De voorzorgsmaatregelen voor het gieten van waterglaszand:
Wat zijn de factoren die de "veroudering" van waterglas beïnvloeden? Hoe de "veroudering" van waterglas te elimineren?
Het vers bereide waterglas is een echte oplossing. Tijdens het opslagproces zal het kiezelzuur in het waterglas echter condensatiepolymerisatie ondergaan, die geleidelijk zal polycondenseren van de echte oplossing tot een macromoleculaire kiezelzuuroplossing en uiteindelijk een kiezelzuurgel wordt. Daarom is waterglas eigenlijk een heterogeen mengsel dat bestaat uit polykiezelzuur met verschillende polymerisatiegraden, dat gemakkelijk wordt beïnvloed door zijn modulus, concentratie, temperatuur, elektrolytgehalte en bewaartijd.
Tijdens opslag ondergaan de moleculen van waterglas condensatiepolymerisatie om een gel te vormen, en de hechtsterkte ervan neemt geleidelijk af met de verlenging van de opslagtijd. Dit fenomeen wordt "veroudering" van waterglas genoemd.
Het fenomeen "veroudering" kan worden verklaard door de volgende twee reeksen testgegevens: waterglas met hoge modulus (M=2.89, ρ=1.44 g/cm3) na 20, 60, 120, 180, 240 dagen opslag, de CO2 uitgehard waterglas wordt geblazen. De droge treksterkte van zand daalt dienovereenkomstig met 9.9%, 14%, 23.5%, 36.8% en 40%; natriumsilicaat met lage modulus (M=2.44, ρ=1.41 g/cm3) wordt na drogen 7, 30, 60 en 90 dagen bewaard. De treksterkte nam af met respectievelijk 4.5%, 5%, 7.3% en 11%.
De bewaartijd van waterglas heeft weinig effect op de initiële sterkte van estergehard waterglas zelfhardend zand, maar heeft wel een significant effect op de latere sterkte. Volgens metingen wordt het verminderd met ongeveer 60% voor waterglas met een hoge modulus en 15-20% voor waterglas met een lage modulus. . De reststerkte neemt ook af met de verlenging van de opslagtijd.
Tijdens de opslag van waterglas verlopen de polycondensatie en depolymerisatie van polykiezelzuur tegelijkertijd, wordt het molecuulgewicht disproportioneel en tenslotte wordt een multi-gedispergeerd systeem gevormd waarin mono-orthokiezelzuur en colloïdale deeltjes naast elkaar bestaan. Dat wil zeggen, tijdens het verouderingsproces van waterglas, is de polymerisatiegraad van kiezelzuur onevenredig en neemt het gehalte aan monoorthokiezelzuur en hoog polykiezelzuur toe met de verlenging van de opslagtijd. Als gevolg van condensatiepolymerisatie en depolymerisatiereactie van waterglas tijdens opslag, wordt de hechtsterkte verminderd, dat wil zeggen dat het fenomeen van "veroudering" optreedt.
De belangrijkste factoren die de "veroudering" van waterglas beïnvloeden zijn: bewaartijd, modulus en concentratie van waterglas. Hoe langer de bewaartijd, hoe hoger de modulus en hoe groter de concentratie, hoe ernstiger de "veroudering".
Het al lang bestaande waterglas kan op verschillende manieren worden aangepast om "veroudering" te elimineren en het waterglas te herstellen naar de prestaties van zoetwaterglas:
1. Fysieke wijziging
De veroudering van waterglas is een spontaan proces waarbij langzaam energie vrijkomt. De fysieke modificatie van "verouderd" waterglas is het gebruik van magnetisch veld, ultrageluid, hoge frequentie of verwarming om energie te leveren aan het waterglassysteem en de hoge polymerisatie van polysilicaatlijm te bevorderen. De deeltjes depolymeriseren opnieuw en bevorderen de homogenisering van het molecuulgewicht van polykiezelzuur, waardoor het verouderingsverschijnsel, dat het mechanisme van fysieke modificatie is, wordt geëlimineerd. Na behandeling met een magnetisch veld wordt bijvoorbeeld de sterkte van natriumsilicaatzand met 20-30% verhoogd, wordt de toegevoegde hoeveelheid natriumsilicaat met 30-40% verminderd, wordt CO2 bespaard, wordt de inklapbaarheid verbeterd en zijn er goede economische voordelen.
Het nadeel van fysieke modificatie is dat het niet duurzaam is, en de hechtsterkte zal afnemen bij opslag na behandeling, dus het is geschikt om zo snel mogelijk na behandeling in de gieterij te gebruiken. Vooral voor waterglas met M>2.6 is de concentratie kiezelzuurmoleculen groot en na fysieke modificatie en depolymerisatie zal het relatief snel polycondenseren. Het is het beste om het direct na de behandeling te gebruiken.
2. Chemische modificatie
Chemische modificatie is het toevoegen van een kleine hoeveelheid verbindingen aan het waterglas, deze verbindingen bevatten allemaal carboxyl, amide, carbonyl, hydroxyl, ether, amino en andere polaire groepen, die worden geadsorbeerd aan kiezelzuurmoleculen of colloïdale deeltjes door waterstofbruggen of statische elektriciteit. Oppervlakte, verander de potentiële energie van het oppervlak en het solvatatievermogen, verbeter de stabiliteit van polykiezelzuur, waardoor wordt voorkomen dat "veroudering" doorgaat.
Door bijvoorbeeld polyacrylamide, gemodificeerd zetmeel, polyfosfaat, enz. aan het waterglas toe te voegen, kunnen betere resultaten worden bereikt.
Het opnemen van organisch materiaal in gewoon waterglas of zelfs gemodificeerd waterglas kan verschillende functies vervullen, zoals: het veranderen van de viskeuze stromingseigenschappen van waterglas; verbetering van de modelleringsprestaties van waterglasmengsels; het verhogen van de hechtsterkte om het waterglas absoluut toegevoegd te maken De hoeveelheid wordt verminderd; de plasticiteit van de kiezelzuurgel wordt verbeterd; de reststerkte wordt verminderd, waardoor het waterglaszand beter geschikt is voor gietijzer en non-ferro legeringen.
3. Fysisch-chemische modificatie
Fysieke modificatie is geschikt voor "verouderd" waterglas en kan direct na modificatie worden gebruikt. Chemische modificatie is geschikt voor het verwerken van zoetwaterglas en het gemodificeerde waterglas kan lange tijd worden bewaard. De combinatie van fysieke modificatie en chemische modificatie kan ervoor zorgen dat het waterglas een blijvend modificatie-effect heeft. Bijvoorbeeld het toevoegen van polyacrylamide aan de autoclaaf om het "verouderde" waterglas te modificeren heeft een goed effect. Onder hen worden de druk en de druk van de autoclaaf gebruikt. Roeren is een fysieke modificatie en het toevoegen van polyacrylamide is een chemische modificatie.
Hoe CO2 blazen voorkomen gehard natriumsilicaat zand schimmel (kern) oppervlakte krijten?
Nadat soda-natriumsilicaatzand met CO2 is gehard en een tijdje is gelaten, verschijnt soms een substantie zoals rijp op het oppervlak van de onderste mal (kern), die de oppervlaktesterkte van de plaats ernstig zal verminderen en gemakkelijk zand zal produceren wasfouten tijdens het gieten. Volgens analyse is het hoofdbestanddeel van deze witte stof NaHCO3, dat kan worden veroorzaakt door overmatig vocht of CO2 in het natriumsilicaatzand. De reactie is als volgt:
- Na2CO3+H2O → NaHCO3 + NaOH
- Na2O+2CO2+H2O→2NaHCO3
- NaHCO3 migreert gemakkelijk naar buiten met vocht, waardoor poederachtig ijs op het oppervlak van de mal en de kern ontstaat.
De oplossing is als volgt:
- Zorg ervoor dat het vochtgehalte van het natriumsilicaatzand niet te hoog is (vooral in het regenseizoen en de winter).
- De tijd voor het blazen van CO2 mag niet te lang zijn.
- De geharde mal en kern mogen niet lang worden geplaatst en moeten op tijd worden gevormd en gegoten.
- Het toevoegen van ongeveer 1% (massafractie) van de siroop met een dichtheid van 1.3 g/cm3 aan het natriumsilicaatzand kan effectief voorkomen dat het oppervlak verpoedert.
Hoe de vochtopnameweerstand van de waterglaszandvorm (kern) te verbeteren?
De door CO2 of verhitting uitgeharde sodawaterglas zandkern wordt in de natte kleivorm geassembleerd. Als het niet op tijd wordt gegoten, zal de sterkte van de zandkern sterk afnemen, niet alleen kruipen, zelfs instorten; het wordt opgeslagen in een vochtige omgeving. Ook wordt de sterkte van de zandkern aanzienlijk verminderd. Tabel 1 toont de sterktewaarden van CO2 geharde natriumwaterglas zandkernen bij plaatsing in een omgeving met een relatieve vochtigheid van 97% gedurende 24 uur. De reden voor het verlies van sterkte bij opslag in een vochtige omgeving is te wijten aan de rehydratatie van natriumwaterglas. De Na+ en OH- in de natriumsilicaatbindmiddelmatrix absorberen vocht en erodeert de matrix, waardoor uiteindelijk de silicium-zuurstofbinding Si-O-Si wordt verbroken, wat resulteert in een significante afname van de hechtsterkte van het natriumsilicaatzand.
De maatregelen om dit probleem op te lossen zijn:
- 1. Lithiumwaterglas wordt toegevoegd aan natriumwaterglas, of Li2CO3, CaCO3, ZnCO3 en andere anorganische additieven worden toegevoegd aan natriumwaterglas, omdat relatief onoplosbare carbonaten en silicaten kunnen worden gevormd en vrije natriumionen kunnen worden verminderd. absorptieweerstand van het natriumwaterglasbindmiddel kan worden verbeterd.
- 2. Voeg een kleine hoeveelheid organisch materiaal of organisch materiaal met oppervlakteactieve functie toe aan het natriumwaterglas. Wanneer het bindmiddel is uitgehard, kunnen de hydrofiele Na+- en OH-ionen in de natriumwaterglasgel worden vervangen door organische hydrofobe groepen, of gecombineerd met elkaar, verbetert de blootgestelde organische hydrofobe base de vochtabsorptie.
- 3. Verbeter de modulus van waterglas, omdat de vochtbestendigheid van waterglas met hoge modulus sterker is dan die van waterglas met lage modulus.
- 4. Voeg zetmeelhydrolysaat toe aan natriumsilicaatzand. Een betere methode is om zetmeelhydrolysaat te gebruiken om natriumwaterglas te modificeren.
4 Wat zijn de kenmerken van het CO2 blazend gehard water glas-alkalisch fenolhars zand composiet proces?
In de afgelopen jaren hebben sommige kleine en middelgrote ondernemingen dringend het harszandproces nodig om de kwaliteit van staalgietstukken te verbeteren. Vanwege de beperkte economische capaciteit zijn ze echter niet in staat om harszandregeneratieapparatuur aan te schaffen en kan het oude zand niet worden gerecycled en hergebruikt, wat resulteert in hoge productiekosten. Om een effectieve manier te vinden om de kwaliteit van gietstukken te verbeteren zonder de kosten te veel te verhogen, kunnen de proceskenmerken van CO2 blazend gehard natriumsilicaatzand en CO2 blazend gehard alkalisch fenolharszand worden gecombineerd, en CO2 blazen gehard natriumsilicaat-alkalisch fenolhars kan worden gebruikt. Het harszandcompoundproces maakt gebruik van alkalisch fenolharszand als oppervlaktezand en waterglaszand als rugzand, terwijl CO2 wordt geblazen voor verharding.
De fenolhars die wordt gebruikt in CO2-alkalisch fenolharszand wordt gemaakt door polycondensatie van fenol en formaldehyde onder de werking van een sterke alkalische katalysator en toevoeging van een koppelingsmiddel. De PH-waarde is ≥13 en de viscositeit is ≤500mPa•s. De hoeveelheid fenolhars die aan het zand wordt toegevoegd is 3% tot 4% (massafractie). Wanneer het CO2-debiet 0.8 ~ 1.0 m3/h is, is de beste blaastijd 30 ~ 60 s; als de blaastijd te kort is, zal de uithardingssterkte van de zandkern laag zijn; als de blaastijd te lang is, zal de sterkte van de zandkern niet toenemen en is het verspild gas.
CO2-Alkalisch fenolharszand bevat geen schadelijke elementen zoals N, P, S, enz., dus gietdefecten zoals poriën, microscheurtjes in het oppervlak, enz. Die door deze elementen worden veroorzaakt, worden geëlimineerd; schadelijke gassen zoals H2S en SO2 komen niet vrij tijdens het gieten, wat gunstig is voor de bescherming van het milieu; Goede inklapbaarheid, gemakkelijk schoon te maken; hoge maatnauwkeurigheid; hoge productie-efficiëntie.
Het CO2-blazende geharde waterglas-alkalische fenolharszandcomposietproces kan op grote schaal worden gebruikt in staalgietstukken, ijzergietstukken, koperlegeringen en gietstukken van lichte legeringen.
Het samengestelde proces is een eenvoudig en handig proces. Het proces is als volgt: meng eerst harszand en natriumsilicaatzand afzonderlijk en doe ze vervolgens in twee zandemmers; voeg dan het gemengde harszand toe als oppervlaktezand in de zandbak. En pond, de dikte van de oppervlaktezandlaag is over het algemeen 30-50 mm; dan wordt waterglaszand toegevoegd om het achterzand te vullen en te verdichten; ten slotte wordt CO2-gas in de mal geblazen om uit te harden.
De diameter van de blaasbuis is over het algemeen 25 mm en het hardbare bereik is ongeveer 6 keer de diameter van de blaasbuis.
De blaastijd is afhankelijk van de grootte, vorm, gasstroom en oppervlakte van de uitlaatplug van de zandvorm (kern). Over het algemeen wordt de blaastijd binnen 15 ~ 40s geregeld.
Na het blazen van de harde zandvorm (kern) kan de mal worden genomen. De sterkte van de zandvorm (kern) stijgt snel. Borstel de verf binnen een half uur na het nemen van de mal, en sluit de doos voor het gieten na 4 uur.
Het composietproces is met name geschikt voor staalgietfabrieken die geen apparatuur voor het regenereren van harszand hebben en gietstukken van hoge kwaliteit moeten produceren. Het proces is eenvoudig en gemakkelijk te controleren en de kwaliteit van de geproduceerde gietstukken is gelijk aan die van andere harszandgietstukken.
CO2 blazend gehard natriumsilicaatzand kan ook worden gecompoundeerd met CO2 blazend gehard natriumpolyacrylaatharszand voor de productie van diverse hoogwaardige gietstukken.
Wat zijn de voor- en nadelen van het CO2-organische estercomposiet gehard natriumsilicaatzandproces?
In de afgelopen jaren heeft het met CO2-organische estercomposiet geharde natriumsilicaatzandproces een trend van groeiende toepassingen. Het proces is als volgt: voeg een bepaalde hoeveelheid organische ester toe tijdens het mengen van zand (meestal de helft van de normaal benodigde hoeveelheid of 4 ~ 6% van het gewicht van waterglas); nadat de modellering is voltooid, blaast u CO2 om uit te harden tot de sterkte van de vormloslating (drukweerstand is over het algemeen vereist) De sterkte is ongeveer 0.5 MPa); na het ontvormen blijft de organische ester uitharden en neemt de sterkte van het vormzand sneller toe; nadat de CO2 is geblazen en 3 ~ 6 uur is geplaatst, kan de zandvorm worden gecombineerd en gegoten.
Het uithardingsmechanisme is:
Wanneer het waterglaszand CO2 blaast, onder invloed van het gasdrukverschil en het concentratieverschil, zal het CO2-gas in alle richtingen van het vormzand proberen te stromen. Nadat het CO2-gas in contact komt met het waterglas, reageert het er onmiddellijk mee om een gel te vormen. Door het diffusie-effect is de reactie altijd van buiten naar binnen en vormt de buitenste laag eerst een gelfilm, waardoor het CO2-gas en het waterglas niet verder kunnen reageren. Daarom is het in korte tijd, ongeacht welke methode wordt gebruikt om CO2-gas te beheersen, onmogelijk om het te laten reageren met al het waterglas. Volgens analyse, wanneer het vormzand de beste blaassterkte bereikt, is het waterglas dat reageert met CO2-gas ongeveer 65%. Dit betekent dat het waterglas zijn hechteffect niet volledig uitoefent en dat minimaal 35% van het waterglas niet reageert. De organische esterverharder kan een uniform mengsel vormen met het bindmiddel en kan de bindingswerking van het bindmiddel ten volle spelen. Alle delen van het kernzand bouwen met dezelfde snelheid kracht op.
Door meer waterglas toe te voegen, zal de uiteindelijke sterkte van de zandvorm toenemen, maar ook de reststerkte zal toenemen, waardoor het moeilijk wordt om het zand schoon te maken. Wanneer de toegevoegde hoeveelheid waterglas te klein is, is de uiteindelijke sterkte te klein en kan deze niet voldoen aan de gebruikseisen. Bij de feitelijke productie wordt de toegevoegde hoeveelheid waterglas in het algemeen geregeld op ongeveer 4%.
Wanneer alleen organische ester wordt gebruikt om uit te harden, is de algemene hoeveelheid toegevoegde organische ester 8-15% van de hoeveelheid waterglas. Bij composietverharding wordt geschat dat ongeveer de helft van het waterglas is uitgehard wanneer CO2 wordt geblazen en ongeveer de helft van het waterglas nog niet is uitgehard. Daarom is het passender dat de hoeveelheid organische esters 4 tot 6% van de hoeveelheid waterglas uitmaakt.
De composietverhardingsmethode kan de dubbele voordelen van CO2-verharding en organische esterverharding ten volle benutten, en kan het bindende effect van waterglas volledig uitoefenen om een hoge verhardingssnelheid, vroege vormlossing, hoge sterkte, goede inklapbaarheid en lage kosten te bereiken. Uitgebreide werking.
Bij het uithardingsproces van CO2-organische estercomposiet moet echter 0.5 tot 1% meer waterglas worden toegevoegd dan bij de eenvoudige uithardingsmethode met organische ester, wat de regeneratie van het gebruikte waterglaszand moeilijker zal maken.
Waarom is het gemakkelijk om kleverig zand te produceren wanneer het natriumsilicaatzandproces wordt gebruikt om ijzeren gietstukken te produceren? Hoe het te voorkomen?
Wanneer de zandvorm (kern) gemaakt van natriumsilicaatzand wordt gebruikt voor het gieten van gietijzeren gietstukken, wordt vaak ernstig kleverig zand geproduceerd, wat de toepassing ervan bij de productie van gietijzer beperkt.
Het Na2O, SiO2 in het natriumsilicaatzand en het ijzeroxide geproduceerd door het vloeibare metaal tijdens het gieten vormen laagsmeltend silicaat. Zoals eerder vermeld, als deze verbinding meer smeltbaar amorf glas bevat, is de hechtkracht tussen deze glaslaag en het oppervlak van het gietstuk erg klein en is de krimpcoëfficiënt anders dan die van het metaal. Grote spanning is eenvoudig van het oppervlak van het gietstuk te verwijderen zonder dat zand blijft plakken. Als de verbinding gevormd op het oppervlak van het gietstuk een hoog gehalte aan SiO2 en een laag gehalte aan FeO, MnO, enz. heeft, heeft de gestolde structuur in feite een kristallijne structuur, die stevig wordt gecombineerd met het gietstuk, wat resulteert in kleverig zand .
Wanneer het natriumsilicaatzand wordt gebruikt om ijzeren gietstukken te produceren, vanwege de lage giettemperatuur en het hoge koolstofgehalte van de ijzeren gietstukken, worden ijzer en mangaan niet gemakkelijk geoxideerd, en de resulterende kleverige zandlaag heeft een kristallijne structuur en het is moeilijk om een geschikte laag tussen de ijzeren gietstukken en de kleverige zandlaag aan te brengen. De dikte van de ijzeroxidelaag verschilt van het harszand tussen het gietstuk en de kleverige zandlaag, die een heldere koolstoffilm kan produceren door harspyrolyse bij het produceren van ijzeren gietstukken, dus de kleverige zandlaag is niet gemakkelijk te verwijderen.
Om de productie van sodawaterglaszand uit de productie van gietijzeren gietstukken te voorkomen, kunnen geschikte coatings worden gebruikt. Zoals verf op waterbasis, moet het oppervlak na het schilderen worden gedroogd, dus sneldrogende verf op alcoholbasis is het beste.
In het algemeen kunnen ijzergietstukken ook een geschikte hoeveelheid steenkoolpoeder (zoals 3% tot 6%) (massafractie) aan het natriumsilicaatzand toevoegen, zodat de pyrolyse van het steenkoolpoeder tussen het gietstuk en de zandlaag kan produceren een heldere koolstoffilm. Het wordt niet bevochtigd door metalen en hun oxiden, zodat de kleverige zandlaag gemakkelijk van het gietstuk wordt afgepeld.
Wordt natriumsilicaatzand naar verwachting milieuvriendelijk vormzand zonder afvalzandafvoer?
Waterglas is kleurloos, geurloos en niet giftig. Het veroorzaakt geen ernstige problemen als het de huid en kleding aanraakt en afspoelt met water, maar spatten in de ogen moet worden vermeden. Waterglas heeft geen irriterende of schadelijke gassen die vrijkomen bij het mengen, modelleren, uitharden en gieten van zand en er is geen zwart- en zuurvervuiling. Als het proces echter onjuist is en er te veel natriumsilicaat wordt toegevoegd, zal de inklapbaarheid van het natriumsilicaatzand niet goed zijn en zal het stof tijdens het zandreinigen wegvliegen, wat ook vervuiling zal veroorzaken. Tegelijkertijd is het moeilijk om oud zand te regenereren en veroorzaakt de lozing van afvalzand alkalische vervuiling van het milieu.
Als deze twee problemen kunnen worden overwonnen, kan natriumsilicaatzand milieuvriendelijk vormzand worden met in principe geen afvalzandafvoer.
De fundamentele maatregel om deze twee problemen op te lossen, is de hoeveelheid toegevoegd waterglas te verminderen tot minder dan 2%, wat in principe het zand kan afschudden. Wanneer de hoeveelheid toegevoegd waterglas wordt verminderd, wordt ook het resterende Na2O in het oude zand verminderd. Met een relatief eenvoudige droge regeneratiemethode is het mogelijk om het resterende Na2O in het circulerende zand onder de 0.25% te houden. Dit teruggewonnen zand kan voldoen aan de toepassingsvereisten van enkelvoudig vormzand voor kleine en middelgrote stalen gietstukken. Op dit moment, zelfs als het oude natriumsilicaatzand niet de dure en gecompliceerde natte methode gebruikt om te regenereren, maar de relatief eenvoudige en goedkope droge methode wordt gebruikt, kan het volledig worden gerecycled, er wordt in principe geen afvalzand geloosd en de verhouding van zand tot ijzer Het kan worden teruggebracht tot minder dan 1:1.
Hoe natriumsilicaatzand effectief te regenereren?
Als het resterende Na2O in het oude natriumsilicaatzand te hoog is, zal het vormzand na toevoeging van het natriumsilicaat aan het zand niet genoeg bruikbare tijd hebben en zal de ophoping van teveel Na2O de vuurvastheid van het kwartszand verslechteren. Daarom moet het resterende Na2O zoveel mogelijk worden verwijderd bij het regenereren van het gebruikte natriumsilicaatzand.
Bewaar de bron en het adres van dit artikel voor herdruk: De voorzorgsmaatregelen voor het gieten van waterglaszand:
Minge Spuitgietbedrijf zijn toegewijd aan het vervaardigen en leveren van hoogwaardige en hoogwaardige gietstukken (het assortiment metalen spuitgietonderdelen omvat voornamelijk: Dunwandig spuitgieten,Hot Chamber Spuitgieten,Koude kamer spuitgieten),Ronde Service (Die Casting Service,CNC-bewerking,Matrijzen maken, Oppervlaktebehandeling). Elk aangepast aluminium spuitgieten, magnesium of Zamak / zink spuitgieten en andere gietstukken zijn welkom om contact met ons op te nemen.
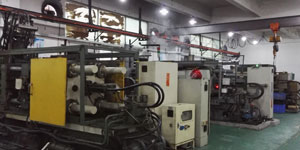
Onder controle van ISO9001 en TS 16949 worden alle processen uitgevoerd door honderden geavanceerde spuitgietmachines, 5-assige machines en andere faciliteiten, variërend van blasters tot Ultra Sonic-wasmachines. Minghe heeft niet alleen geavanceerde apparatuur, maar heeft ook professionele team van ervaren ingenieurs, operators en inspecteurs om het ontwerp van de klant waar te maken.
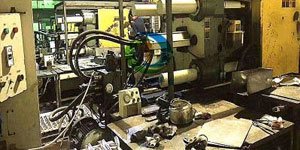
Contractfabrikant van spuitgietwerk. Mogelijkheden zijn onder meer koude kamer aluminium spuitgietonderdelen vanaf 0.15 lbs. tot 6 lbs., snelwissel instellen en machinaal bewerken. Diensten met toegevoegde waarde omvatten polijsten, trillen, ontbramen, stralen, schilderen, plateren, coaten, assembleren en bewerken. Materialen waarmee gewerkt is, zijn legeringen zoals 360, 380, 383 en 413.
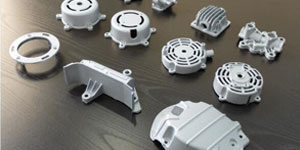
Hulp bij ontwerp van spuitgieten van zink/concurrent engineering. Custom fabrikant van precisie gegoten zink. Miniatuurgietstukken, hogedrukgietstukken, multi-slide gietstukken, conventionele gietstukken, eenheidsmatrijs en onafhankelijke spuitgietstukken en holteverzegelde gietstukken kunnen worden vervaardigd. Gietstukken kunnen worden vervaardigd in lengtes en breedtes tot 24 inch met een tolerantie van +/- 0.0005 inch.
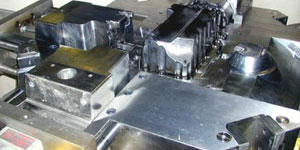
ISO 9001: 2015 gecertificeerde fabrikant van gegoten magnesium. Mogelijkheden zijn onder hoge druk spuitgieten van magnesium tot 200 ton hete kamer en 3000 ton koude kamer, gereedschapsontwerp, polijsten, gieten, machinale bewerking, poeder- en vloeistofverven, volledige QA met CMM-mogelijkheden , montage, verpakking & levering.
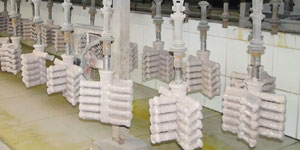
ITAF16949 gecertificeerd. Extra castingservice omvat: investering gieten,zandgieten,Zwaartekracht gieten, Verloren schuimafgietsel,Centrifugaal gieten,Vacuümgieten,Permanent vormgieten,. Mogelijkheden zijn onder meer EDI, technische assistentie, solide modellering en secundaire verwerking.
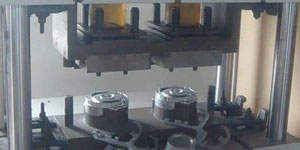
Gietindustrieën Casestudy's over onderdelen voor: auto's, fietsen, vliegtuigen, muziekinstrumenten, waterscooters, optische apparaten, sensoren, modellen, elektronische apparaten, behuizingen, klokken, machines, motoren, meubels, sieraden, mallen, telecom, verlichting, medische apparaten, fotografische apparaten, Robots, sculpturen, geluidsapparatuur, sportuitrusting, gereedschap, speelgoed en meer.
Wat kunnen we u hierna helpen doen?
∇ Ga naar de startpagina voor Spuitgieten China
→Gietonderdelen- Zoek uit wat we hebben gedaan.
→Gerangschikte tips over Spuitgietdiensten
By Minghe Die Casting Fabrikant: |Categorieën: Handige artikelen |Materiaal Tags: Aluminium gieten, Zink gieten, Magnesium gieten, Titanium gieten, Gieten van roestvrij staal, Messing gieten,Brons gieten,Video casten,Geschiedenis van ons bedrijf,Aluminium spuitgieten |Reacties uitgeschakeld