Typische gietfouten van meerfasige nodulair gietijzeren slijpballen
De meerfasige slijpbal van nodulair gietijzer is een projectproduct dat is ontwikkeld door de elektromechanische reparatie- en montagefabriek en het is een opgewaardeerd product van de originele laaggelegeerde slijpbal. De mechanische en elektrische reparatiefabriek heeft een jaarlijkse productie van bijna 10,000 ton van dit soort maalkogels. In de werkelijke productie worden de maalkogels, vanwege het bestaan van verschillende soorten defecten, onder werkelijke werkomstandigheden gebruikt, en vaak hebben niet-slijtage, onrondheid, enz. invloed op het gebruik van de maalkogels. Voor de ongunstige kwaliteitsfactoren is het noodzakelijk om alle soorten defecten één voor één te analyseren en overeenkomstige preventiemethoden te formuleren om de productiepraktijk te begeleiden.
Veelvoorkomende defecten en functies
Slechte sferoïdisatie en afname van sferoïdisatie
Slechte sferoïdisatie betekent dat de sferoïdisatiebehandeling niet voldoet aan de vereisten voor sferoïdisatie. Afname van sferoïdisatie betekent dat de resterende hoeveelheid sferoïdiserende elementen in de maalkogel in het latere stadium van het gieten te laag is om de sferoïdisatie te laten mislukken. Beide hebben dezelfde defectkenmerken.
Macroscopische kenmerken: De breuk van het gietstuk is zilvergrijs met zwarte sesamvlekken erop. Het grote aantal en de grote diameter duiden op een serieuze graad. Het zijn allemaal donkergrijze grove korrels, wat aangeeft dat er helemaal geen sferoïdisatie is.
Metallografische structuur: een groot aantal dikke vlokgrafiet is geconcentreerd verdeeld. Hoe meer de hoeveelheid en de toename van de oppervlakteverhouding, het geeft aan dat de mate ernstig is, en degene zonder sferoïdisatie is vlokgrafiet.
Oorzaak: Het ruwe gesmolten ijzer bevat een hoog zwavelgehalte en de sterk geoxideerde lading bevat overmatige desferoïdiserende elementen; het resterende magnesium- en zeldzame aardegehalte in het gesmolten ijzer na behandeling is te laag. Hoge opgeloste zuurstof in gesmolten ijzer is een belangrijke reden voor slechte sferoïdisatie.
Kies laagzwavelige cokes en laagzwavelige metaallading, ontzwaveling indien nodig, verwijder roest van schrootstaal, verhoog indien nodig de hoeveelheid zeldzame aardelementen in het sferoïdiseermiddel en controleer het sferoïdisatieproces strikt.
2.2 Krimpholte en krimpporositeit
Eigenschappen en oorzaken: Krimp treedt op wanneer de temperatuur van het gesmolten ijzer één keer daalt en krimpt. Als de atmosferische druk de vaste dunne laag op het oppervlak laat zakken, zal deze oppervlaktedepressies en lokale hete gewrichtsdepressies vertonen. Anders zal het gas in het gesmolten ijzer neerslaan in de bovenste schaal en zich verzamelen in de gladde donkere krimpgaten op de binnenwand van de luchtgaten, die soms communiceren met de buitenwereld om heldere holtes te vormen. Krimpholte, hoewel het binnenoppervlak glad is, maar is geoxideerd. De eutectische stollingstijd van nodulair gietijzer is langer dan die van grijs gietijzer en stolt in de vorm van een pap. De gestolde schaal is zwakker. Tijdens de tweede expansie zet de schaal uit onder invloed van de grafitisatie-expansiekracht, die de interne druk ontspant. Daarom is in het tweede krimpproces de interne druk van de laatste gestolde hete verbinding lager dan de atmosferische druk, en wordt de kleine gesmolten poel gescheiden door dendrieten een vacuümzone. Na volledige stolling wordt het een ruw gat gevuld met dendrieten. Dat wil zeggen, krimpdefecten. Wat met het blote oog zichtbaar is, wordt macroscopische krimp genoemd. Het komt voor in het vroege stadium wanneer het resterende gesmolten ijzer in het hete verbindingsgebied in grote hoeveelheden begint te stollen. Het omvat de primaire en secundaire krimp van het resterende gesmolten ijzer, dus de maat is iets groter en de binnenwand zit vol met dendrieten, die grijs en donker zijn. Losse gaten of zwarte vlekken zoals vliegenvoeten. Wat onder de microscoop zichtbaar is, wordt microscopische krimp genoemd. Het wordt geproduceerd aan het einde van de secundaire contractie. Het gesmolten ijzer in de eutectische groep of zijn groep kan niet onder negatieve druk worden gevoed. Het wordt gevormd door stollen en krimpen, wat gebruikelijk is in dikke secties.
2.3 Subcutane huidmondjes
Morfologische kenmerken: sferische, elliptische of pinhole-achtige gladde gaten op de binnenwand van het gietoppervlak 2-3 mm gelijkmatig of honingraat verdeeld, met een diameter van 0.5-3 mm, die kan worden gevonden na warmtebehandeling en stralen, blootstelling of machinale bewerking , klein Er zijn er meer.
Redenen voor vorming: De oppervlaktespanning van de magnesiumhoudende ijzervloeistof is groot en het is gemakkelijk om een oxidefilm te vormen, die de afvoer van het neergeslagen gas en het binnendringende gas belemmert, en wordt gevormd door onder de huid te blijven. De temperatuur van de vormende film neemt toe met de toename van de hoeveelheid achtergebleven magnesium, wat het belemmerende effect ervan versterkt. Dunwandige (7-20 mm) onderdelen koelen snel af en vormen de film vroeg, wat gemakkelijk is om dit defect te vormen. De gasbron is voornamelijk de magnesiumdamp die tijdens het koelproces uit het gesmolten ijzer wordt geprecipiteerd, en het gesmolten ijzer rolt op tijdens het vulproces. Magnesium in het gesmolten ijzer reageert met het vocht van het vormzand. Magnesium werkt als een katalysator om de reactie tussen koolstof en het vocht van het vormzand te bevorderen. Magnesium zorgt ervoor dat het ijzer bij verhoogde activiteit reageert met het vocht. De reactie van water, magnesium en carbiden om acetyleenontleding te produceren, kan waterstof produceren. Bovendien kunnen natte en roestige ovenlading, nat ferrosilicium en tussenliggende legeringen en koepelhoge temperatuurontploffing waterstof binnenbrengen. Een kleine hoeveelheid Al (0.02%-0.03%) kan de subcutane poriën aanzienlijk vergroten. Medium mangaan nodulair gietijzer bevat meer stikstof. Het harsbindmiddel met zandkern bevat meer stikstof en de bovengenoemde factoren kunnen de vorming van dit defect bevorderen. De pasta-achtige stollingskarakteristiek van nodulair gietijzer zorgt ervoor dat de gasdoorgang eerder wordt geblokkeerd en bevordert ook de vorming ervan.
2.4 Spanningsvervorming en scheuren
Vormingsredenen en morfologische kenmerken: tijdens het koelproces van het gieten, de algebraïsche som van de krimpspanning, thermische spanning en fasetransformatiespanning, dat wil zeggen, de gietspanning overschrijdt de breukweerstand van het profielmetaal, en dan worden scheuren gevormd. Bij hoge temperaturen (1150-1000 ) worden thermische scheuren gevormd, die donkerbruine ongelijke breuken vertonen. Koude scheuren verschijnen in het elastische bereik onder 600°C, met lichtbruine gladde en rechte breuken. Plastische vervorming kan optreden wanneer de gietspanning de vloeigrens boven 600°C overschrijdt. Wanneer de samenstelling van nodulair gietijzer normaal is, is het niet gemakkelijk te kraken.
Beïnvloedende factoren: Factoren die de neiging tot witte mond vergroten, zoals een laag koolstof- en siliciumgehalte, verhoogde carbidevormende elementen, onvoldoende incubatie en overmatige koeling, kunnen allemaal de gietspanning en de neiging tot koudscheuren vergroten. Fosfor verhoogt de neiging tot koudscheuren en P>0.25 kan ook warmscheuren veroorzaken. De wanddikte van gietstukken varieert sterk, de vorm is complex en vervorming en scheuren zijn gemakkelijk op te treden.
2.5 Slakkenopname
Morfologische kenmerken: Verdeeld op het bovenoppervlak van de gietpositie, onder de kern en in de dode hoek van het gietstuk. Donkerzwarte en matte insluitsels van verschillende diepten verschijnen op het gebroken oppervlak, met tussenpozen verspreid. Metallografische waarneming kan strookvormige en blokvormige insluitsels vertonen, en aangrenzend grafiet kan de vorm hebben van vlokken of bollen. Tijdens magnetische deeltjesinspectie worden de magnetische markeringen in stroken verdeeld en zijn de strepen dik en dicht, wat wijst op ernstige slakopname. Elektronensonde-analyse toont aan dat de slak Mg, Si, O, S, C, A1 enz. bevat en is samengesteld uit magnesiumsilicaat, zuurstof-zwavelverbindingen, magnesiumspinel, enz.
Vormingsproces: Mg en RE reageren met O en S in gesmolten ijzer om slakken te vormen tijdens sferoïdisatie. Wanneer de temperatuur van het gesmolten ijzer laag is, het effect van het dunne slakmiddel niet goed is, de slak niet goed drijft of de slak niet gereinigd wordt en in het gesmolten ijzer achterblijft, is dit een primaire slak. Wanneer het gesmolten ijzer wordt getransporteerd, gegoten, gegoten en gevuld en gerold, wordt de oxidefilm gebroken en in de mal getrokken, drijvend in de mal, sulfide adsorberend en verzamelend op het bovenoppervlak of dode hoeken, wat de secundaire slak is . Over het algemeen is secundaire slak de steunpilaar.
3. Preventieve maatregelen
3.1 Oorzaken van achteruitgang van sferoïdisatie en preventieve maatregelen
De sulfide- en oxideslakken gevormd na de sferoïdisatiebehandeling van hoogzwavel en oxidatie bij lage temperatuur van het gesmolten ijzer zijn niet volledig drijvend, de slak wordt niet adequaat verwijderd en het gesmolten ijzer is niet goed bedekt. De zuurstof in de lucht gaat door de slaklaag of komt direct in het gesmolten ijzer. Effectieve oxidatie van sferoïdiserende elementen en het verhogen van actieve zuurstof zijn belangrijke redenen voor de achteruitgang van sferoïdisering. De zwavel in de slak kan ook opnieuw het gesmolten ijzer binnendringen om de sferoïdiserende elementen erin te consumeren. Tijdens het transporteren, roeren en dumpen van het gesmolten ijzer, hoopt magnesium zich op, drijft en wordt geoxideerd, waardoor de effectieve resterende sferoïdiserende elementen worden verminderd en de sferoïdisatie afneemt. Bovendien vermindert de zwangerschapsafname ook het aantal grafietbollen en leidt dit tot verslechtering van de grafietmorfologie. De bovengenoemde factoren die een slechte sferoïdisatie veroorzaken, versnellen ook de achteruitgang van sferoïdisatie.
Het zwavel- en zuurstofgehalte van het oorspronkelijke gesmolten ijzer moet zoveel mogelijk worden verlaagd en de temperatuur moet op de juiste manier worden geregeld. Slakverdunner kan worden toegevoegd om de slak volledig te laten drijven en de slak volledig te verwijderen. Voeg na het verwijderen van de slak grasas, kryolietpoeder, grafietpoeder of andere afdekmiddelen toe om de lucht te isoleren. Het toevoegen van een deksel of het gebruik van een afgesloten gietlepel en het gebruik van stikstof- of argonbescherming kan effectief voorkomen dat de sferoïdisatie afneemt. Het gieten moet worden versneld en de tijd van lossen, transport en verblijf moet worden geminimaliseerd. Het gebruik van op yttrium gebaseerde zware zeldzame-aarde magnesium sferoïdizer kan de vervaltijd met 1.5-2 keer verlengen, en de vervaltijd van lichte zeldzame-aarde magnesium sferoïdiserende agent is iets langer dan die van magnesium sferoïdiserend middel. Indien nodig kan de toegevoegde hoeveelheid sferoïdiserend middel ook op geschikte wijze worden verhoogd. De grafietmorfologie verslechterde door de incubatiedaling, die na suppletie kan worden verbeterd.
3.2 Beïnvloedende factoren en preventieve maatregelen voor krimp en porositeit
Laag koolstofequivalent verhoogt de neiging tot krimpholten en porositeit. Het fosforeutectische middel verzwakt de sterkte van de gestolde schaal en het ternaire fosforeutectische middel vermindert de grafitiseringsexpansie, zodat het hoge fosforgehalte de neiging tot krimpen aanzienlijk verhoogt. Molybdeen verhoogt de stabiliteit van carbiden, vooral onder hoge fosforomstandigheden, het is gemakkelijk om carbide-fosfor-eutectische composieten te vormen en het verhoogt ook de neiging tot krimp en krimp. Een te hoog residuaal magnesium verhoogt de neiging tot krimpporositeit en krimpholten, een matige hoeveelheid resterende zeldzame aarde kan de krimpporositeit verminderen, en een te hoog gehalte verhoogt de neiging van beide. Daarom moet het koolstofequivalent van het gesmolten ijzer worden verhoogd, moet het fosforgehalte worden verlaagd, moet de resterende hoeveelheid zeldzame-aardmagnesium zo veel mogelijk worden verminderd onder de gegarandeerde sferoïdisatie-omstandigheden en moet het molybdeen rationeel worden gebruikt. Verbeter de stijfheid van de mal, zoals hogedrukgieten, waszandvorm en metalen malzandcoating, kan krimp en krimp verminderen, terwijl het koolstofequivalent van gesmolten ijzer wordt verhoogd, de giettemperatuur op de juiste manier wordt verlaagd en een dun en breed binnenste runner om het in de tweede keer uit te breiden. Vóór stolling en afdichting wordt grafitisatie-expansie gebruikt om te compenseren voor krimp van vloeibaar ijzer en krimp door stolling, wat krimp en porositeit kan elimineren.
3.3 Preventieve maatregelen voor onderhuidse poriën: De giettemperatuur mag niet lager zijn dan 1300°C. Wanneer het resterende magnesiumgehalte hoog is, moet de giettemperatuur dienovereenkomstig worden verhoogd; het resterende magnesiumgehalte moet zoveel mogelijk worden verminderd onder de gegarandeerde sferoïdisatieconditie en zeldzame aardmetalen moeten op de juiste manier worden gebruikt; het open multi-runner gietsysteem wordt gebruikt om het gesmolten ijzer soepel in de holte te laten stromen en de holte te vermijden. Draai naar binnen om het vochtgehalte van het vormzand ≤ 4.5% één s te regelen. 5%, gemengd met steenkoolpoeder 8% -15% kan worden verbrand tot CO, remt de reactie van waterdamp en magnesium om H2 te vormen (het sproeien van spindelolie op het oppervlak van de mal kan ook dezelfde rol spelen); het oppervlak van de mal wordt verwijderd van kryolietpoeder en reageert met waterdamp bij hoge temperaturen. De vorming van HF-gas beschermt het gesmolten ijzer tegen reactie en regelt het lage aluminiumgehalte van het gesmolten ijzer. Controleer strikt het drogen van de ovenlading en verminder de roest, de koepelontvochtiging en luchttoevoer, verminder het gas in het gesmolten ijzer en gebruik het harszand met minder of geen stikstof, enz.
3.4 Maatregelen om spanning, vervorming en scheuren te voorkomen: koolstofequivalent op gepaste wijze verhogen, fosforgehalte verlagen, inoculatie versterken en noodzakelijke gietprocesmaatregelen.
3.5 Beïnvloedende factoren van slakinsluiting en preventieve maatregelen: De belangrijkste reden voor de vorming van slakinsluiting is het hoge zwavelgehalte van het oorspronkelijke gesmolten ijzer en ernstige oxidatie. De fundamentele preventieve maatregelen zijn het verminderen van het zwavel- en zuurstofgehalte van het oorspronkelijke gesmolten ijzer en het verhogen van de temperatuur. De belangrijkste reden voor de vorming van secundaire slakken is dat de hoeveelheid achtergebleven magnesium te hoog is, wat de temperatuur van de oxidefilmvorming verhoogt. De belangrijkste maatregel is om het resterende magnesiumgehalte (kleine en middelgrote onderdelen van maximaal 0.055%) te minimaliseren onder de omstandigheden om sferoïdisatie te garanderen. Het toevoegen van een juiste hoeveelheid zeldzame aarde kan de filmvormingstemperatuur verlagen; voeg 0.16% kryoliet toe tijdens de sferoïdisatiebehandeling en strooi vervolgens 0.3% op het oppervlak na de behandeling, gebruikt om slakken te verdunnen en A1F3-gas en MgF2-film te genereren om secundaire oxidatie te verminderen. Deze methode wordt voornamelijk gebruikt om insluiting van slakken in grote delen te voorkomen, en de giettemperatuur mag niet lager zijn dan 1300 making, waardoor de giettemperatuur hoger is dan de filmvormingstemperatuur, wat secundaire slakvorming kan voorkomen. Het poortsysteem moet zo worden ontworpen dat de vulling stabiel is en de stijgbuis voor de afvoer van slakken wordt geplaatst op de locatie die vatbaar is voor zandinsluiting. De installatie van een filter kan voorkomen dat de primaire slak de spouw binnendringt.
Bewaar de bron en het adres van dit artikel voor herdruk:Typische gietfouten van meerfasige nodulair gietijzeren slijpballen
Minge Spuitgietbedrijf zijn toegewijd aan het vervaardigen en leveren van hoogwaardige en hoogwaardige gietstukken (het assortiment metalen spuitgietonderdelen omvat voornamelijk: Dunwandig spuitgieten,Hot Chamber Spuitgieten,Koude kamer spuitgieten),Ronde Service (Die Casting Service,CNC-bewerking,Matrijzen maken, Oppervlaktebehandeling). Elk aangepast aluminium spuitgieten, magnesium of Zamak / zink spuitgieten en andere gietstukken zijn welkom om contact met ons op te nemen.
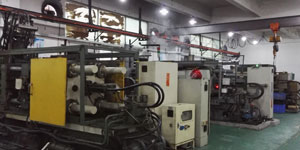
Onder controle van ISO9001 en TS 16949 worden alle processen uitgevoerd door honderden geavanceerde spuitgietmachines, 5-assige machines en andere faciliteiten, variërend van blasters tot Ultra Sonic-wasmachines. Minghe heeft niet alleen geavanceerde apparatuur, maar heeft ook professionele team van ervaren ingenieurs, operators en inspecteurs om het ontwerp van de klant waar te maken.
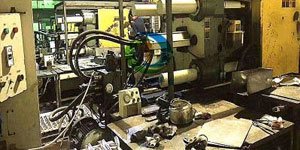
Contractfabrikant van spuitgietwerk. Mogelijkheden zijn onder meer koude kamer aluminium spuitgietonderdelen vanaf 0.15 lbs. tot 6 lbs., snelwissel instellen en machinaal bewerken. Diensten met toegevoegde waarde omvatten polijsten, trillen, ontbramen, stralen, schilderen, plateren, coaten, assembleren en bewerken. Materialen waarmee gewerkt is, zijn legeringen zoals 360, 380, 383 en 413.
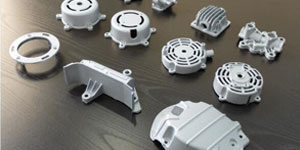
Hulp bij ontwerp van spuitgieten van zink/concurrent engineering. Custom fabrikant van precisie gegoten zink. Miniatuurgietstukken, hogedrukgietstukken, multi-slide gietstukken, conventionele gietstukken, eenheidsmatrijs en onafhankelijke spuitgietstukken en holteverzegelde gietstukken kunnen worden vervaardigd. Gietstukken kunnen worden vervaardigd in lengtes en breedtes tot 24 inch met een tolerantie van +/- 0.0005 inch.
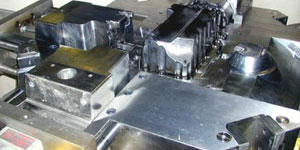
ISO 9001: 2015 gecertificeerde fabrikant van gegoten magnesium. Mogelijkheden zijn onder hoge druk spuitgieten van magnesium tot 200 ton hete kamer en 3000 ton koude kamer, gereedschapsontwerp, polijsten, gieten, machinale bewerking, poeder- en vloeistofverven, volledige QA met CMM-mogelijkheden , montage, verpakking & levering.
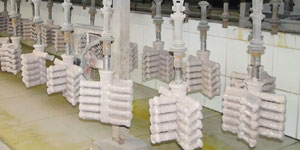
ITAF16949 gecertificeerd. Extra castingservice omvat: investering gieten,zandgieten,Zwaartekracht gieten, Verloren schuimafgietsel,Centrifugaal gieten,Vacuümgieten,Permanent vormgieten,. Mogelijkheden zijn onder meer EDI, technische assistentie, solide modellering en secundaire verwerking.
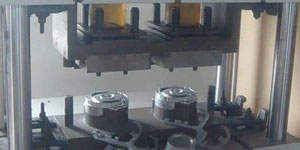
Gietindustrieën Casestudy's over onderdelen voor: auto's, fietsen, vliegtuigen, muziekinstrumenten, waterscooters, optische apparaten, sensoren, modellen, elektronische apparaten, behuizingen, klokken, machines, motoren, meubels, sieraden, mallen, telecom, verlichting, medische apparaten, fotografische apparaten, Robots, sculpturen, geluidsapparatuur, sportuitrusting, gereedschap, speelgoed en meer.
Wat kunnen we u hierna helpen doen?
∇ Ga naar de startpagina voor Spuitgieten China
→Gietonderdelen- Zoek uit wat we hebben gedaan.
→Gerangschikte tips over Spuitgietdiensten
By Minghe Die Casting Fabrikant: |Categorieën: Handige artikelen |Materiaal Tags: Aluminium gieten, Zink gieten, Magnesium gieten, Titanium gieten, Gieten van roestvrij staal, Messing gieten,Brons gieten,Video casten,Geschiedenis van ons bedrijf,Aluminium spuitgieten |Reacties uitgeschakeld