Zeven voorzorgsmaatregelen bij het tekenen van matrijsontwerp
Rekmatrijzen zijn goed voor een zeer groot deel van de gehele stempelmatrijzenindustrie. Onze gewone cups, de schaal op de motor en bijna de meeste producten hebben meer of minder producten die moeten worden uitgerekt. Het ontwerp van de matrijs wil niet zeggen dat deze berekend kan worden volgens het conventionele algoritme. Er zijn te veel processen vol variabelen, vooral het uitrekken van sommige niet-roterende lichamen, wat onbetaalbaar is.
Omdat er te veel factoren zijn om rekening mee te houden bij het ontwerp van de trekmatrijs, zoals de trekcoëfficiënt, of deze de limiet van het materiaal bereikt, de beslissing van de veerkracht, de richting van tekenen, of deze naar boven of naar beneden is , vaak niet Eenmalig gieten vereist veel proeven om het gewenste resultaat te bereiken, en soms kan de mal worden gesloopt. Het opdoen van ervaring in de praktijk is dan ook een grote hulp bij het ontwerpen van de tekenmal.
Daarnaast speelt de maat van het snijmateriaal ook een belangrijke rol bij de proefproductie van de gehele matrijs. Dus meestal, wanneer we wat onregelmatige diepgetrokken onderdelen ontwerpen, reserveren we vaak een lege stap in het ontwerpstadium van de matrijs.
Stretchmateriaal
Wanneer de eisen van de klant aan het materiaal niet erg veeleisend zijn en herhaalde matrijsproeven niet aan de eisen voldoen, kunt u overstappen op een materiaal met goede trekeigenschappen en het opnieuw proberen. Een goed materiaal is het halve succes. Voor stretching mag het niet worden genegeerd. Koudgewalste dunne staalplaten voor trekken omvatten voornamelijk 08Al, 08, 08F, 10, 15 en 20 staalsoorten. De grootste hoeveelheid is 08-staal, dat is onderverdeeld in omrand staal en gedood staal. Het omrande staal is laag in prijs en heeft een goede oppervlaktekwaliteit. De segregatie is ernstiger en heeft de neiging tot "spanningsveroudering". Het is niet geschikt voor onderdelen die hoge eisen stellen aan stempelprestaties en uiterlijk. Dood staal is beter, met uniforme prestaties maar hogere prijs. Het representatieve merk is aluminium gedood staal 08Al. Buitenlands staal heeft Japans SPCC-SD dieptrekstaal gebruikt en de trekeigenschappen zijn beter dan 08Al.
De afwerking van het matrijsoppervlak
Bij dieptrekken zijn de twee zijden van de matrijs en de blanco houder niet voldoende geslepen, vooral bij het tekenen van roestvrijstalen platen en aluminium platen, is de kans groter dat er littekens ontstaan, wat in ernstige gevallen tot trekbreuken kan leiden.
De bepaling van de grootte van de blanco
Meer rimpels en minder scheuren is ons uitgangspunt. Het blanco positioneringsontwerp moet correct zijn. De blanco diameter van het draaiende lichaamsdeel met eenvoudige vorm wordt niet dunner. Hoewel de materiaaldikte verandert, komt deze in principe sterk overeen met de oorspronkelijke dikte. Nabijheid kan worden berekend op basis van het principe dat het gebied van de blanco en het gebied van het uitgerekte deel (als trimmen moet worden toegevoegd) gelijk zijn. De vorm en het proces van uitgerekte onderdelen zijn echter vaak gecompliceerd en soms moeten ze worden uitgedund en uitgerekt. Hoewel er veel 3D-software is die uitvouwberekeningen kan uitvoeren, kan hun nauwkeurigheid niet 100% aan de vereisten voldoen.
Een product moet meerdere processen doorlopen en het eerste proces is over het algemeen een blankingproces. Allereerst is het noodzakelijk om de berekening van het ongevouwen materiaal uit te voeren en een algemeen begrip te hebben van de vorm en grootte van de plano om de totale grootte van de stansmatrijs te bepalen. Verwerk de convexe en concave vormgrootte van de stansvorm niet nadat het vormontwerp is voltooid. Gebruik eerst draadsnijden om de plano te bewerken (wanneer de plano groter is, kan deze worden gefreesd door een freesmachine en vervolgens worden vastgeklemd). Na herhaalde experimenten in het daaropvolgende rekproces, wordt uiteindelijk de grootte van de plano bepaald en vervolgens worden de convexe en concave mallen van de stansmatrijs verwerkt.
Probeer in het omgekeerde proces eerst de tekenmatrijs en verwerk vervolgens de stansrandmaat van de plano, wat de helft van de moeite is.
Trekcoëfficiënt
De uitrekcoëfficiënt is een van de belangrijkste procesparameters bij de berekening van het uitrekproces en wordt meestal gebruikt om de volgorde en het aantal uitrekken te bepalen.
Er zijn veel factoren die de rekcoëfficiënt m beïnvloeden, waaronder materiaaleigenschappen, relatieve dikte van het materiaal, rekmethode (verwijzend naar of er een planohouder is), rektijden, reksnelheid, convexe en concave matrijsfiletradius, smering, enz.
De berekenings- en selectieprincipes van de trekcoëfficiënt m zijn de belangrijkste punten die in verschillende stempelhandleidingen worden geïntroduceerd. Er zijn veel methodes zoals rekenen, tabel opzoeken, rekenen etc., en ik kies ook volgens het boekje. Er zijn geen nieuwe dingen. Lees alstublieft het boek. .
De relatieve dikte van het materiaal, de uitrekmethode (verwijzend naar of er een blanco houder is) en het aantal uitrekken zijn niet eenvoudig aan te passen bij het repareren van de mal, dus je moet voorzichtig zijn. Het is het beste om een collega te zoeken om het te controleren bij het kiezen van de rekcoëfficiënt m.
De keuze van verwerkingsolie
De keuze van de verwerkingsolie is erg belangrijk. De manier om te onderscheiden of de smeerolie geschikt is, is wanneer het product uit de mal wordt gehaald, als de producttemperatuur te hoog is om met de handen te worden aangeraakt, de keuze van de smeerolie en de smeermethode moeten worden heroverwogen, en de smeerolie moet op de holte worden aangebracht. , Of leg een foliezakje op het laken.
Breng in het geval van trekscheuren smeerolie aan op de concave mal (niet aanbrengen op de convexe mal), en het werkstuk is bedekt met een plastic film van 0.013-0.018 mm aan de concave malzijde.
Warmtebehandeling van het werkstuk
Hoewel het niet wordt aanbevolen, is het nog steeds noodzakelijk om te zeggen dat tijdens het rekproces het werkstuk koudverharding zal ondergaan als gevolg van koude plastische vervorming, wat de plasticiteit zal verminderen en de vervormingsweerstand en hardheid zal verhogen. Naast het onredelijke vormontwerp, moet het worden uitgevoerd. Tussengloeien om het metaal zachter te maken en de plasticiteit te herstellen.
Opmerking: In het algemene proces is tussentijds gloeien niet nodig. Het is immers noodzakelijk om de kosten te verhogen. U moet kiezen tussen het verhogen van het proces en het verhogen van de uitgloeiing, en wees voorzichtig!
Gloeien maakt over het algemeen gebruik van gloeien bij lage temperatuur, dat wil zeggen herkristallisatie-gloeien. Bij het uitgloeien zijn er twee dingen waar je op moet letten: ontkoling en oxidatie. We hebben het hier vooral over oxidatie. Nadat het werkstuk is geoxideerd, zal er een oxidehuid ontstaan, die twee nadelen heeft: het maakt de effectieve dikte van het werkstuk dunner en verhoogt de slijtage van de mal.
Wanneer de voorwaarden van het bedrijf niet beschikbaar zijn, wordt over het algemeen gewoon gloeien gebruikt. Om de productie van oxidehuid te verminderen, moet de oven tijdens het gloeien zoveel mogelijk gevuld zijn. Ik heb ook grondmethoden gebruikt:
- Als er weinig onderdelen zijn, kan het met andere onderdelen worden gemengd (uitgangspunt: de parameters van het gloeiproces moeten in principe hetzelfde zijn)
- Plaats het werkstuk in de ijzeren kist en las het vervolgens aan de oven. Om de oxidehuid te verwijderen, moet een beitsbehandeling worden uitgevoerd volgens de situatie na het gloeien.
Wanneer de omstandigheden van het bedrijf beschikbaar zijn, kan gloeien in een stikstofoven worden gebruikt, dat wil zeggen helder gloeien. Als je niet goed kijkt, is de kleur bijna hetzelfde als voor het uitgloeien.
Wanneer er geen andere manier is om met het metaal om te gaan met sterke koudverharding of trekscheuren in de proefmal, voeg dan het tussengloeiproces toe.
Voeg een paar punten toe
- De maat op de producttekening moet zoveel mogelijk aan één zijde worden gemarkeerd om duidelijk te maken of de buitenmaat of de binnenmaat van de holte is gegarandeerd en de binnen- en buitenafmetingen kunnen niet tegelijkertijd worden gemarkeerd. Als de door anderen verstrekte tekeningen dergelijke problemen hebben, moeten ze met hen worden gecommuniceerd. Als ze kunnen worden verenigd, moeten ze worden verenigd. Als ze niet kunnen worden verenigd, moeten ze de assemblagerelatie tussen het werkstuk en andere onderdelen kennen.
- Voor het laatste proces is de maat van het werkstuk buiten, de matrijs is de belangrijkste, de opening wordt verkregen door de maat van de pons te verkleinen; de maat van het werkstuk is binnen, de pons is de hoofdmatrijs en de opening wordt verkregen door de maat van de matrijs te vergroten;
- De hoekradius van de convexe en concave mallen moet zo klein mogelijk worden ontworpen, wat de daaropvolgende malreparatie gemakkelijker zal maken.
- Raadpleeg bij het beoordelen van de oorzaak van het scheuren van het werkstuk: de scheuren veroorzaakt door slechte materiaalkwaliteit zijn meestal gekartelde of onregelmatige vormen, en de scheuren veroorzaakt door het proces en de mal zijn over het algemeen relatief netjes.
- "Meer rimpels, minder scheuren". Pas volgens dit principe de stroom van het materiaal aan. De methoden omvatten het aanpassen van de druk van de planohouder, het vergroten van de trekrups, het trimmen van de straal van de convexe en concave matrijsfilet en het snijden van de procesopening op het werkstuk.
- Om slijtvastheid te garanderen en trekkrassen te voorkomen, moeten de convexe en concave vorm en de blanco houder worden gedoofd, of hard verchroomd, of oppervlakte-TD-behandeling. Wolfraamstaal kan indien nodig worden gebruikt als convexe en concave vorm.
Bewaar de bron en het adres van dit artikel voor herdruk: Zeven voorzorgsmaatregelen bij het tekenen van matrijsontwerp
Minge Spuitgietbedrijf zijn toegewijd aan het vervaardigen en leveren van hoogwaardige en hoogwaardige gietstukken (het assortiment metalen spuitgietonderdelen omvat voornamelijk: Dunwandig spuitgieten,Hot Chamber Spuitgieten,Koude kamer spuitgieten),Ronde Service (Die Casting Service,CNC-bewerking,Matrijzen maken, Oppervlaktebehandeling). Elk aangepast aluminium spuitgieten, magnesium of Zamak / zink spuitgieten en andere gietstukken zijn welkom om contact met ons op te nemen.
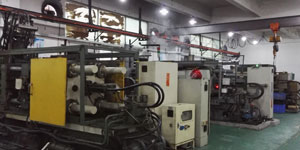
Onder controle van ISO9001 en TS 16949 worden alle processen uitgevoerd door honderden geavanceerde spuitgietmachines, 5-assige machines en andere faciliteiten, variërend van blasters tot Ultra Sonic-wasmachines. Minghe heeft niet alleen geavanceerde apparatuur, maar heeft ook professionele team van ervaren ingenieurs, operators en inspecteurs om het ontwerp van de klant waar te maken.
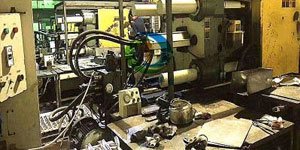
Contractfabrikant van spuitgietwerk. Mogelijkheden zijn onder meer koude kamer aluminium spuitgietonderdelen vanaf 0.15 lbs. tot 6 lbs., snelwissel instellen en machinaal bewerken. Diensten met toegevoegde waarde omvatten polijsten, trillen, ontbramen, stralen, schilderen, plateren, coaten, assembleren en bewerken. Materialen waarmee gewerkt is, zijn legeringen zoals 360, 380, 383 en 413.
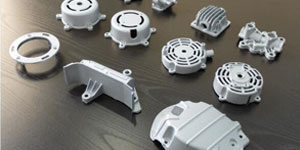
Hulp bij ontwerp van spuitgieten van zink/concurrent engineering. Custom fabrikant van precisie gegoten zink. Miniatuurgietstukken, hogedrukgietstukken, multi-slide gietstukken, conventionele gietstukken, eenheidsmatrijs en onafhankelijke spuitgietstukken en holteverzegelde gietstukken kunnen worden vervaardigd. Gietstukken kunnen worden vervaardigd in lengtes en breedtes tot 24 inch met een tolerantie van +/- 0.0005 inch.
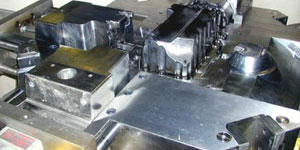
ISO 9001: 2015 gecertificeerde fabrikant van gegoten magnesium. Mogelijkheden zijn onder hoge druk spuitgieten van magnesium tot 200 ton hete kamer en 3000 ton koude kamer, gereedschapsontwerp, polijsten, gieten, machinale bewerking, poeder- en vloeistofverven, volledige QA met CMM-mogelijkheden , montage, verpakking & levering.
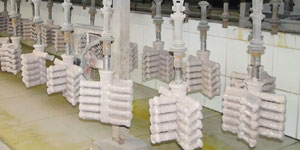
ITAF16949 gecertificeerd. Extra castingservice omvat: investering gieten,zandgieten,Zwaartekracht gieten, Verloren schuimafgietsel,Centrifugaal gieten,Vacuümgieten,Permanent vormgieten,. Mogelijkheden zijn onder meer EDI, technische assistentie, solide modellering en secundaire verwerking.
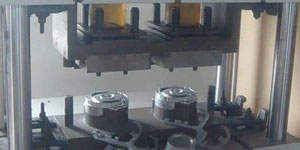
Gietindustrieën Casestudy's over onderdelen voor: auto's, fietsen, vliegtuigen, muziekinstrumenten, waterscooters, optische apparaten, sensoren, modellen, elektronische apparaten, behuizingen, klokken, machines, motoren, meubels, sieraden, mallen, telecom, verlichting, medische apparaten, fotografische apparaten, Robots, sculpturen, geluidsapparatuur, sportuitrusting, gereedschap, speelgoed en meer.
Wat kunnen we u hierna helpen doen?
∇ Ga naar de startpagina voor Spuitgieten China
→Gietonderdelen- Zoek uit wat we hebben gedaan.
→Gerangschikte tips over Spuitgietdiensten
By Minghe Die Casting Fabrikant: |Categorieën: Handige artikelen |Materiaal Tags: Aluminium gieten, Zink gieten, Magnesium gieten, Titanium gieten, Gieten van roestvrij staal, Messing gieten,Brons gieten,Video casten,Geschiedenis van ons bedrijf,Aluminium spuitgieten |Reacties uitgeschakeld