Onderzoek naar spuitgietmatrijspoortsysteem
Spuitgieten is een van de belangrijkste middelen voor het vormen van non-ferrometalen. Tijdens het spuitgietproces kunnen, als gevolg van de verschillende stromingstoestanden van het gesmolten metaal in de holte, ongewenste verschijnselen optreden zoals koude barrières, patronen, poriën en segregatie. Om deze ongewenste verschijnselen te voorkomen, is het zeer noodzakelijk om de stroom van gesmolten metaal in de holte te beheersen. De sleutel tot het beheersen van de stroom van gesmolten metaal in de holte ligt in het onderzoek en het ontwerp van het spuitgietmatrijspoortsysteem.
Het productieproces van spuitgietmatrijzen
Het CAD/CAE/CAM/CAT-proces van spuitgieten van matrijzen:.
Het ontwerp van het gietvormgietsysteem
Bij het onderzoek naar het spuitgietmatrijspoortsysteem zijn de positie en vorm van de poort belangrijke factoren om de stroomtoestand en vulrichting van de oplossing te regelen. Focus eerst op de locatie van de poort en de vorm van de loper, ontwerp de poort, loper, slakkenzak, overloopgoot en uitlaatkanaal; gebruik vervolgens CAE-software om de stroom van oplossing in de holte te analyseren. De positie en grootte van de binnengeleider en de binnenpoort hebben een beslissende invloed op de vulmethode.
Het ontwerp van de binnenpoort
Bij het plaatsen van de poort op het eindproduct, wordt dit meestal uitgevoerd volgens de volgende procedure:
- Berekeningsformule van het dwarsdoorsnede-oppervlak van de poort: A=U/(vt): productvolume (cIn.):A: het dwarsdoorsnede-oppervlak van de poort (cm2)/v: de snelheid van de aluminiumoplossing van de poort (cm/s)/T: vulling keer)
- Bereken de oppervlakte van de dwarsdoorsnede van de binnenpoort.
- Stel volgens het dwarsdoorsnede-oppervlak van de binnenste poort de poortvorm in en stel vervolgens de poortpositie in, en ontwerp in eerste instantie de positie van de stroomgoot en de slakkenzak.
- Maak verschillende poortschema's (maak meestal eerst het dwarsdoorsnede-oppervlak van de binnenloper kleiner en breid dit indien nodig uit na de test) en maak 3D-gegevens.
- Voer CAE-analyse (dat wil zeggen stroomanalyse) uit op basis van de geproduceerde 3D-gegevens.
- Evalueer de analyseresultaten.
- Als er na de evaluatie ongunstige verschijnselen optreden, moet het plan worden verbeterd en moet vervolgens een CAE-analyse worden uitgevoerd totdat een meer bevredigend plan is verkregen.
Ontwerp van sprue en uitlaatsysteem
De binnenste poort moet worden geplaatst op een positie waar het gesmolten metaal het beste in de holte stroomt, de uitlaat is gevuld en alle hoeken van de holte kunnen worden gevuld met gesmolten metaal. Gebruik waar mogelijk een interne poort. Als er meerdere interne poorten nodig zijn, moet ervoor worden gezorgd dat de stroom gesmolten metaal elkaar niet hindert of samenkomt in de holte zonder te dispergeren (dwz de metaalstroom in één richting te laten stromen) om de convergentie van de gesmolten metaal in de vortex van de holte.
Wanneer de grootte van de spuitgieten groot is, is het soms onmogelijk om het vereiste dwarsdoorsnede-oppervlak van de loper uit slechts één loper te verkrijgen, dus er moeten meerdere lopers worden gebruikt. Er moet echter worden opgemerkt dat de instelling van de binnenste geleider ervoor moet zorgen dat het gesmolten metaal slechts in één richting wordt geleid, om wervelstromen te voorkomen wanneer het gesmolten metaal in de holte samenvloeit.
De gesmolten metaalstroom moet zo min mogelijk in de holte draaien, zodat het gesmolten metaal het dikwandige deel van het spuitgietstuk kan bereiken.
De gesmolten metaalstroom moet zo kort en gelijkmatig mogelijk zijn.
Het dwarsdoorsnede-oppervlak van de binnenste runner wordt geleidelijk verkleind naar de binnenste runner om het meesleuren van gas te verminderen, wat gunstig is om de compactheid van het spuitgietwerk te verbeteren. De binnenste runner moet soepel worden overgezet tijdens het stroomproces om scherpe bochten en stroomimpact zoveel mogelijk te voorkomen.
Wanneer er meerdere holtes zijn, moet het dwarsdoorsnede-oppervlak van de loper in secties worden verkleind volgens de volumeverhouding van elke holte.
De lucht in de holte en het vervluchtigde gas van het smeermiddel moeten door het stromende gesmolten metaal naar de uitlaatgroef worden geduwd en vervolgens uit de uitlaatgroef ontsnappen. In het bijzonder mag de stroom gesmolten metaal het gas niet in het blinde gat achterlaten en de uitlaatgroef voortijdig blokkeren.
De metaalstroom mag geen thermische schok vormen op de slechte warmteafvoer. Bij spuitgietstukken met ribben moet het metaal zoveel mogelijk in de richting van de ribben stromen.
Vermijd dat gesmolten metaal gemakkelijk beschadigde vormdelen en kernen wegspoelt. Wanneer het onvermijdelijk is, moet een isolatiezone op de spruw worden ingesteld om thermische schokken te voorkomen.
Over het algemeen geldt: hoe breder en dikker de binnenloper, hoe groter het risico op niet-uniforme stroming. Probeer tegelijkertijd geen te dikke poorten te gebruiken; vermijd vervorming bij het snijden van de poorten.
Uitlaat van holte
De overloopgoot wordt gebruikt om het gesmolten metaal te verwijderen dat aanvankelijk tijdens het gieten is gespoten en om de temperatuur van de mal constant te maken. De vloeistofstroomgroef is ingesteld op de positie waar de mal gemakkelijk gas kan bevatten en wordt gebruikt voor uitlaatgas om de stroomtoestand van het gesmolten metaal te verbeteren en het gesmolten metaal naar alle hoeken van de holte te leiden om een goed gietoppervlak te verkrijgen . De uitlaatgroef is verbonden met de voorkant van de overloopgroef en de slakkenzak, of direct verbonden met de spouw.
Het totale oppervlak van de dwarsdoorsnede van de uitlaatsleuf moet ongeveer gelijk zijn aan het oppervlak van de dwarsdoorsnede van de binnenste runner.
De positie van de uitlaatgroef op het scheidingsoppervlak wordt bepaald volgens de stroomtoestand van het gesmolten metaal in de holte. De uitlaatgroef kan het beste "niet recht" maar "gebogen" zijn om te voorkomen dat het gesmolten metaal opspuit en mensen pijn doet. De diepte van de uitlaatgroef op het scheidingsoppervlak is meestal 0.05 mm - 0.15 mm; de diepte van de uitlaatgroef in de holte is meestal 0.3 mm ~ 0.5 mm; de diepte van de uitlaatgroef aan de rand van de mal is meestal 0.1 mm ~ 0.15 mm; De breedte van de uitlaatsleuf is over het algemeen 5 mm ~ 20 mm.
De uitlaatopening tussen de uitwerppen en de duwstang is erg belangrijk voor de uitlaat van de holte, meestal geregeld op 0.01 mm-0.02 mm, of vergroot totdat er geen bramen worden geproduceerd.
De vaste kernuitlaat is ook een effectieve uitlaatmethode. Gewoonlijk wordt een opening van 0.05 mm-0.08 mm aan de omtrek van de kern geregeld, zodat de positioneringshals van de kern wordt geopend met een uitlaatsleufbreedte en -dikte van 1 mm-2 mm, en het gas in de holte wordt geopend uit de uitlaatsleuf langs de nek. Het wordt afgevoerd via de bodem van de holte. De ruwheid van de uitlaatsleuf mag niet worden verwaarloosd. Het moet een hoge mate van gladheid behouden om te voorkomen dat het tijdens gebruik wordt geblokkeerd door de verf die aan het vuil blijft kleven, wat de uitlaat zal beïnvloeden.
Stroomanalyse Evaluatie en tegenmaatregelen
In het matrijsontwerpproces moet de metaalstroom zoveel mogelijk in één richting kunnen stromen. Nadat de stroming is geanalyseerd, wanneer wervelstromen in de holte worden gevonden, moet de geleidingshoek of grootte van de binnenste poort worden gewijzigd om de wervelstroomtoestand te elimineren.
Wanneer gesmolten metaal samenkomt, laat het gesmolten metaal dan een bepaalde afstand stromen voordat u de stroom stopt; daarom moeten een overlooptrog en een slakkenzak buiten de holte bij de kruising worden toegevoegd om het onderkoelde gesmolten metaal en de luchtverbindingen in de overlooptrog en de slakkenzak te laten stromen; laat het daaropvolgende gesmolten metaal schoon en op kamertemperatuur zijn.
Wanneer de vulsnelheid van verschillende onderdelen verschillend is, moet de dikte of breedte van de binnenste poort worden aangepast (indien nodig geleidelijk verhogen) om het doel van in principe dezelfde vulsnelheid te bereiken, maar dit moet worden bereikt door de binnenste runner zoveel mogelijk te verbreden als mogelijk.
Na de stromingsanalyse wordt het vullende achterliggende deel gevonden en kan er ook een binnenloper worden toegevoegd. Voor dunwandige spuitgietonderdelen moet bij spuitgieten een kortere vultijd worden gekozen; daarom moet de vultijd worden verkort door het dwarsdoorsnede-oppervlak van de binnenloper te vergroten om een betere oppervlaktekwaliteit te bereiken.
Voor dikwandige spuitgietstukken die een hoge compactheid vereisen, is een effectieve ontluchting noodzakelijk. Voor spuitgieten moet een gemiddelde vultijd worden gebruikt. Daarom moet de doorsnede van de binnengeleider worden aangepast om de overeenkomstige vultijd te verkrijgen en een betere oppervlaktekwaliteit en interne kwaliteit te verkrijgen.
Kortom, bij het ontwerpen van spuitgietmatrijzen moet aandacht worden besteed aan het voorkomen van veel ongewenste verschijnselen. Zelfs in het huidige tijdperk waarin CAE-analysemethoden beschikbaar zijn, wordt in het vroege stadium van sprue-ontwerp de samengevatte ervaring eerst overwogen in het poortsysteem, organisch gecombineerd, geanalyseerd, verbeterd en geüpgraded, wat ongetwijfeld een multiplicatoreffect zal bereiken met de helft van de moeite.
Bewaar de bron en het adres van dit artikel voor herdruk:Onderzoek naar spuitgietmatrijspoortsysteem
Minge Spuitgietbedrijf zijn toegewijd aan het vervaardigen en leveren van hoogwaardige en hoogwaardige gietstukken (het assortiment metalen spuitgietonderdelen omvat voornamelijk: Dunwandig spuitgieten,Hot Chamber Spuitgieten,Koude kamer spuitgieten),Ronde Service (Die Casting Service,CNC-bewerking,Matrijzen maken, Oppervlaktebehandeling). Elk aangepast aluminium spuitgieten, magnesium of Zamak / zink spuitgieten en andere gietstukken zijn welkom om contact met ons op te nemen.
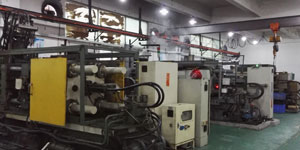
Onder controle van ISO9001 en TS 16949 worden alle processen uitgevoerd door honderden geavanceerde spuitgietmachines, 5-assige machines en andere faciliteiten, variërend van blasters tot Ultra Sonic-wasmachines. Minghe heeft niet alleen geavanceerde apparatuur, maar heeft ook professionele team van ervaren ingenieurs, operators en inspecteurs om het ontwerp van de klant waar te maken.
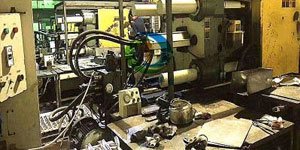
Contractfabrikant van spuitgietwerk. Mogelijkheden zijn onder meer koude kamer aluminium spuitgietonderdelen vanaf 0.15 lbs. tot 6 lbs., snelwissel instellen en machinaal bewerken. Diensten met toegevoegde waarde omvatten polijsten, trillen, ontbramen, stralen, schilderen, plateren, coaten, assembleren en bewerken. Materialen waarmee gewerkt is, zijn legeringen zoals 360, 380, 383 en 413.
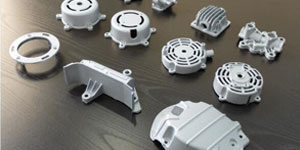
Hulp bij ontwerp van spuitgieten van zink/concurrent engineering. Custom fabrikant van precisie gegoten zink. Miniatuurgietstukken, hogedrukgietstukken, multi-slide gietstukken, conventionele gietstukken, eenheidsmatrijs en onafhankelijke spuitgietstukken en holteverzegelde gietstukken kunnen worden vervaardigd. Gietstukken kunnen worden vervaardigd in lengtes en breedtes tot 24 inch met een tolerantie van +/- 0.0005 inch.
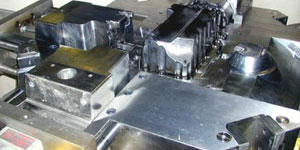
ISO 9001: 2015 gecertificeerde fabrikant van gegoten magnesium. Mogelijkheden zijn onder hoge druk spuitgieten van magnesium tot 200 ton hete kamer en 3000 ton koude kamer, gereedschapsontwerp, polijsten, gieten, machinale bewerking, poeder- en vloeistofverven, volledige QA met CMM-mogelijkheden , montage, verpakking & levering.
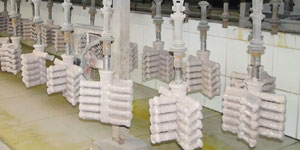
ITAF16949 gecertificeerd. Extra castingservice omvat: investering gieten,zandgieten,Zwaartekracht gieten, Verloren schuimafgietsel,Centrifugaal gieten,Vacuümgieten,Permanent vormgieten,. Mogelijkheden zijn onder meer EDI, technische assistentie, solide modellering en secundaire verwerking.
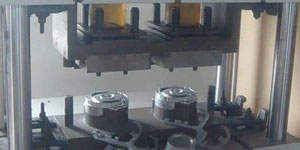
Gietindustrieën Casestudy's over onderdelen voor: auto's, fietsen, vliegtuigen, muziekinstrumenten, waterscooters, optische apparaten, sensoren, modellen, elektronische apparaten, behuizingen, klokken, machines, motoren, meubels, sieraden, mallen, telecom, verlichting, medische apparaten, fotografische apparaten, Robots, sculpturen, geluidsapparatuur, sportuitrusting, gereedschap, speelgoed en meer.
Wat kunnen we u hierna helpen doen?
∇ Ga naar de startpagina voor Spuitgieten China
→Gietonderdelen- Zoek uit wat we hebben gedaan.
→Gerangschikte tips over Spuitgietdiensten
By Minghe Die Casting Fabrikant: |Categorieën: Handige artikelen |Materiaal Tags: Aluminium gieten, Zink gieten, Magnesium gieten, Titanium gieten, Gieten van roestvrij staal, Messing gieten,Brons gieten,Video casten,Geschiedenis van ons bedrijf,Aluminium spuitgieten |Reacties uitgeschakeld