De relatie tussen stalen gietscheuren en insluitsels in staal
De insluitsels die ontstaan tijdens het smeltproces van gesmolten staal zijn een van de belangrijkste oorzaken van scheuren in stalen gietstukken. Om de insluitingen in het gesmolten staal tijdens het smeltproces te verminderen, is het noodzakelijk om de smeltactiviteiten zoals deoxidatie, ontzwaveling, onzuiverheidsverwijdering en ontgassing te versterken, en de nodige maatregelen te nemen in de pollepel achter de oven, zoals het toevoegen van zeldzame aardmetalen, enz. De vorm van de insluitsels kan het bestaan van insluitsels verminderen en de scheuren van de stalen gietstukken beter elimineren.
1 Soorten en oorzaken van insluitsels in staal
Insluitsels in staal verwijzen voornamelijk naar niet-metalen insluitsels in staal. Algemeen wordt aangenomen dat niet-metalen insluitsels in staal vaak in de volgende vormen voorkomen: oxiden: FeO, Fe2, M nO, A3, SiO 2, M gO, enz.; Sulfiden: M nS, FeS, enz.; Silicaten: FeSiO 3, M nSiO 2, FeO ·Al4 ·SiO4, enz.; Nitriden: AlN, Si2N 3 enzovoort.
Niet-metalen insluitsels in staal komen voort uit twee aspecten: ten eerste worden ze gegenereerd tijdens het smeltproces, dat wil zeggen dat de deoxidatieproducten van ferrolegeringen worden toegevoegd tijdens het tappen en de secundaire oxidatieproducten van gesmolten staal en lucht tijdens het gietproces, die endogene insluitsels genoemd. Dergelijke insluitsels zijn over het algemeen fijne deeltjes en gelijkmatig verdeeld in het staal; ten tweede worden ze om verschillende redenen van buitenaf binnengebracht, de zogenaamde buitenlandse insluitsels. Dergelijke insluitsels zijn vaak onregelmatig van vorm, groot van formaat en ongelijk verdeeld, wat de oorzaak is van scheuren. De belangrijkste reden is dat het schadelijker is voor staal.
Endogene insluitsels worden voornamelijk geproduceerd in de volgende situaties:
- ①Tijdens het smeltproces werden de deoxidatieproducten niet volledig geëlimineerd, of daalde de temperatuur tijdens het gietproces, en de deoxidatieproducten die door de voortgezette reactie werden gegenereerd, hadden geen tijd om te drijven en in het gesmolten staal achter te blijven. Sommige komen voor in de matrixstructuur van het staal als kleine deeltjes, en andere aggregeren dan in grote deeltjes van Al2O3), en sommige bestaan in het staal in een vaste oplossingstoestand (zoals M nO, F eO);
- ②Tijdens het tappen en gieten wordt het gesmolten staal geoxideerd in contact met lucht en zuurstof en staal. De middelste elementen vormen samen secundaire oxiden en blijven in het gesmolten staal; tijdens het stollen van het gesmolten staal worden FeS, FeO, enz. met een laag smeltpunt uiteindelijk neergeslagen in de korrelgrenzen en tussen de dendrieten als gevolg van de "selectieve kristallisatie" van het gesmolten staal.
Vreemde insluitsels: Dit soort insluitsels is voornamelijk betrokken bij het zand, slakken en schimmelslakken die door de grondstoffen worden aangevoerd. De vuurvaste materialen van het gietsysteem worden geschuurd en geërodeerd door het gesmolten staal. Ze worden vastgehouden in het gesmolten staal en zijn meestal insluitingen van grote deeltjes. Dingen.
Niet-metalen insluitsels worden opgelost in gesmolten staal bij hoge temperaturen, of bestaan alleen in gesmolten staal, maar naarmate de temperatuur daalt en de samenstelling, gasdruk en andere omstandigheden veranderen, zullen de oorspronkelijke insluitsels opgelost in gesmolten staal worden. De onafhankelijke fasen worden gescheiden en verzameld op de korrelgrenzen tijdens het kristallisatieproces, en worden de kleine eenheden die de verbinding tussen de gietstalen matrix doorsnijden en de initiële bron van scheuren vormen, waardoor potentiële scheuren worden gevormd.
2 De relatie tussen hoofdinsluitingen en gietstalen scheuren en maatregelen om te verminderen
Van de niet-metalen insluitsels is de belangrijkste oorzaak van scheuren in stalen gietstukken sulfide-insluitingen, en het heeft vaak een wisselwerking met andere factoren om de neiging van stalen gietstukken om te barsten te vergroten. In gietstaal zijn sulfide-insluitingen onderverdeeld in drie categorieën:
- Type Ⅰ-bolvormig;
- Type Ⅱ-punt keten interkristallijne film;
- Type Ⅲ-willekeurig verdeelde scherpe hoek.
- Onder hen zijn type II-insluitingen het schadelijkst voor staal, gevolgd door type III en type I het minst.
De sulfide-insluitingen zijn gerelateerd aan de mate van deoxidatie van het staal en de hoeveelheid achtergebleven aluminium in het staal. Wanneer de hoeveelheid vaste aluminiumoplossing laag is en het zuurstofresidu klein is, kunnen Type I-insluitsels worden verkregen.
De deoxidator heeft een grote invloed op de vorming van insluitsels en de prestaties van staal. De desoxiderende werking van de samengestelde desoxidator is beter dan die van een enkele deoxidator. Dit komt omdat de insluitsels gevormd door de samengestelde deoxidator groter zijn, die gemakkelijk te drijven en te verwijderen zijn. Als het gesmolten staal onvoldoende gedeoxideerd is, zullen waarschijnlijk poriedefecten optreden en zullen er waarschijnlijk scheuren optreden in de stalen gietstukken. De hoeveelheid aluminium die wordt gebruikt voor de uiteindelijke deoxidatie is echter net voldoende voor deoxidatie en er is geen residu. Het vaste-oplossingsgehalte van aluminium is laag en de resterende zuurstof is klein, wat type II-insluitingen zal produceren. In het algemeen, als overmatig aluminium wordt gebruikt voor deoxidatie, zullen type III insluitsels worden verkregen. Het is vermeldenswaard dat als overmatig aluminium wordt gebruikt, er meer aluminiumnitride-insluitingen zullen worden gevormd en neerslaan langs de korrelgrenzen, wat leidt tot "steenachtige" brosse breuken en verslechtering van de prestaties van het staal. Daarom is het onredelijk om overmatig aluminium te gebruiken voor deoxidatie. De hoeveelheid aluminium die tijdens de staalproductie wordt toegevoegd en de hoeveelheid achtergebleven aluminium in het staal mag niet te laag of te hoog zijn.
Deoxidatie met aluminium is een veelgebruikte methode voor deoxidatie van staal. Twee soorten deoxidatieprocessen worden meestal gebruikt bij industriële productie, de ene is het aluminiumdeoxidatieproces en de andere is het gecontroleerde aluminiumdeoxidatieproces. De eerste is om aluminium te gebruiken om de opgeloste zuurstof in het staal volledig te verwijderen en vervolgens om zoveel mogelijk Al2O3-insluitingen te verwijderen door middel van verschillende roermethoden; de laatste is om alleen silicomanganese te gebruiken voor grove deoxidatie en het aluminium en aluminium in het staal strikt te controleren. Calciumgehalte om de samenstelling, aard en morfologie van de in het staal neergeslagen oxide-insluitingen te controleren. De primaire deoxidatiesnelheid van de eerste is groter dan 90 en het deoxidatieproduct is voornamelijk Al2O3; de hoeveelheid deoxidatieproducten die door de laatste deoxidatie worden geprecipiteerd, is sterk verminderd en het primaire deoxidatieproduct is voornamelijk SiO2.
De vreemde insluitsels kunnen volgens hun bron worden verwijderd door overeenkomstige maatregelen te nemen, terwijl de endogene insluitsels moeten worden gecontroleerd door de nieuwe technologie van het deoxidatieproces en het calciumbehandelingsproces.
Tijdens het raffineren van pollepels is het blazen van meer en kleinere argonbellen in het gesmolten staal gunstig voor de verwijdering van de eerste deoxidatieproducten.
Om de insluitingen in het staal beter te verwijderen en scheuren te verminderen, neemt het smeltproces de volgende maatregelen.
- (1) Bereid grondstoffen goed voor om vreemde insluitsels te voorkomen.
- (2) Adopteer redelijke staalproductieprocessen: zoals het toepassen van redelijke zuurstofblaas- en stroomdistributieprocessen, zorgen voor een bepaalde ontkolingssnelheid om insluitsels te laten drijven, en het handhaven van goede ovenomstandigheden.
- (3) Gebruik samengestelde desoxidatiemiddel in plaats van enkelvoudige desoxidatiemiddel.
- (4) Zeldzame aardmetalen worden toegevoegd aan de pollepel achter de oven om de vorm van insluitsels te veranderen en insluitsels te verminderen om de neiging van stalen gietstukken om te barsten te verminderen en de vloeibaarheid van gesmolten staal te vergroten.
- (5) Om het verwijderen van insluitsels te vergemakkelijken, moet het gesmolten staal, naast het waarborgen van voldoende temperatuur van het gesmolten staal, na het tikken op de juiste manier in de gietpan worden geplaatst.
Daarnaast zijn het gebruik van hoogwaardige vuurvaste materialen om ervoor te zorgen dat het gietsysteem schoon is of het gebruik van filters ook belangrijke maatregelen om insluitsels te verminderen.
3 Zeldzame aarde-composietmodificatiebehandeling om insluitsels in staal te verwijderen en methoden toe te voegen
Het toevoegen van zeldzame aarde heeft een goed effect op het verwijderen van insluitsels in staal. Zeldzame aarde wordt voornamelijk gebruikt om sulfide in staal te beheersen en kan deoxideren en ontzwavelen.
In de gegoten toestand zijn de M nS-insluitingen in het staal elliptisch of ongeveer cirkelvormig. De grotere elliptische insluitsels zijn samengestelde insluitsels gevormd door M nO als de kern en de buitenste laag omgeven door M nS of M nSO. Na toevoeging van de zeldzame aarde zijn de verdeling en samenstelling van de as-cast insluitsels veranderd en zijn de MnS insluitsels vervangen door ongeveer bolvormige fijne en verspreide zeldzame aarde insluitsels. Om zeldzame aarden goed te verminderen, moeten zeldzame aardoxiden worden gemengd met sterke reductiemiddelen (Ca-Si, Ca-B) en vervolgens aan het gesmolten staal worden toegevoegd om de rol van modificatiebehandeling te spelen. Met de juiste modificatiebehandeling kunnen sulfide-insluitsels bolvormige insluitsels vormen met een hoog smeltpunt, lage plasticiteit en stabiele thermodynamische eigenschappen. Men kan zeggen dat zeldzame aarde en calcium goede ontzwavelingsmiddelen en goede modificatoren zijn voor sulfide-insluitingen. Het gebruik van RE-Ca-composietbehandeling kan beter deoxideren, ontzwavelen, zuiveren en verslechteren, de vorm en distributie van niet-metalen insluitsels regelen en de uitgebreide mechanische eigenschappen van gegoten laaggelegeerd staal verbeteren.
Om het effect van zeldzame aarde op de eigenschappen van gietstaal verder te onderzoeken, werd het gebruik van zeldzame aarde-composietmodificatiebehandeling in ZG 35CrM o-staal getest. De gebruikte zeldzame aardlegering is YX 20, met 20.53 RE, 40.95 Si; Si-Ca samenstelling Bevat 26.45 Ca en 57.07 Si.
De samengestelde behandeling keurt de methode goed om in de pollepel toe te voegen. Wanneer de zeldzame aarde wordt toegevoegd, moet het gesmolten staal volledig worden gedeoxideerd om verbranding te voorkomen wanneer de zeldzame aarde wordt toegevoegd, en om te voorkomen dat het reageert met het vuurvaste materiaal van de gietpan. Zeldzame aardmetalen moeten goed worden gebakken voordat ze worden toegevoegd. De specifieke methode is om de hoeveelheid RE en Si-Ca te bepalen aan de hand van de hoeveelheid gesmolten staal in de pollepel en hoeveel zwavel deze bevat, RE en Si-Ca in kleine stukjes te breken en gelijkmatig te mengen, ze te bedekken met ijzeren platen , en plaats snel aluminium voor definitieve desoxidatie. Het gesmolten staal na de slak wordt constant geroerd en de behandelingstemperatuur wordt binnen het bereik van 1 600 - 1 650 gehouden, vervolgens wordt de slak verwijderd en blijft deze 1 tot 2 minuten staan om te gieten.
Volgens verschillende terugwinningspercentages wordt de juiste waarde van RE/S voor het resterende zeldzame aard- en zwavelgehalte in gesmolten staal gecontroleerd om een goed degradatie-effect te verkrijgen. Studies hebben aangetoond dat wanneer RE/S ≈3, M nS-insluitsels volledig kunnen verslechteren; wanneer RE/S <3, kan slechts gedeeltelijke achteruitgang worden bereikt; wanneer S ≈ 0.02 in staal, RE/S = 1.8 ~ Verslechteringseffect is het beste na 2.5 uur.
De rol van de behandeling van zeldzame aardecomposietmodificatie is voornamelijk het zuiveren van gesmolten staal en het beheersen van de vorm van insluitsels, het verminderen van insluitsels en tegelijkertijd het elimineren van de Widmanstatten-structuur, het verfijnen van korrels en microlegeringen. Dat wil zeggen, na toevoeging van het zeldzame-aarde-composietmiddel, kan het niet alleen deoxideren en ontzwavelen, maar ook wanneer RE/S ≥3 ~ 6, MnS bolvormige insluitsels zal worden, waardoor de schade van zwavel wordt verminderd en heet kraken wordt voorkomen of verminderd. Zeldzame aarde is effectief in het veranderen van de insluitsels in gesmolten staal. De vorm van het object vermindert scheuren en het effect is duidelijk.
De tandwielen geproduceerd met ZG 35C rM o-staal hebben een hoog schrootpercentage vóór de samengestelde modificatiebehandeling, maar na de samengestelde modificatiebehandeling wordt het schrootpercentage met meer dan 40% verlaagd, wat duidelijke resultaten heeft opgeleverd en goede economische voordelen heeft opgeleverd.
4 Conclusie
- (1) Insluitingen in gesmolten staal zijn een van de belangrijkste oorzaken van scheuren in gietstaal. Verschillende insluitsels hebben verschillende manieren om scheuren te produceren.
- (2) Om niet-metalen insluitsels in gesmolten staal te verminderen en scheuren in stalen gietstukken te voorkomen, is het noodzakelijk om goed werk te leveren in de aspecten van de voorbereiding van grondstoffen, het smeltproces, deoxidatie, het staan van de pollepel en de modificatiebehandeling.
- (3) Het gebruik van gecombineerde modificatoren van zeldzame aarde en calcium voor composietmodificatie van gesmolten staal is een effectieve methode om niet-metalen insluitsels in gesmolten staal te verminderen, hun vorm te veranderen en scheuren in stalen gietstukken te verminderen.
Bewaar de bron en het adres van dit artikel voor herdruk: De relatie tussen stalen gietscheuren en insluitsels in staal
Minge Spuitgietbedrijf zijn toegewijd aan het vervaardigen en leveren van hoogwaardige en hoogwaardige gietstukken (het assortiment metalen spuitgietonderdelen omvat voornamelijk: Dunwandig spuitgieten,Hot Chamber Spuitgieten,Koude kamer spuitgieten),Ronde Service (Die Casting Service,CNC-bewerking,Matrijzen maken, Oppervlaktebehandeling). Elk aangepast aluminium spuitgieten, magnesium of Zamak / zink spuitgieten en andere gietstukken zijn welkom om contact met ons op te nemen.
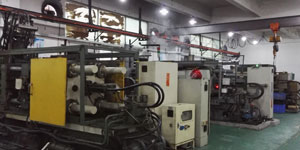
Onder controle van ISO9001 en TS 16949 worden alle processen uitgevoerd door honderden geavanceerde spuitgietmachines, 5-assige machines en andere faciliteiten, variërend van blasters tot Ultra Sonic-wasmachines. Minghe heeft niet alleen geavanceerde apparatuur, maar heeft ook professionele team van ervaren ingenieurs, operators en inspecteurs om het ontwerp van de klant waar te maken.
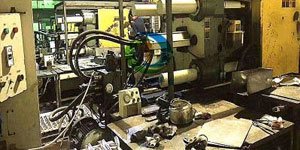
Contractfabrikant van spuitgietwerk. Mogelijkheden zijn onder meer koude kamer aluminium spuitgietonderdelen vanaf 0.15 lbs. tot 6 lbs., snelwissel instellen en machinaal bewerken. Diensten met toegevoegde waarde omvatten polijsten, trillen, ontbramen, stralen, schilderen, plateren, coaten, assembleren en bewerken. Materialen waarmee gewerkt is, zijn legeringen zoals 360, 380, 383 en 413.
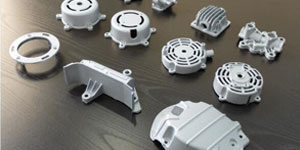
Hulp bij ontwerp van spuitgieten van zink/concurrent engineering. Custom fabrikant van precisie gegoten zink. Miniatuurgietstukken, hogedrukgietstukken, multi-slide gietstukken, conventionele gietstukken, eenheidsmatrijs en onafhankelijke spuitgietstukken en holteverzegelde gietstukken kunnen worden vervaardigd. Gietstukken kunnen worden vervaardigd in lengtes en breedtes tot 24 inch met een tolerantie van +/- 0.0005 inch.
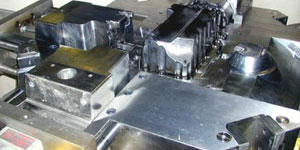
ISO 9001: 2015 gecertificeerde fabrikant van gegoten magnesium. Mogelijkheden zijn onder hoge druk spuitgieten van magnesium tot 200 ton hete kamer en 3000 ton koude kamer, gereedschapsontwerp, polijsten, gieten, machinale bewerking, poeder- en vloeistofverven, volledige QA met CMM-mogelijkheden , montage, verpakking & levering.
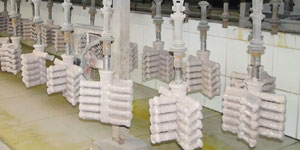
ITAF16949 gecertificeerd. Extra castingservice omvat: investering gieten,zandgieten,Zwaartekracht gieten, Verloren schuimafgietsel,Centrifugaal gieten,Vacuümgieten,Permanent vormgieten,. Mogelijkheden zijn onder meer EDI, technische assistentie, solide modellering en secundaire verwerking.
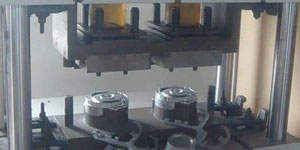
Gietindustrieën Casestudy's over onderdelen voor: auto's, fietsen, vliegtuigen, muziekinstrumenten, waterscooters, optische apparaten, sensoren, modellen, elektronische apparaten, behuizingen, klokken, machines, motoren, meubels, sieraden, mallen, telecom, verlichting, medische apparaten, fotografische apparaten, Robots, sculpturen, geluidsapparatuur, sportuitrusting, gereedschap, speelgoed en meer.
Wat kunnen we u hierna helpen doen?
∇ Ga naar de startpagina voor Spuitgieten China
→Gietonderdelen- Zoek uit wat we hebben gedaan.
→Gerangschikte tips over Spuitgietdiensten
By Minghe Die Casting Fabrikant: |Categorieën: Handige artikelen |Materiaal Tags: Aluminium gieten, Zink gieten, Magnesium gieten, Titanium gieten, Gieten van roestvrij staal, Messing gieten,Brons gieten,Video casten,Geschiedenis van ons bedrijf,Aluminium spuitgieten |Reacties uitgeschakeld