Optimalisatie en toepassing van spuitgietschema van ETC Throttle Aluminium Shell Casting op basis van MAGMASOFT
In de afgelopen jaren, met de ontwikkeling van de wereldeconomie, heeft de vraag naar auto-onderdelen van aluminiumlegeringen een grote invloed op de algemene ontwikkelingsvooruitzichten van de spuitgietindustrie. In het licht van de steeds hevigere concurrentie in de industrie en de steeds korter wordende ontwikkelingscycli van nieuwe producten, zal de levering van gekwalificeerde producten die in korte tijd voldoen aan de eisen van de klant een nieuwe richting zijn voor de ontwikkeling van spuitgietbedrijven; dit artikel gebruikt de DOE-functie van MAGMASOFT om simulatie-analyse en vergelijking van verschillende gietschema's en verschillende procesparameters uit te voeren in de vroege fase van ETC-throttle aluminium shell-gietstukken. En optimalisatie, om de beste oplossing te selecteren, waardoor de ontwikkelingscyclus wordt verkort en het succes van de eenmalige proef van het product en een soepele massaproductie en levering wordt gegarandeerd.
In het licht van de verergerende wereldwijde klimaatcrisis en de steeds sterker wordende trend van energiebesparing, emissiereductie en vervuilingsreductie, zal de auto-industrie zich ook blijven ontwikkelen in de richting van energiebesparing, emissiereductie en intelligentie; en het elektronische gasklepsysteem werd in deze omgeving geboren (Electronic Throttle Control System voor afgekort ETC) is een onmisbaar en belangrijk onderdeel van het huidige automotorsysteem. Het bepaalt de bedrijfsomstandigheden van de motor door de inlaatluchtstroom van de motor te regelen om het beste vermogen en de beste brandstof van het voertuig te garanderen. Zuinig, om de emissie-eisen verder te beheersen. Het is te voorzien dat de elektronische gashendel, als een van de sleuteltechnologieën van geavanceerde voertuigcontrole- en veiligheidssystemen, zeker goede toepassingsmogelijkheden zal hebben, net als andere geavanceerde voertuigcontroletechnologieën.
Als een van de belangrijkste componenten in het elektronische gasklepsysteem, zullen gietstukken van ETC-gasklepaluminiumschalen de haalbaarheid en stabiliteit van het systeem zeker beïnvloeden; daarom zal de productie van ETC-throttle aluminium gietstukken die aan de eisen voldoen, uiterst belangrijk zijn. In dit artikel worden, met behulp van de DOE-functie van MAGMASOFT, in de vroege fase van ETC-throttle aluminium behuizingsgietstukken, verschillende gietschema's en verschillende procesparametersimulatie-analysevergelijkingen en -optimalisaties uitgevoerd om het beste schema te selecteren, waardoor de ontwikkelingscyclus wordt verkort en dit product eenmaal wordt gegarandeerd Het succes van het proefmodel en de vlotte massaproductie en levering.
1 Analyse van de productstructuur en technische vereisten
De kwaliteit van het spuitgietmateriaal van het ETC-gietwerk met gasklephuis dat in dit artikel is bestudeerd, is AlSi12Cu1Fe, en de maximale omtrekafmeting is 111 mm * 109 mm * 84 mm. De gemiddelde dikte van dit gietstuk is 4 mm en de dikte bij de maximale wanddikte is 13 mm. De algemene structuur van het product is ingewikkelder. , Er zijn veel geïsoleerde hoge ribben, wat niet bevorderlijk is voor het ordelijk vullen van het gesmolten aluminium; de wanddikte van sommige posities verschilt enorm, en het dunwandige gebied zal eerst stollen tot een vaste toestand, wat overeenkomt met het verdelen van de gesmolten legering in vele. Het kleine omsloten gebied vormt een geïsoleerd vloeistoffasegebied bij de dikke wand. Wanneer het stollings- en krimpproces van gesmolten metaal in deze geïsoleerde vloeistoffasegebieden niet kan worden aangevuld, zal het probleem van krimpholten en porositeit onvermijdelijk binnenin optreden.
Vanwege de gecompliceerde werkomgeving van ETC-smoorklep aluminium schaalgietstukken, is gritstralen vereist om de oppervlaktekwaliteit van de gietstukken te versterken en de corrosieweerstand te verbeteren; de bijpassende installatiepositie van het product heeft hogere geometrische en dimensionale tolerantie-eisen; Zorg ervoor dat het lekvolume bij de lektestdruk van 3 bar kleiner is dan of gelijk is aan 3 cc/min, en dat de diameter van het krimpgat in het lokale gebied van het product niet groter is dan 0.7 mm, het totale aantal niet groter is dan 5, de afstand niet kleiner is dan 10 mm en niet groter is dan 10% van het totale gebied. ; Daarom zijn voor dit spuitgieten zeer hoge ontwerpvereisten voor het gietproces vereist om ervoor te zorgen dat de interne kwaliteit van het gietstuk kan voldoen aan de acceptatienorm van de klant;
2 Productspuitschema en procesparameterontwerp
2.1 Ontwerp van het spuitgieten van producten
De uiterst belangrijke ontwerpkoppeling van de spuitgietpoort in de spuitgietproductietechnologie bepaalt de kwaliteit van de spuitgietonderdelen, de spuitgietproductie-efficiëntie, de levensduur van de matrijs, het trimmen en reinigen van spuitgietonderdelen, de hersmeltsnelheid van spuitgietlegeringen en energie-efficiëntie van spuitgietmachines. Het heeft een verstrekkende impact; daarom zijn het ontwerp van een redelijke poortpositie, poortdikte en -grootte en poorthoeveelheid de sleutels om gekwalificeerde spuitgietkwaliteit te garanderen; uit de analyse van de kenmerken van de productstructuur en de procesontwerpervaring, de aluminium behuizing van de ETC-smoorklep. Er zijn drie locaties voor gietstukken die geschikt zijn voor het ontwerp van de invoerinlaat; daarom zal dit artikel drie verschillende gietschema's voor spuitgieten ontwerpen. Vanuit het theoretische vulpad en de stroomafstand zullen verschillende gietschema's verschillende vuleffecten produceren, dus ze moeten gebaseerd zijn op MAGMA-simulatiesoftwareresultaten die worden vergeleken en geanalyseerd voor verificatie;
2.1.1 Stortplan één ontwerp
Zoals weergegeven in de afbeelding, is het aantal poorten in het eerste gietschema ontworpen als dubbele strengen, die respectievelijk zijn ontworpen in het zijwandgebied van de motorinbouwpositie en de klepplaatinbouwpositie. De injectiestempel met een diameter van 60 mm is geselecteerd en de injectiesnelheidsverhouding is 1:14; Het voordeel van dit gietschema is dat de stroom gesmolten metaal relatief kort is, wat weinig invloed heeft op de temperatuurverlagingswaarde tijdens het vulproces; het ontwerp van drie stroomkanalen is bevorderlijk voor de overdracht van druk en de toevoer van het gesmolten metaal, wat nuttig is om het latere productieproces te verminderen. Het risico op krimpdefecten heeft een bepaald positief effect; het nadeel is dat vanwege productclassificatie en structuurredenen de loper moet worden ontworpen met bepaalde treden en dunwandige gebieden. Deze posities zijn vatbaar voor omhullend gas tijdens het latere vulproces. Bovendien wordt de motorinstallatiepositie van dit product niet verwerkt en is het poortontwerp hier, wat gemakkelijk de binnenmuurkern en de temperatuur bij de poortpositie direct kan wassen. Hoger, het is gemakkelijk om de gebreken van matrijs en erosie in de motorinstallatiepositie te veroorzaken; en de poortpositie wordt niet verwerkt, wat een zekere negatieve invloed heeft op het trimmen en reinigen van de latere spuitgietstukken;
2.1.2 Ontwerp van het tweede stortschema
Zoals weergegeven in de afbeelding, is het aantal poorten in het tweede gietschema ontworpen om één te zijn, en de positie is ontworpen in het zijgebied met ronde gaten van de installatiepositie van de klepplaat. De injectiestempel met een diameter van 60 mm is geselecteerd en de injectiesnelheidsverhouding is 1:30; dit gieten Het voordeel van de oplossing is dat de loper kan worden ontworpen met een relatief soepele overgang, wat gunstig is voor het vullen van het gesmolten metaal en het fenomeen van gasomhulling tijdens het vulproces vermindert, en de defecten vermindert die worden veroorzaakt door het gas dat door de loper wordt gebracht; de poort is ontworpen op de positie van het verwerkingsoppervlak. Verminder de werklast van het bijsnijden en reinigen van spuitgietstukken en verlaag de productiekosten; enkelstrengige poort kan voorkomen dat meerdere strengen gesmolten metaal de holte binnendringen en wervelingen, meesleuren en oxidatie veroorzaken. Het nadeel is dat het aan het einde van de poort is. Het voedingseffect van de hotspot-positie ontbreekt in wezen en er moet rekening worden gehouden met andere aanvullende voedingsschema's; en de gesmolten metaalstroom is relatief lang, wat een zekere negatieve invloed heeft op de gesmolten metaaltemperatuur tijdens het vulproces, en op lokale locaties kunnen koude materiaaldefecten optreden. ;
2.1.3 Ontwerp van het derde stortschema
Zoals weergegeven in de afbeelding, is het aantal van drie poorten in het gietschema ontworpen om één te zijn en wordt de positie ingesteld in het zijgebied met ronde gaten van de installatiepositie van de klepplaat. De injectiestempel met een diameter van 60 mm is geselecteerd en de injectiesnelheidsverhouding is 1:30; Het voordeel van de poort is dat de poort is ontworpen in de positie van het verwerkingsoppervlak, wat de werklast van het trimmen en reinigen van de spuitgietmachine kan verminderen en de productiekosten kan verlagen. De poort is ontworpen met een lineaire vulstijl, die de vulslag van het gesmolten aluminium en het temperatuurverlies van het gesmolten aluminium kan verminderen. Het bedrag wordt verlaagd; de afstand tussen de stempel en de poort is kort, wat kan zorgen voor een effectieve overdracht van de stempeldruk; het nadeel is dat de flexibiliteit van de latere productieaanpassingsparameters slecht is en dat de productkwaliteit niet kan worden verbeterd door de spuitgietparameters aan te passen.
2.2 Productprocesparameterontwerp
Volgens de structurele analyse en kwaliteitseisen van ETC-throttle aluminium shell-gietstukken, gebruikt dit product een 350T spuitgietmachine, één vorm en één holteontwerp, en de gietdruk is ingesteld op 100 MPa om voldoende voedingsefficiëntie te garanderen en het optreden van krimpdefecten in de latere periode. ; De giettemperatuur is ontworpen om 660-680 ℃ te zijn, en de bewegende en vaste vormkernen worden voorverwarmd tot 180-200 ℃; tijdens het vullen wordt de lage snelheid ingesteld op 0.25 m/s, de hoge snelheid op 3 m/s en worden de schakelpunten voor hoge snelheid getest op respectievelijk 340 mm en 350 mm. De positie wordt gebruikt om de meest stabiele vultoestand van het gesmolten metaal en het minste wervelstroom- en meesleepverschijnsel te bepalen; tegelijkertijd wordt het temperatuurregelsysteem van lijnkoeling en puntkoeling gebruikt om een goede thermische balans van de mal te garanderen;
3. Numerieke simulatie en vergelijkende analyse van importeren met één klik
De controle van het vul- en stollingsproces van het gietstuk heeft een beslissende invloed op de kwaliteit van het spuitgieten, maar aangezien deze twee processen tijdens het productieproces in een gesloten en onzichtbare holte worden voltooid, is het onmogelijk om direct of indirect waar te nemen en te analyseren, dus de vorige waarde Simulatie is bijzonder belangrijk; door gebruik te maken van de MAG-code DOE-functie, import met één klik van de bovenstaande drie injectieschema's en twee snelle testschakelposities, eenmalige berekening van meerdere schema's, de snelste voorspelling van de defectlocatie en het vinden van het beste plan om de interne kwaliteit van producten te verbeteren, ontwikkelingscycli te verminderen en productiekosten te verlagen.
3.1 Simulatie en analyse van het vulproces
Zoals weergegeven in figuur 3, is het simulatieresultaat van de eerste rij van de afbeelding de vultijd. De snelle schakelpositie van de eerste drie schema's is 340 mm en de vultijd is kort. De snelle schakelpositie van de laatste drie schema's is 350 mm en de vultijd is lang. De felle kleurpositie is de laatste vulpositie van de drie injectieschema's;
Het resultaat van de tweede rij van de afbeelding is het maximale luchtdrukresultaat. De felle kleur van het simulatieresultaat is de hoge luchtdrukpositie en het risico op huidmondjes is hoog. Uit vergelijking blijkt dat de luchtdrukwaarde van Schema 2 en Schema 5 relatief laag is, en het risico op stoma relatief klein;
Het resultaat van de derde rij van de afbeelding is het resultaat van het vulvolume. Het simulatieresultaat heeft een hoog luchtgehalte in de heldere stand en een hoog risico op lekkage. Uit vergelijking blijkt dat de waarde van het tweede en vijfde deel van het schema relatief laag is en dat het risico op lekkage relatief klein is;
Uitgebreide analyse van de simulatieresultaten van het vulproces laat zien dat de luchtdruk en meevoering van de tweede en vijfde optie relatief laag zijn, en de tweede snelle schakelpositie naar voren is, en de vultijd kort is, dus de algehele vervormbaarheid is goed.
3.2 Simulatie en analyse van het stollingsproces
Zoals weergegeven in figuur 4, is het resultaat van de eerste rij van de afbeelding het vriestemperatuurveld. De simulatieresultaten laten zien dat de stollingstijd van de binnenpoort van schema 3 en schema 6 het langst is en dat de druktoevoertijd het langst is; schema 1 en schema 4 zijn de tweede en de drukvoedingstijd is de middelste; de stollingstijd van de binnenpoort van schema 2 en schema 5 De kortste en de kortste tijd voor druktoevoer;
Het resultaat van de tweede rij is de effectieve toevoertijd van de hete joint, en de felle kleur van het simulatieresultaat is de positie van de hete joint van het product, de positie waar de productstructuur relatief dik is en uiteindelijk gestold. De locaties van programma's 1, 2, 4 en 5 zijn in principe hetzelfde. Schema 3 en Schema 6 hebben relatief dikke binnenpoorten, dus als de twee hotspots bij de binnenpoort met elkaar verbonden zijn, zullen de hotspots toenemen;
Het resultaat van de derde rij is het krimpresultaat. Vanwege de druktoevoer is de krimptoestand van schema 3 en schema 6 het kleinst en is de krimp van de andere vier schema's in wezen hetzelfde. Ter vergelijking: schema 2 en schema 5 zijn relatief klein.
Gebaseerd op de analyse van de simulatieresultaten van het stollingsproces, is de krimpholte van schema 3 en schema 6 het kleinst, maar de hete verbinding bij de binnenste poort is het grootst, en de resultaten van de warmteverbinding en krimp van schema 2 en schema 5 zijn relatief beter.
4. Productieverificatie
Uitgebreide simulatieanalyse, de tweede gietmethode wordt gebruikt voor productie. Figuur 5 toont het productiebeeld van ETC-afgietsels met aluminium behuizing; door productinspectie en röntgeninspectie vertoonden de gietstukken geen poriën en krimpdefecten die de kwaliteitseisen van de klant overtroffen; ook geslaagd voor de vereisten voor zijlekkage, er is geen lekkage opgetreden; het oppervlak van het gietstuk was helder, er waren geen duidelijke defecten van koud materiaal en er verscheen onvoldoende gieten, het algehele effect voldeed volledig aan de kwaliteitsinspectie-eisen van de klant en een soepele massaproductie.
Bewaar de bron en het adres van dit artikel voor herdruk:Optimalisatie en toepassing van spuitgietschema van ETC Throttle Aluminium Shell Casting op basis van MAGMASOFT
Minge Spuitgietbedrijf zijn toegewijd aan het vervaardigen en leveren van hoogwaardige en hoogwaardige gietstukken (het assortiment metalen spuitgietonderdelen omvat voornamelijk: Dunwandig spuitgieten,Hot Chamber Spuitgieten,Koude kamer spuitgieten),Ronde Service (Die Casting Service,CNC-bewerking,Matrijzen maken, Oppervlaktebehandeling). Elk aangepast aluminium spuitgieten, magnesium of Zamak / zink spuitgieten en andere gietstukken zijn welkom om contact met ons op te nemen.
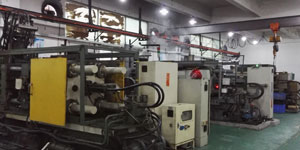
Onder controle van ISO9001 en TS 16949 worden alle processen uitgevoerd door honderden geavanceerde spuitgietmachines, 5-assige machines en andere faciliteiten, variërend van blasters tot Ultra Sonic-wasmachines. Minghe heeft niet alleen geavanceerde apparatuur, maar heeft ook professionele team van ervaren ingenieurs, operators en inspecteurs om het ontwerp van de klant waar te maken.
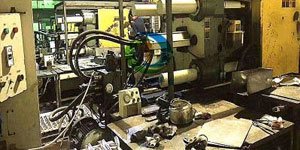
Contractfabrikant van spuitgietwerk. Mogelijkheden zijn onder meer koude kamer aluminium spuitgietonderdelen vanaf 0.15 lbs. tot 6 lbs., snelwissel instellen en machinaal bewerken. Diensten met toegevoegde waarde omvatten polijsten, trillen, ontbramen, stralen, schilderen, plateren, coaten, assembleren en bewerken. Materialen waarmee gewerkt is, zijn legeringen zoals 360, 380, 383 en 413.
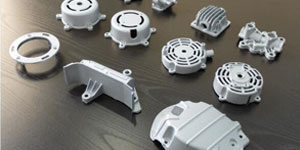
Hulp bij ontwerp van spuitgieten van zink/concurrent engineering. Custom fabrikant van precisie gegoten zink. Miniatuurgietstukken, hogedrukgietstukken, multi-slide gietstukken, conventionele gietstukken, eenheidsmatrijs en onafhankelijke spuitgietstukken en holteverzegelde gietstukken kunnen worden vervaardigd. Gietstukken kunnen worden vervaardigd in lengtes en breedtes tot 24 inch met een tolerantie van +/- 0.0005 inch.
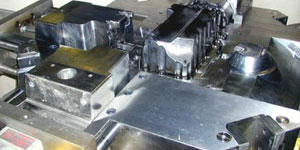
ISO 9001: 2015 gecertificeerde fabrikant van gegoten magnesium. Mogelijkheden zijn onder hoge druk spuitgieten van magnesium tot 200 ton hete kamer en 3000 ton koude kamer, gereedschapsontwerp, polijsten, gieten, machinale bewerking, poeder- en vloeistofverven, volledige QA met CMM-mogelijkheden , montage, verpakking & levering.
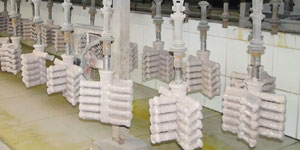
ITAF16949 gecertificeerd. Extra castingservice omvat: investering gieten,zandgieten,Zwaartekracht gieten, Verloren schuimafgietsel,Centrifugaal gieten,Vacuümgieten,Permanent vormgieten,. Mogelijkheden zijn onder meer EDI, technische assistentie, solide modellering en secundaire verwerking.
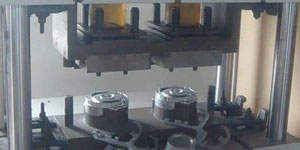
Gietindustrieën Casestudy's over onderdelen voor: auto's, fietsen, vliegtuigen, muziekinstrumenten, waterscooters, optische apparaten, sensoren, modellen, elektronische apparaten, behuizingen, klokken, machines, motoren, meubels, sieraden, mallen, telecom, verlichting, medische apparaten, fotografische apparaten, Robots, sculpturen, geluidsapparatuur, sportuitrusting, gereedschap, speelgoed en meer.
Wat kunnen we u hierna helpen doen?
∇ Ga naar de startpagina voor Spuitgieten China
→Gietonderdelen- Zoek uit wat we hebben gedaan.
→Gerangschikte tips over Spuitgietdiensten
By Minghe Die Casting Fabrikant: |Categorieën: Handige artikelen |Materiaal Tags: Aluminium gieten, Zink gieten, Magnesium gieten, Titanium gieten, Gieten van roestvrij staal, Messing gieten,Brons gieten,Video casten,Geschiedenis van ons bedrijf,Aluminium spuitgieten |Reacties uitgeschakeld