Wat is spuitgieten onder druk? Wat is een spuitgietproces?
Hogedrukgieten is een soort speciale gietmethode met minder snijden en geen snijden die zich snel heeft ontwikkeld in de moderne metaalverwerkingstechnologie. Het is een proces waarbij gesmolten metaal onder hoge druk en hoge snelheid in een mal wordt gevuld en onder hoge druk wordt gekristalliseerd en gestold om een gietstuk te vormen. Hoge druk en hoge snelheid zijn de belangrijkste kenmerken van hogedrukgieten. De algemeen gebruikte druk is tientallen megapascals, de vulsnelheid (binnenste poortsnelheid) is ongeveer 16-80 m/s, en de tijd die gesmolten metaal nodig heeft om de vormholte te vullen, is extreem kort, ongeveer 0.01-0.2 seconden. Omdat de producten die met deze methode worden geproduceerd de voordelen hebben van een hoge productie-efficiëntie, eenvoudige procedures, hogere tolerantieniveaus van gietstukken, goede oppervlakteruwheid en hoge mechanische sterkte, kan het veel bewerkingsprocedures en apparatuur besparen, grondstoffen besparen, enz. , dus het is een casting geworden. Een belangrijk onderdeel van de industrie.
De belangrijkste procesparameters van het spuitgietproces:
1. Inleiding tot het spuitgietproces
- A: Het spuitgietproces is een proces van organische combinatie van de drie elementen van de spuitgietmachine, de spuitgietvorm en de spuitgietlegering.
- B: Het proces waarbij metaal de holte vult tijdens het spuitgieten is een proces waarbij procesfactoren zoals druk, snelheid, temperatuur en tijd dynamisch in evenwicht worden gebracht.
- C: Deze procesfactoren beperken elkaar en vullen elkaar aan. Alleen door deze factoren correct te selecteren en aan te passen om ze op elkaar af te stemmen, kunnen de verwachte resultaten worden bereikt. In het spuitgietproces kan niet alleen de verwerkbaarheid van de gietstructuur, maar ook de geavanceerde aard van de mal worden verkregen. De prestaties en structuur van de spuitgietmachine zijn uitstekend, het aanpassingsvermogen van de selectie van spuitgietlegeringen en de standaardisatie van het smeltproces. Er moet meer aandacht worden besteed aan het belangrijke effect van druk, snelheid en tijd op de kwaliteit van gietstukken.
2. Druk
Het bestaan van druk is het belangrijkste kenmerk dat het spuitgietproces onderscheidt van andere gietmethoden. Druk is de factor die ervoor zorgt dat de gietstukken een compacte structuur en een duidelijk overzicht krijgen; druk kan worden uitgedrukt in injectiekracht en specifieke druk.
2.1 Injectiekracht
Injectiekracht is de kracht die de beweging van de injectiezuiger in het injectiemechanisme van de spuitgieten machine. Injectiekracht is een hoofdparameter die de functie van de spuitgietmachine weerspiegelt. De grootte van de injectiekracht wordt bepaald door het dwarsdoorsnede-oppervlak van de injectiecilinder en de druk van de werkvloeistof in de injectiekamer. De formule van de injectiekracht is als volgt: F druk = P vloeistof XA cilinder
2.2 Specifieke druk
De druk van het gesmolten metaal in de drukkamer per oppervlakte-eenheid wordt de specifieke druk genoemd. De specifieke druk is de verhouding van de injectiekracht tot het dwarsdoorsnede-oppervlak van de drukkamer. De berekeningsformule is als volgt: P-verhouding = P-injectie / A-kamer
De specifieke druk is de uitdrukkingsmethode van de werkelijke kracht van het gesmolten metaal in elke fase van het vulproces, en weerspiegelt het concept van de kracht van het gesmolten metaal in elke fase van het vullen en wanneer het metaal door verschillende dwarsdoorsneden stroomt. gebieden. De specifieke druk tijdens het vullen wordt de vulspecifieke druk of injectiespecifieke druk genoemd. De specifieke druk in de boostfase wordt de specifieke boostdruk genoemd. De grootte van de twee specifieke drukken wordt ook bepaald volgens de injectiekracht.
2.3 De rol en invloed van druk
- A: De vulspecifieke druk is om de stroomweerstand in het poortsysteem en de holte te overwinnen, vooral de weerstand bij de binnenpoort, zodat de metaalvloeistofstroom de vereiste binnenpoortsnelheid kan bereiken.
- B: De vuldruk en de specifieke druk bepalen de druk op het gestolde metaal en de op dat moment gevormde uitpuilende kracht. De invloed van de specifieke druk op de mechanische eigenschappen van het gietstuk: verhoogde specifieke druk, fijne kristallen en verhoogde fijnkorrelige lagen Dikker door verbeterde vuleigenschappen, verbeterde oppervlaktekwaliteit, verminderde porie-effecten en verbeterde treksterkte.
- C: Effect op vulomstandigheden: de legeringssmelt vult de holte onder hoge specifieke druk, de temperatuur van de legering stijgt en de vloeibaarheid verbetert, wat gunstig is voor de verbetering van de kwaliteit van gietstukken.
3. Snelheid
Tijdens het spuitgietproces wordt de injectiesnelheid direct beïnvloed door de druk en samen met de druk speelt het een belangrijke rol in de interne kwaliteit, oppervlaktevereisten en contourhelderheid van het gietstuk. Druk is de basissnelheidsweergave van snelheid is verdeeld in twee soorten: ponssnelheid en ingaatsnelheid.
3.1 De relatie tussen stootsnelheid en geslachtsgemeenschap
Volgens het continuïteitsprincipe moet tegelijkertijd het volume van de metaalstroom die door de legeringsvloeistof stroomt met het dwarsdoorsnede-oppervlak van de drukkamer F1 met de snelheid V1 gelijk zijn aan het volume van de legeringsvloeistof stroomt door de binnenste poort met het dwarsdoorsnede-oppervlak F2 met de snelheid V2 F1 kamer V1 shot = Binnen F2 en binnen V2. Daarom, hoe hoger de injectiesnelheid van de injectiehamer, hoe hoger het metaal dat door de poort stroomt.
3.2 Injectiesnelheid
- A: De injectiesnelheid is verdeeld in twee niveaus. De injectiesnelheid van het eerste niveau wordt ook langzame injectiesnelheid genoemd. Dit snelheidsniveau verwijst naar de bewegingssnelheid van de pons vanaf de eerste beweging totdat de pons het gesmolten metaal in de kamer naar de binnenpoort stuurt. In dit stadium is het nodig om de drukkamer te vullen met het gesmolten metaal in de drukkamer, volgens het principe om de temperatuur van de legeringsvloeistof niet te veel te verlagen, maar ook om het gas in de drukkamer te verwijderen.
- B: De secundaire injectiesnelheid wordt ook wel de snelle injectiesnelheid genoemd. Deze snelheid wordt bepaald door de eigenschappen van de spuitgietmachine. De maximale injectiesnelheid die door de spuitgietmachine wordt gegeven, ligt in het algemeen binnen het bereik van 4-5 m/s.
3.3 De rol en invloed van snelle injectiesnelheid
Het effect en de invloed van een hoge injectiesnelheid op de mechanische eigenschappen van legeringen, het verhogen van de injectiesnelheid, het omzetten van kinetische energie in warmte-energie, het verbeteren van de vloeibaarheid van de legeringssmelt, het helpen elimineren van defecten zoals vloeisporen, koude barrières en het verbeteren van mechanische eigenschappen en oppervlaktekwaliteit, maar wanneer de snelheid te hoog is, zal de legeringssmelt nevelig zijn en met gas worden gemengd, wat in ernstige beknelling en verslechtering van mechanische eigenschappen resulteert.
3.4 Snelheid binnenpoort
De lineaire snelheid wanneer het gesmolten metaal de binnenste poort binnenkomt en in de holte wordt ingebracht, wordt de snelheid van de binnenste poort genoemd; het gebruikelijke bereik van de snelheid van de binnenpoort is 15-70 m/s. De snelheid van de binnenpoort heeft een grote invloed op de mechanische eigenschappen van het gietstuk. Als de snelheid van de binnenpoort te laag is, neemt de sterkte van het gietstuk af; de snelheid neemt toe, de kracht neemt toe; de snelheid is te hoog en de kracht neemt af.
4. temperatuur
In het spuitgietproces speelt temperatuur een belangrijke rol in de thermische toestand van het vulproces en de efficiëntie van de bewerking. De temperatuur waarnaar wordt verwezen in spuitgieten heeft betrekking op gieten, temperatuur en matrijstemperatuur. Temperatuurbeheersing is een belangrijke industriële factor voor het verkrijgen van goede gietstukken. De giettemperatuur van gesmolten metaal verwijst naar de gemiddelde temperatuur wanneer het de holte binnenkomt vanuit de drukkamer. Omdat het onhandig is om de temperatuur van het gesmolten metaal in de vulkamer te meten, wordt deze in het algemeen uitgedrukt als de temperatuur van de warmhoudoven.
4.1 De rol en invloed van de giettemperatuur
De invloed van legeringstemperatuur op de mechanische eigenschappen van gietstukken. Naarmate de temperatuur van de legering toeneemt. De mechanische prestaties zijn verbeterd, maar na een bepaalde limiet verslechteren de prestaties, de belangrijkste redenen zijn:
- A: De oplosbaarheid van gas in de legering neemt toe met de temperatuurstijging. Hoewel het gas in de legering oplost, is het moeilijk om tijdens het spuitgietproces neer te slaan, wat de mechanische eigenschappen beïnvloedt.
- B: Het ijzergehalte neemt toe met de toename van de temperatuur van de legering, wat de vloeibaarheid, grove kristallen vermindert en de prestaties verslechtert
- C: Aluminium- en magnesiumlegeringen worden meer geoxideerd bij toenemende temperatuur, oxiderende insluitsels en verslechtering van de eigenschappen van de legering.
4.2 De rol en invloed van schimmeltemperatuur
Tijdens het spuitgieten heeft de mal een bepaalde temperatuur nodig. De temperatuur van de mal is een andere belangrijke factor in het spuitgietproces, dat een belangrijke rol speelt bij het verbeteren van de productie-efficiëntie en het verkrijgen van hoogwaardige gietstukken.
Tijdens het vulproces heeft de matrijstemperatuur een grote invloed op de metaalvloeistoftemperatuur, viscositeit, vloeibaarheid, vultijd, directe vulstroom, enz. Wanneer de matrijstemperatuur te laag is, wordt de oppervlaktelaag gecondenseerd en de hoge snelheid vloeistofstroom breekt weer, wat resulteert in een oppervlaktelaag Defecten, zelfs als de vormtemperatuur te hoog is, hoewel het gunstig is om een glad oppervlak van het gietstuk te verkrijgen, is het gemakkelijk te krimpen en te deuken
De vormtemperatuur heeft een significant effect op de afkoelsnelheid, kristallijne toestand en krimpspanning van de legeringssmelt.
Als de matrijstemperatuur te laag is, neemt de krimpspanning toe en is het gietstuk vatbaar voor scheuren.
De maltemperatuur heeft een grote invloed op de levensduur van de mal. Intense temperatuurveranderingen vormen een complexe spanningstoestand en frequente spanningsveranderingen veroorzaken vroege scheuren.
De matrijstemperatuur heeft invloed op de maattolerantie van het gietstuk. Als de vormtemperatuur stabiel is, is de dimensionale krimp van het gietstuk ook stabiel en wordt het dimensionale tolerantieniveau ook verbeterd.
5. Tijd
De "tijd" in het spuitgietproces is de vultijd, drukopbouwtijd, drukhoudtijd en malretentietijd. Deze "tijden" zijn alle drie factoren van druk, snelheid en temperatuur, plus de fysieke eigenschappen van gesmolten metaal. , Gietstructuur (vooral wanddikte), vormstructuur (vooral gietsysteem en overloopsysteem) en andere uitgebreide resultaten.
5.1 Vultijd
De tijd die het gesmolten metaal nodig heeft om onder druk de holte binnen te gaan totdat het is gevuld, wordt de vultijd genoemd. De vultijd van gegalvaniseerde onderdelen is 0.02S en de vultijd van brandstofinjectieonderdelen is 0.04S.
5.2 Vultijd
De opbouwtijd van de vuldruk verwijst naar de vulfase van het gesmolten metaal in het vulproces, te beginnen vanaf het moment dat de holte is gevuld, totdat de vuldruk een vooraf bepaalde waarde bereikt, dat wil zeggen vanaf de injectiespecifieke drukstijging tot de toename De tijd die nodig is om de druk op te bouwen
5.3 Houdtijd
Nadat het gesmolten metaal de holte heeft gevuld, wordt de tijdsperiode waarin het gesmolten metaal onder invloed van de boostdruk stolt, de houdtijd genoemd. De functie van de houdtijd is om ervoor te zorgen dat de injectiepons de druk door het niet-gestolde resterende materiaal en het niet-gestolde metaal in het poortgedeelte naar de holte overbrengt, zodat het gestolde metaal onder de druk zal kristalliseren om een dicht gietstuk te verkrijgen.
3. Ontwerp voor spuitgieten
Om het ontstaan van defecte producten en massaproductie van spuitgietonderdelen tegen lage kosten fundamenteel te voorkomen, moet het ontwerp van spuitgietonderdelen geschikt zijn voor spuitgietproductie. Een goed spuitgietontwerp kan de levensduur, productie en productiebetrouwbaarheid van de matrijs garanderen. Met een goede opbrengst worden hieronder de ontwerpprincipes en vereisten van de structuur en het proces van spuitgieten uitgelegd.
1. Vermijd binnenste concave en minimaliseer het aantal zijkerntrekkingen bij het ontwerpen;
2. Ontwerp van de wanddikte van spuitgietstukken
De wanddikte van spuitgietstukken is over het algemeen 2-5 mm. Over het algemeen wordt aangenomen dat een wanddikte van 7 mm of meer niet goed is omdat de sterkte ervan afneemt met de toename van de wanddikte. Bovendien moet het ontwerp van de wanddikte zoveel mogelijk het principe van gelijke wanddikte volgen, voornamelijk om te voorkomen dat het grote verschil tussen de krimpspanning die wordt gegenereerd door lokale hete verbindingen en verschillende diktes interne poriën, vervorming, scheuren en andere defecten veroorzaakt .
3. Rond hoekontwerp van spuitgieten;
Met uitzondering van speciale aanpassingsvereisten, moeten alle delen van het gietstuk worden ontworpen met afgeronde hoeken. De functie van afgeronde hoeken is om spanningsconcentratie en barsten te voorkomen en tegelijkertijd de levensduur van de mal te verlengen. Bovendien, wanneer de onderdelen oppervlaktebehandeling vereisen, kunnen de afgeronde hoeken gelijkmatig worden gecoat. Vloer.
4. Ontwerp van de ontwerphoek van het spuitgieten;
De rol van de trekhoek is om het product soepel uit de vorm te laten komen, de spankracht van de onderdelen te verminderen en te voorkomen dat de onderdelen overbelasten. De minimale helling van de gegoten onderdelen staat in de volgende tabel en de grootste helling moet worden genomen als dit is toegestaan. , Het algemene bereik is 1-3 graden aan één kant.
5. Het ontwerp van de uitwerppositie van het spuitgietproces
Nadat de mal is geopend in het spuitgietproces, wordt het product op de beweegbare mal gewikkeld en moet het worden uitgeworpen door de uitwerppen van de mal. Daarom moet het product voldoende ruimte hebben om de uitwerppin te plaatsen. De diameter van de uitwerppen van het gegoten product is over het algemeen groter dan 5 mm en kleiner dan 5 mm. Het is vaak kapot tijdens de productie, dus het wordt niet aanbevolen. Overweeg bij het ontwerpen van gegoten producten of er voldoende uitwerpruimte en positie is. Probeer het gebruik van een speciaal gevormde vingerhoed te vermijden en gebruik een ronde vingerhoed. Let tegelijkertijd op de positie van de vingerhoed en de muur. Voldoende afstand, doorgaans groter dan 3 mm.
6. Verminder het ontwerp van de daaropvolgende verwerking van spuitgietstukken;
Spuitgietonderdelen kunnen een hoge maatnauwkeurigheid bereiken, dus de meeste oppervlakken en onderdelen vereisen geen mechanische bewerking en kunnen direct worden geassembleerd en gebruikt. Tegelijkertijd wordt mechanische verwerking om de volgende twee redenen niet ondersteund. Een daarvan is dat het oppervlak van het gietstuk hard en slijtvast is en na verwerking verloren gaat. Deze gekoelde laag, de tweede is dat er meestal poriën in het spuitgietwerk zitten. De verspreide kleine poriën hebben geen invloed op het gebruik. Na verwerking worden de poriën blootgesteld om het uiterlijk en de gebruiksfunctie te beïnvloeden. Zelfs als er speciale vereisten zijn die mechanische verwerking vereisen, moet het worden gebruikt. Beheers de bewerkingstoegift redelijk, verminder de bewerkingstijd en de kans op lekkende luchtgaten. Over het algemeen wordt de bewerkingstoegift onder 0.8 geregeld. Om de mechanische verwerking te minimaliseren, is het vereist om de tolerantie van de tekening redelijk te formuleren om de installatie van de onderdelen te garanderen. Een ongeschikt tolerantiebereik zal de latere bewerking vergroten. Ten tweede vermindert een redelijk ontwerp de krimp en vervorming van onderdelen. Ten derde kunnen schuine montagegaten worden overwogen voor stompe gaten.
7. Ingebed ontwerp in spuitgietontwerp die
Metalen of niet-metalen inzetstukken kunnen in spuitgietonderdelen worden gegoten, voornamelijk om de lokale sterkte en slijtvastheid te verbeteren of om moeilijk te vormen binnenholtes te vormen. Het deel waar het inzetstuk in het metaal is ingebed, moet zo zijn ontworpen dat het niet draait en axiale beweging voorkomt. Overweeg het gemak van het inbrengen van het inzetstuk in de mal en de stabiliteit van het weerstaan van de impact van gesmolten metaal
5. Gevallen van het oplossen van de kwaliteitsproblemen van matrijzenafgietsels.
Het probleem van het niet zien van licht bij de verwerking van 100 gezichten uit de schaal
1.1 Statusonderzoek
1.2 De reden waarom de verwerking het licht niet ziet
1.2.1 Gebruik bij het verwerken van de schaal eerst de B1-, B2- en B3-eindvlakken als referentieoppervlak om het bewegende matrijsoppervlak te verwerken en gebruik vervolgens het bewerkte bewegende matrijsoppervlak als het referentieoppervlak om het statische matrijsoppervlak te verwerken. Na meting van het onzichtbare deel blijkt dat het beweegbare matrijsoppervlak na bewerking een afschuining is (zoals weergegeven in onderstaande figuur). Vergeleken met het normale bewerkte deel, wordt het beweegbare matrijsoppervlak van het onzichtbare deel lokaal 1 mm meer verwerkt. Het wordt veroorzaakt door een onjuiste klemming van het B2-referentievlak of vervorming van het referentievlak tijdens de verwerking.
1.3. Redenen voor vervorming van B2-datumgat:
1.3.1 De dikte van de partiële braam zorgt ervoor dat het kopvlak van het B2-referentiegat hoger wordt. De wanddikte van het onzichtbare deel B2 is 8 mm, en de twee wanddiktes van het normaal verwerkte deel B zijn hetzelfde. De dikte van de muur verandert weinig. De dikte van de braam is niet de reden voor de toename van het eindoppervlak van het B2-referentiegat.
1.3.2 De kernen van gaten B1, B2 en B3 op de mal zijn bevestigd en er is geen kernterugtrekking gevonden. Het kernretraiteprobleem kan worden geëlimineerd.
1 De bult bij het B3-gat veroorzaakt de vervorming. Observeer het geretourneerde defecte onderdeel. Er zijn serieuze hobbels bij het B2-gat en het is geen nieuwe hobbel. De hobbel is de belangrijkste oorzaak van de vervorming bij het B2-gat.
1.4 Conclusie
Conclusie: Door de botsing is het B2-gat vervormd naar de statische matrijszijde, waardoor de B2 hoger wordt wanneer het beweegbare matrijsoppervlak wordt verwerkt. Het beweegbare matrijsoppervlak wordt verwerkt tot een afschuining en de lokale verwerking is 1 mm meer; bij het verwerken van het statische matrijsoppervlak wordt het beweegbare matrijsoppervlak gebruikt als het referentievlak. Het statische matrijsdeel dat overeenkomt met de multi-verwerkingspositie van de beweegbare matrijs heeft geen verwerkingshoeveelheid, waardoor de statische matrijszijverwerking onzichtbaar is.
1.5 Verbetermaatregelen
1.5.1 Wanneer u de onderdelen in de spuitgietwerkplaats en de reinigingswerkplaats plaatst, plaatst u ze zorgvuldig en netjes om te voorkomen dat de gietstukken stoten en volgt u het proces strikt. Leg tussen elke laag gietstukken twee lagen karton. Afdeling opslag en transport. Voorkom tijdens de omzet dat de vorkheftruck de onderdelen raakt en voorkom dat de onderdelen stoten als gevolg van ongepaste vorktransportmethoden en overmatige transportsnelheid.
1.5.2 Maak de afsteekbramen op tijd schoon om te dikke afsteekbramen te voorkomen.
2.2 Redenanalyse
2.2.1 De gatdiameter van het onderdeel waar de poriën verschijnen in het 701 # gat van Lishell is q26, de gatdiameter na verwerking is p27.9, de bewerkingstoeslag is 0.95 mm, de bewerkingstoeslag is groot en de poriën zijn eenvoudig verschijnen.
2.3 Conclusie
Conclusie: de 701# kerntemperatuur is te hoog, deze bevindt zich in de diepe holte en de uitlaat is slecht, en de bewerkingstoegift is te groot, waardoor het 701#-gat na verwerking vatbaar is voor poriën.
2.4 Verbetermaatregelen
2.4.1 De technische afdeling die is ontworpen om water toe te voegen aan het 701#-gat om de kerntemperatuur te verlagen; verander de vormtekening, voeg een overloopgroef toe bij het 701#-gat om het uitlaateffect te versterken; verander de kerntekening en verander de 701#-gatbewerkingstoegift Verlaagd van 0.9 mm naar 0.7 mm.
Bewaar de bron en het adres van dit artikel voor herdruk: Wat is spuitgieten onder druk? Wat is een spuitgietproces?
Minge Spuitgietbedrijf zijn toegewijd aan het vervaardigen en leveren van hoogwaardige en hoogwaardige gietstukken (het assortiment metalen spuitgietonderdelen omvat voornamelijk: Dunwandig spuitgieten,Hot Chamber Spuitgieten,Koude kamer spuitgieten),Ronde Service (Die Casting Service,CNC-bewerking,Matrijzen maken, Oppervlaktebehandeling). Elk aangepast aluminium spuitgieten, magnesium of Zamak / zink spuitgieten en andere gietstukken zijn welkom om contact met ons op te nemen.
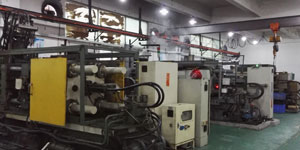
Onder controle van ISO9001 en TS 16949 worden alle processen uitgevoerd door honderden geavanceerde spuitgietmachines, 5-assige machines en andere faciliteiten, variërend van blasters tot Ultra Sonic-wasmachines. Minghe heeft niet alleen geavanceerde apparatuur, maar heeft ook professionele team van ervaren ingenieurs, operators en inspecteurs om het ontwerp van de klant waar te maken.
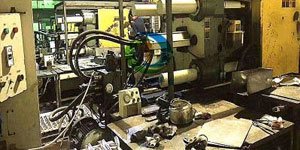
Contractfabrikant van spuitgietwerk. Mogelijkheden zijn onder meer koude kamer aluminium spuitgietonderdelen vanaf 0.15 lbs. tot 6 lbs., snelwissel instellen en machinaal bewerken. Diensten met toegevoegde waarde omvatten polijsten, trillen, ontbramen, stralen, schilderen, plateren, coaten, assembleren en bewerken. Materialen waarmee gewerkt is, zijn legeringen zoals 360, 380, 383 en 413.
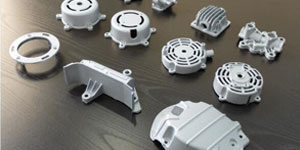
Hulp bij ontwerp van spuitgieten van zink/concurrent engineering. Custom fabrikant van precisie gegoten zink. Miniatuurgietstukken, hogedrukgietstukken, multi-slide gietstukken, conventionele gietstukken, eenheidsmatrijs en onafhankelijke spuitgietstukken en holteverzegelde gietstukken kunnen worden vervaardigd. Gietstukken kunnen worden vervaardigd in lengtes en breedtes tot 24 inch met een tolerantie van +/- 0.0005 inch.
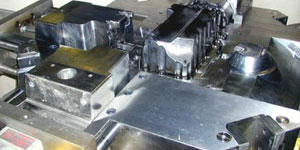
ISO 9001: 2015 gecertificeerde fabrikant van gegoten magnesium. Mogelijkheden zijn onder hoge druk spuitgieten van magnesium tot 200 ton hete kamer en 3000 ton koude kamer, gereedschapsontwerp, polijsten, gieten, machinale bewerking, poeder- en vloeistofverven, volledige QA met CMM-mogelijkheden , montage, verpakking & levering.
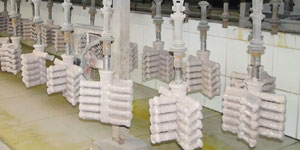
ITAF16949 gecertificeerd. Extra castingservice omvat: investering gieten,zandgieten,Zwaartekracht gieten, Verloren schuimafgietsel,Centrifugaal gieten,Vacuümgieten,Permanent vormgieten,. Mogelijkheden zijn onder meer EDI, technische assistentie, solide modellering en secundaire verwerking.
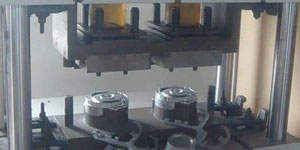
Gietindustrieën Casestudy's over onderdelen voor: auto's, fietsen, vliegtuigen, muziekinstrumenten, waterscooters, optische apparaten, sensoren, modellen, elektronische apparaten, behuizingen, klokken, machines, motoren, meubels, sieraden, mallen, telecom, verlichting, medische apparaten, fotografische apparaten, Robots, sculpturen, geluidsapparatuur, sportuitrusting, gereedschap, speelgoed en meer.
Wat kunnen we u hierna helpen doen?
∇ Ga naar de startpagina voor Spuitgieten China
→Gietonderdelen- Zoek uit wat we hebben gedaan.
→Gerangschikte tips over Spuitgietdiensten
By Minghe Die Casting Fabrikant: |Categorieën: Handige artikelen |Materiaal Tags: Aluminium gieten, Zink gieten, Magnesium gieten, Titanium gieten, Gieten van roestvrij staal, Messing gieten,Brons gieten,Video casten,Geschiedenis van ons bedrijf,Aluminium spuitgieten |Reacties uitgeschakeld