De procesbeheersing van vermiculaire ijzerproductie
In vergelijking met grijs ijzer wordt de treksterkte van vermiculair ijzer met ten minste 70% verhoogd, de elasticiteitsmodulus met 35% verhoogd en de vermoeiingssterkte bijna verdubbeld. In vergelijking met een aluminiumlegering zijn de sterkte en stijfheid van vermiculair ijzer twee keer zo hoog en is de vermoeiingssterkte twee keer zo hoog. Deze eigenschappen van vermiculair ijzer bieden de motor de mogelijkheid om de verhouding vermogen/gewicht te verbeteren en de cilinderdruk te verhogen. Het verhogen van de cilinderdruk is de sleutel tot optimale prestaties van de volgende generatie dieselmotor met directe injectie. Om tegemoet te komen aan de wijdverspreide toepassing van vermiculair ijzer, bereidt de gieterij-industrie zich momenteel actief voor, investeert zwaar en herbouwt nieuwe processen om de productie van vermiculair ijzer stabiel en betrouwbaar te maken.
Voor vermiculair ijzermotoren van prototype tot massaproductie is kwaliteitsrisico de doorslaggevende factor. Voor vermiculair ijzer van hoge kwaliteit is de stabiele zone erg klein, alleen in het bereik van 0.008% magnesiumgehalte. Een spoorhoeveelheid, zoals een verlies van 0.001% magnesium, zal vlokgrafiet produceren, waardoor de mechanische eigenschappen met 25% tot 40% zullen afnemen. Dit artikel beschrijft een procesbesturingssysteem op basis van thermische analysemethoden. Het systeem meet het magnesiumverlies en past online de toestand van gesmolten ijzer aan om de vorming van grafietschilfers te voorkomen. Deze online controlemethode van meten en afstellen vermindert de vluchtigheid in het proces van het produceren van vermiculair ijzer tot het laagste punt en elimineert fundamenteel het kwaliteitsrisico dat wordt veroorzaakt door de productie van vermiculair ijzer.
De vraag naar een hoog vermogen, een hoog koppel, lage uitlaatemissies en een lager brandstofverbruik blijft groeien. Dit dwingt de ontwerpers van krachtige dieselmotoren om de ontstekingspiekdruk te verhogen, wat de thermische belasting en mechanische belasting van de motor sterk verhoogt. Tegelijkertijd nemen de thermische belasting en de mechanische belasting toe, zodat de conventionele motoren van gietijzer en gelegeerd gietijzer (CrMo) die momenteel worden gebruikt de bovengrens van hun gebruik hebben bereikt of overschreden. Motorfabrikanten hebben materialen nodig met een hogere sterkte en een betere hittebestendigheid.
Vermiculair ijzer is snel het materiaal bij uitstek geworden voor mensen. Het verbetert de betrouwbaarheid van het cilinderblok, de cilinderkop en de cilindervoering van de nieuwe generatie vrachtwagenmotoren aanzienlijk. Om de beste combinatie van verschillende eigenschappen (zoals gieteigenschappen, bewerkingseigenschappen, thermische geleidbaarheid en mechanische eigenschappen) te bereiken, moeten deze onderdelen worden gemaakt met een sferoïdisatiegraad van 0% tot 20% (kruipsnelheid van 80% tot 100%). Gemaakt van vermiculair ijzer. Als de sferoïdisatiesnelheid hoger is dan 20%, zal dit een reeks ongunstige factoren veroorzaken. Zo is de mate van krimp te groot en zijn onderdelen met complexe vormen zoals cilinderkoppen bijzonder gevoelig voor krimp. Een ander voorbeeld is de verkorting van de standtijd door overmatige slijtage tijdens de bewerking. Er is ook een aanzienlijke afname van de thermische geleidbaarheid, waardoor thermische stress ontstaat, enzovoort. Aan het andere uiteinde van het vermiculair ijzer zal het verschijnen van schilfergrafiet een lineaire achteruitgang van de mechanische eigenschappen veroorzaken, waardoor de motor niet aan de nieuwe eisen kan voldoen. Samengevat, om aan de behoeften van de nieuwe generatie vrachtwagenmotoren te voldoen, moet de sferoïdisatiesnelheid van hoogwaardig vermiculair ijzer tussen 0% en 20% liggen (d.w.z. de kruipsnelheid is hoger dan 80%, zonder vlokken).
Het al dan niet gebruiken van productieprocescontrole hangt af van de jaarlijkse output van het product, de complexiteit van het product en het toegestane bereik van veranderingen in de metallografische structuur. Zoals weergegeven in figuur 1, kunnen relatief eenvoudige onderdelen met een laag volume, zoals gietvormen, over het algemeen worden geproduceerd met conventionele gietmethoden. Procesbeheersing is over het algemeen niet nodig en het is economisch niet rendabel. Wanneer de jaarlijkse productie van componenten, zoals uitlaatpijpen, krukhulzen en beugels, toeneemt, moet het zinvol zijn om procesbeheersing in te voeren. Hoewel dit type product een grote jaarlijkse productie heeft, is het jaarlijkse tonnage gietwerk niet hoog. De vereisten van de metallografische structuur zijn niet erg streng, waardoor de sferoïdisatiesnelheid kan oplopen tot 50%. Bovendien kan, vanwege de kleine hoeveelheid machinale bewerking van dergelijke onderdelen, de toename van titanium die aan de productie kan worden toegevoegd, worden toegestaan om het regelbare bereik uit te breiden. Voor dit type product zijn conventionele gietmethoden en strikte training over het algemeen geschikt voor de productie van vermiculair ijzer. Maar vanuit het oogpunt van kwaliteitscontrole zou procesbeheersing veiliger moeten zijn. Evenzo biedt procesbeheersing ook een garantie voor de productie van grote scheepsmotorblokken en cilinderkoppen. Hoewel de grote omvang en de lage productiehoeveelheid bevorderlijk zijn voor de vervaardiging van producten, zijn de economische verliezen die worden veroorzaakt doordat de producten de norm overschrijden, voldoende om een set procesbesturingssystemen toe te voegen.
De producten die het meest behoefte hebben aan procesbeheersing zijn motorblokken, cilinderkoppen en remschijven voor auto's met grote jaarlijkse productie, hoge complexiteit en strikte technische vereisten. Het jaarlijkse productievolume en de jaarlijkse tonnage van deze producten zijn zeer hoog. Ze zijn complex van formaat, stellen hoge eisen aan de metallografische structuur en hebben de neiging om krimpholtes te produceren. Deze producten mogen geen kwaliteitsrisico's hebben, anders is het verlies zeer ernstig.
De strenge eisen aan de prestaties van het motorblok, de cilinderkop en de cilinderzitting hebben de basis gelegd voor het vervaardigen van productspecificaties. Om de beste uitgebreide prestaties van gietbaarheid, bewerkbaarheid en mechanische eigenschappen te verkrijgen, moet de sferoïdisatiesnelheid in het bereik van 0% tot 20% liggen in alle belangrijke onderdelen van het onderdeel. Wat nog belangrijker is, is dat grafietschilfers absoluut vermeden moeten worden om schade aan onderdelen veroorzaakt door lokale zwakte te voorkomen. Om een goede mechanische additiviteit te bereiken, moeten vrije carbiden tot een minimum worden beperkt. Daarom mag titanium nooit worden toegevoegd. Ten slotte heeft de gieterij vanuit productieoogpunt een stabiel en betrouwbaar proces nodig om de laagste hoeveelheid afval als gevolg van de metallografische structuur te garanderen. Fabrikanten in de auto-industrie eisen kwaliteitsborging en 100% van de gietstukken moet voldoen aan metallografische eisen. Grootschalige, betrouwbare productie van cilinderblokken, cilinderkoppen en cilinderzittingen vereist nauwkeurige analyse en online aanpassing van gesmolten ijzer om fluctuaties in het proces vóór het gieten te elimineren.
Vermiculaire ijzerstabiliteit
De reden waarom verdicht ijzer niet in grote hoeveelheden wordt gebruikt om complexe onderdelen (zoals motorblokken) te produceren, is omdat het stabiele gebied van verdicht ijzer te klein is om ervoor te zorgen dat er geen risico's zijn in de productie. Over het algemeen beslaat deze stabiele zone slechts het gebied van 0.008% magnesium, zoals weergegeven in figuur 2. De grootte en positie van het platform in de stabiele zone variëren per product. In feite is het beschikbare magnesiumbereik kleiner dan dit. Omdat elke 5 minuten actief magnesium 0.001% verbrandt. Het aanvankelijke gietpunt van het gesmolten ijzer moet voldoende verwijderd zijn van het scherpe keerpunt van het verdichte ijzer naar het grijze ijzer om ervoor te zorgen dat er geen schilfergrafiet in het uiteindelijke gegoten onderdeel verschijnt. Wanneer magnesium aan het gesmolten ijzer wordt toegevoegd, zal er in ongeveer 15 minuten vlokgrafiet verschijnen.
Het startpunt mag niet te dicht bij de rechterkant van het stabiele platform liggen (hoog magnesiumgehalte), anders ontstaat er een grote hoeveelheid bolvormig grafiet in het dunnere deel en het snelkoelende deel.
Naast het kleine beschikbare platformoppervlak is het platformgebied altijd in beweging. Als het gehalte aan actieve zuurstof en zwavel hoog is, zullen ze meer actief magnesium verbruiken en zal het hele platform naar rechts bewegen (hoog magnesiumgehalte). Omgekeerd, als het actieve zuurstof- en zwavelgehalte laag is, zal het platform naar links bewegen (laag magnesiumgehalte). Veranderingen in de samenstelling van grondstoffen, zuiverheid, mate van oxidatie en vochtigheid, enz., maken het voor mensen onmogelijk om vermiculair ijzer met een vast bereik van chemische samenstelling te beheersen.
Hoewel de omzetting van vermiculair ijzer naar grijs ijzer het actieve magnesium slechts met 0.001% hoeft te verminderen, zorgt de verbranding van magnesium er niet voor dat het hele onderdeel in vlokgrafiet verandert. Wanneer het actieve magnesium niet genoeg is, vormt grafiet eerst vlokken en zet het uit naar buiten terwijl het stolt, en magnesium zakt en concentreert zich aan de voorkant van de vaste stof-vloeistof interface. Als de initiële hoeveelheid actief magnesium geschikt is, wordt vermiculair grafiet gevormd aan de grens van het eutecticum, zoals weergegeven in figuur 3. Vlokgrafiet verschijnt eerst als verspreide vlokgrafietvlekken. In tegenstelling tot alle gewone schilfergrafiet zijn deze geïsoleerde schilfergrafietvlekken moeilijk te detecteren met echografie. De kans dat ze worden gescand door middel van echografie is niet groot.
De gevoeligheid van magnesium voor vermiculair ijzer kan worden weergegeven in figuur 4: voeg in een ton hete metalen gietlepel gewoon 10 gram magnesium toe, de vlokgrafietvlekken die in het Φ25-testmonster zijn verspreid, kunnen volledig worden omgezet in vermiculair grafiet. De treksterkte van de teststaaf met schilferende grafietvlekken is slechts 300 MPa, terwijl de treksterkte van dezelfde teststaaf met volledige kruip 450 MPa bereikt.
Het inoculant is ook erg gevoelig voor het stabiele platform van vermiculair ijzer, zoals weergegeven in figuur 5: het toevoegen van 80 gram inoculant aan één ton gesmolten ijzer zal de sferoïdisatiesnelheid in de Φ25-testbalk verhogen van 3% naar 21%. De inentingshoeveelheid is hoog en de kristalkern is talrijk, wat bevorderlijk is voor de vorming van bolvormig grafiet. Dit verhoogt het vermiculaire ijzeren platform in de richting van een hoge sferoïdisatiesnelheid. Door de lage entgraad beweegt het platform naar beneden. Talrijke factoren, zoals de oververhittingstemperatuur van gesmolten ijzer, de verblijftijd, de chemische samenstelling van de grondstoffen, het type inoculant en de hoeveelheid inoculatie, zullen de positie van het vermiculaire ijzeren platform beïnvloeden.
De meest fundamentele vereiste van elke procesbesturingstechnologie is het nauwkeurig meten en analyseren van de toestand van gesmolten ijzer. Voor vermiculair ijzer vereist betrouwbare productiecontrole gelijktijdige meting van het kritieke punt van actief magnesium vanaf de kruip-asovergang, de mate van daaropvolgende magnesiumverbranding en de mate van inenting.
Het thermische analysemonster van 200 gram wordt verkregen door de Xinte-sonde in het gesmolten ijzer te steken na sferoïdisatie en inoculatie. Tijdens het inbrengproces van drie seconden bereiken de sondewand en het gesmolten ijzer een thermisch evenwicht. Anders dan de conventionele monsterbeker voor thermische analyse, garandeert deze dunwandige sampler niet alleen elke keer hetzelfde monstervolume, maar voorkomt ook oxidatie in het gesmolten ijzer dat in de monsterbeker wordt gegoten. De meting van oververhitting is nauwkeuriger omdat er geen fenomeen is zoals het fenomeen van gewelddadige condensatie in conventionele thermische analyse.
Zoals weergegeven in figuur 6a, is de Xinte-sonde gemaakt van geperst gestrekt plaatstaal. Het is eigenlijk een bolvormige container. De dunne stalen wand die het gesmolten ijzer bevat, heeft een thermosflesachtige isolatielaag. De dikte van de isolatielaag is symmetrisch verdikt volgens de richting van de hoogte om een uniforme warmteafvoer en koeling naar de omgeving te garanderen, en het ijzer zz-water daarin ligt dicht bij de stolling van een bolvormig lichaam. Er zitten twee N-type thermokoppels in de beschermbuis in de sonde. Het thermokoppel kan na elke meting worden uitgetrokken en meer dan 100 keer worden gebruikt. Een van de twee thermokoppels bevindt zich aan de onderkant van de container en de andere bevindt zich in het thermische centrum van de container. Aangezien de houder bolvormig is en vrij hangt (dit verschilt van de conventionele monsterbeker voor thermische analyse die op een warmteabsorberende beugel rust), genereert het gesmolten ijzer een uniforme warmtestroom in de houder, zoals weergegeven in figuur 6b. Deze warmtestroom zorgt ervoor dat het gesmolten ijzer continu wordt uitgewisseld in de container, waardoor er een stroomscheiding ontstaat aan de onderkant van de sonde.
Om het natuurlijke verlies van gesmolten ijzer tijdens het gieten na te bootsen, zit er een coating op de sondewand die reageert met actief magnesium. Het gesmolten ijzer stroomt langs de gecoate wand aangedreven door de warmtestroom. Na de reactie neemt het magnesiumgehalte van het gesmolten ijzer af en hoopt het zich op in het compartiment onderin de container. Direct gesproken: het thermokoppel in het midden van de sonde meet het niet-gereageerde gesmolten ijzer, wat de begintoestand van het gieten is; het thermokoppel aan de onderkant meet de toestand na het einde van het gieten. De formulering van de reactieve coating is zeer bijzonder. Er moet nauwkeurig worden gezorgd dat het gesmolten ijzer dat zich ophoopt in het compartiment 0.003% minder actief is dan het middelste gesmolten ijzer. Daarom, als het initiële magnesiumgehalte te dicht bij het keerpunt van de kruip-as ligt, zal het gesmolten ijzer in het compartiment grijs ijzer genereren, dat zal worden gemeten door het thermokoppel in dit gebied. Op deze manier kan de werkplaats aan het begin van het gieten meer magnesium toevoegen om het onvermijdelijke magnesiumverbrandingsverlies te compenseren.
Als het thermokoppel aan de onderkant een vermiculaire ijzercurve vertoont, geeft dit aan dat het aanvankelijke magnesiumgehalte hoog genoeg is om na het gieten geen schilfergrafiet meer te hebben.
Figuur 7 is een erosiediagram in dwarsdoorsnede van de Xinte-sonde na monstermeting. In de afbeelding kunt u duidelijk het scheidingsgebied, het hoofdmonstergebied en de thermokoppelbeschermingsbuis zien. Omdat het actieve magnesium met 0.003% wordt verminderd, wordt in de scheidingszone een D-vormige grafiet- en ferrietmatrix gevormd. De grootte van het vlokgrafietgebied aan de onderkant geeft direct het aanvankelijke magnesiumgehalte in het hoofdmonstergebied weer. De grootte van deze zone kan worden berekend uit de warmte die aan de onderkant vrijkomt. De regressiecoëfficiënt-coëfficiënt tussen warmteafgifte en de grootte van de scheidingswand is groter dan 0.9, wat bewijst dat de relatie tussen de twee zeer nauw is. De vrijgekomen warmte wordt verkregen door de tijdsintegratie van de koelcurve. Deze methode om de toestand van het gesmolten ijzer bij stroom en aan het einde van het gieten te meten, zorgt tegelijkertijd voor de nauwkeurigheid van het magnesiumgehalte vóór het gieten.
Aangezien vermiculair ijzer zeer gevoelig is voor bolvormende middelen en inoculanten, is het voor gieterijen onmogelijk om de buitensporige behandelingsmethoden toe te passen die worden gebruikt bij de productie van grijs ijzer en nodulair gietijzer. Zoals te zien is in figuur 8, is vermiculair ijzer vanwege zijn gevoeligheid alleen stabiel binnen een vierkant venster, niet alleen het magnesiumplatformgebied. Een betrouwbaar productieproces van vermiculair ijzer moet sferoïdisatie en inoculatie van begin tot eind beheersen om ervoor te zorgen dat de metallografische structuur het doel bereikt.
Hoeveel moeite er ook wordt gedaan, hoe streng het management ook is, de fluctuatie van gesmolten ijzer is altijd onvermijdelijk. Laat staan hoe nauwkeurig mensen weten over de behandeling met gesmolten ijzer, behandelmethoden in één stap, zoals de sandwichmethode, kunnen niet garanderen dat elke behandeling binnen het smalle venster van vermiculair ijzer valt. Talrijke productievariabelen, zoals de mengverhouding, de oventemperatuur, de verblijftijd, de mate van voorverwarmen van de gietpan van gesmolten ijzer, de tapsnelheid, de tappositie van het tappen van gesmolten ijzer (binnen- of buitenmeting), het gewicht van het tappen van gesmolten ijzer, de staat van de legeringszak, het sferoïdiserende middel. Het werkelijke magnesiumgehalte van (PeSiMg), de legeringsrangschikking van elke laag in de sandwichmethode en de dekking van schrootvijlsel, enz., zullen allemaal de absorptie van magnesium beïnvloeden. Naast deze factoren zal het gehalte aan actieve zuurstof en actieve zwavel ook de grootte en positie van het vermiculaire ijzeren venster veranderen. Veranderingen in de verblijftijd van gesmolten ijzer in de gietpan, transporttijd en giettijd zullen allemaal de beschikbare brandtijd veranderen.
De meest onvoorspelbare fluctuatiefactoren zijn echter operatorfouten of verschillen tussen verschillende operators als gevolg van verschillende werkgewoonten.
Bij massaproductie op grote schaal is de enige veilige manier het meten van de stollingseigenschappen van het gesmolten ijzer na behandeling. Op deze manier zijn verschillende factoren die van invloed zijn op de grootte, positie en legeringsabsorptie van het vermiculaire ijzeren venster uitgebreid gemeten, geanalyseerd en overwogen. Vervolgens kan de juiste hoeveelheid magnesium en inoculant worden toegevoegd. Elke gietlepel gesmolten ijzer wordt gegoten nadat het is opgewaardeerd tot een ideale staat. Deze procescontrolemethode in twee stappen, meting en aanpassing, minimaliseert productievariabiliteit en elimineert volledig het risico van grafietschilfers in het gietstuk.
Procesbeheersing van de productie van vermiculair ijzer met hete metalen pollepel
Zoals weergegeven in figuur 9, begint de procescontrole met de thermische analyse van het gesmolten ijzer na de initiële sferoïdisatie- en inoculatiebehandeling. Volgens het analyseresultaat geeft de draadaanvoermachine automatisch de lengte van de draad weer die moet worden toegevoegd met magnesium en inoculant, en wacht tot de operator deze start. Wanneer de voerlijn is voltooid, wordt de pollepel onmiddellijk naar de gietlijn gestuurd. Het gehele meet- en justeerproces duurt ongeveer drie minuten. Tijdens deze periode kan de werkplaats conventionele voorgietbehandelingen uitvoeren, zoals slakverwijdering. Dit zorgt voor de continuïteit van de gietlijn.
Vanuit operationeel oogpunt bevat ruw gesmolten ijzer geen magnesium en is de incubatiecapaciteit ook zeer beperkt. Na sferoïdisatie en inoculatie eten magnesium en inoculanten eerst de actieve zuurstof en zwavel in het gesmolten ijzer op en "springen" het gesmolten ijzer vervolgens naar een bepaalde positie op het bord. In het voorbeeld in afbeelding 10 zijn de magnesiumindex en inoculatie-index van gesmolten ijzer respectievelijk 65 en 45. Omdat de belangrijkste veranderingsparameters van de schaduwproductie na meting en behandeling in het gesmolten ijzer worden weergegeven, geven de resultaten van de thermische analyse direct de huidige toestand van het gesmolten ijzer weer. Het enige dat overblijft is de juiste hoeveelheid magnesium en inoculant toe te voegen om het gesmolten ijzer van zijn huidige positie naar het vereiste startpunt te brengen. In het voorbeeld in afbeelding 10 worden eerst zeven eenheden magnesiumkabels toegevoegd en daarna 23 eenheden inoculantkabels. De corresponderende relatie tussen de indexeenheid en de kabellengte wordt afhankelijk van het product en de werkplaats gekalibreerd en in het programma samengesteld. Gebaseerd op de ervaringen uit het verleden van bijna 100,000 gietstukken van vermiculair ijzer, is de gemiddelde hoeveelheid toegevoegde magnesiumkabel 5 meter per ton. Het bevat 12 gram magnesium per meter en berekend bij een absorptiegraad van 50% is de toegevoegde hoeveelheid magnesium per ton gesmolten ijzer slechts 30 gram. Aangezien de toegevoegde hoeveelheid erg klein is en de belangrijkste veranderingen al in de eerste behandeling hebben plaatsgevonden, is de aanpassing zeer effectief en betrouwbaar. Na aanpassing is er geen noodzaak om thermische analyse uit te voeren.
Bij de initiële behandeling moet de toestand na de behandeling lager zijn dan de initiële gietpositie, zodat zelfs als alle factoren die gunstig zijn voor de absorptie van magnesium en inoculant de optimale waarde bereiken, het gesmolten ijzer alleen de initiële giettoestand zal bereiken. Behalve om niet te veel te behandelen, is het gesmolten ijzer na de behandeling niet in de staat van grijs ijzer en wit ijzer. Om het gietproces efficiënter te maken, worden de magnesiumindex en inoculatie-index van elke gietpan met gesmolten ijzer weergegeven in het blokschema van het proces. Volgens de veranderende trend van het blokdiagram kan de operator de hoeveelheid gesmolten ijzer aanpassen die aan de volgende gietpan wordt toegevoegd. De koolstofequivalentwaarde wordt ook weergegeven op het scherm. Deze gegevens zijn bewerkt en opgeslagen in het productielogboek, zodat het traceerbaar en volledig is en bovendien voldoet aan de eisen van kwaliteitsborging.
Hoewel thermische analyse en daaropvolgende aanpassingen de productie van vermiculair ijzer kunnen garanderen, wordt aanbevolen om monsters te nemen uit de spruwbeker van het uiteindelijke gietstuk voor analyse. Vergeleken met conventionele kwaliteitsinspectie, kan dit resultaat van thermische analyse een online analyse bieden en indien nodig gietstukken classificeren. De simulatie van magnesiumverlies in de sonde maakt deze "niet-destructieve" inspectietechniek effectiever dan metallografische en ultrasone methoden. Omdat deze methode een grotere steekproefomvang meet, detecteert het ook hoe het gesmolten ijzer in de komende 10-15 minuten zal stollen.
Op te sommen
De keuze van het procesbesturingssysteem is afhankelijk van het product en het gietproces. Bij het gieten van complexe producten, zoals de motorkap en cilinder van vermiculair ijzer, moet het systeem tegelijkertijd het gehalte aan magnesium en inoculant regelen, zodat het van het begin tot het einde van het gieten binnen een zeer smal gebied blijft. Het sferoïdisatiepercentage moet tussen 0% en 20% liggen (kruipsnelheid 80% tot 100%) om de beste gietbaarheid, mechanische additiviteit en andere uitgebreide prestaties en de beste gebruiksfunctie te garanderen. Schilfergrafietvlekken moeten volledig worden geëlimineerd om lokale defecten en zwakheden te voorkomen.
Het uitgangspunt van elk procesbesturingssysteem is het nauwkeurig en effectief meten van de toestand van het gesmolten ijzer. Betrouwbare grootschalige productie van vermiculair ijzer moet haalbare controlemethoden hebben om procesveranderingen en menselijke bedieningsfouten te elimineren. De meest effectieve manier om procesveranderingen te elimineren, is thermische analyse uit te voeren op gesmolten ijzer na sferoïdisatie en inoculatie. Volgens de resultaten van de thermische analyse wordt een nauwkeurige hoeveelheid magnesium en inoculant toegevoegd vóór het gieten. Deze online meet- en afstelmethode zorgt voor de stabiliteit van de gietproductielijn en elimineert verschillende risico's die gepaard gaan met de grootschalige productie van vermiculair ijzer.
Bewaar de bron en het adres van dit artikel voor herdruk: De procesbeheersing van vermiculaire ijzerproductie
Minge Spuitgietbedrijf zijn toegewijd aan het vervaardigen en leveren van hoogwaardige en hoogwaardige gietstukken (het assortiment metalen spuitgietonderdelen omvat voornamelijk: Dunwandig spuitgieten,Hot Chamber Spuitgieten,Koude kamer spuitgieten),Ronde Service (Die Casting Service,CNC-bewerking,Matrijzen maken, Oppervlaktebehandeling). Elk aangepast aluminium spuitgieten, magnesium of Zamak / zink spuitgieten en andere gietstukken zijn welkom om contact met ons op te nemen.
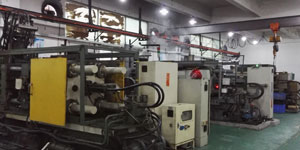
Onder controle van ISO9001 en TS 16949 worden alle processen uitgevoerd door honderden geavanceerde spuitgietmachines, 5-assige machines en andere faciliteiten, variërend van blasters tot Ultra Sonic-wasmachines. Minghe heeft niet alleen geavanceerde apparatuur, maar heeft ook professionele team van ervaren ingenieurs, operators en inspecteurs om het ontwerp van de klant waar te maken.
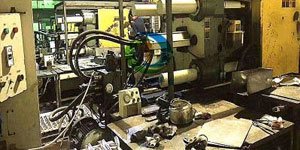
Contractfabrikant van spuitgietwerk. Mogelijkheden zijn onder meer koude kamer aluminium spuitgietonderdelen vanaf 0.15 lbs. tot 6 lbs., snelwissel instellen en machinaal bewerken. Diensten met toegevoegde waarde omvatten polijsten, trillen, ontbramen, stralen, schilderen, plateren, coaten, assembleren en bewerken. Materialen waarmee gewerkt is, zijn legeringen zoals 360, 380, 383 en 413.
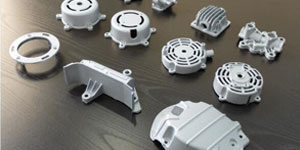
Hulp bij ontwerp van spuitgieten van zink/concurrent engineering. Custom fabrikant van precisie gegoten zink. Miniatuurgietstukken, hogedrukgietstukken, multi-slide gietstukken, conventionele gietstukken, eenheidsmatrijs en onafhankelijke spuitgietstukken en holteverzegelde gietstukken kunnen worden vervaardigd. Gietstukken kunnen worden vervaardigd in lengtes en breedtes tot 24 inch met een tolerantie van +/- 0.0005 inch.
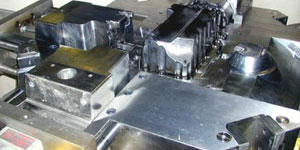
ISO 9001: 2015 gecertificeerde fabrikant van gegoten magnesium. Mogelijkheden zijn onder hoge druk spuitgieten van magnesium tot 200 ton hete kamer en 3000 ton koude kamer, gereedschapsontwerp, polijsten, gieten, machinale bewerking, poeder- en vloeistofverven, volledige QA met CMM-mogelijkheden , montage, verpakking & levering.
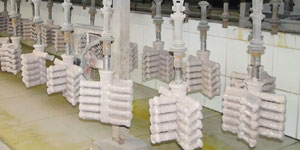
ITAF16949 gecertificeerd. Extra castingservice omvat: investering gieten,zandgieten,Zwaartekracht gieten, Verloren schuimafgietsel,Centrifugaal gieten,Vacuümgieten,Permanent vormgieten,. Mogelijkheden zijn onder meer EDI, technische assistentie, solide modellering en secundaire verwerking.
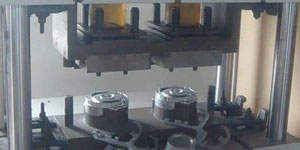
Gietindustrieën Casestudy's over onderdelen voor: auto's, fietsen, vliegtuigen, muziekinstrumenten, waterscooters, optische apparaten, sensoren, modellen, elektronische apparaten, behuizingen, klokken, machines, motoren, meubels, sieraden, mallen, telecom, verlichting, medische apparaten, fotografische apparaten, Robots, sculpturen, geluidsapparatuur, sportuitrusting, gereedschap, speelgoed en meer.
Wat kunnen we u hierna helpen doen?
∇ Ga naar de startpagina voor Spuitgieten China
→Gietonderdelen- Zoek uit wat we hebben gedaan.
→Gerangschikte tips over Spuitgietdiensten
By Minghe Die Casting Fabrikant: |Categorieën: Handige artikelen |Materiaal Tags: Aluminium gieten, Zink gieten, Magnesium gieten, Titanium gieten, Gieten van roestvrij staal, Messing gieten,Brons gieten,Video casten,Geschiedenis van ons bedrijf,Aluminium spuitgieten |Reacties uitgeschakeld