de reactie komt de verhouding van de verschillende gassen overeen met de verhouding aan het einde van de reactie, die in het algemeen (1000-1100°C) is.
Na de reactie, als de temperatuur van het gas verandert, zullen het koolstofpotentieel van het gemengde gas, het dauwpunt en de verhouding van verschillende gassen veranderen. Veel poedermetallurgiefabrikanten gebruiken één exotherme gasgenerator om de vereiste sinteratmosfeer voor meerdere sinterovens tegelijkertijd door de pijpleiding te leveren. De temperatuur van de atmosfeer is verlaagd voordat deze de sinteroven bereikt. . Als de isolatie van de pijpleiding niet goed is en de temperatuur van de pijpleidingwand lager is dan 800 ° C, zal een deel van de koolstof in het gemengde gas zich op de pijpleidingwand afzetten in de vorm van roet. Met andere woorden, wanneer het gemengde gas opnieuw wordt verwarmd tot de sintertemperatuur in de sinteroven, is zijn koolstofwarmte veel lager dan de koolstofpotentiaal die de endotherme gasgenerator kan leveren.
In dit geval moet een geschikte hoeveelheid methaan of propaan aan de sinteroven worden toegevoegd om het koolstofpotentieel in de oven te waarborgen. Nu zijn sommige buitenlandse poedermetallurgiefabrikanten begonnen met het installeren van een kleine endotherme gasgenerator naast elke sinteroven, en gebruiken het endotherme gas dat zojuist is geproduceerd rechtstreeks in de sinteroven zonder koeling, om te voorkomen dat de sinteratmosfeer wordt beïnvloed door temperatuurveranderingen . . Een ander punt om eraan te herinneren is dat zelfs met het katalytische effect van de nikkeloxidekatalysator, een kleine hoeveelheid koolwaterstofgas (CH4 of C3H8, enz.) in het na het transport verkregen menggas achterblijft. Bovendien zal tussen de gassen bij 900-1100 ℃ Nadat de reactie een evenwicht heeft bereikt, een kleine hoeveelheid CO2 en H2O (gasvormig) worden geproduceerd, die voor gebruik moeten worden gedroogd.
De toevoeging van stikstof aan het endotherme gas kan het relatieve gehalte aan CO, CO2 en H2O in het endotherme gas verminderen, om de gevoeligheid van de atmosfeer voor koolstofpotentiaal en dauwpunt te bufferen, en sommige correlatiecoëfficiënten in de sinteratmosfeer gemakkelijker te maken te beheersen.
Synthetisch gas is een methode die de afgelopen jaren door buitenlandse fabrikanten van sinterovens is voorgesteld om direct (verdund) endotherm gas in de sinteroven te genereren (zonder dat een endotherm gasgenerator buiten de oven nodig is). Het mengt gasvormige methylalcohol en stikstof in een bepaalde verhouding en leidt het vervolgens rechtstreeks naar de sinteroven. De volgende reacties zullen optreden in de sinterzone bij hoge temperatuur:
CH3OH—CO+2H2
Omdat de verhouding van CO en H2 in het ontbonden gas gelijk is aan de verhouding van het endotherme gas geproduceerd door de gebruikelijke methode met CH4, en de gemengde stikstof kan worden gecombineerd om een gemengde atmosfeer te synthetiseren met dezelfde samenstelling als het endotherme gas (1L Het methaan komt overeen met 1.05nm3 stikstof). Het grootste voordeel is dat er geen endotherme gasgenerator buiten de oven nodig is. Bovendien kunnen gebruikers naar eigen behoefte verschillende hoeveelheden stikstofgas mengen om verdund endotherm gas te produceren.
Vacuüm is ook een soort sinteratmosfeer, die meestal wordt gebruikt voor het sinteren van roestvrij staal en andere materialen, maar niet vaak wordt gebruikt voor het sinteren van koolstofstaal.
Fysische eigenschappen van sinteratmosfeer
De meeste artikelen en rapporten over sinteratmosfeer bespreken voornamelijk het chemische gedrag tussen verschillende sinteratmosferen en het sinterlichaam tijdens het sinterproces, maar bespreken zelden de invloed van de fysieke eigenschappen van verschillende atmosferen op sinteren, hoewel dit effect in veel gevallen niet kan. genegeerd worden. Het verschil in gasviscositeit zal bijvoorbeeld de chemische concentratiegradiënt van het gesinterde lichaam van het oppervlak naar de binnenkant langs de opening veroorzaken, waardoor de oppervlakte-eigenschappen van het gesinterde lichaam worden beïnvloed. Een ander voorbeeld is dat de warmtecapaciteit en thermische geleidbaarheid van verschillende gassen een grote invloed hebben op de sintertijd en afkoelsnelheid. Deze sectie geeft een overzicht van de belangrijkste fysieke eigenschappen van sommige sinteratmosferen bij verschillende temperaturen (rond de sintertemperatuur) ter referentie van de lezers.
Voorbeelden van problemen met betrekking tot de atmosfeer tijdens sinteren
1 Voorbeelden van barsten op het oppervlak van onderdelen tijdens het ontparaffineren
Wanneer een sinteroven met gaasband wordt gebruikt en endotherm gas wordt gebruikt als de sinteratmosfeer, zullen, als de temperatuurstijging en de atmosfeer in de ontparaffineringszone niet goed worden gecontroleerd, oppervlaktescheuren optreden. Veel mensen denken dat dit fenomeen te wijten is aan de snelle afbraak van het smeermiddel. Het wordt veroorzaakt, maar het is niet het geval. De echte reden is dat het koolmonoxide in het endotherme gas wordt afgebroken tot vaste koolstof en kooldioxide in het temperatuurbereik van 450-700 ℃ onder de katalyse van ijzer, nikkel en andere metalen. Het is de nieuw afgezette vaste koolstof in de poriën van het gesinterde lichaam die het volume ervan vergroot en het bovengenoemde fenomeen van oppervlaktescheuren veroorzaakt.
De kwaliteit van de onderdelen varieert met de temperatuur tijdens het sinterproces in verschillende atmosferen. Hiervan is atmosfeer 3 droog endotherm steenkoolgas, en atmosfeer 4 en 5 zijn endotherm steenkoolgas waaraan verschillende hoeveelheden waterdamp zijn toegevoegd. Het is te zien dat tijdens het sinterproces de kwaliteit van de onderdelen begint af te nemen bij ongeveer 200°C, wat betekent dat het vaste smeermiddel erin continu wordt afgebroken en over het sinterlichaam stroomt, waardoor de kwaliteit afneemt. Als er geen vast smeermiddel in het gemengde poeder zit, bestaat het bovenstaande fenomeen natuurlijk niet. Als de bovengenoemde drie atmosferen worden gebruikt, hoe droger de atmosfeer van de kwaliteit van het gesinterde lichaam bij ongeveer 450°C, hoe ernstiger dit fenomeen zal zijn.
Maar wat interessant is, is dat wanneer gas 3 (droog endotherm gas) wordt gebruikt, oppervlaktescheuren optreden ongeacht de aanwezigheid van vaste smeermiddelen, wat aangeeft dat het niet direct gerelateerd is aan ontparaffinering, en koolstofrijk gas wordt gevonden in de scheuren. Fenomeen, we kunnen de juistheid van bovenstaande uitleg bevestigen.
Er zijn verschillende manieren om het optreden van het bovengenoemde scheurverschijnsel te voorkomen. Het meest directe is om de sinteratmosfeer te veranderen van endotherm gas naar waterstof-stikstofmengsel zonder gebroken lijnen te kraken. Als de sinteratmosfeer niet kan worden veranderd, zijn er twee methoden. Een daarvan is het blazen van een deel van het endotherme gas dat waterdamp bevat in de ontparaffineringszone van de sinteroven. Het is echter moeilijk om met deze methode een stabiele besturing te verkrijgen in de praktijk.
De luchtstroomregeling van de sinteroven is niet goed, en het fenomeen van een hoge dauwpuntatmosfeer die de sinterzone binnenkomt, kan de sinterkwaliteit beïnvloeden. De tweede en beste methode is om de verwarmingssnelheid van de onderdelen in de ontparaffineringszone van de sinteroven te verhogen om deze zo snel mogelijk door 450 te laten gaan. In het gebied waar scheurvorming optreedt bij -600°C, is het zogenaamde snelle ontparaffineren meestal bedoeld voor dit fenomeen.
2 AstaloyCrM-sintervoorbeeld
Metaalchroom wordt veel gebruikt in gelegeerd staal vanwege de lage prijs en het goede versterkende effect. Chroomhoudend gesinterd staal zal echter veel problemen tegenkomen in het productieproces. Een daarvan is de productie van chroomhoudend ijzerpoeder, dat een strikt vernevelings- en gloeireductieproces moet ondergaan om grondstofpoeder met een lager zuurstof- en koolstofgehalte te verkrijgen. .
Honganas AB uit Zweden is momenteel de enige fabrikant ter wereld die dit grondstofpoeder tegen lage kosten kan produceren. De tweede is dat zelfs als chroomhoudend ijzerpoeder van hoge kwaliteit kan worden verkregen, als de sinter- en mediumtemperatuur, met name de sinteratmosfeer, niet goed kunnen worden gecontroleerd, de kans groter is dat deze tijdens het sinteren en oxideren wordt geoxideerd, en de sinterprestaties worden verminderd.
Thermodynamische berekeningen en een groot aantal experimenten hebben aangetoond dat als het endotherme gas wordt gebruikt als de sinteratmosfeer van AsaloyCrM, niet aan de sintervereisten kan worden voldaan, zelfs als het dauwpunt erg laag is.
Met andere woorden, voor het sinteren van AsaloyCrM kan alleen zuiver waterstof of waterstof-stikstofmengsel worden gebruikt. Momenteel worden de meeste van de laatste gebruikt. , Het aandeel waterstof is goed voor 5%-20%. De lezer moet er niet alleen aan worden herinnerd om de samenstelling van de sinteratmosfeer te waarborgen, maar ook om de kwaliteit van de sinteratmosfeer te waarborgen.
De zogenaamde kwaliteit verwijst hier naar de mate van oxidatie in de sinteratmosfeer, die in het algemeen wordt gekalibreerd door de partiële zuurstofdruk in de atmosfeer. Bij sinteren bij 1120 ℃, als de partiële zuurstofdruk in de atmosfeer lager is dan 1 × 10-14 Pa, zal er geen oxidatie optreden tijdens het sinterproces.
Wanneer de temperatuur wordt verlaagd, om oxidatie te voorkomen, moet de partiële zuurstofdruk in de atmosfeer zelfs laag zijn. Het kan er ook voor zorgen dat AsaloyCrM gesinterd bij 1125 ℃ niet zal oxideren bij 1 × 10-14 Pa. De bovenstaande berekening is bevestigd door experimentele gegevens.
Bewaar de bron en het adres van dit artikel voor herdruk: De atmosfeercontrole tijdens het sinterproces van gesinterd staal en zijn prestaties
Minge Spuitgietbedrijf zijn toegewijd aan het vervaardigen en leveren van hoogwaardige en hoogwaardige gietstukken (het assortiment metalen spuitgietonderdelen omvat voornamelijk: Dunwandig spuitgieten,Hot Chamber Spuitgieten,Koude kamer spuitgieten),Ronde Service (Die Casting Service,CNC-bewerking,Matrijzen maken, Oppervlaktebehandeling). Elk aangepast aluminium spuitgieten, magnesium of Zamak / zink spuitgieten en andere gietstukken zijn welkom om contact met ons op te nemen.
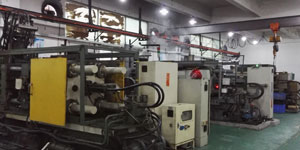
Onder controle van ISO9001 en TS 16949 worden alle processen uitgevoerd door honderden geavanceerde spuitgietmachines, 5-assige machines en andere faciliteiten, variërend van blasters tot Ultra Sonic-wasmachines. Minghe heeft niet alleen geavanceerde apparatuur, maar heeft ook professionele team van ervaren ingenieurs, operators en inspecteurs om het ontwerp van de klant waar te maken.
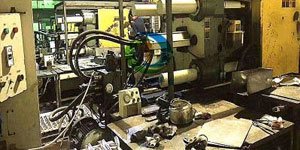
Contractfabrikant van spuitgietwerk. Mogelijkheden zijn onder meer koude kamer aluminium spuitgietonderdelen vanaf 0.15 lbs. tot 6 lbs., snelwissel instellen en machinaal bewerken. Diensten met toegevoegde waarde omvatten polijsten, trillen, ontbramen, stralen, schilderen, plateren, coaten, assembleren en bewerken. Materialen waarmee gewerkt is, zijn legeringen zoals 360, 380, 383 en 413.
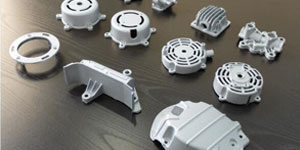
Hulp bij ontwerp van spuitgieten van zink/concurrent engineering. Custom fabrikant van precisie gegoten zink. Miniatuurgietstukken, hogedrukgietstukken, multi-slide gietstukken, conventionele gietstukken, eenheidsmatrijs en onafhankelijke spuitgietstukken en holteverzegelde gietstukken kunnen worden vervaardigd. Gietstukken kunnen worden vervaardigd in lengtes en breedtes tot 24 inch met een tolerantie van +/- 0.0005 inch.
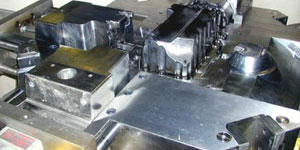
ISO 9001: 2015 gecertificeerde fabrikant van gegoten magnesium. Mogelijkheden zijn onder hoge druk spuitgieten van magnesium tot 200 ton hete kamer en 3000 ton koude kamer, gereedschapsontwerp, polijsten, gieten, machinale bewerking, poeder- en vloeistofverven, volledige QA met CMM-mogelijkheden , montage, verpakking & levering.
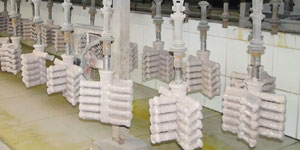
ITAF16949 gecertificeerd. Extra castingservice omvat: investering gieten,zandgieten,Zwaartekracht gieten, Verloren schuimafgietsel,Centrifugaal gieten,Vacuümgieten,Permanent vormgieten,. Mogelijkheden zijn onder meer EDI, technische assistentie, solide modellering en secundaire verwerking.
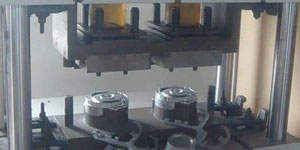
Gietindustrieën Casestudy's over onderdelen voor: auto's, fietsen, vliegtuigen, muziekinstrumenten, waterscooters, optische apparaten, sensoren, modellen, elektronische apparaten, behuizingen, klokken, machines, motoren, meubels, sieraden, mallen, telecom, verlichting, medische apparaten, fotografische apparaten, Robots, sculpturen, geluidsapparatuur, sportuitrusting, gereedschap, speelgoed en meer.
Wat kunnen we u hierna helpen doen?
∇ Ga naar de startpagina voor Spuitgieten China
→Gietonderdelen- Zoek uit wat we hebben gedaan.
→Gerangschikte tips over Spuitgietdiensten
By Minghe Die Casting Fabrikant: |Categorieën: Handige artikelen |Materiaal Tags: Aluminium gieten, Zink gieten, Magnesium gieten, Titanium gieten, Gieten van roestvrij staal, Messing gieten,Brons gieten,Video casten,Geschiedenis van ons bedrijf,Aluminium spuitgieten |Reacties uitgeschakeld