De belangrijkste punten van het nieuwe type multifunctionele aluminium oliebehuizing spuitgieten:
Gericht op de ontwikkelingstrend van automotoren naar lichter gewicht en integratie, worden de belangrijkste punten van een nieuw type spuitgietoliecarter nadrukkelijk toegelicht. Ontwerptechnologiepunten voor spuitgieten zijn verdeeld in drie delen, waarbij verschillende gietmethoden en nieuwe technologieën worden gebruikt om producten te ontwerpen; vanaf de controlepunten van het spuitgietproces wordt elke factor die de productkwaliteit in het productieproces beïnvloedt, gecontroleerd om het aantal productdefecten te verminderen. Door deze twee aspecten van controle is het productkwalificatiepercentage meer dan 97% en is de massaproductie stabiel.
Met de snelle ontwikkeling van de auto-industrie worden er hogere eisen gesteld aan de materialen, het ontwerp en de fabricage van onderdelen, en zijn hoge integratie, hoge prestaties en lage kosten de ontwikkelingstrend geworden. Zowel het oliecarter als het onderste cilinderblok zijn belangrijke onderdelen van de automotor. Door de balansas van het onderste cilinderblok en de opvang- en filterfunctie van het oliecarter op hetzelfde onderdeel te integreren, worden het gewicht en het volume van de motor effectief verminderd. Vanwege de complexe structuur en grote veranderingen in de wanddikte moet het echter worden opgesplitst in verschillende producten en afzonderlijk worden verwerkt en vervolgens worden gecombineerd en verwerkt, wat resulteert in problemen bij de productie van het product.
Het geïntegreerde oliecarter van een in dit onderwerp bestudeerde motor bevat drie gietstukken: het oliecarterlichaam, het balanslagerdeksel en een enkelvoudig balanslagerdeksel. Met A380 gemodificeerd legeringsmateriaal is de gemiddelde wanddikte van het gietstuk 3 mm, de minimale wanddikte is 2.5 mm en de massa van de blanco is 10.74 kg. De binnenholte moet lekvrij zijn onder 300 kPa, en de oliedoorgang lekt niet bij 600 kPa en de temperatuur overschrijdt 60 ℃. Lekkage, gebruikt in 1.5T-motoren, met een jaarlijkse productie van 400,000 stuks, wat een typisch complex oliecartergietwerk is.
Technische punten van spuitgieten
1.1 Loperontwerp
Gieten 1 heeft een driezijdig gietontwerp, maar richt zich op het algehele gieten aan één kant, zoals weergegeven in figuur 1. Aangezien het product lang is (de lengte omhoog en omlaag bereikt 437.2 mm), kan het driezijdige gietontwerp het probleem van een lang proces effectief verlichten, om het product in verschillende gebieden te vullen. Aangezien de totale wanddikte van het product echter dikker is en er veel verhoogde inzetstukken zijn in de gietpositie, om te voorkomen dat de vloeibaarheid van het gesmolten aluminium wordt geblokkeerd, wordt de vulling aan één kant versterkt en wordt de dwarsdoorsnede als geheel geleidelijk versmald om de stroom van het gesmolten aluminium te versnellen. Ontwerp spruw.
Gietstuk 2 is een balanslagerdeksel, met een relatief eenvoudige vorm, alleen de middelste twee oliegroeven van de balansas zijn dik. Gebaseerd op het eenvoudige stroompatroon van het gesmolten aluminium, om kosten te besparen en de effectieve uitvoersnelheid van het gesmolten aluminium te verhogen, wordt een enkelzijdig gietschema toegepast en wordt de poort in het wanddiktegebied geplaatst voor toevoer, zoals weergegeven in figuur 2.
Gietstuk 3 is een enkele balansas-tegelafdekking met een kleiner deel (afmeting 63 mm) × 15 mm × Het ontwerp van één holte en acht vormen wordt gebruikt voor vullen en gieten, zoals getoond in Fig. 3.
1.2 Uitlaatmethode
Voor complexe casting 1 wordt hoogvacuüm gebruikt voor afzuiging. Gieten 2, met behulp van een gewoon uitlaatblok van het "wasbord". Gieten 3 neemt direct de slakkenzak en het uitlaatkanaal van de vormkern aan de staart van de slakkenzak over. De hoofdlijnen van de uitlaattechniek van gietstuk 1 worden hier benadrukt.
Aangezien de hogedrukoliedoorgangen en oliefilters van de gietstukken geconcentreerd zijn in de waterstaart, is het uitlaateffect van de waterstaart de belangrijkste factor die de interne kwaliteit van deze locaties bepaalt. Gietstuk 1 gebruikt een hoogvacuümuitlaat om de luchtdruk in de onderdrukzone van de waterstaart van het gietstuk te verminderen. Allereerst moet het volume van de vacuümtank ≥ 800 L worden geselecteerd (800 L is hier meer dan 10 keer het volume van de vorm die de holte en de trog bevat) om snel het onderdrukkanaal te vormen. Ten tweede moet de pijpleiding die de vorm en de vacuümmachine verbindt, worden afgedicht en luchtdicht, en de vacuümgraad van de pijpleiding moet binnen 2 000 Pa worden gehouden. Ten derde wordt de vorm afgedicht met een afdichtband en zijn alle vingerhoed- en kernpennen bedekt met afdichtmiddel. Nadat de vorm is gesloten, moet het holtevacuüm binnen 4 000 Pa worden gehouden. Kies ten slotte de beste productie van de verzegelde pons, of gebruik de verlengde versie van de pons om het afdichtingsgebied van de pons te vergroten en het lekken van lucht in de holte effectief te verminderen.
1.3 Vormtemperatuur
Vanwege de kenmerken van een hoog vacuüm is het gesmolten aluminium niet volledig gevuld in overeenstemming met de theoretische vloeibare toestand (zie figuur 4), en het gesmolten aluminium kan op bepaalde plaatsen gemakkelijk snel stollen wanneer het erin wordt gezogen, waardoor spuitgietfouten ontstaan, zoals spuitgietporiën, krimpgaten en scheuren. Het product van dit gietstuk 1 begint te vacumeren wanneer de pons naar de positie van 410 mm beweegt (de aluminiumvloeistofvolheid bereikt de vereiste van 70%) en sluit het vacuüm op de positie van 540 mm. Tijd), de vacuümslag is 130 mm en de tijd is 0.874 s. In zo'n korte tijd moet ervoor worden gezorgd dat de getrokken aluminiumvloeistof niet van tevoren op een belangrijke plek in de staart van het water stolt. Daarom wordt de matrijstemperatuur op deze posities geregeld op respectievelijk 220 ℃ en 180 ℃ door een olietemperatuurmachine te gebruiken. Verhoogde matrijstemperatuur en verbeterde vloeibaarheid van gesmolten aluminium zijn de sleutel tot het waarborgen van de interne kwaliteit van deze twee belangrijke locaties.
Gietstukken 2 en 3 zijn relatief eenvoudig van structuur, hebben een korte vulafstand en zijn gemakkelijk te vormen. Ze vereisen geen hoge vormtemperatuur, zolang de oppervlaktetemperatuur van de vorm hoog is en het product niet zwart wordt.
1.4 Mold koeling opties
Deze casting 1 maakt gebruik van superpuntkoeltechnologie en intermitterende watertoevoertechnologie. Aangezien de gietproductie een hogere temperatuur moet handhaven en er meer inzetnokken zijn aan de beweegbare matrijszijde, is het noodzakelijk om ervoor te zorgen dat de hoge temperatuur niet alleen wordt gegarandeerd, maar ook dat de verhoogde inzetstukken geen hete voegen vormen en krimpscheuren en andere defecten veroorzaken. Het snijproces wordt voor elke wisselplaat uitgevoerd en de puntkoeling wordt in het inwendige van de wisselplaat gedreven. De synchrone randapparatuur maakt gebruik van een intermitterende watertoevoermethode. Tijdens de stollingsfase van het product wordt de magneetklep geopend om het product plaatselijk af te koelen. Hierdoor wordt niet alleen een hogere temperatuur verkregen, maar wordt ook een goed koelend effect verkregen. Het superpuntkoelproces is ontworpen voor het spuitgieten van kernnaalden, zoals weergegeven door de pijl in figuur 1. Een naald van 4 mm in het midden van het wanddiktegebied veroorzaakt direct krimp. Het superpunt-koelontwerp wordt gebruikt voor de naald van 4 mm, die het porieprobleem van het schroefdraadgat kan oplossen. Op dezelfde manier wordt op andere hotspots het superpuntige koude naaldontwerp gebruikt waar de naald kan worden uitgeworpen, wat de problemen van brandwonden, huidmondjes en gebroken naalden aanzienlijk verlicht. De tijdsinstelling van superpuntkoeling en intermitterende watertoevoer moet rekening houden met de wanddikte van het geperforeerde materiaal en de locatie ervan. Daarom moeten de koude naalden in deze verschillende gebieden worden gezoneerd.
Casting 2 heeft alleen een oliegroefgat van 4 mm in het midden van de balansas en een boutgat van Φ8 mm bij de invoerinlaat, dat superpunt-koudecontrole gebruikt. Omdat nadat de aluminiumvloeistof is geschuurd, een los kanaal zal worden gevormd tussen de middelste wanddiktegebieden, moet een koude naald boven het punt worden gebruikt om de dichte laag rond het gaatje met geweld te vergroten, met een vertraging van 1 s en koeling gedurende 10 s. De 16 kleine naalden van Φ8 mm in gietstuk 3 maken allemaal gebruik van superpunt koude controle om de dikte van de dichte laag nabij het gaatje te behouden.
1.5 Selectie van lokale extrusietechnologie
De lokale extrusiepen kan de krimp in het wanddiktegebied snel oplossen en wordt veel gebruikt op het gebied van spuitgieten. De analyse van hete verbindingen van de vormstroom wordt weergegeven in figuur 5. Er zijn veel hete verbindingen in gietstuk 1 en de positie van de extrusiepennen moet redelijk worden geregeld. Elimineer eerst de hete knooppunten die kunnen worden geëlimineerd door de koude naald te gebruiken en elimineer ten tweede de hete knooppunten die niet op sleutelposities staan. Ten slotte moet u rekening houden met de plaatsing van de knijppencilinder in de interne ruimte van de mal. Het wordt over het algemeen geplaatst op een punt waar de structuur gecompliceerd is en luchtlekkage wordt voorkomen.
Kernpunten van de controle van het spuitgietproces
2.1 Controle van de sproeistroom tijdens het spuitgieten
Tijdens het spuitgietproces wordt het sproeidebiet afzonderlijk gemeten door de bewegende en vaste matrijzen, de bewegende matrijs wordt geregeld op 3 200 ml en de vaste matrijs wordt geregeld op 2 200 ml. Daarnaast worden de bovenste en onderste afwijkingswaarden apart ingesteld voor de dynamische en vaste matrijsstroomsnelheden. Aangezien de geselecteerde elektromagnetische flowmeter een nauwkeurigheid heeft van 50 ml, is de instelafwijking ±200 ml en is 200 ml de werkelijk gemeten waarde nadat één spuitpistool is verkleind. Als tijdens het productieproces de afwijkingswaarde wordt overschreden, wordt er direct een alarmsignaal afgegeven om de spuitgietproductiecyclus te stoppen. Daarom kan het effectief voorkomen dat het spuiten wordt geblokkeerd door het spuitpistool, wat kan leiden tot schimmelvorming en brandwonden.
2.2 Procesbeheersing van gesmolten aluminiumtemperatuur
Aangezien het warmtebehoudseffect van de warmhoudoven goed is, maar de verwarmingssnelheid langzamer is dan die van de kwantitatieve oven, moet de inkomende temperatuur van het gesmolten aluminium worden geregeld. De giettemperatuur van gesmolten aluminium is 675 ± 10 °C, dus de inkomende temperatuur van gesmolten aluminium in de transportpan moet boven de 700 °C worden gehouden. Voeding onder deze temperatuur zal de stroomtoestand van het gesmolten aluminium tijdens het vulproces beïnvloeden, wat resulteert in een toename van het aantal poriën op lokale locaties. Het toevoegen van materialen boven 730 ℃ veroorzaakt ernstige verbrandingen en plakken van aluminium op het oppervlak van de mal, wat de uiterlijke kwaliteit van het gietstuk zal beïnvloeden. Stel het temperatuuralarm in van het gesmolten aluminium voor de warmhoudoven. Als de giettemperatuur niet binnen het bereik ligt, zal de warmhoudoven alarmeren en de spuitgietproductiecyclus stoppen, wat de defecten veroorzaakt door de temperatuurafwijking van het gesmolten aluminium effectief kan voorkomen.
2.3 Vacuümregeling
Aangezien de gietvorm 1 is afgedicht met een beweegbare en vaste vormafdichtingstape, worden alle huls- en kernpennen afgedicht door afdichtmiddel aan te brengen, en de trechter is ook een integrale trechter, maar de pons gebruikt geen speciale afdichtstempel, maar gebruikt een verlengplaatpons (verlengd tot 150 mm). In een dergelijke verzegelde toestand wordt een alarm geactiveerd wanneer de vacuümgraad hoger is dan 4 kPa (4 kPa is een empirische alarmwaarde die is ingesteld op basis van het hoge slagingspercentage tijdens het productieproces), en de vacuümgraad is over het algemeen rond de 2.3 kPa. De reinheids- en verstoppingswaarden liggen over het algemeen in de buurt van 101 kPa en de ingestelde alarmwaarde is 90 kPa (90 kPa wordt ingesteld volgens de reinigingscyclus van de filtertank in de fabriek). Aan het einde van een reinigingscyclus moet de filtertank van het vacuümventiel tijdig worden gereinigd. Als u het niet schoonmaakt, heeft dit invloed op het zuigeffect. De instelwaarde van de vacuümtank is 1 kPa, doorgaans tussen de 2.2 en 400 Pa. Zolang de gewenste waarde wordt overschreden, wordt alarm gegeven en wordt de spuitgietmachine uitgeschakeld.
2.4 Bewaking van de feitelijke injectieparameters
De spuitgietmachine gebruikt het binnenlandse Ube 1650T-model. Naast het eigen parameterbesturingssysteem van de spuitgietmachine, gebruikt het ook een tweedimensionaal codetraceerbaarheidssysteem (in de fabriek MES-systeem genoemd) om de spuitgietmachine en randapparatuur aan te sluiten, zodat het MES-systeem de productieparameters van elke mal in realtime kan lezen en terugsturen naar de cloud voor vergelijking in de cloud (de cloudvergelijkingswaarde wordt indien nodig vooraf in de cloud ingevoerd en verschillende bereikwaarden worden uitgevoerd op basis van het daadwerkelijke bereiken van verschillende parameters. De lage snelheid is bijvoorbeeld ± 0.05 m/s , de hoge snelheid is ±3 m/s, enz., zie Tabel 2), producten die na vergelijking het bereik overschrijden, worden door het systeem vergrendeld en als niet-gekwalificeerd beoordeeld. Cloud Big Data berekent ook regelmatig de real-time relatie tussen productveroudering en parameterwijzigingen op basis van het bijgewerkte datavolume. Ontdek de redenen voor de schommelingen in het schroottarief binnen een bepaalde periode, en verbeter het gekwalificeerde tarief om producten te handhaven. Er zijn schommelingen in het productieproces van spuitgieten, waardoor de probleempunten snel kunnen worden opgespoord en ter plekke effectief een deugdzame cyclus kan worden bevorderd.
2.5 Controle van spuitgieten watertransport
Aan het begin van het watertransport gebruikt elke lijn een magneetventiel om de tijd van directe koeling of gewoon koudwatertransport te regelen. De waterdruk is 0.4 MPa en de watertemperatuur is 30 ℃ zuiver water. Behalve trog, materiaalhuls, pons, geforceerde koude plaat met gespleten kegel en materiaalhuls die normaal open zijn en directe koeling, worden alle andere directe koeling (waterbarrières) en grote puntkoeling geregeld door een magneetventiel, vertraging 3 s, koeling 15 s om de matrijstemperatuur te waarborgen. Alle naalden, van Φ4 mm tot Φ14 mm (de centrale buis van Φ1.5 mm tot Φ5.5 mm) worden gecontroleerd door superpuntkoude, de superpuntkoude watertransportdruk is 10 MPa en de watertransporttemperatuur is 10 ℃ (hier kan de temperatuur niet te laag worden ingesteld, te laag zal meer warmte wegnemen, maar het zal gemakkelijk gebroken naalden veroorzaken), elke groep superkoude naalden van dezelfde grootte is niet groter dan 8 (meer dan 8 naalden overschrijden de diameter van de diameter G1/2 verbindingspijpdiameter), alle naalden worden gecombineerd in een totaal van 6 groepen, behalve de Φ4 mm punt koude naald, de vertragingstijd is 5 s en de koeling is 13 s, en de Φ4 mm punt koude naald is ingesteld om 4 s te vertragen en de koeltijd is 13 s om het temperatuurveld van de mal te richten. In het gebied dat snel moet worden gekoeld, verminder je het ontstaan van hotspots. Het garandeert niet alleen de balans en het warmtebehoud van de schimmeltemperatuur, maar elimineert ook lokale hotspots en garandeert de productkwaliteit.
3. De kwaliteit van de nieuwe multifunctionele oliecarter. De drie producten worden geproduceerd op twee verschillende machines en de dagelijkse output is zo hoog als 980 stuks/dag, 1,500 stuks/dag en 12,000 stuks/dag van gieten 1 tot gieten 3. Het totale slagingspercentage van de drie producten tot aan de uiteindelijke assemblage is zo hoog als 97%. Afbeelding 8 is een afbeelding van het uiterlijk van de gietstukken 1, 2 en de interne kwaliteit van de gietstukken 1, 2 en 3.
4 Conclusie
- Het ontwerp en de technische punten van dit nieuwe type oliepan zijn het flexibele gebruik van vacuüm, spotkoeling, extrusie, matrijstemperatuurbalans en andere processen onder 3 verschillende giet- en uitlaatmodi, en de uiteindelijke verwerking wordt gecombineerd tot één component.
- Het belangrijkste punt van spuitgieten is om continu dieper te graven en de factoren te bewaken die de instabiliteit van de productkwaliteit beïnvloeden, om zo een stabiel productieproces te bereiken.
- Na het passeren van het voorlopige planontwerp en de identificatie en analyse van de technische punten, wordt de procescontrole aangenomen die neigt naar geautomatiseerde monitoring, zodat de qu
Bewaar de bron en het adres van dit artikel voor herdruk: De belangrijkste punten van het nieuwe type multifunctionele aluminium oliebehuizing spuitgieten:
Minge Spuitgietbedrijf zijn toegewijd aan het vervaardigen en leveren van hoogwaardige en hoogwaardige gietstukken (het assortiment metalen spuitgietonderdelen omvat voornamelijk: Dunwandig spuitgieten,Hot Chamber Spuitgieten,Koude kamer spuitgieten),Ronde Service (Die Casting Service,CNC-bewerking,Matrijzen maken, Oppervlaktebehandeling). Elk aangepast aluminium spuitgieten, magnesium of Zamak / zink spuitgieten en andere gietstukken zijn welkom om contact met ons op te nemen.
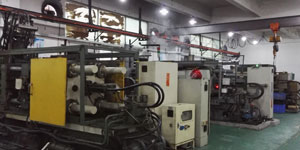
Onder controle van ISO9001 en TS 16949 worden alle processen uitgevoerd door honderden geavanceerde spuitgietmachines, 5-assige machines en andere faciliteiten, variërend van blasters tot Ultra Sonic-wasmachines. Minghe heeft niet alleen geavanceerde apparatuur, maar heeft ook professionele team van ervaren ingenieurs, operators en inspecteurs om het ontwerp van de klant waar te maken.
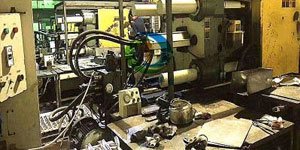
Contractfabrikant van spuitgietwerk. Mogelijkheden zijn onder meer koude kamer aluminium spuitgietonderdelen vanaf 0.15 lbs. tot 6 lbs., snelwissel instellen en machinaal bewerken. Diensten met toegevoegde waarde omvatten polijsten, trillen, ontbramen, stralen, schilderen, plateren, coaten, assembleren en bewerken. Materialen waarmee gewerkt is, zijn legeringen zoals 360, 380, 383 en 413.
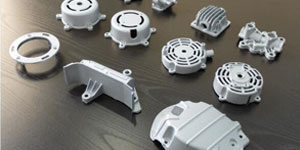
Hulp bij ontwerp van spuitgieten van zink/concurrent engineering. Custom fabrikant van precisie gegoten zink. Miniatuurgietstukken, hogedrukgietstukken, multi-slide gietstukken, conventionele gietstukken, eenheidsmatrijs en onafhankelijke spuitgietstukken en holteverzegelde gietstukken kunnen worden vervaardigd. Gietstukken kunnen worden vervaardigd in lengtes en breedtes tot 24 inch met een tolerantie van +/- 0.0005 inch.
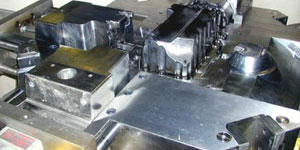
ISO 9001: 2015 gecertificeerde fabrikant van gegoten magnesium. Mogelijkheden zijn onder hoge druk spuitgieten van magnesium tot 200 ton hete kamer en 3000 ton koude kamer, gereedschapsontwerp, polijsten, gieten, machinale bewerking, poeder- en vloeistofverven, volledige QA met CMM-mogelijkheden , montage, verpakking & levering.
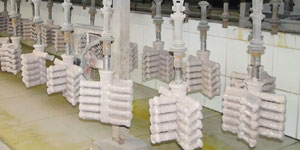
ITAF16949 gecertificeerd. Extra castingservice omvat: investering gieten,zandgieten,Zwaartekracht gieten, Verloren schuimafgietsel,Centrifugaal gieten,Vacuümgieten,Permanent vormgieten,. Mogelijkheden zijn onder meer EDI, technische assistentie, solide modellering en secundaire verwerking.
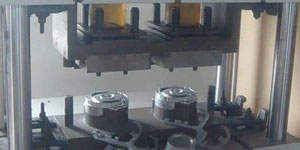
Gietindustrieën Casestudy's over onderdelen voor: auto's, fietsen, vliegtuigen, muziekinstrumenten, waterscooters, optische apparaten, sensoren, modellen, elektronische apparaten, behuizingen, klokken, machines, motoren, meubels, sieraden, mallen, telecom, verlichting, medische apparaten, fotografische apparaten, Robots, sculpturen, geluidsapparatuur, sportuitrusting, gereedschap, speelgoed en meer.
Wat kunnen we u hierna helpen doen?
∇ Ga naar de startpagina voor Spuitgieten China
→Gietonderdelen- Zoek uit wat we hebben gedaan.
→Gerangschikte tips over Spuitgietdiensten
By Minghe Die Casting Fabrikant: |Categorieën: Handige artikelen |Materiaal Tags: Aluminium gieten, Zink gieten, Magnesium gieten, Titanium gieten, Gieten van roestvrij staal, Messing gieten,Brons gieten,Video casten,Geschiedenis van ons bedrijf,Aluminium spuitgieten |Reacties uitgeschakeld