Verzameling van veelvoorkomende defecten en preventieve maatregelen bij carboneren en blussen
Carbureren en afschrikken is eigenlijk een samengesteld proces, namelijk carboneren + afschrikken. We zijn vaak gewend om over de twee samen te praten, omdat de twee processen die op dezelfde apparatuur worden voltooid, het meest voorkomen in de productie (maar er zijn ook carbonisatieluchtkoeling, carbonisatie-langzame koeling en vervolgens processen voor opwarmen en afschrikken, en secundaire afschrikken. Proces) Dan zijn enkele van de ongewenste verschijnselen die men tegenkomt bij de productie problemen met het carboneren, sommige zijn afschrikproblemen en sommige zijn het resultaat van de gecombineerde effecten van carboneren en afschrikken.
We weten dat alle warmtebehandelingsprocessen onlosmakelijk verbonden zijn met drie kernthema's: verwarming, warmtebehoud en koeling. In detail, inclusief verwarmingstemperatuur, verwarmingssnelheid, houdtijd, koelsnelheid en natuurlijk atmosfeerproblemen. Dus zodra er iets misgaat, zullen we gewoonlijk de oorzaak van deze aspecten analyseren.
Voor carboniseren en afschrikken testen we vaak deze indicatoren: uiterlijk van het productoppervlak, oppervlaktehardheid, kernhardheid, gecarboneerde laagdiepte, (effectieve geharde laagdiepte, volledig geharde laagdiepte) metallografische structuur en vervorming. Laten we mijn mening over deze indicatoren delen.
1. Uiterlijk probleem
1. Oxideaanslag: dit is voornamelijk te wijten aan lekkage van apparatuur, onzuiver draaggas of watergehalte. Behoefte om de reden van de apparatuur en grondstoffen te vinden.
2. Het andere meest lastige probleem is het probleem van vlekken, wat ook een nieuwe en uitdagende vereiste is voor warmtebehandeling in de moderne tijd. De redenen zijn ingewikkeld en zeer diepgaand.
twee. Ongekwalificeerde hardheid
1. Hoge hardheid (niet besproken)
2. Lage hardheid: er zijn twee situaties, één is ongekwalificeerd carboniseren. De reden kan zijn dat de gecarboniseerde laag te ondiep is om aan de vereisten van de tekeningen te voldoen (de gecarboniseerde laag is niet geïnfiltreerd), of de geselecteerde detectieschaal overschrijdt het bestaande aanvaardbare bereik van de gecarboniseerde laag, waardoor de gecarboniseerde laag wordt afgebroken.
Oplossing: Vul de kwel aan en volg de inspectieliniaal. JBT 6050-2006 "Algemene principes voor warmtebehandeling, hardheidsinspectie van stalen onderdelen" De diepte van de gecarboniseerde laag is eigenlijk een functie van temperatuur, tijd en koolstofpotentieel. Op basis van de bovenstaande factoren kunnen we manieren overwegen om de verwarmingstemperatuur te verhogen, de bewaartijd te verlengen en het carboneringspotentieel te vergroten. (Natuurlijk moet de aanpassing van elke parameter volledig worden gecombineerd met de vereisten van uw eigen uitrusting en producten) Het kan ook komen door het bestaan van niet-paardenorganisaties aan de oppervlakte. Een andere situatie doet zich voor wanneer de hardheid laag is, dat wil zeggen, het carboneren is gekwalificeerd, maar het blussen is niet gekwalificeerd. Over het algemeen wordt het niet geblust. Deze situatie is het meest gecompliceerd, zoals het gezegde luidt: warmtebehandeling berust op verwarming voor driekwart en koeling voor zevenkwart. Het weerspiegelt ook de positie die het koelproces inneemt in het warmtebehandelingsproces.
Het volgende is een vergelijkende test die ik heb ontworpen. U kunt het effect van koeling op de hardheid bespreken.
Neem 3 groepen teststaven met verschillende materialen maar met dezelfde specificaties en afmetingen, waarvan de afmeting Φ20mmX100mm is. (We noemen nr. 20 stalen teststaaf nr. 1, 20Cr-teststaaf nr. 2 en 20CrMnTi-teststaaf nr. 3) De teststaven worden volgens hetzelfde proces in dezelfde hitte gecarboneerd. Ervan uitgaande dat de diepte van de gecarboniseerde laag van de drie teststaven 0.6-0.7 mm is (ps: de aanname is alleen vastgesteld in een ideale toestand).
Houd rekening met de volgende voorwaarden:
A. Beëindig het blussen onder dezelfde omstandigheden
B. Blusmedium is langzame olie, snelle olie, helder water, zout water
C. In hetzelfde medium zonder roeren en intensief roeren en afschrikken worden de drie proefstaven elk in twee groepen genomen om te testen.
Nadat het carboniseren is voltooid, wordt de A-groep geblust op 800 graden en de B-groep op 860 graden. Wat is de volgorde van hun hardheid van hoog naar laag? Hoe bestel je de uitgeharde laag (met 550HV1.0 als limiet) van diep naar ondiep? Neem twee teststaven van hetzelfde materiaal en vergelijk en test, welke groep kan een hogere afschrikhardheid en effectieve geharde laagdiepte verkrijgen?
Kan uit de bovenstaande testresultaten worden geconcludeerd dat de diepte van de gecarboniseerde laag niet gelijk is aan de diepte van de effectieve geharde laag en dat de werkelijke diepte van de geharde laag wordt beïnvloed door de hardbaarheid van het materiaal, de afschriktemperatuur en de koeling tarief. De koeleigenschappen en de afschrikintensiteit van het koelmedium hebben ook invloed op het afschrikeffect. Het bovenstaande zijn de meningen van mensen, als er onvolledigheden zijn, kunt u deze toevoegen. Natuurlijk heeft ook het grootte-effect van de onderdelen invloed op het verhardingseffect.
Ik denk dat een ervaren inspecteur de echte oorzaak van de lage hardheid kan bepalen door andere testmethoden te organiseren en te combineren, en vervolgens de echte oorzaak kan vinden om het probleem op te lossen; als vakman, als u bekend bent met de kenmerken van conventionele metalen grondstoffen, hebben de koelprestaties van zijn eigen apparatuur en medium een bepaald niveau van herkenning bereikt, wat een grote hulp is bij het formuleren van carbonerings- en blusprocessen.
3. Ongelijke hardheid: uniforme oventemperatuur (beïnvloedt de uniformiteit van de carbonisatie), de structuur van de apparatuur, de circulatie van de atmosfeer, de ovenbelasting (beïnvloedt de uniformiteit van de carbonisatielaag en beïnvloedt tegelijkertijd de uniformiteit van het doven)
4. De kernhardheid is ongekwalificeerd. Te hoog: de afschriktemperatuur is te hoog, de hardbaarheid van het materiaal is te goed, de bovengrens van koolstof- en legeringssamenstelling en de gemiddelde koelsnelheid is te hoog. De kernhardheid is laag: juist het tegenovergestelde.
Voorbeeld delen: 20 # staal 1.5 mm product, vereisten: infiltratielaag 0.2-0.4 mm kern HV250, sommige vrienden in dezelfde branche denken dat de vereisten onredelijk zijn (iedereen zou moeten weten dat de hoogste hardheid van 20 # staalplaatmartensiet zal zijn HV450- 470) Om dit probleem op te lossen, moeten we eerst de kenmerken van dit materiaal begrijpen: inclusief hardbaarheid en hardbaarheid.
Combineer vervolgens de bovengenoemde factoren die van invloed zijn op het bluseffect en vind manieren om te verwarmen en af te koelen. In dit geval is het materiaal gefixeerd. We kunnen een manier vinden uit de afschriktemperatuur en afkoelsnelheid. Deze fabrikant gebruikt toevallig te hoge snelheid olie. Als het verminderen van de afschrikintensiteit niet aan de eisen voldoet, kunnen we ook de afschriktemperatuur verlagen. Methode.
Nog steeds dezelfde zin, van 860-760 graden, (wanneer de temperatuur wordt verlaagd tot een bepaald niveau, zal een bepaalde hoeveelheid ferriet worden neergeslagen uit het onderkoelde austeniet in de kern, en de hardheid zal op dit moment afnemen. , Hoe meer de temperatuur daalt, hoe meer ferriet er neerslaat, hoe meer de hardheid afneemt.
Hier is een herinnering: het is noodzakelijk om de bestaande omstandigheden van de apparatuur volledig te combineren en ophef te maken over de speciale gunstige index van ondiepe doorlaatbaarheid.
3. De gecarboniseerde laag of effectieve gecarboniseerde laag is dieper en ondieper
Zoals eerder vermeld, is de diepte van de infiltratielaag een uitgebreide functie van temperatuur, tijd en koolstofconcentratie. Om dit probleem op te lossen, moeten we beginnen met de verwarmingstemperatuur, de verwarmingssnelheid, de houdtijd, de koelsnelheid en het regelen van de koolstofconcentratiegradiënt in de koolstoflaag. Hoe hoger de temperatuur, hoe langer de tijd en hoe hoger het koolstofpotentieel, hoe dieper de infiltratielaag en vice versa.
Maar in feite is het veel meer dan dat eenvoudig. Om een carbonisatieproces te ontwerpen, moet u ook rekening houden met de apparatuur, ovencapaciteit, oliekarakteristieken, metallografische structuur, materiaalhardbaarheid, de koolstofconcentratiegradiënt in de gecarboniseerde laag en de koelsnelheid. En vele andere factoren. Dit kan worden geanalyseerd met verwijzing naar de eerdere situatie met lage hardheid en zal niet diepgaand worden uitgelegd.
Ten vierde, metallografische organisatie
Overmatig martensiet: de grondstof heeft grove korrels of is niet genormaliseerd en de carboniseringstemperatuur is te hoog. Oplossing: normaliseren of meervoudig normaliseren, (het wordt aanbevolen dat de normalisatietemperatuur 20-30 graden hoger is dan de carbonisatietemperatuur) Overweeg indien mogelijk carbonering en langzame afkoeling en vervolgens opnieuw opwarmen en afschrikken
Overmatige paralympische spelen: de afschriktemperatuur is te hoog, het koolstofgehalte in het austeniet is te hoog (het koolstofpotentieel is te hoog). Oplossing: Volledige diffusie en omstandigheden die het toelaten, kunnen de afschriktemperatuur, temperen bij hoge temperatuur en opnieuw opwarmen en afschrikken, of cryogene behandeling verlagen.
Overmatig carbide: te hoog koolstofgehalte in austeniet (te hoog koolstofpotentieel), te langzaam koelproces, carbideprecipitatie
Oplossing: volledig diffuus, regel de koelsnelheid, verminder het temperatuurverschil tussen carbonering en afschrikken zo min mogelijk en gebruik zo min mogelijk afschrikken bij lage temperatuur of ondertemperatuur. Als dit proces moet worden gebruikt, moet de ovenbelasting worden gecontroleerd. Laten we ons voorstellen: dezelfde apparatuur wordt gecarboneerd bij 920°C en afgeschrikt bij 820°C. De capaciteit van de oven is 1000 kg en 600 kg, en de koelsnelheid is hetzelfde? Welke duurt langer? Welke hardmetaalsoort is hoger?
Vijven. Niet-paard en interne oxidatie
Interne oxidatie: het is de reactie tussen legeringselementen zoals chroom, mangaan en molybdeen in het staal en de oxiderende atmosfeer in de atmosfeer (voornamelijk zuurstof, water, kooldioxide), die de legeringselementen in de matrix uitput, wat resulteert in een afname in de hardbaarheid van het materiaal. De zwarte netwerkstructuur is te zien onder de microscoop, de essentie ervan is de troostietstructuur die wordt verkregen door de uitputting van legeringselementen in de matrix en de afname van de hardbaarheid.
De oplossing is om manieren te vinden om de koelsnelheid van het medium te verhogen, de afschrikintensiteit te verbeteren en de oxiderende atmosfeer in de oven te verminderen (zorg voor de zuiverheid van de carbonerende grondstoffen en hulpmaterialen, minimaliseer de hoeveelheid gebalanceerde lucht, controleer de gebalanceerde luchtvochtigheid en zorg ervoor dat de apparatuur niet lekt Voldoende afzuiging) Conventionele apparatuur is moeilijk te elimineren. Er wordt gezegd dat de lagedruk-vacuümcarboneringsapparatuur volledig kan worden geëlimineerd. Bovendien kan krachtig kogelstralen ook het interne oxidatieniveau verminderen.
Ik heb de meningen van sommige experts gelezen en sommigen zijn van mening dat overmatige ammoniak in het carbonitreerproces ook ernstige non-horseness kan veroorzaken. Ik heb hier persoonlijk een andere mening over: misschien wordt het veroorzaakt door een te hoog watergehalte in ammoniak? Omdat ik ben blootgesteld aan vele carbonitreerprocessen, werd er geen duidelijk niet-paardenweefsel gevonden bij het inspecteren van het product. (Maar ik denk niet dat deze mening verkeerd is) Sommige buitenlandse machine-industrieën hechten veel belang aan interne oxidatie, vooral de tandwielindustrie. In het binnenland moet de diepte over het algemeen niet meer dan 0.02 mm zijn, zoals gekwalificeerd.
Niet-martensitisch: er verschijnt een niet-martensitische structuur op het oppervlak van de gecarboniseerde laag als gevolg van carburatie- of afschrikproblemen na afschrikken, zoals ferriet, bainiet en natuurlijk troostiet van het interne oxidatietype. Het generatiemechanisme is vergelijkbaar met interne oxidatie en de oplossing is vergelijkbaar.
Zes. Vervorming probleem
Dit is een systeemprobleem en het is ook het meest lastige probleem voor onze medewerkers die zich bezighouden met warmtebehandeling. Het wordt gegarandeerd door verschillende aspecten van het koelmedium van het grondstofproces. De bovenstaande inhoud is slechts een persoonlijke ervaring. Als er enige inconsistentie is, kunt u mij corrigeren, dank u.
Bewaar de bron en het adres van dit artikel voor herdruk:Verzameling van veelvoorkomende defecten en preventieve maatregelen bij carboneren en blussen
Minge Spuitgietbedrijf zijn toegewijd aan het vervaardigen en leveren van hoogwaardige en hoogwaardige gietstukken (het assortiment metalen spuitgietonderdelen omvat voornamelijk: Dunwandig spuitgieten,Hot Chamber Spuitgieten,Koude kamer spuitgieten),Ronde Service (Die Casting Service,CNC-bewerking,Matrijzen maken, Oppervlaktebehandeling). Elk aangepast aluminium spuitgieten, magnesium of Zamak / zink spuitgieten en andere gietstukken zijn welkom om contact met ons op te nemen.
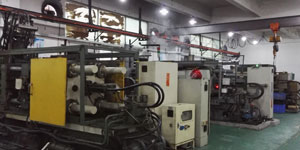
Onder controle van ISO9001 en TS 16949 worden alle processen uitgevoerd door honderden geavanceerde spuitgietmachines, 5-assige machines en andere faciliteiten, variërend van blasters tot Ultra Sonic-wasmachines. Minghe heeft niet alleen geavanceerde apparatuur, maar heeft ook professionele team van ervaren ingenieurs, operators en inspecteurs om het ontwerp van de klant waar te maken.
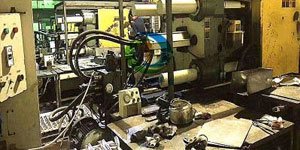
Contractfabrikant van spuitgietwerk. Mogelijkheden zijn onder meer koude kamer aluminium spuitgietonderdelen vanaf 0.15 lbs. tot 6 lbs., snelwissel instellen en machinaal bewerken. Diensten met toegevoegde waarde omvatten polijsten, trillen, ontbramen, stralen, schilderen, plateren, coaten, assembleren en bewerken. Materialen waarmee gewerkt is, zijn legeringen zoals 360, 380, 383 en 413.
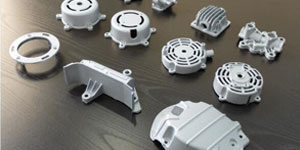
Hulp bij ontwerp van spuitgieten van zink/concurrent engineering. Custom fabrikant van precisie gegoten zink. Miniatuurgietstukken, hogedrukgietstukken, multi-slide gietstukken, conventionele gietstukken, eenheidsmatrijs en onafhankelijke spuitgietstukken en holteverzegelde gietstukken kunnen worden vervaardigd. Gietstukken kunnen worden vervaardigd in lengtes en breedtes tot 24 inch met een tolerantie van +/- 0.0005 inch.
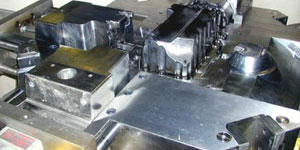
ISO 9001: 2015 gecertificeerde fabrikant van gegoten magnesium. Mogelijkheden zijn onder hoge druk spuitgieten van magnesium tot 200 ton hete kamer en 3000 ton koude kamer, gereedschapsontwerp, polijsten, gieten, machinale bewerking, poeder- en vloeistofverven, volledige QA met CMM-mogelijkheden , montage, verpakking & levering.
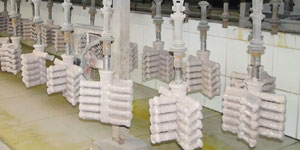
ITAF16949 gecertificeerd. Extra castingservice omvat: investering gieten,zandgieten,Zwaartekracht gieten, Verloren schuimafgietsel,Centrifugaal gieten,Vacuümgieten,Permanent vormgieten,. Mogelijkheden zijn onder meer EDI, technische assistentie, solide modellering en secundaire verwerking.
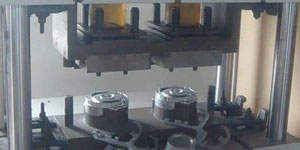
Gietindustrieën Casestudy's over onderdelen voor: auto's, fietsen, vliegtuigen, muziekinstrumenten, waterscooters, optische apparaten, sensoren, modellen, elektronische apparaten, behuizingen, klokken, machines, motoren, meubels, sieraden, mallen, telecom, verlichting, medische apparaten, fotografische apparaten, Robots, sculpturen, geluidsapparatuur, sportuitrusting, gereedschap, speelgoed en meer.
Wat kunnen we u hierna helpen doen?
∇ Ga naar de startpagina voor Spuitgieten China
→Gietonderdelen- Zoek uit wat we hebben gedaan.
→Gerangschikte tips over Spuitgietdiensten
By Minghe Die Casting Fabrikant: |Categorieën: Handige artikelen |Materiaal Tags: Aluminium gieten, Zink gieten, Magnesium gieten, Titanium gieten, Gieten van roestvrij staal, Messing gieten,Brons gieten,Video casten,Geschiedenis van ons bedrijf,Aluminium spuitgieten |Reacties uitgeschakeld